Question 50: Chemical cleaning of towers and vessels prior to entry is being used to reduce time to entry. What practices are you employing and how much time is saved?
Eric Thraen (Flint Hills Resources)
Our chemical cleaning practices for Crude/Vacuum and Coking units have evolved over many years. The starting point in most cases, after feed is out and the unit has circulated down, cooled and pumped out, is a flush with diesel or LCO followed by a good steamout. A good steamout helps to eliminate residual oil adhering to metal surfaces and also helps eliminate pockets of oil trapped in piping low points. A good decommissioning closed piping and slop containment system is essential to ensure this residual oil is removed before beginning the subsequent chemical cleaning steps. In a small number of units, the decommissioning piping is a permanent facility but, in most cases, this decommissioning piping consists of temporary piping installed at grade level prior to shut down. A system of piping, pumps, and temporary cooling exchangers is needed along with the ability to route uncondensed hydrocarbon vapors and steam to the flare. Often this is integrated with the unit or area flare knockout, with the added ability to pump recovered oily steam condensate to closed temporary storage “frac” tanks. Care must be taken to segregate the recovered chemical cleaning condensate to prevent contamination of the sour water system and to prevent high chemical flowrate to Waste Water Treatment Plant. The chemical cleaning condensate is later processed through the refinery’s WWTP in a controlled manner staying within the WWTP’s load capabilities.
The decommissioning piping is also used in the chemical cleaning step that follows initial steamout. Generally, the lighter oil sections of fractionating towers and related piping and exchangers are vapor-phase cleaned, whereas the reduced crude and heavier sections are water (liquid) – phase cleaned. The liquid-phase cleaning is simpler to plan than the vapor phase cleaning but can produce larger amounts of wastewater to process. The vapor-phase cleaning also has the advantage of the higher temperatures employed during steaming. Without under-appreciating the value of the chemical cleaning agents, the extended steamout required for vapor-phase cleaning would in itself provide better oil and gas removal than the cleaning provided by simple short steamout decommissioning plans that were used many years ago.
The chemicals employed include detergents/degreasers to remove oil and degas equipment, followed by oxidizing agents (permanganate) to greatly reduce the potential for iron sulfide deposits smoldering when equipment is later opened.
The times required for chemical cleaning vary depending on the size of the equipment and the complexity of the piping systems involved. Care must be taken to not recontaminate parallel systems after they have been cleaned. Generously sized decommissioning piping and generously sized exchangers for condensing and recovering oily condensate are essential to ensure good equipment drainage. Failure to adequately drain condensate formed during vapor phase chemical cleaning can cause liquid barriers to collect in piping system low points including low points found at rack piping expansion loops, piping manifolds, exchanger piping and other piping low points. Preventing this liquid buildup will save much time trying to deinventory, again, large complex piping systems. The ability of the boiler house to provide adequate steam for vapor phase cleaning needs to be considered. Generally, the vapor/steam-phase cleaning will require sustained steamout rates approaching the peak rates used in simple steamouts.
Ralph Goodrich (KBC Advanced Technologies, Inc.)
KBC has a Reliability, Availability, and Maintenance (RAM) consulting group that provides among other services a Turnaround Optimization Program. This program and corresponding support services are designed to help clients in optimizing the various stages of turnaround preparation and execution activities. This includes the need to optimize a turnaround duration, part of which is equipment cleaning in preparation for vessel entry for inspection and maintenance work.
It is our belief that implementing a comprehensive chemical cleaning program using today’s “Best Practice” technology should be an integral part of ensuring a safe environment for workers while at the same time reducing the time for equipment cleaning prior to vessel entry. Current leading-edge technology includes vapor-phase chemical cleaning agents which can be injected through a steam source. Advantages of the vapor-phase application typically include faster clean-out times, less waste, and the ability to contact all surfaces. We have found that the proper application of state-of-the-art cleaning and decontamination chemicals can reduce the clean-out time significantly.
For example, our experience has shown that using latest chemical cleaning technology for crude units we can expect up to 2-3 days can be saved from more historical cleaning methods. A single large vessel such as a vacuum column or coker fractionator can typically see up to a 2-day savings. Also, since the unit is normally much cleaner compared to historical cleaning methods, the maintenance effort becomes more efficient as significant post cleaning is not necessary and the inspection and maintenance activities can start much quicker than when utilizing traditional cleaning practices.
An example of how the improved cleanliness can make the maintenance easier and reduce costs is provided by a major refiner who recently decided to make a significant improvement in their vessel cleaning procedures. This included using a “new” vendor, whom they selected after an extensive evaluation process to improve their cleaning strategy and execution for a large vacuum column. Not only did they reduce the cleaning timeline by two days, but the resulting cleaning was also so complete they were able to cancel plans to replace the packing. The savings from that alone was worth over 3MM$ and saved two weeks of turnaround time. The two photographs at the end of the text indicate the post cleaning state of the column internals.
As a final point, we would recommend performing at least a short HAZOP or MOC review before conducting any new chemical cleaning procedure. It is also important to utilize an experienced vendor and to work closely with them throughout the entire process, from initial planning including modification of shutdown procedures to incorporate the nuances of the chemical cleaning process through final execution to help ensure a safe, successful, and on schedule equipment clean-out.
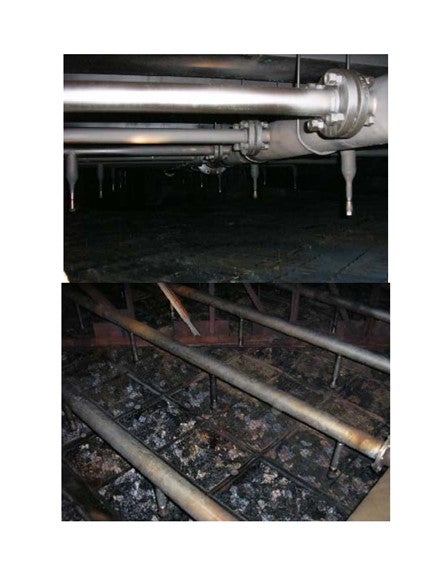
Jim Johnson (Marathon Petroleum)
Our decontamination procedures and practices have evolved over the years with the crude and vacuum units utilizing chemical cleaning to prepare the equipment for maintenance. One of our refineries has developed a practice that concentrates on flushing the residual oil from the system prior to addition of chemical resulting in a more effective chemical cleaning.
1.Rather than installing drain piping throughout the unit to tie into the slop system, all oil is water flushed to the crude or vacuum column where the water is subsequently drained to the sewer and the oil is pumped to the slop tanks utilizing the existing bottoms pumps.
2.The entire crude pre-heat and column side-draw circuits are water flushed to the column, with fire water connected to the appropriate pump suction. This provides a clean water flush rather than circulating oily water from the tower.
3.The chemical cleaning step follows the cold-water flush. On the crude unit water is circulated from the pre-flash tower through the heater and back to the pre-flash tower using the main fractionator bottoms pumps through the start-up circulation piping. The heater outlet is brought up to 250 degrees. Chemical is injected into each of the product draws and the water flush of each circuit is resumed. 4.After the water circulation, fresh water is used to flush the pre-heat exchanger circuit to the tower where the water with chemical and any recovered oil is pumped to storage to be processed through the WWTP later at a controlled rate.
5.As the side draw circuits have been water flushed, the water can be drained from all low points directly to the sewer without a detrimental effect to the WWTP.
6.The unit is then steamed out with steam introduced at the heater coils and at multiple locations on the column. The heater is re-lit with the outlet increased to 500 degrees for a final unit steam–out.
7.After verifying the unit is hydrocarbon free through ‘bomb tests and lab GC the tower is rinsed with cold water. An oxidizer is also used to reduce the potential for iron sulfide deposits to smolder.
Gregg McAteer (Nalco Company)
We are applying cleaning chemistry to towers and vessels and cutting normal steam-out time by approximately 2/3. The tower or vessel is then clean and saves further cleaning time so repairs can begin immediately.