Question 5: Reforming of feedstocks from ‘tight oil’ crudes offers unique challenges such as low naphthene and aromatic (N+A) content, lighter feed, and differences in coke yield.What are refiners doing to address these challenges and generate opportunities for these new crudes?
BULLEN (UOP LLC, A Honeywell Company)
From a project standpoint, there have been inquiries related to tight oil and proposals generated, but not a significant number of actual projects realized for revamping units. It appears that most refiners are able to accommodate the tight oil in their existing units. Some of this accommodation has to do with the naphtha area capacity issues in the U.S. of which I am sure everyone is aware. There are opportunities to change the catalyst types to be a more active type and come up with a more coke-tolerant type catalyst to address the higher coke make you get with more paraffinic feeds.
MELDRUM (Phillips 66)
This whole subject of tight oils or shale oils is interesting. I am not sure there has been an event in the industry that has had as quick and broad of an acceptance as the bringing of tight oils to market. A typical operating company could probably anticipate seeing a doubling (or greater) of their use of tight oils over the next five years from where they are currently processing. Tight oils are typically more paraffinic and lighter than many of the current crude oils. As such, the naphtha cut being fed to the reformer unit from these oils will be leaner and have a lower naphthene and aromatics content. Additionally, the quantity of that cut will increase, which will impact the reformer in all areas of activity, selectivity, and stability, the extent of which depends upon the type and amount of the tight oil or shale crude that is processed.
One of our sites processes 20% of an Eagle Ford crude. They have experienced a 4 to 6- number drop in their naphtha feed quality as measured by the naphthene and aromatic content (N+2A). The process impact was a 1-number drop in the octane number that was offset by adding 4 to 6°F additional reactor temperature to hold the previous octane target. The associated yield decline has been about 1.5 liquid volume percent C5 plus. The coke make is expected to increase by about 10% due to the added severity on the unit. This would then have an associated shorter cycle life to the catalyst from regeneration to regeneration.
Another of our sites processing 35% of Bakken crude has seen a 5-number drop in its naphtha feed quality (N+2A), which has lowered the reformate octane. The additional naphtha from that processing, which is not able to fit into the reformer unit, bypasses the unit and goes directly to fuel blending.
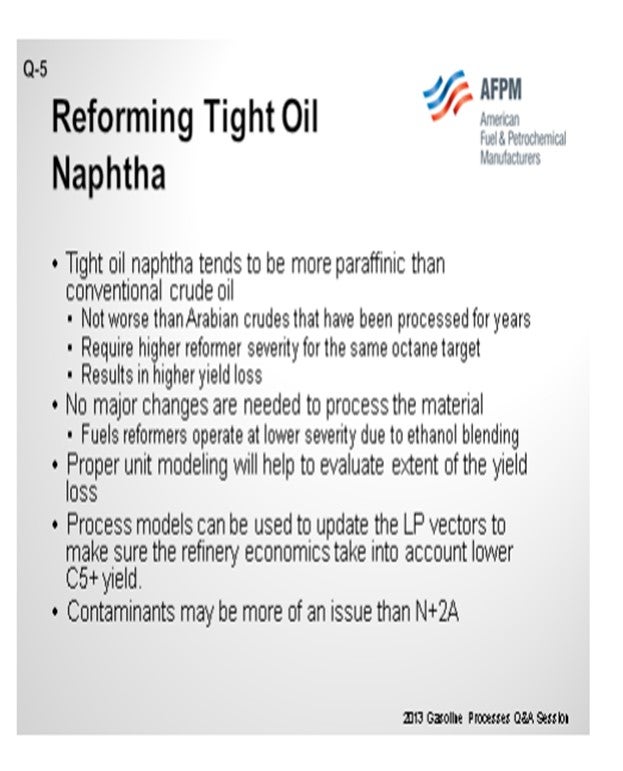
STREIT (KBC Advanced Technologies, Inc.)
I do not have a lot to add, more of a confirmation. We alluded to it in the last question. We make some assumptions or generic statements about tight oil; but in fact, it is a rather broad spectrum. It does tend to be more paraffinic, but it is not, by definition, more paraffinic. It is not really worse than any of the Arabian crudes that have been processed through the years, as far as N+2A. Typically, it will be a little more paraffinic, which means you need a little more severity for the same octane target, as was stated before. This results in a slightly higher yield loss through the reformer; but in general, no major changes are needed to process this material. Because of ethanol blending and the corresponding lack of demand for octane from a reformer, most reformers in the United States now have the room to go up on severity. So, there is likely available capacity to make up for that additional severity that you need.
I want to point out that it is very possible that the LP (linear program) models, which are making the decisions on what kinds of crudes to buy and the economic value of those feedstocks, may not properly reflect the yield loss that you might see from a tight oil. So those LP vectors need to be updated to make sure the LP is up to speed to properly reflect that yield loss. The final point outside of the N+2A or the paraffinicity issue is that there seems to be a lot more contaminants which we have not seen in the past that are showing up, and those may be a larger concern than the actual N+2A or the reformer feed quality.
VICTOR TAILER (Commonwealth Engineering & Construction)
I have a general question. Since the quantity of tight oil processing is going to increase, how does this increase impact delayed coker units which operate at the low pressure, and how will the coker yields will change? How does tight oil processing impact the fractionator operation? Do they need any revamp, or is it done with any equipment modification?
MEL LARSON (KBC Advanced Technologies, Inc.)
If I understand the question correctly, you are asking about the impact of the tight oils that would go through the coker. The issue is going to be with the quantity. We would expect that quantity of material because there is not as much bottoms within 50-plus in the material. In general, for that material, if the Conradson carbon residue content is about the same, we would not expect the yield shift to be too much more dramatic or even the yield profile to be an issue. Most of what we have seen so far in the coking conferences I have attended are strictly hydraulic rate issues about the minimum feed rate. If those change, the coker distillate or coker naphthas will not be too much different than they are today, as far as their properties; only the mass rate will drop quite substantially.
JESUS CABELLO (Foster Wheeler USA Corporation)
What we have seen with some of the clients processing tight oils is some kind of incompatibility between tight oils and conventional oils that is creating issues in the heaters.
TERRY HIGGINS (Hart Energy Research and Consulting)
I have a quick comment on the crude N+A (naphthene plus aromatic content). One of the biggest impacts has to do with the crude oil you are backing out. For example, many people have had to back out Nigerian crude in order to accommodate the excess domestic light crudes. There you have a significant N+A shift. However, it is true that if you start backing out crude oil such as Arabian, you will not see that much difference.
PATRICK BULLEN (UOP LLC, A Honeywell Company)
Refiners are looking at potential options such as CCR (continuous circulation rate) Platforming™ process unit regeneration section revamps to increase coke burn capacity or even catalyst volume increases via reactor additions. Other options include catalyst changes to more active and more coke-tolerant catalysts.
The general activity for revamps is not particularly high for tight oil-related additions presently. Some of the potential reasons for this are the following:
a. Tight oil is difficult to define as the assays vary within the field and over time, depending on the recovery. This difficulty makes long-term predictions and economics harder to calculate. This, in turn, makes projects more difficult to justify.
b. Tight oil in the naphtha range is not too different from some paraffinic crudes, such as Saudi Light, so the general effects are known and can be put into existing systems that may be underloaded.
c. The volumes of tight oil are still growing and being established.
Contaminants vary in tight oil as well due to the unique processing to recover these oils. Combined nitrogen and olefin spikes have been noted by refiners. These types of contaminants tend to require severe hydrotreating similar to that required for coker naphthas.
ERIC STREIT (KBC Advanced Technologies, Inc.)
First of all, reformer feed from tight oil is not any worse than Arabian crudes, which many folks processed for a number of years without major issue. Tight oil naphtha does tend to be more paraffinic and, therefore, makes worse reformer feed than naphtha from most conventional crudes.
More paraffinic reformer feed means higher severity, higher coke makes, and lower hydrogen yield for the same octane. However, in the U.S. and elsewhere, there has been a big drop in reformer octane target (due to ethanol/oxygenates use) on units that are not making BTX (benzene, toluene, and xylene). As a result, there is likely room for handling the additional severity required due to tight oil.
A separate challenge may be due to the various contaminants that might be in the naphtha from various chemicals used in the production field. This may require tighter monitoring of contaminants in the naphtha and better management of the naphtha hydrotreater performance. A particular contaminant that may be present in higher-than-expected concentrations is nitrogen. High levels of nitrogen can result in severe corrosion and fouling in the reformer, so anyone changing crudes should be regularly monitoring naphtha nitrogen content in the reformer feed.
SONI OYEKAN (Prafis Energy Solutions)
First, we know that the cheaper ‘tight oils' or unconventional oils have had the beneficial economic impact of lowering overall average prices of crude slate processed by oil refiners who are favorably positioned to capitalize on processing the tight oils. Within the refineries, there are some processing challenges due to some changes in the compositions of the resultant oil fractions. The challenges with low naphtha N+A qualities from ‘tight oil’ crudes are typically and reasonably managed by co-processing ‘tight oil’ crudes with crude oils that produce more naphthenic naphthas. Via the processing of mixed crude oil slates, total naphtha qualities can be adjusted over a broad range to meet fixed-bed semi-regenerative reformers cycle targets and regeneration frequency schedules if those are of concerns to the refiners. If product selectivity is a concern, moderating the low naphtha quality of such oils via co-processing with crude oils that produce naphthenic naphtha would also aid in improving product selectivity.
In the case of CCR reformers that are being operated with low coke naphtha reforming operations challenges, the lower N+A quality of the total naphtha feed is a bonus for the reformer as that would lead to increased catalytic coke make and aid in maintaining steady-state, complete, continuous catalyst regenerator operations at constant reforming process conditions. By complete regeneration, I mean that due to the higher coke make as a consequence of reforming lower N+A, quality naphtha could lead to steady-state white burn operations and full catalyst regeneration and redispersion of the metals in reforming bimetallic catalysts. Therefore, in the case of a continuous catalyst regeneration reformer, the reforming of lower N+A quality naphtha at constant reforming process conditions could aid in optimizing the reforming operations of the previous low coke reforming operations and non-steady-state catalyst regenerations and activation. All of the above could help minimize some of the reformate octane barrel losses from processing a more paraffinic naphtha from ‘tight oils’ crudes.