Question 52: What is your recommended method for mitigating fouling in reforming unit recycle compressors? Has any technique proven successful? Is anyone using reformate to clean the compressor online?
MUEHLBAUER (Valero Energy Corporation – Benicia Refinery)
The best method for reducing fouling in the compressor is to take the nitrogen out of the feed. In Valero, we have recently reviewed our naphtha hydrotreater performance. In a lot of cases, we found that the naphtha hydrotreaters can actually be pressure drop-limited versus activity-limited. We have changed some of the operating philosophy on some of the units to the point of operating them at higher temperatures knowing that if the unit was pressure drop-limited, then we might be leaving activity on the shelf. So, operating the reactors at a higher severity is one of the moves that could be possible to remove nitrogen from the reformer feed.
Also, using a catalyst like a NiMo (nickel molybdenum) can promote the HDN (hydrodenitrification) reaction in the upstream hydrotreater. I think those two steps are probably the best ways we have found to mitigate the compressor fouling. In the event that the compressor does get fouled during online water-washing, which we have experienced at two of our locations, we will work very closely with the Rotating Equipment Group and the compressor manufacturers which both have very specific procedures on how to perform the waterwash. We have been successful mitigating the effects of cleaning the fouling with online water-washing. We are actually water-washing one unit, at one point, on a daily basis. With that frequent exposure, one of the side effects we saw was that we had less chloride retention on some of our catalysts, just with the added moisture to the system.
Finally, if the goal is to just extend the interval between times for the shutdown and offline water-washing of the compressor, we have been successful revalidating the trip setting on the hydrogen flow. In some events, we found that the initial trip setting we used was not necessarily based on the process limitation; it was more of an instrumentation limitation and dependent on how accurate the instrument would read at the lower flow rates. So, by changing the flow instrument technology, we were able to get more accuracy and perhaps lower that trip setting to get a couple more months between shutdowns. If you end up doing that, you will have to closely examine the economics around the compressor inefficiency. However, you may gain the extra couple of months you need to do a scheduled shutdown.
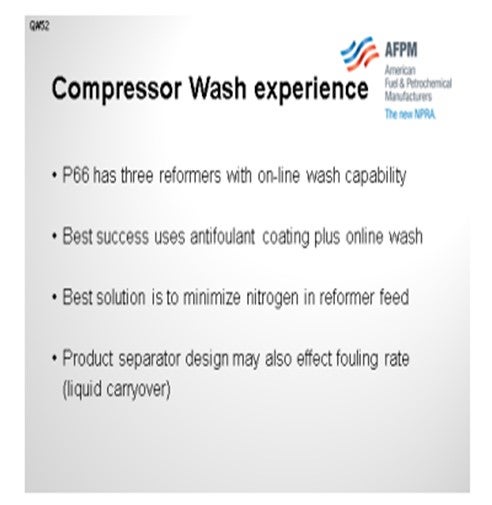
PIZZINI (Phillips 66)
The Phillips 66 experience with online washes: We have three reformers set up for an online wash, although I believe only one uses it continuously. These are all naphtha washes, by the way. We have had the best success at a site that combines the naphtha wash with a coding on the compressor impeller; so, it is using both techniques. To echo what Joe said, keeping nitrogen out of feed is your best option. We have some evidence that the design of the product separator makes a difference, for example, the distance between the liquid level and the outlet nozzle.
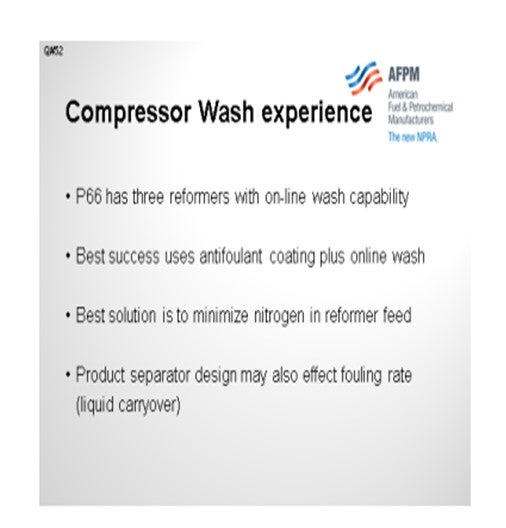
On the next slide, I have listed some Best Practices as guidelines for installing these wash systems. We recommend an all-welded design. You do not want any loose parts in front of a compressor. Locate the quill 10 diameters upstream of the compressor and aim the quill in the direction of the flow. For our wash fluids, we recommend using dry naphtha range hydrocarbon and routing it through a strainer to take out any particles that might be present. The next bullet should probably have been first. Any time you undertake this kind of wash, make sure the manufacturer has reviewed your plans and agrees with the amount of liquid you are planning to inject. In some of our refineries, the target is 1 wt% or 2 wt% of liquid relative to the vapor flow through the machine. Lastly, check the seal oil viscosity to make sure there is no naphtha leakage into the seal oil.
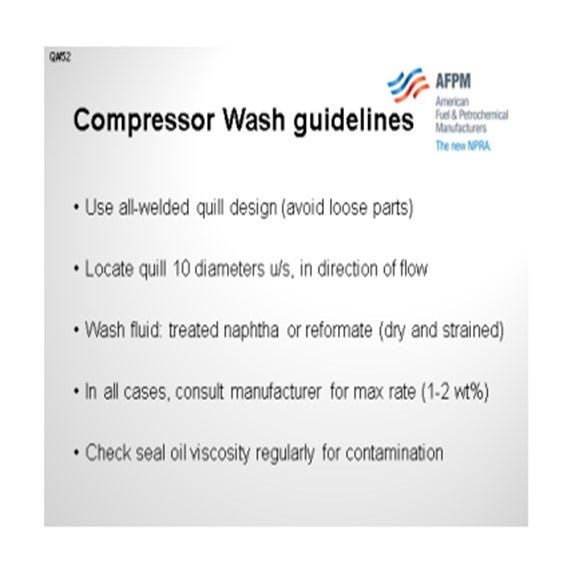
WILLIAM BANDY (Tesoro Refining and Marketing Company)
My question is about the waterwash on the recycle compressor. Are you talking about centrifugal compressors, and do those have dry gas seals or not?
MUEHLBAUER (Valero Energy Corporation – Benicia Refinery)
I am actually not sure about the type of seal design on those compressors. Our Reliability group and equipment manufacturers did note that having the ability to control the speed of the compressor was one of the main factors used when choosing the suitability of waterwash for particular compressors. Turbine-driven is preferred to be able to drop it down to a minimum speed before performing this procedure, but I am not sure about the seal design.
WILLIAM BANDY (Tesoro Refining and Marketing Company)
I think you have to be really careful with gas seals. We used to water-wash the centrifugal compressor on our reformer all the time to get rid of salt fouling. And then during the last turnaround, we converted to dry gas seals. According to the seal manufacturer, we are no longer able to water-wash, so we are in a bind.
The other question is for Paul. When you mentioned a naphtha wash, did you mean a continuous naphtha injection into the suction of the compressor? You did not mean filling the case with naphtha, did you?
PIZZINI (Phillips 66)
That is right: a continuous wash into the suction of the compressor. Also, if a compressor has already gotten really dirty, you have to think twice about establishing that wash. It might throw off the wheel balance. So, when we do the online wash, we would like to start with a clean impeller and continue it throughout the run.
WILLIAM BANDY (Tesoro Refining and Marketing Company)
We do that, too. I just was not sure if you meant a continuous naphtha injection or some kind of a discontinuous batch wash. Thanks.
ALLEN KAISER (Delek Refining Ltd.)
When we have the liquid wash, does the compressor face any vibration issues? In the case of a waterwash on a continuous basis, is there an issue with the moisture control in the recycle gas?
PIZZINI (Phillips 66)
In response to the vibration question, the vibration is really the reason they are doing the wash in the first place. It is generally not done on a compressor that goes three years without a vibration problem. We have only installed wash systems where there were known vibration issues.
MUEHLBAUER (Valero Energy Corporation – Benicia Refinery)
I will add just a few comments. We monitor the vibration throughout the procedure. Monitoring the compressor vibration during the procedure and noting the decrease in vibration levels will indicate that the compressor has cleared up. With regard to the recycle gas moisture: These online waterwashes are done for a matter of seconds or minutes. So, we do not go out of the way to monitor the recycle moisture. We believe that some of the older grades of catalyst had a harder time retaining chlorides with frequent washing.
BRAD PALMER (Phillips 66)
Joe, about how much water is being injected during those online washes? You said for just a few seconds to minutes, but how much are you adding?
MUEHLBAUER (Valero Energy Corporation – Benicia Refinery)
It is not much. The number I was quoted was about one gallon per minute, which might actually correspond to this 1 wt% range.
R.K. (RICK) GRUBB (Chevron Products Company)
You said seconds or minutes. How do they actually determine how long?
MUEHLBAUER (Valero Energy Corporation – Benicia Refinery)
We monitor the compressor vibration, which apparently comes down right away.
PIZZINI (Phillips 66)
At P66, our experience has been mixed as to the effectiveness of online compressor washes. We have three units that have the capability for online naphtha washing, but only one is currently using it. We have also tried coating the rotors. Our best success was where we have both an anti-foulant coating plus an online naphtha wash. This area is so subjective because every unit is different and the amount of nitrogen in the feed and other water/chloride conditions
effects where ammonium chloride lays down and how rapidly. The design of the upstream separator can also affect the fouling rate of the compressor. By far, the best solution is preventing nitrogen from reaching the reformer.
In all cases the compressor manufacture should be consulted in developing any offline waterwash procedures, online naphtha wash systems or coating applications. Whenever a compressor is water-washed the reactor effluent exchangers, trim coolers and stabilizer overhead should also be evaluated for waterwashing.
Use an all-welded quill design because you do not want pieces coming off. The quill should be located 10 diameters upstream of compressor, oriented with the flow. The maximum rate, as approved by the manufacturer, is 1 wt% to 2 wt%. Use low moisture low solids naphtha or reformate, routed through a screen. Use buffer gas to prevent contamination of the seal oil. Typical buffer gas is hydrogen set at 4 psig to 7 psig above the seal chamber suction pressure. Check the viscosity of lube and seal oil to ensure oil not being contaminated by the wash fluid. Monitor compressor performance and vibration on a regular basis.
BRUCE WRIGHT (Baker Hughes)
The foulant material is typical salts, iron sulfide, or corrosion products. Baker Hughes ’antifoulant additives have been successfully used to mitigate compressor fouling. However, proper additive injection techniques are required to ensure program performance and avoid potential problems.