Question 52: What is the configuration of thermocouples that can be used to effectively monitor radial temperature differences, and what is the acceptable radial temperature spread in hydrotreaters/hydrocrackers?
SIVADASAN (UOP LLC, A Honeywell Company)
The UOP bed thermometry consists of a stab-in type of assembly with three thermocouples on top of the bed. Typically, a multipoint thermometer is provided in the case of the first bed of a hydrotreating unit and if the bed length is more than 11 feet for a hydrocracking bed. At the bottom of the catalyst bed, industry-standard flexible-type multipoint thermocouples are specified.
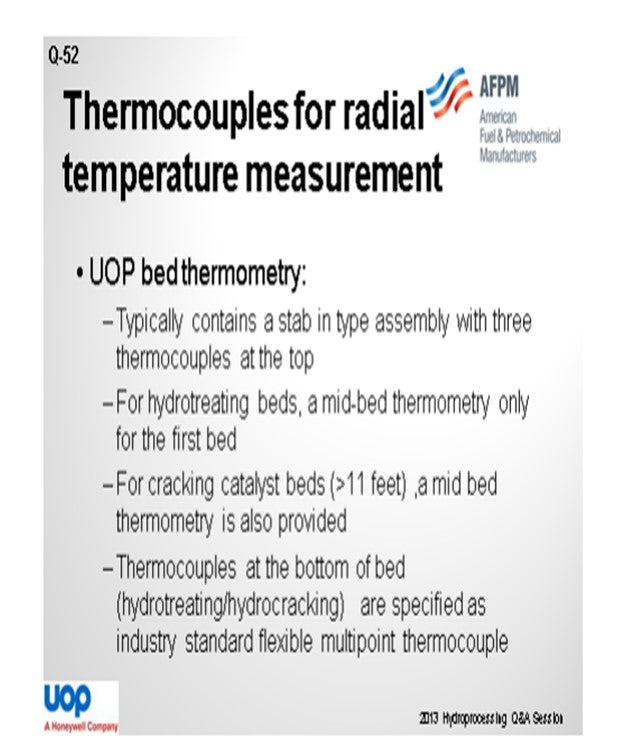
Radial temperature spread is the difference between the maximum and minimum temperature at the same elevation level. It is monitored at various levels in the reactor and is the primary indicator of flow distribution within the catalyst bed. Ideally, the thermocouple at the same level should register identical temperatures; but sometimes, less-than-perfect distribution of the reactants in the catalyst bed happens due to different factors.
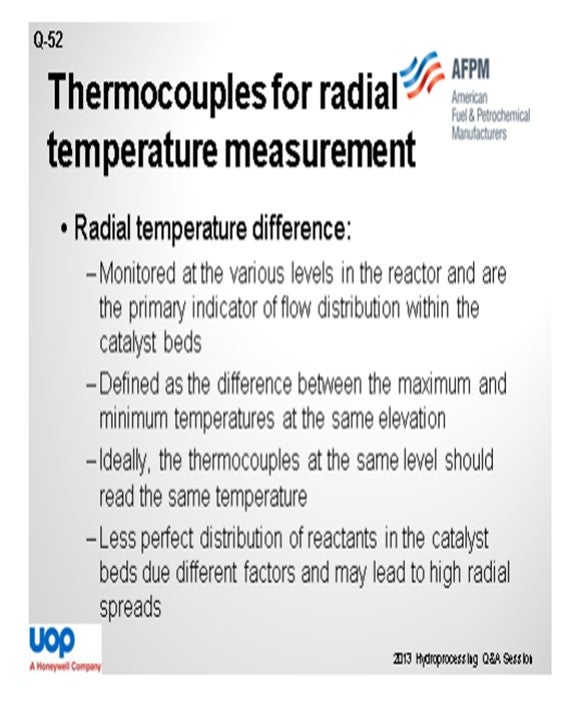
Our guideline is that a radial gradient higher than 20°F is considered a point of concern. It is not acceptable for it to be more than 30°F. So how can you prevent this radial spread? Try to have a well-designed internal with proper installation and maintenance and good catalyst loading with appropriate catalyst bed design. Also, avoid process upsets and loss of catalyst containment and prevent contaminants in the feed or recycle oil.
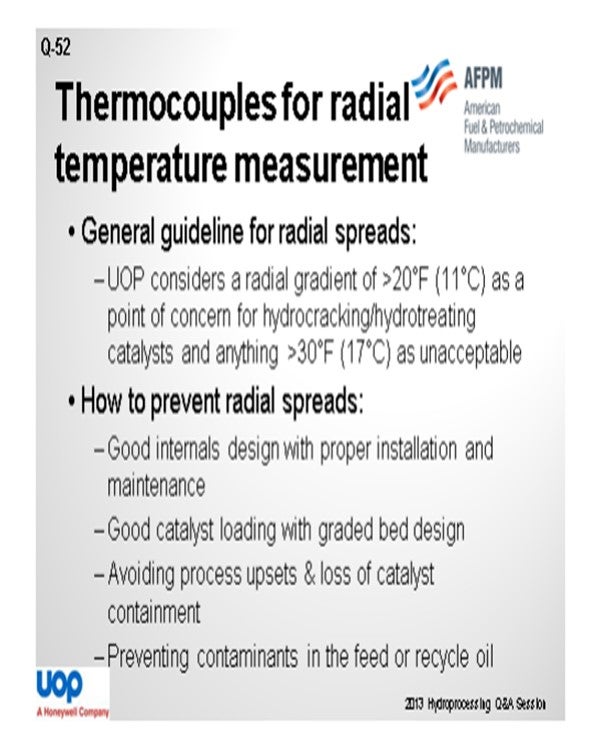
LIOLIOS (DuPont Clean Technologies)
Configuration of thermocouples at the top of the bed are effective for evaluation of quench and distributor performance. When placed in the top, middle, and bottom of the bed, they are used to evaluate catalyst activity and flow distribution. Point density, of course, depends on the application. Higher density is required for systems prone to coking and which require a very uniform flow for successful operations, such as hydrocracking or ultra-low sulfur diesel. Lower density is also necessary for less severe applications. The 2005 AFPM Q&A transcript has a lot of valuable discussion on point density. A flexible thermometry can be arranged to provide the appropriate number of points in almost any geometry at different bed elevations. In any case, an open area of approximately 36 inches in diameter is recommended.
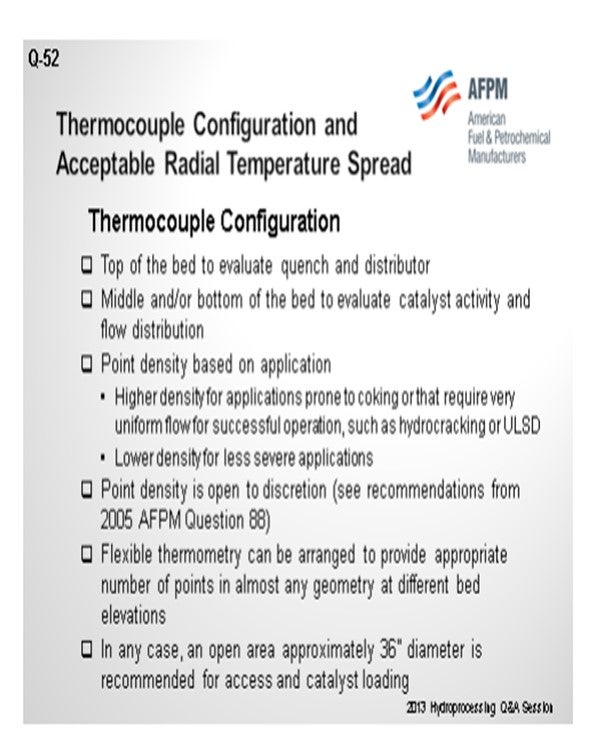
The acceptable radial temperature spread of 5°C is typical for good operation of the trickle bed. For a liquid-phase hydroprocessing reactor, the radial temperature spread is lower due to the heat sink of the recycled liquid. Typically, we experience about 5°F as a maximum radial temperature spread.
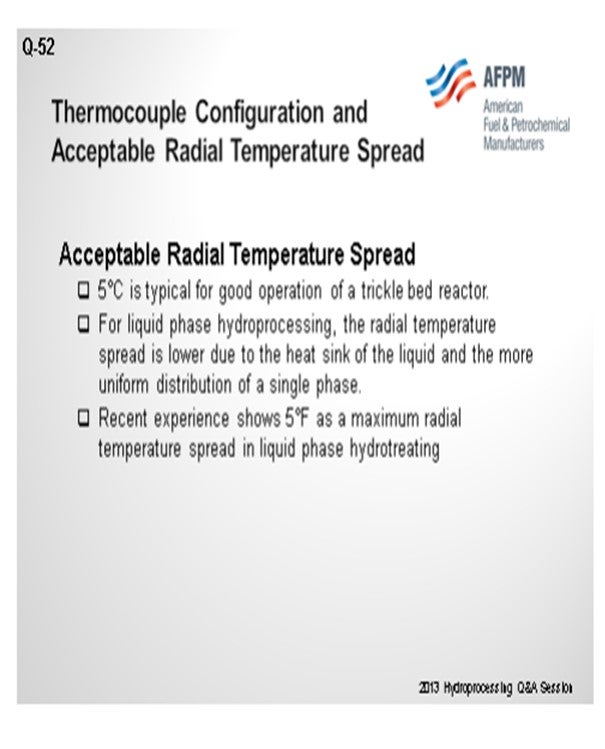
This graph shows an example of thermocouple configuration and acceptable radial temperature spread. It was derived from a liquid-full reactor with 12 thermocouples and two concentric rings and basically shows very uniform and comprehensive fuel temperature differences in the radial change in FCC pre-treat service.
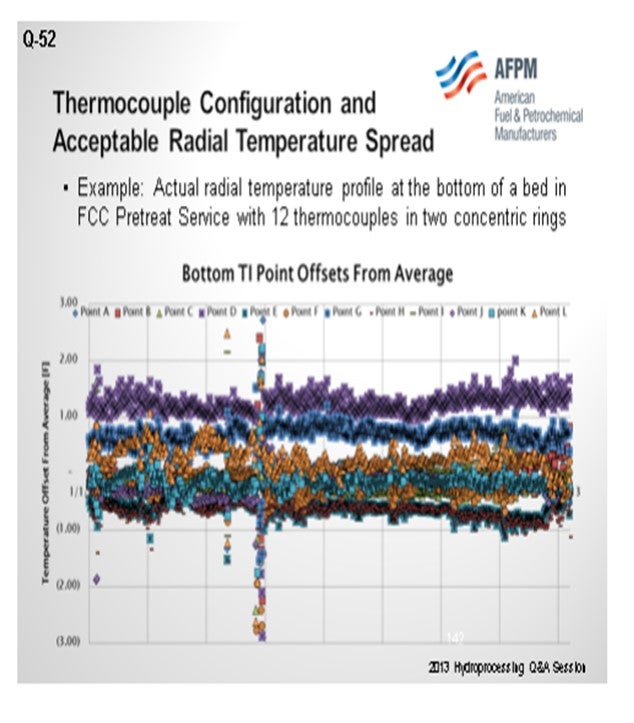
VICHAILAK (Marathon Petroleum Corporation)
From the picture, you can see that we require 6” below the top, as well as 6” both at the bottoms and one-third of the bed and then two-thirds of the bed. These are the minimum readings per ring, which add up to nine readings. The radius of the ring has to be two-thirds of reactor radius. If you have high severity like in a hydrocracker, then you will have an additional four skin thermocouples at the bottom of each bed, too. Also, we add another ring at the very bottom and one more thermocouple in the middle of the reactors. The more you add thermocouples, the more information will be available to you.
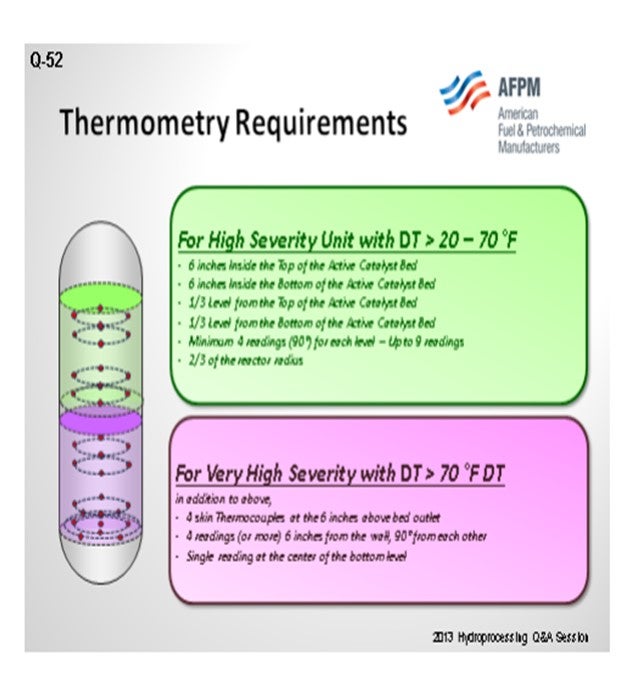
We have one reactor that did not have enough thermocouples. Once added in, we started seeing new information, and people were not able to sleep. A hot side is normally a dry side because liquid is a very good heat sink. If you have a dry side, then you see that the temperature will be higher. We normally require 10°F as it is considered normal radial ∆T. But if you do not have axial ∆T, you should not have radial ∆T; nor if you have 10°F or 20% of axial ∆T, whichever is lower. Thirty degrees is considered the normal maximum probably for as long as you have quench. For example, if you have a 60-foot catalyst bed and 30°F at the bottom, there is no way you will be able to quench as well; so that scenario can be considered severe. But if a temperature of greater than 50°F is not acceptable, we will shut down and replace the bed.
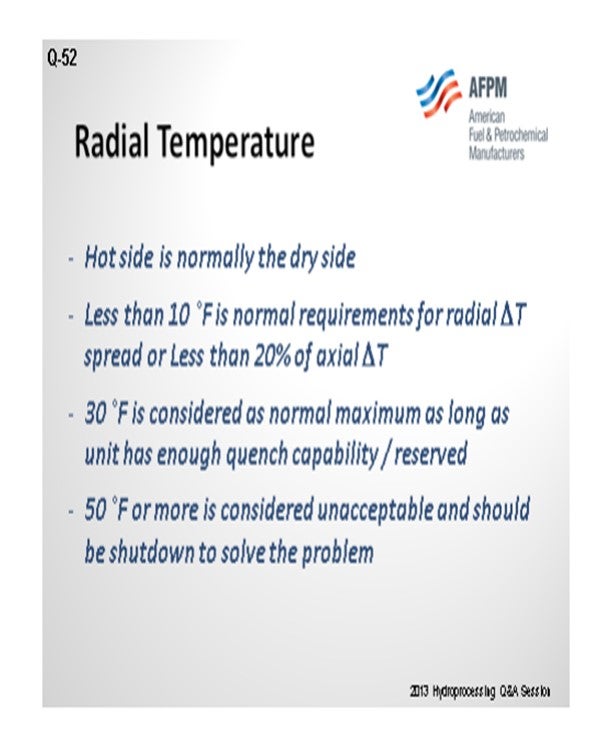
RAJESH SIVADSAN (UOP LLC, A Honeywell Company)
UOP bed thermometry typically contains a stab-in-type assembly with three thermocouples at the top.
For hydrotreating beds, mid-bed thermometry for the first bed is provided and not included in any other hydrotreating beds. Mid-bed thermometry is also provided for long cracking catalyst beds (greater than 11 feet).
The thermocouples at the bottom of bed are specified as industry standard flexible multipoint thermocouples. A typical Flexible Multipoint Sheathed Thermocouple arrangement is shown below.
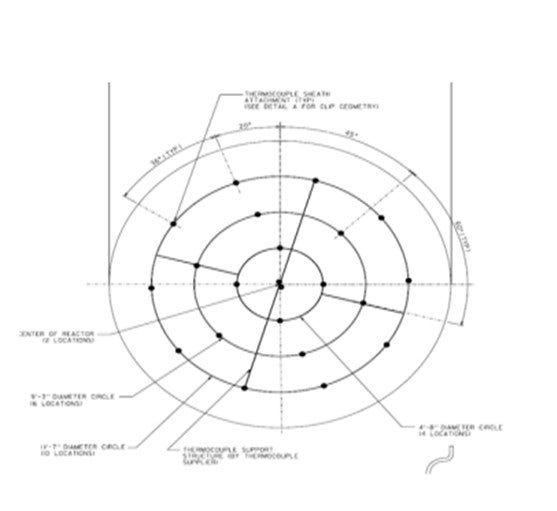
The radial temperature profiles are monitored at the various levels in the reactor and are the primary indicator of flow distribution within the catalyst beds. Radial temperature differential is defined as the difference between the maximum and minimum temperatures at the same elevation. Ideally, the thermocouples at the same level should read the same temperature. The bulk of our experience suggests that most Unicracking™/Unionfining™ units do have fairly uniform radial temperature profiles in the catalyst beds. However, less than perfect distribution of reactants in the catalyst beds can occur. This may be due to improper catalyst loading, damage to reactor internals, or the reliance on older reactor designs with deep catalyst beds and older internals. Consequently, the temperature of the fluids leaving the catalyst bed at different locations can vary.
As a general guideline, a hydrocracking/hydrotreating catalyst radial gradient greater than 20°F (11°C) is considered by UOP to be high and a point of concern, while greater than 30°F (17°C) is considered unacceptable. In order to prevent radial gradients, there should be a perfect distribution of reactants in the catalyst beds, and this can be obtained by:
• Good internals design,
• Proper internals installation and maintenance,
• Good catalyst loading,
• Appropriate graded bed design, and
• Avoiding process upsets by
o Preventing contaminants in the feed or recycle oil (particulates including iron sulfide, organic iron) and
o Preventing loss of catalyst containment (usually leads to hot spots or temperature excursions and pressure drop buildup).
MONTRI VICHAILAK (Marathon Petroleum Corporation)
For a high severity unit with ∆T > 20°F to 70°F, the following parameters are recommended:
- 6 inches inside the top of the active catalyst bed,
- 6 inches inside the bottom of the active catalyst bed,
- 1/3 level from the top of the active catalyst bed,
- 1/3 level from the bottom of the active catalyst bed, and
- minimum 4 readings (90°) for each level: up to nine readings at 2/3 of the reactor radius
For a very high severity unit with ∆T > 70°F ∆T, in addition to the above suggestions, you will need:
- Four skin thermocouples at the 6 inches above bed outlet,
- Four readings (or more) 6 inches from the wall, 90° from each other, and
- A single reading at the center of the bottom level.
Flow maldistribution can be detected by observing the radial temperature differences. The hot side is almost always the dry side. We prefer to see any radial ∆T is less than 10°F or at most 20% of axial ∆T. Radial ∆T of 30°F is considered as normal maximum as long as unit has quench capability or reserved. Radial ∆T of 50°F or more is considered unacceptable and should be shutdown to solve the problem.
GLENN LIOLIOS (DuPont Clean Technologies)
Prior responses to this question [from the 2005 NPRA Q&A by Krause (Albemarle Corporation), McGrath (Foster Wheeler USA Corporation), and Spearman (Barnes and Click)] give good recommendations for the thermometry layout.
Thermocouples are useful in determining performance of the quench and distributor at the top of the bed and catalyst activity and flow distribution at the middle and/or bottom of the bed. Radial deviations can help troubleshoot issues inside the reactor that can influence the operation of the unit.
Using flexible thermocouples, radial arrangements in different geometries can be created at any bed level desired. Sufficient thermocouples at a particular level to monitor any process deviations are recommended; however, the exact number is open to discretion. A higher density should be used in applications that are prone to coking or where very uniform flow is required to achieve process goals. A lower density can be used in simpler applications. In any application, an open space of approximately 36” diameter should be left in the center of the reactor to allow for access and catalyst loading.
In IsoTherming® liquid phase hydroprocessing, the radial temperature spread is typically low, as the heat sink of the liquid and the more uniform distribution of single-phase hydroprocessing avoids hot spots and the associated temperature gradients. A point density on the low end of the scale should be considered. Regarding acceptable radial temperature spread, a maximum of 5°C would be typical for a trickle bed with lower spread as reported for state-of-the-art internals from some licensors. Recent experience shows 5°F as a maximum (with 2 to 3°F typical) in liquid phase hydroprocessing.
DAN MORTON (Haldor Topsøe, Inc.)
We recommend use of the new flexible thermocouples in a ring pattern at the top and the bottom of each bed.
Top Layer: Two to four sensing points are required. This is enough sensing points to be sure that interbed and inlet stream mixing is sufficient. These points are located on equally spaced intervals, each at 70% of the diameter at 50 mm below the bottom of the inert layer. Also, preferably they are not directly below a “dead” spot like dump tubes, beam, etc. in the bed above. Access down through the center of the reactor – from manways, for example – needs to be considered on smaller reactors. Keeping the points as far from the manways as possible also limits the possibility of damage during a turnaround.
Middle Layer: This is at the client’s discretion or optional if the catalyst bed is higher than 5 meters (about 15 feet). If so, there should be four sensing points, with the same considerations as above, midway between the other sensing points. Adding thermometry in the middle of the bed is not a must, but it will provide additional information flow maldistribution.
Bottom Layer: This is a ring of sensing points near the reactor wall and in the middle which are located 50 mm above the bottom inert layer. The number of points here increases with the diameter. For small reactors less than 1.8 meters, we recommend four in the outer. There is no need for inner points as the reactor is so small. For 1.8-to-3.0-meter diameter reactors, we recommend configuration of four inner and four outer points. For diameters greater than 3 meters, we see as many as four inner and eight outer points. The middle ring diameter should be selected so that each sensing point covers a reactor cross-sectional area of equivalent size. We have a formula which we use to determine this, again, also keeping a minimum distance from the manways. The flow distribution through the bed is considered good if the radial temperature spread at the bottom is less than 20% of the axial ∆T across the bed.
For hydrocracking reactor beds, we will recommend a similar scheme but will add more temperature points for additional safety.
ROBERT TORGERSON and SYDNEY GARRETT (Gayesco International)
It is most common these days to find the modern flexible thermometry in the active catalyst, and the use of pipewell designs has really diminished over that past decade in hydroprocessing applications. This is due to the modern flexible thermometry designs allowing for a much quicker response time and more measurement points and locations.
The number and placement of points is always a Process/Engineering decision. As a multipoint manufacturer, we do see a wide variation in number and location of points specified. Generally, the greatest emphasis has been on bed outlet temperatures. Bed inlet temperature requirements have been increasing over the past 10 years, especially where new reactor internals are being used. The use of mid-bed temperature measurement has been limited. In hydrotreating, we see that most applications require a thermocouple to cover between 10 and 25 ft2 of cross-sectional area. In hydrocracking where the service is more difficult, we see the thermocouples covering between 2.5 and 15 ft2 of a cross-sectional area.
In any case, one of the most critical ways to successfully utilize radial temperature measurement information is to know the exact accuracy of that data. Calculating true factory calibrations of actual individual sensors is a good Best Practice for new units, and field verification is essential for existing units that may have seen years of service. This eliminates any questions about sensor variation and its effect radial temperature spread.
ROBERTSON (AFPM)
Those are the responses from the panel. Before we get to the last Hydro question, I want to remind you that there is a P&P (Principles & Practices) session tomorrow at 8:00. The topics and presenters are listed in the program. If you have a subject that was not discussed in this forum, tomorrow’s P&P session is a great place to bring it up to the group. It will be an open session. The subjects listed in the program are discussion starters, as you know if you have attended in the past. The P&P is a good place to get more information or have more one-on-one/back-and-forth if you would like.