Question 5: What are the typical dispositions of coker olefins, light coker naphtha, and heavy coker naphtha in refineries that you employ? How are the sulfur contaminants, such as dimethyl sulfide and dimethyl disulfide, best removed from these streams?
HUTCHINSON (Axens North America)
This question asks about the fate of coker olefins and coker naphthas. What we are looking at here are the three coker product streams, which include coker LPGs (liquefied petroleum gas), your C3s(propane/propylenes) and C4s (butane and butylenes), and light and heavy coker naphthas, which must be further processed before they can be blended or sold into the gasoline pool. Coker products are really a challenging feedstock. They are rich in sulfur, nitrogen, olefin, and diolefins and contain other contaminants including arsenic and silicon. What I have provided for you here on the slide is a comparison of a typical straight-run naphtha and typical cracked refinery naphthas, light coker naphtha and heavy coker naphtha, and FCC naphtha. What you can see is that there is significantly more sulfur and nitrogen, and also some other contaminants including silicon and arsenic, in the cracked naphthas. However, the octane is relatively good, especially in the light coker range.
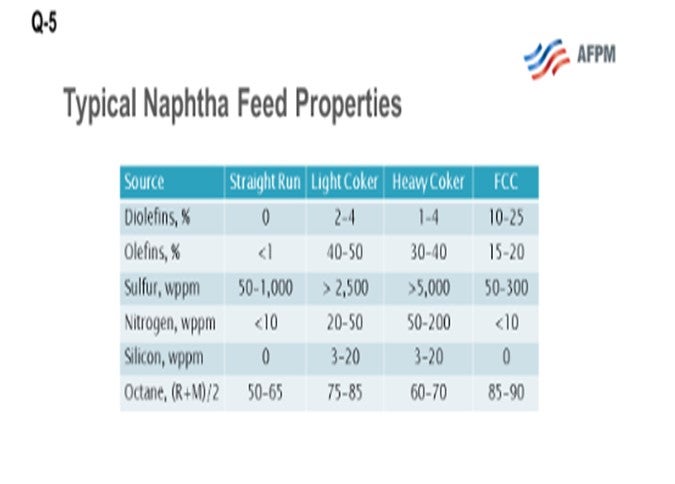
The coker LPGs typically get blended with the FCC LPGs, both in a common or a separate gas plant. They are then upgraded to motor fuels in the same manner as FCC olefins: either through an alkylation or Polynaphtha™ process. Alternatively, the olefins might be recovered through fractionation and sold as chemical feedstock. When you co-process LPGs with existing equipment designed to process the FCC, C3s, and C4s, you need to pay particular attention to the potential for arsenic or arsenic contamination.
Both the light and heavy coker naphtha contain diolefins and olefin compounds in relatively high levels compared to other refinery naphthas. The presence of olefins makes the streams particularly difficult to treat in a conventional naphtha hydrotreater. Also, they are very high in sulfur and other contaminants. Diolefins can form gums when heated, resulting in fouling in the feed effluent exchangers. Olefin saturation has a very high heat reaction, resulting in large reactor exotherms. So, if your unit is not designed for high exotherms and severity, it becomes very difficult to treat coker naphtha in a standard straight-run naphtha hydrotreater, especially when you start to process a significant percentage of coker naphtha which may require a quench between reactor beds.
As I mentioned earlier, the high-octane value of the light coker naphtha makes it a good stream for blending into premium gasoline if the octane can be retained during desulfurization and is therefore a good fit for a selective hydrogenation unit, or SHU. The SHU will selectively saturate the diolefins, eliminating the potential for gums while preserving the high-octane olefin. Nearly all the light mercaptans, as well as a substantial portion of the light sulfides such as dimethyl sulfide (DMS), are converted to heavy sulfur compounds. The light naphtha is, therefore, functionally desulfurized and can be split out. If you look at the next slide, you will see an SHU process flow diagram. The naphtha flows through the SHU reactor where the diolefins are saturated and the light mercaptans are “shifted” to heavy sulfur compounds. The SHU reactor product then flows to a splitter where you can remove the light coker naphtha (LCN). This LCN can then be sent to a gasoline blending as a low sulfur component. The heavier portion from the splitter bottom, which includes most of the sulfur after the sulfur shift, is sent downstream to be desulfurized in a selective HDS (hydrodesulfurization) unit. The heavy coker naphtha, which commonly includes dimethyl disulfides, could alternatively be treated in a conventional naphtha hydrotreater and then sent to a catalytic reformer to recover the octane.
The heavy coker naphtha can be a burden for the conventional hydrotreater unit (NHT), especially if the NHT is designed for straight-run materials, as previously mentioned. Coker naphthas are really quite challenging feedstocks because they are laden with impurities and rich in sulfur and nitrogen. The high impurity loads, and more difficult desulfurization and denitrification loads can make this feedstock particularly challenging because typical straight-run naphtha hydrotreaters are not designed to provide sufficient severity. They are typically designed for lower pressure. They do not have the catalyst volume necessary to achieve the target cycle exit you might desire.
Alternatively, the heavy coker naphtha can be processed in the FCC gasoline selective hydrotreater, but with fewer synergies as compared to the light coker naphtha. Depending on the refinery configuration, co-processing of heavy coker naphtha with FCC gasoline can be practical when using Axens’ Prime-G+™ technology. Axens has successfully demonstrated this application in multiple refineries while maintaining normal unit cycle lengths.
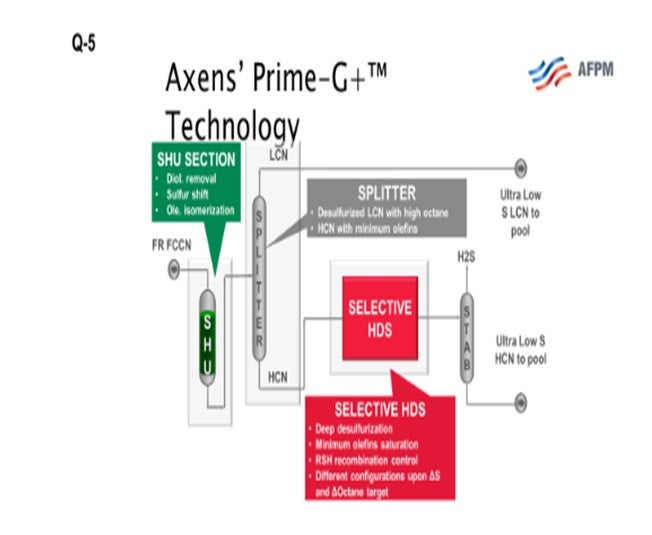
JEFF BRAY and CHRIS ANDERLE (Honeywell UOP)
Coker C3/C4 olefins are usually processed with FCC olefins so that the value of the olefin content is captured. If there is no FCC, these olefins would be hydrotreated and routed with LPG. The coker naphthas (both light and heavy) are typically routed with the straight-run crude naphtha and hydrotreated in the naphtha hydrotreater. Coker naphtha does have olefins that have to be saturated in this unit, as well as having higher nitrogen and sulfur levels; therefore, the NHT (naphtha hydrotreater) requires a more robust unit design. The olefins will generate an increased exotherm that the unit design needs to accommodate to avoid mercaptan recombination. The dimethyl sulfides and disulfides are among the slowest reacting compounds removed in naphtha hydrotreaters, but they can be treated effectively if there is sufficient catalyst volume and pressure, producing naphtha that meets the low sulfur levels needed for reforming or blending. Where naphtha hydrotreating capacity is not sufficient to process this effectively, an alternative is to send it to diesel hydrotreating units. One issue with this approach is that the unit’s separation section needs to be able to recover the naphtha from the diesel. Most coker naphtha is processed in naphtha hydrotreaters. Once hydrotreated, coker light naphtha would go to the same destinations as the straight-run light naphtha including isomerization, gasoline blending, or naphtha sales. The heavy naphtha could go to reforming, gasoline blending, or naphtha sales.