Question 49: As the demand for higher octane gasoline components increases and lobbying for a 95 RON gasoline standard continues, how are you adjusting your operations to meet the market demand? What FCC specific changes do you make to produce higher octane gasoline components?
SAEED ALALLOUSH (Saudi Aramco)
Catalyst
Reaction severity
Olefin content (with some limitation) by Increasing the naphtha cut from the fractionation column.
TIFFANY CLARK (BASF)
Refiners are optimizing their gasoline blend components to maximize high octane components. Alkylate and reformate yields are becoming increasingly important, as well as minimizing low octane component yields. The emergence of tight oil feeds has created an increase in low octane natural gasoline and LPG saturate production.
While some operational changes, such as raising the riser outlet temperatures, may seem like an obvious response to increase the gasoline octane, current economics in the U.S. penalize incremental production of dry gas due to its big discount to crude and other product slates; they limit octane gain via higher riser outlet temperature. Not only this, increase dry gas production limits Wet Gas Compressor throughput, which is a typical FCC constraint.
On the other hand, base catalyst reformulations that promote production of higher-octane gasoline and more LPG olefins production to increase the feed to the alkylation unit have become mainstream. Opportunistic usage of ZSM-5 and other butylene-increasing additives have become an important avenue for FCCs to increase the amount of high-octane gasoline blending components via alkylation. They also increase the octanes of the remaining gasoline as an added benefit.
MICHAEL TALMADGE (Johnson Matthey)
Many refiners are adding ZSM-5 and C4-selective additives to the FCC catalyst inventory to maximize FCC-derived gasoline octane. Gasoline octane is increased with these zeolite components from the following yield-shifting mechanisms in the FCC:
- These additives crack straight chain C6 - C10 molecules, which are low-octane, gasoline-range components. Therefore, gasoline octane is increased when these molecules are cracked to smaller molecules and the higher-octane molecules are increased in concentration.
- The additives also possess isomerization activity, which converts remaining straight chain gasoline-range molecules to higher-octane, branched isomers.
- With the resulting increase in C4 (and C3) olefins and iC4 resulting from selective cracking and isomerization reactions, the potential for producing high-octane alkylate increases.
- These additives may also decrease octane loss from gasoline hydrotreating due to lowering the concentrations of olefins (from cracking to C3/C4) in the untreated FCC gasoline. Substantial percentages of olefins are saturated to lower octane paraffins in the hydrotreating reactor.
The figure below shows example yield shifts and RON increases for two of Johnson Matthey’s FCC additives, Super Z Excel (ZSM-5) and ZMX-HP (C4-selective).
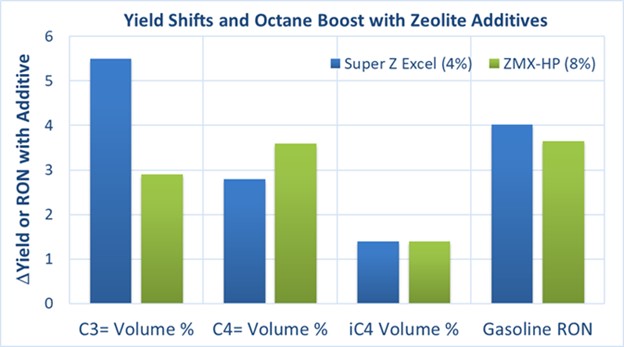
KEN BRYDEN and BOB RILEY (W.R. Grace & Co.)
Octane is a relative measure of the knocking characteristics of a fuel in an internal combustion engine. Knocking is caused by auto-ignition of fuel ahead of the flame front. Different hydrocarbon molecules have different resistance to auto-ignition, related to their role in hydrogen peroxide formation under combustion conditions (Reference 1). Hence, gasoline octane is governed by the types and relative concentrations of the individual hydrocarbon molecules that comprise the fuel. Figure 1 presents octane trends by hydrocarbon type and carbon number based on data from API Research Project 45 (Reference 2). As seen in the graphs, lighter molecules have higher octane. RON and MON values trend by hydrocarbon type as follows:
Aromatics ~ Olefins > Naphthenes > Iso-Paraffins > Paraffins.
Also, for olefins and iso-paraffins, octane increases as the degree of branching increases. To increase gasoline octane, the composition of the molecular types in the stream must be changed. Changes that can be made specific to the FCC to produce higher refinery gasoline octane fall into two main categories: (A) changes inside the FCC unit that change the composition of the FCC gasoline, and (B) adjustments to FCC operation that improve overall refinery gasoline pool octane.
Figure 1- Octane Trends by Hydrocarbon Type
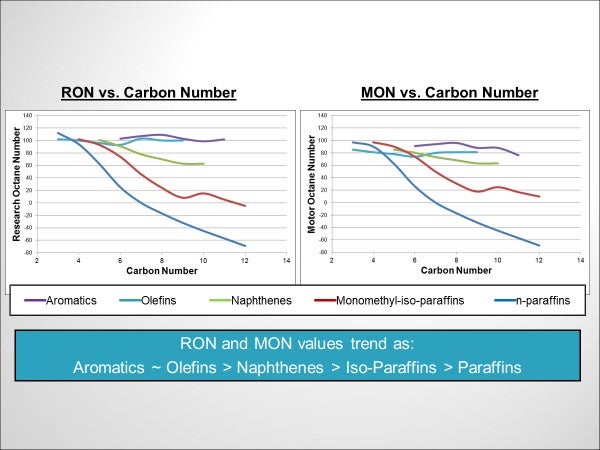
A) Changes Inside the FCC Unit
1) Gasoline Cutpoints
Changing the distillation range of gasoline from the FCC can influence octane. Butane is part of the light end of the gasoline and possesses a high-octane number. Increasing amounts of butane will increase RON. However, this must be balanced against vapor pressure considerations. For the heavy end, the effect of increasing gasoline endpoint on octane can vary. For aromatic gasolines, increasing end point will generally increase octane as more higher boiling point aromatic molecules are included in the gasoline. For other gasolines, the effect of endpoint on octane will vary with the feedstock to the unit, the conversion level and the catalyst. Detailed hydrocarbon analysis of FCC gasoline via gas chromatography and application of gasoline octane prediction models can be used to simulate how octane will change with gasoline endpoint (References 3 and 4).
2) Feedstock
The feedstock to the FCC will have a major effect on octane. Feedstock paraffins generally crack to form low octane gasoline range paraffins. Feed naphthenes crack to form high octane gasoline range aromatics and olefins. Aromatics with side chains present in the feed generally crack to form high octane gasoline range aromatics. As the feed becomes less paraffinic, octane increases. As a rule of thumb, a 0.2 number decrease in the UOP K factor of the feed will result in a 1 number increase in RON (Reference 5). Similarly, a 0.1 number increase in the ratio of naphthenic to paraffinic carbons (Cn/Cp) in the feed will generally result in a 1 number RON increase (Reference 6).
3) Operating Variables
Increasing riser outlet temperature will increase RON by increasing the number of olefins in the gasoline. As a rule of thumb, at a base RON of 90, an 18°F increase in riser temperature will result in a 1 number increase in RON (Reference 7). The octane gains with increasing riser outlet temperature will diminish as reactor temperature increases. More precise values can be determined by cat cracker operators through observations made on their own units.
Increasing conversion will increase octane. As conversion increases, cracked products increase, which means that the number of olefins and aromatics in the gasoline increases. As a rule of thumb, a 10 LV% increase in conversion will result in a 1 number increase in RON at constant riser outlet temperature.
Decreasing hydrocarbon partial pressure will increase FCC gasoline octane. Gasoline olefin content increases when the rate of bi-molecular hydrogen transfer reactions drops – which happens as hydrocarbon partial pressure drops.
4) Catalyst and Additives
The molecular composition of FCC gasoline is governed by the relative rates of cracking and hydrogen transfer reactions. Lowering zeolite unit cell size will lower hydrogen transfer and increase gasoline range olefins and thus increase octane. Increasing matrix content of the catalyst will help to crack side chains off aromatic cores and increase octane by increasing gasoline range aromatics. Dual-zeolite catalysts that incorporate both faujasite and pentasil type zeolites will lead to increased rates of isomerization and result in higher octane from the greater amount of branched hydrocarbons. ZSM-5 based additives and butylene selective additives can also be used to increase octane. These additives can increase isomerization reactions. Also, by cracking some gasoline range olefins to LPG olefins, they concentrate aromatics in the FCC gasoline, resulting in increased octane.
B) FCC Adjustments to Improve Overall Refinery Gasoline Pool Octane
1) Increasing alkylate production
With a typical RON of 95+, alkylate is one of the highest-octane blend streams in the gasoline blending pool. For refineries with alkylation capacity, FCC adjustments that increase the amount of LPG olefins used as alkylation feedstock will increase alkylate production and refinery gasoline pool octane. LPG olefins from the FCC can be increased by adjustments to reactor conditions, base catalyst, and use of ZSM-5 based additives. For units desiring a higher ratio of butylene to propylene in their LPG, butylene selective additives can be used instead of conventional ZSM-5 type additives. Variables that affect LPG olefin production in the FCC have been covered in detail in previous AFPM Q&A sessions (References 8, 9).
2) Reducing FCC gasoline hydrotreating severity
Refiners report losses between 1 and 5 numbers of octane when FCC gasoline is hydrotreated to remove sulfur. Hydrotreater severity can be lowered when the FCC gasoline contains less sulfur. Lower FCC gasoline sulfur can be achieved through use of gasoline sulfur reducing catalysts and additives that convert gasoline range sulfur to hydrogen sulfide. A detailed discussion of preserving octane with gasoline desulfurization technology can be found in Reference 10.
In summary, there are many ways FCC operations can be adjusted to increase octane. Inside the FCC unit, octane can be increased through feedstock selection, choice of operating conditions, tuning of base catalyst properties, and use of specialty additives. Outside of the FCC, the amount of alkylation feed derived from the FCCU can be increased through careful FCC catalyst and additive selection, and octane loss during FCC gasoline hydrotreating can be reduced by lowering FCC gasoline sulfur through use of gasoline sulfur reducing catalysts and additives.
As always in FCC, changes to influence one variable (octane), will result in changes to other FCC unit yield objectives. Refiners should work closely with their catalyst supplier to understand the options available to increase octane and how to balance these with other yield objectives. Grace has a wide portfolio of catalyst and additive solutions and would be happy to engage with refiners to discuss options to increase gasoline octane.
References
1) Westbrook, C.K., "Chemical Kinetics of Hydrocarbon Ignition in Practical Combustion Systems," Proceedings of the Combustion Institute, Volume 28 (2000), pp. 1563–1577.
2) Knocking characteristics of pure hydrocarbons, Developed under American Petroleum Institute Research Project 45, Special Technical Publication No. 225; American Society for Testing and
Materials: West Conshohocken, PA, 1958.
3) Cotterman, R.L., Plumlee, K.W., “Effects of Gasoline Composition on Octane Number,” Proceedings of the Symposium of the Division of Petroleum Chemistry, American Chemical Society Meeting, Miami Beach, Florida, 1989, pp. 165-171.
4) Haas, A., McElhiney, G., Ginzel, W., Buchsbaum, A., “Gasoline Quality- The Measurement of Compositions and Calculation of Octanes,” Petrochem/Hydrocarbon Technol. 1990, 43, 21-26.
5) Magee, J.S., Ritter, R.E., Wallace, D.N., and Blazek, J.J, "How Cat-Cracker Feed Composition Affects Catalyst Octane Performance AM-80-48" 1980 NPRA Annual Meeting, New Orleans, Louisiana.
6) Andreasson, H.U. and Upson, L.L., "Four Main FCC Factors Affect Octane," Oil and Gas Journal, August 5, 1985. p. 91.
7) Chapter 6, "FCC Operation," in Grace Davison Guide to Fluid Catalytic Cracking
8) Question 101, FCC Q&A Session, AFPM Q&A and Technology Forum, October 2014.
9) Question 10, Process Q&A Session, AFPM Cat Cracker Seminar August 2016.
10) Cheng, G., "Preserving Octane for a Tier 3 Gasoline Market CAT-16-23," 2016 AFPM Cat Cracker Seminar.
MATTHEW WOJTOWICZ (UOP)
If a potential future scenario occurs, where specifications require production of higher-octane gasoline, refiners in the United States have several options to enable production of greater amounts of higher-octane gasoline. Each refinery would require a unique solution, depending upon the existing configuration, future target gasoline specifications and future target gasoline production rates – the extent of any modifications would also depend upon the existing refinery complexity and process unit capabilities. UOP has studied ways to increase gasoline RON for our customers with different types of refineries, and lower complexity refineries would likely require significant investment to enable higher octane gasoline production compared with more complex refineries. Production of 95+ RON gasoline is being achieved throughout most of the world. The United States (US) is one of the few countries in the world that does not currently consume gasoline with a RON of 95 or higher.
Solutions for improving octane:
CCR Reformer
-
Increase existing CCR Reformer severity to produce higher octane reformate for blending (~101* RON could potentially be achieved based on typical designs). This will lower yield but will enable refiners to utilize latent octane capability in existing units. With the introduction of ethanol (120+ RON) into the US gasoline blend, refiners have dialed back reforming severity and reformate octane.
-
Revamp an existing CCR reformer to achieve ~105* RON.
-
Add a CCR reformer if a reformer does not currently exist in the refinery.
SR Reformer
-
Increase existing SR reformer severity to produce higher octane reformate for blending (~95* RON could potentially be achieved based on typical designs). This will lower yield but will enable refiners to utilize latent octane capability in existing units.
-
Revamp an existing SR reformer to achieve ~101* RON.
Light Naphtha Isomerization
-
Add an isomerization unit if one does not currently exist – this will increase the octane of the light naphtha (~85* RON could be achieved).
-
Add a deisohexanizer to an existing isomerization unit – this will further increase the octane of the light naphtha (~88* RON could be achieved).
-
Add deisohexanizer and a deisopentanizer to an existing isomerization unit to achieve ~91* RON.
FCC
-
Increasing FCC operating severity (increased conversion) in conjunction with the addition of ZSM-5 additive will increase the light olefin yield (propylene, butylenes and amylenes), but at the expense of overall FCC naphtha production. These lighter olefins can be sent to an alkylation unit, where the increased alkylate production, along with its inherently higher RON, will help offset the loss of naphtha production from the FCC. The remaining FCC naphtha will also experience an increase in the RON.
-
As you increase the severity of operation in the FCC unit for higher light olefin production the following will happen: 1) more naphtha range olefins are converted to light olefins (propylene, butylenes and amylenes); 2) aromatics are concentrated in the FCC naphtha, thereby increasing the overall RON.
Alkylation
-
Additional alkylate with ~95 RON can be purchased.
-
Increase alkylation capacity to produce additional alkylate. Increasing FCC operating severity as discussed above increases propylene and butylenes that can be converted to alkylate. The ultimate potential capacity of the alkylation unit is generally limited by the propylene and butylenes that can be produced by the FCC unit.
-
In the US, this could be overcome by leveraging low cost C4’s (from the natural gas fields) and by adding a butane dehydrogenation unit. Increased alkylation capacity is enabled through production of additional butylenes from the low cost C4’s.
*Typical RON representations. These may vary for a specific refiner.