Question 5: Does anyone have proven experience using promoted zinc oxide products for sulfur removal upstream of the reforming section? What improvement have you measured in the downstream catalyst performance?
Brian Moyse (Haldor Topsoe)
Topsoe has installed our new promoted zinc oxide product HTZ-51 upstream the reformer section in a number of Ammonia, Hydrogen and Methanol plants. Topsoe’s promoted zinc oxide is also used as a purification absorbent upstream methanator units.
Our promoted zinc oxide product HTZ-51 provides:
•Improved sulphur uptake
•Increased Hydrogenation activity for inorganic sulfur compounds
These benefits will offer the downstream catalyst the best performance and an increase in lifetime as they are protected from both inorganic and organic sulphur.
It can be difficult to get the necessary data from the steam reforming section to verify the benefit of using a promoted ZnO, but we have good data from a purification unit, using HTZ-51 upstream a methanation unit, which clearly shows that HTZ-51 made a big difference. The operating temperature and process conditions are very similar to the conditions upstream a steam reforming application.
The methanation catalyst is also a Ni containing catalyst as is both the pre-reformer and reformer catalyst. The benefits described below will thus be similar to those obtained for pre-reforming and reforming catalysts.
Prior to installing a Topsoe promoted zinc oxide a plant was operating with a non-promoted zinc oxide upstream the methanation catalyst. The plot in Figure 1 clearly indicates that there is a severe deactivation of the methanation catalyst as indicated by the fall in temperature across the bed. Both the non-promoted zinc oxide absorbent and the methanation catalyst were changed out frequently.
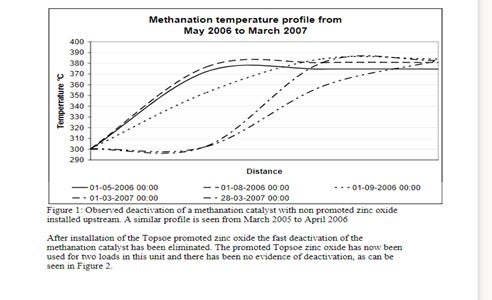
Figure 1: Observed deactivation of a methanation catalyst with non promoted zinc oxide installed upstream. A similar profile is seen from March 2005 to April 2006.
After installation of the Topsoe promoted zinc oxide the fast deactivation of the methanation catalyst has been eliminated. The promoted Topsoe zinc oxide has now been used for two loads in this unit and there has been no evidence of deactivation, as can be seen in Figure 2.
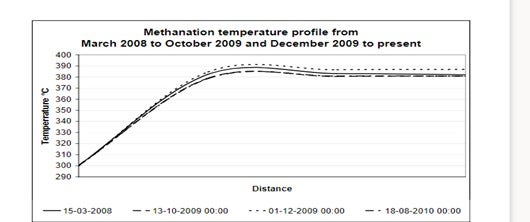
Figure 2: Observed stability of a methanation catalyst with promoted zinc oxide installed upstream.
Thus by installing a Topsoe promoted zinc oxide it is possible to offer the best protection for the downstream nickel catalysts such as prereforming catalysts, steam reforming catalysts and methanation catalysts.
Randy Peterson (STRATCO)
The type of feed is very significant for T90. Amylenes make alkylate with higher T90 in both sulfuric and HF units. Propylene generally makes lower T90 than butylene in HF units. However, with sulfuric-catalyzed technologies, propylene can increase T90 as discussed below. Diene contaminants (butadiene and pentadiene) also raise T90 for both catalysts since they form heavier alkylate. Selective hydrogenation units that remove dienes are therefore helpful in reducing T90.
In sulfuric alkylation, propylene reacted with butylene and especially amylene in the same reactor will lead to higher T90s than if they were alkylated separately. This is due to side reactions that produce heavier alkylate. Therefore, segregated feed systems where different olefins are fed to specific acid stages are beneficial. Normal olefins have lower T-90 and End Points relative to isoolefins. Thus, MTBE/TAME raffinate has lower T-90s than mixed butylene's/mixed amylenes.
For a given feed type in sulfuric alkylation, I/O ratio is the most critical process variable. The lower the I/O, the higher the T90. Low acid strengths also increase T90 so acid staging should be designed to minimize the fraction of alkylate produced at the lowest acid strength.
For HF alkylation, low I/O ratio is also the most significant variable causing increased T90. Acid strengths above 90-92 wt% increase EP and T90 due to the higher activity of the catalyst and tendency for polymerization. Low acid strengths (below 87 wt%) also tend to increase T90 due to increased side reactions and increased acid carryover in the iso recycle. Excessive internal acid regeneration can raise EP/T90 as well.
Higher reactor feed nozzle ΔP and/or increased reaction zone mixing reduce T90 for both catalyst types.
Jamie Chisamore (Johnson Matthey Catalysts)
Feedstock purification is a key unit operation in any Hydrogen plant that employs steam reforming technology. Feedstock purification products are used in hydrogen plants to remove poisons that can affect the performance of downstream catalysts and hardware. The most common catalyst poisons experienced are sulfur compounds present as hydrogen sulfide (H2S), COS, mercaptans, organic sulfides and disulfides, and thiophenes. The key catalysts in hydrogenplants that may be poisoned by trace components in the feed gas are pre-reforming, steam reforming, and low temperature shift. Purification systems are typically designed for a sulfur slip of 0.1 ppmv H2S slip into the steam methane reformer section of a plant at end of run. A traditional purification system containing a sulfur removal system with a hydrodesulphurization bed followed by a zinc oxide based H2S removal absorbent bed, such as KATALCOJMTM 41-6T followed by KATALCOJM 32-5, is sufficient to achieve the necessary design level of sulfur removal levels to protect the downstream catalysts.
Analysis indicates that the total sulfur level exiting the zinc oxide absorbent is typically a few tens of ppb comprising of H2S, COS and traces of organo-sulfur species. The precise levels and mix vary as a function of the feedstock composition, operating conditions and effectiveness of the purification products installed. This low level sulfur slip can still have a negative impact on downstream catalysts for example, if the plant has a pre-reformer or a highly stressed top fired reformer since these are both particularly sensitive to sulfur poisoning. To maximize the catalyst life in these downstream units, Johnson Matthey Catalysts recommends the use of an ultra-purification catalyst, PURASPECJM2084, as a final stage in the purification system. This reacts with and removes the trace sulfur compounds typically to levels below 10 ppbv.
An additional option available from Johnson Matthey Catalysts is KATALCOJM 33-1, which is a unique 3 in 1 purification solution that combines the 3 functions of hydrodesulfurization, H2S removal, and ultra-purification (total sulfur slip less than 10 ppbv) in a single product. This allows simplification in the design, installation and operation of the feed purification system and extends the life of the downstream catalysts.
KATALCOJM and PURASPECJM absorbents use granulation technology to produce spheres with the required combination of properties to maximize the effectiveness of the sulphur absorption in the differing designs for purification beds. These products have been used successfully in many plant operations to improve downstream catalyst performance. For example, a syngas plant suffered from a poorly operating purification system that slipped sulfur to the primary reformer. In order to continue operating, the plant shut down regularly to steam the primary reformer and remove the sulfur. Replacing the purification system with KATALCOJM purification products eradicated the problem saving the plant operator just over two million dollars each year. In another example, when PURASPECJM 2084 was installed on a plant in combination with the traditional sulfur removal system, it resulted in doubling the life of the steam reforming catalyst. This saved the customer over $ 400,000 in replacement catalyst costs.