Question 5: Is the presence of pyrophoric compounds common in feed/effluent exchangers? What neutralization methods do you employ prior to exposing the equipment to the atmosphere?
SABITOV (Phillips 66)
I would like to start by saying that reforming units operate with very low sulfur levels. Typically, reformer feed sulfur is less than one ppm (part per million). Therefore, reformers would fall under the area of low-risk units, with respect to the presence of pyrophoric compounds, compared to, say, hydrotreaters. If we see any issues with pyrophoric compounds, they would be typically encountered more when handling spent catalyst or spent catalyst dust such as the CCR dust collector product.
We did a survey of our sites; and in general, our reformers do not really have issues with pyrophoric compounds in their combined feed effluent exchangers during turnarounds. The same survey also showed that we seem to have two groups of units. The so-called clean units just go ahead and open their CFEs (combined feed exchangers) after conventional nitrogen sweep; so, really no issues. And then, we have the other group of units where they do see black sludge on the effluent side of the CFEs. That material typically represents some mix of PNAs (polynuclear aromatics), ammonium chloride salts, catalyst dust, iron scale, and potentially iron sulfide. The key for handling those cases is to be aware of the pyrophoric component presence. If a preventative action is needed, wetting those deposits with water would be a basic mitigation technique.
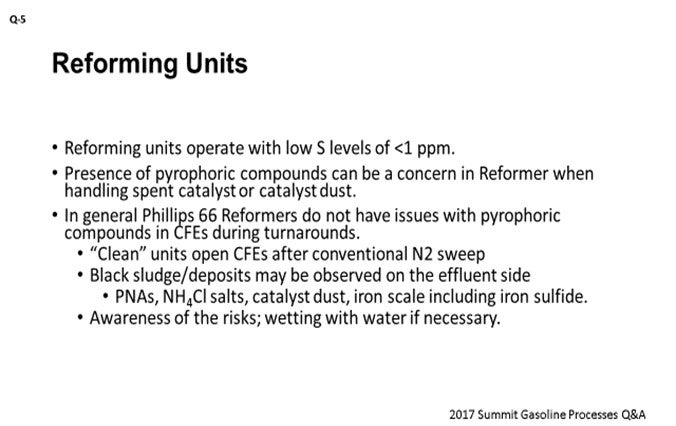
Those units with a history of the exchanger fouling would open their exchangers for turnaround only after performing the cleaning step. Therefore, the risk of pyrophoric material is greatly reduced. We use various cleaning techniques for the exchangers. For those exchangers that can potentially be sensitive to the chloride corrosion attack (such as a Packinox stainless steel bundle), we do a water-wash with the soda ash solution to neutralize the chlorides before those exchangers can be open to the atmosphere. Low-alloy or carbon-steel CFEs have been steamed out or cleaned using a combination of steam and the chemical injection, which is basically a mix of enzymes, surfactants and the oxidizers. I should note that after those cleaning steps, there have been many cases where we still have observed PNAs on the effluent side. Typically, a separate aromatic solvent circulation would be required to remove those PNAs. Our semi-regen units typically open up CFEs after the carbon-burn step of the catalyst regeneration and really do not make any special cleaning provisions for opening.
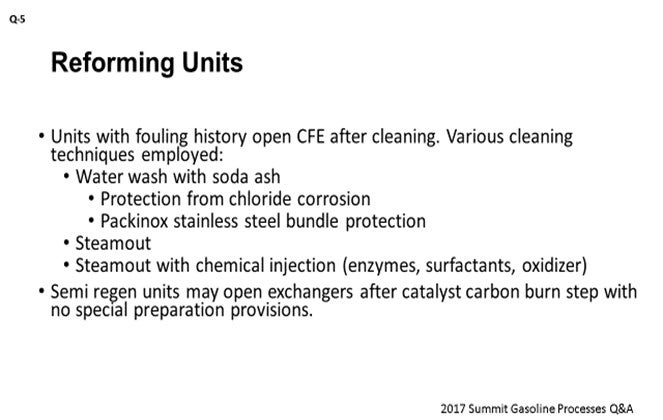
SHARON (Valero)
Alex answered this question well. Our experience is similar, so I just want to add a few points. As Alex said, you should always assume pyrophoric material is present. We concur with Alex’s statement that you can also primarily see these materials in hydroprocessing units. Also, the higher the severity, the higher the risk of HPNAs (heavy polynuclear aromatics) being present.
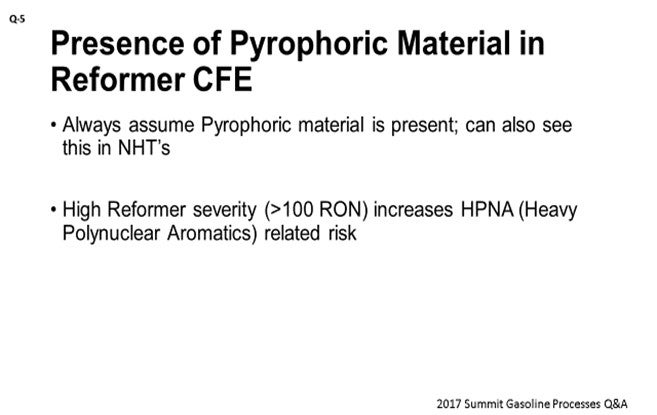
SUGG (Honeywell UOP)
This question could also be about the naphtha hydrotreater unit’s feed effluent exchanger. On this topic, it is generally sufficient to water-wash the hydrotreater feed-effluent exchanger prior to exposure to air. However, if there is a concern or a previous history with iron sulfide fires, we know of others in the industry who have used methods that include strong oxidizers such as potassium permanganate, percarbonate, and peroxymonosulfate. A qualified cleaning contractor experienced in this work could provide more details. I think the rest of it has been covered.
STEVE PHILOON (Honeywell UOP)
In 2015, UOP led a Principles & Practices session on the topic of NHT (naphtha hydrotreater) and reforming unit feed/effluent exchanger fouling and cleaning.
In Honeywell UOP Platforming™ units of both CCR and SR types, the feed/effluent exchanger or combined feed exchanger (CFE) is generally a clean service. There are occasionally problems with feed-side fouling due to peroxide gums, coke or iron scale, or reactor effluent-side fouling due to ammonium chloride salts or polynuclear aromatic compounds. It is uncommon to have problems with pyrophoric compounds (most typically iron sulfide) in CFEs. In principle, it is possible for corrosion products and iron sulfide scale to collect in low flow areas of the combined feed exchanger and be a hazard when exposed to air during maintenance. However, in many units, the CFE is washed with water to remove salts before the exchanger is opened to the air. Water does not prevent iron sulfide from reacting with oxygen, but it does reduce the rate of mass transfer so that the rate of reaction is slowed to the point that the exchanger can be opened, and the material removed before a problem occurs. Also, in semi-regen units, a coke burn is generally done before the unit is opened for maintenance. While this does not remove all of the iron sulfide, it may reduce its concentration.
Note that the most common location of problems with pyrophoric material in CCR units is with the dust removed from fines removal system. Both semi-regen and CCR-type units may experience problems with pyrophoric material during catalyst unloading. That said, UOP is aware of one instance where a fire occurred as the bottom head of a vertical combined feed exchanger was dropped. The refinery reported that hydrocarbon was present due to plugged drain lines, and it suspected that ignition was provided by pyrophoric material. The fire was quickly extinguished without any injuries or significant equipment damage.
NHT units, like all other hydrotreating units, are units where exchanger fouling issues are more common. The feed side of the feed/effluent exchanger may become fouled with peroxide gums or corrosion products from tankage or upstream units. The reactor effluent side may become fouled with ammonium salts, particularly if feeds high in nitrogen are being processed. Because of the presence of sulfur and iron, there is always a concern about pyrophoric iron. When a feed/effluent exchanger train is to be opened for cleaning or other service, it is generally sufficient to water-wash the exchanger prior to changing the environment to air. The wash procedure will easily remove salts and other debris, and the water will provide a layer that reduces the rate of oxygen diffusion and therefore limits the rate of the iron sulfide oxidation reaction. If there is a concern or previous history with iron sulfide fires, over the years, the refining and petrochemical industries have used many methods to treat pyrophoric iron sulfide with various chemicals including strong oxidizers, such as potassium permanganate, percarbonate and peroxymonosulfate. The heat exchanger vendor and the exchanger cleaning contractor may be able to provide a detailed procedure.