Question 43: Can FCCU feed pre-treatment achieve the new Tier 3 gasoline sulfur targets without post-gasoline treatment? What criteria are used to select the optimal combination of pre-treatment and post-treatment severities to meet the Tier 3 objectives?
GATES (Motiva Enterprises LLC)
For Tier 3 gasoline, the anticipated average of 10 ppm sulfur will be required by 2017. In order to understand what will be needed to meet those specs, you will have to do a review of a number of factors that contribute to the sulfur, including understanding your crude diet and the material that is actually going into the gasoline pool, as well as blend components. We talked earlier about light tight oils. The fact is that they tend to have much lower sulfur; so there is a potential that in the future, many of us will see lower sulfur as a result. From the blend component standpoint, there is also the potential need to treat the butane and/or the disulfide oils to make sure that your blend components meet the sulfur requirements for the gasoline pool.
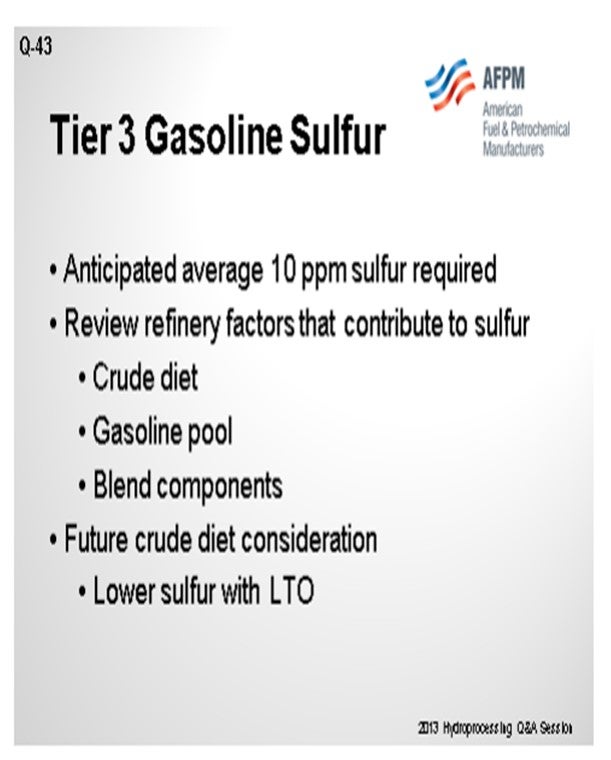
So specifically with regard to using pre-treatment or post-treatment, the pre-treatment may be sufficient to achieve Tier 3 gasoline specs. With feed pre-treatment, you will be able to reduce the sulfur and also achieve additional aromatic saturation, which will play out with improved conversion and volume gain in the cat cracker. It will also contribute to lower cat cracker catalyst usage because there should be lower metals on the cat feed itself. Also with pre-treatment, you are probably operating at much higher pressure; so it will be a more expensive unit to build, from a grassroots standpoint.
For the post-treatment, again, it typically requires a lower capital cost when compared to the pre-treatment options. There will also be less hydrogen consumption. However, you will not see any improvement in the cat cracker yields. One specific consideration you will probably want to include is feed severity. Will you see a change in the materials those hydrotreaters might need to process? The pre-treat option probably has some additional flexibility to it. From a unit operation standpoint, an existing pre-treat unit’s ability to remove the sulfur may influence what you choose to do for post-treatment. Utilizing different techniques, you may be able to increase an existing unit’s hydrogen partial pressure. We talked a little earlier about the benefits of hydrogen partial pressure. You may be able to increase your hydrogen purge rates or potentially add gas treating to remove the H2S (hydrogen sulfide) in order to increase the hydrogen partial pressure and improve your sulfur removal.
The last piece is around cycle length where the increased severity of an operation could cause a shortened cycle length. Again, you will have to take a look at that to understand how it will impact the overall economics of the refinery. We have had a couple of folks talk about different ways of adding catalyst volume to the system. By doing that, you will increase your overall cycle length or at least be able to bring it back to your target.
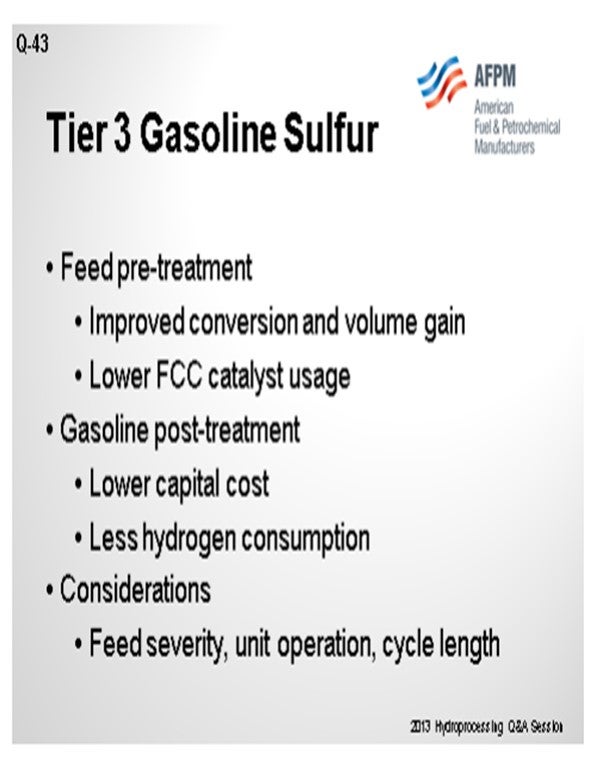
VICHAILAK (Marathon Petroleum Corporation)
I very much agree with Dave. For FCC gasoline today, like most refineries, we produce about 50 to 100 ppm sulfur. When you mix this with the outer blend stream, you get 30 ppm gasoline. But if you go to Tier 3, then it will result in about 10 ppm sulfur in the gasoline pool required.
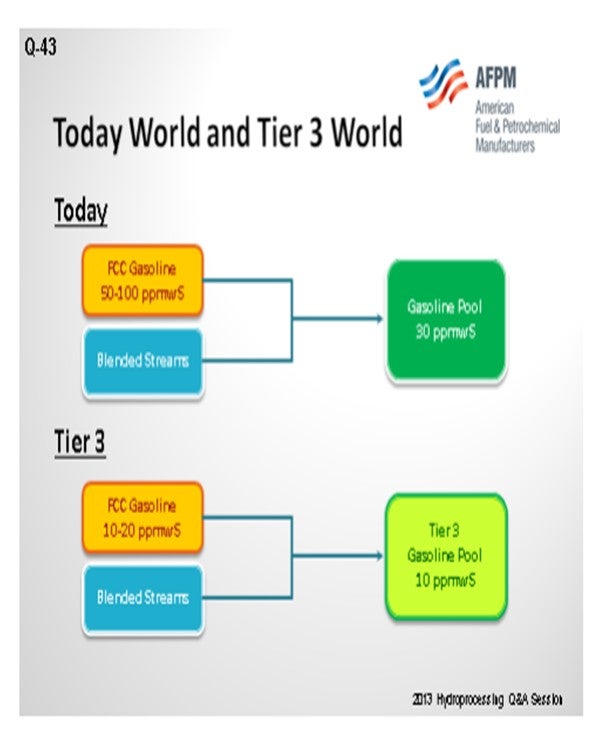
We will also have to reduce FCC gasoline to 10 ppm. If you can increase it to 20, then what will it mean to your FCC or cat feed hydrotreaters? The product will reduce down from 1000 to 1500 ppm down to 300 ppm, with a maximum of 500 ppm. Can it be done? Yes, of course. In most of our refineries, it can be done by changing things around the cat feed hydrotreater and improving the hydrogen purities or changing feed. However, you will need to evaluate the current operation severity and unit capability to utilize new generation catalyst, which is already available on the market. You will probably also have to shorten the cycle length; for example, reducing it from seven years down to two.
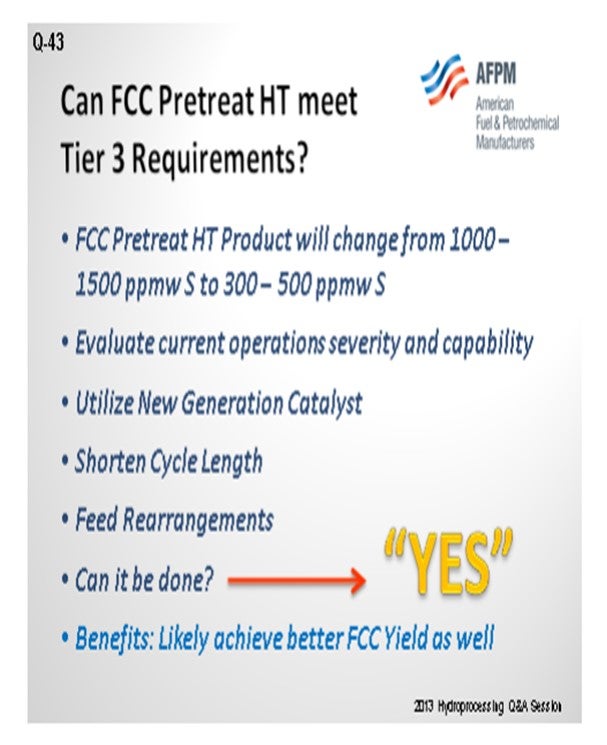
Feed rearrangement can also be done to put the metal traps in there if you have some feed that has, for example, very high metals taking up a lot of space in the reactors. If you reduce that feed, you might be able to increase the volume of active catalyst in the reactors. The benefit of increasing the FCC pre-treat capability or severity is achieving better FCCU conversion. By doing this, you will increase makeup hydrogen requirements. If the unit does not have treat gas or an amine absorber, then you will have to add an amine absorber. That helps a lot because every percent of H2S you remove from the recycle gas will result in about 3°F to 5°F decrease in operating temperatures.
You probably have to consider adding additional storage tanks because you will have a reduced run length. There will be a period when you will need a catalyst change, and the FCC will have to be on service. So you must have a tank that stores all of the FCC feed. Some practice injection of black oil into the FCC. It does not make sense to try to increase severity in the gas hydrotreater and then inject black oil or something similar to reduce opacity in FCC. This is just one consideration.
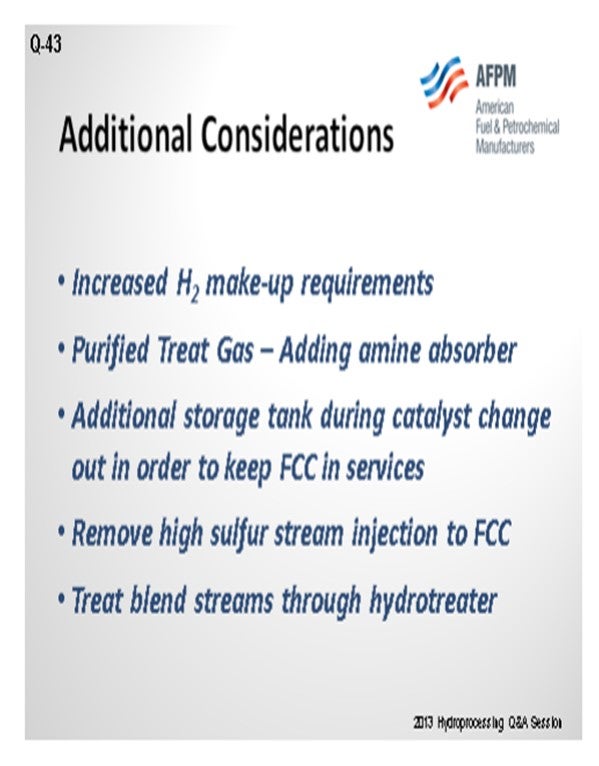
The next slide shows an optimum combination of pre-treat and post-treat, depending on what is on the ground. If you already have an existing post-treat unit, that does not mean you pre-treat for 30 ppm is very weak. So, the requirement on pre-treat will be a lot more. If you want to revamp the post-treat, it could be less likely or remain the same requirement on pre-treat. But if you are going to add a new post-treat unit, then the requirement for the pre-treat will probably be less. So, we calculate that the optimum cycle length for pre-treat unit is about two years.
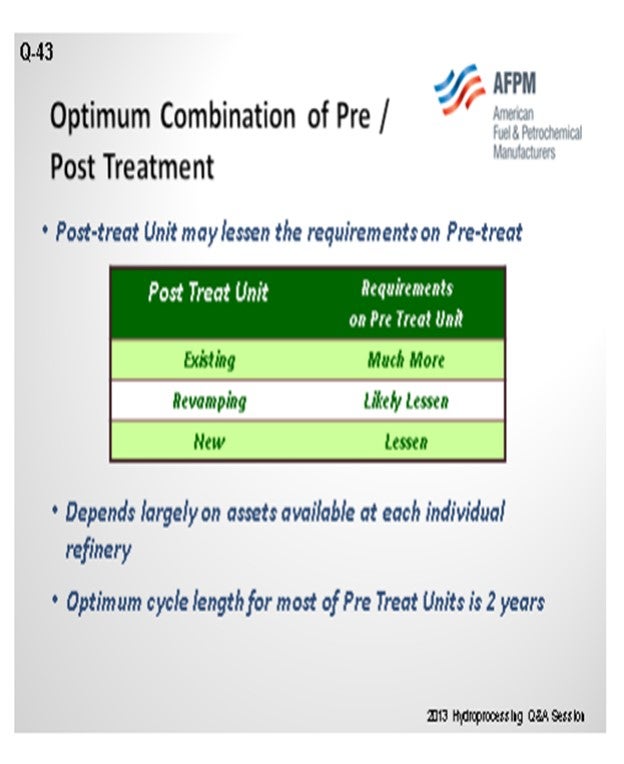
MUKESH PATEL (Reliance Industries Ltd.)
I understand that when Tier 3 is implemented, other than sulfur, there will be a benzene spec. In this option of a high severity operation of FCC pre-treat unit, how will the combination work out when you have to meet sulfur, as well as benzene?
ROBERTSON (AFPM)
Montri, you stipulated that there is some anticipation of an additional benzene spec on top of sulfur. So I believe your question is: “If you had to go for lower sulfur and lower benzene at the same time, how does that change what you need to do?”
GATES (Motiva Enterprises LLC)
If you have a benzene issue with your gasoline pool, it will not necessarily directly relate to the pre-treat or post-treat choice for sulfur removal. You should evaluate the operation of your reformer, the source of the benzene, and the opportunities to either reduce the benzene made in the reformer or treat it in another unit. You could consider putting in a benzene saturation unit or doing some type of benzene extraction where you can send that off to another unit.
SHARPE (Flint Hills Resources, LP)
And, you do not have enough severity in your post-treat unit to saturate benzene.
MONTRI VICHAILAK (Marathon Petroleum Corporation)
The answer to the first question depends heavily on the current operation of CFHU (catalytic feed hydrotreater unit) and what may change in the future. Most of Marathon’s CFH units can achieve Tier 3 gasoline sulfur targets without post-treatment with an expected cycle length of at least two years. These units will achieve specific product sulfur by utilizing new generation catalyst. Minor modifications include makeup hydrogen supply to meet required hydrogen consumption for producing FCC feed that can meet Tier 3 gasoline sulfur.
A refinery that has a CFHU processing highly metals contaminated feeds is unlikely to achieve Tier 3 gasoline sulfur targets without post-treatment unit. Highly metals-contaminated vacuum gas oil or deasphalted oil (DAO) has to be processed in other units so that the CFHU can have more room for active catalyst to accommodate higher HDS (hydrodesulfurization) requirement.
Next question: “What criteria are used to select the optimal combination of pre-treatment and post-treatment severities to meet the Tier 3 objectives?” From what we see, there are no specific criteria for the optimal combinations of pre-treatment and post-treatment severities for Tier 3 objectives. The criteria considered should depend largely on assets available at each individual refinery. A general idea would be maximizing the HDS at pre-treatment first. Increasing HDS in a post-treatment unit will be done at an expense of octane number loss (higher HDS) or volume loss (lower endpoint). Also, upgrading the post-treatment unit will potentially require a much higher capital cost than improving pre-treat units.
MIKE HUNTER (Haldor Topsøe, Inc.)
The proposed rule for Tier 3 gasoline will lower the specification for average sulfur to 10 wppm, a two-thirds reduction in sulfur level from the current Tier 2 limitations. For practical purposes, this can mean that the sulfur from FCCU gasoline will also have to be reduced by twothirds in order to bring the overall gasoline pool down to 10 wppm. A refiner producing FCC gasoline with a sulfur level in the range of 60 to 100 wppm today will need to potentially reduce this to 20 to 40 w to meet the proposed Tier 3 level in the 2017 to 2020 timeframe. If the sulfur level is being managed by feed pre-treatment, this means the typical FCCU feed sulfur level must be reduced from about 0.1 to 0.15 wt% today down to approximately 300 to 500 wppm in the future. The impact on HDS performance requirement will depend on the composition and sulfur content of the untreated feed, as well as the available hydrotreater conditions. The following table summarizes two examples of different HDS operations where product sulfur must be reduced by approximately two-thirds to comply with lower gasoline sulfur requirements. These examples indicate that in order to achieve the required sulfur reduction, catalyst cycle life will be decreased by about 25 to 30%. To maintain current cycle life of the HDS unit will require an increase of approximately 20% in the relative volumetric activity (RVA) of the catalyst or the addition of 20% new reactor volume by revamp.
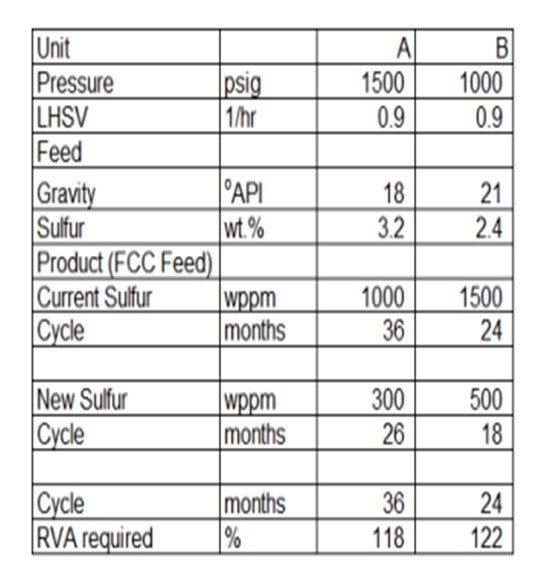
Our clients have proven, in a number of units, that reaching these new low sulfur targets of 200 to 300 wppm in the feed to the FCC is possible with our gas oil BRIM™ catalysts.
An important criterion used to decide on pre-treatment versus post-treatment approach is the potential loss of gasoline octane if HDS severity is substantially increased in the post-treatment step. If the option exists to reduce sulfur by pre-treatment, this will minimize the impact of octane loss on the gasoline pool. The most direct approach would be to install a higher activity catalyst in the feed HDS unit in order to reduce sulfur while minimizing the loss of operating cycle life. Once this is accomplished, additional sulfur reduction by post-treatment can be made with minimum octane loss. Haldor Topsøe has released new products for FCC feed pre-treatment than can achieve 10 to 20% RVA improvement over the previous generation. Such improvements in catalyst performance will play a key role in achieving the new Tier 3 sulfur requirements.
JAMES ESTEBAN (Criterion Catalysts & Technologies)
The anticipated future Tier 3 fuels regulations will require refiners to reduce gasoline pool sulfur to an average of 10 ppm sulfur estimated, effective 2017. In order to accomplish this, a broad review of the entire gasoline pool and its blend components is required. This review must consider the sources of each component and their individual contribution to the overall blended gasoline sulfur concentration.
In many cases, there may be opportunities for refiners to adjust crude diets and purchased blendstocks to reduce pool sulfur which will require an economic evaluation of potential options. In most refineries, FCCU gasoline is the largest volumetric contributor to the gasoline pool, providing both high value and high sulfur. FCCU feed pre-treatment and FCCU gasoline post-treatment are two solutions available to reduce FCCU gasoline sulfur. These treatments can be considered individually or combined for an optimized option.
With respect to the question, it is possible to produce Tier 3 quality FCCU gasoline blend components by adding feed pre-treatment or increasing severity of an existing FCCU pre-treatment unit. In addition to sulfur reductions of all of the FCCU products, adding or improving FCCU pre-treatment saturates more aromatics, reduces nitrogen, and removes metals to improve crackability for increased FCCU conversion and volume gain.
When evaluating the FCCU pre-treatment versus post-treatment options to meet Tier 3 gasoline regulations, the primary considerations are capital investment, margin improvement, feedstock flexibility, and cycle life duration and economics. Capital investment and operating cost are significantly higher for a grassroots FCCU pre-treatment versus post-treatment options. For existing units, increasing severity of an FCCU pre-treater or post-treater may require capital investment to overcome unit limitations such as additional reactor volume, increased recycle or makeup gas compressor capacity, or heat train and furnace modifications. First, the desired level of desulfurization required to meet Tier 3 gasoline specifications must be understood, either by pre-treatment or post-treatment. Then, capital investment requirements for new construction or revamp of existing units are evaluated versus the economic return for each potential option.
Unlike FCCU post-treatment, increased severity of an existing FCCU pre-treater will improve overall FCCU margins. In addition to removing sulfur, pre-treatment reduces FCCU feed nitrogen, metals, and aromatics for increased FCCU conversion and reduced catalyst usage. The economic return counters the higher capital cost for pre-treatment when comparing options. In addition, the potential loss of octane by post-treatment has a negative economic impact versus pre-treatment.
Refinery crude and purchased feedstock flexibility should be considered when evaluating treatment options. In many cases, pre-treatment options for FCCU gasoline sulfur can provide additional flexibility when considering crude diet options given the ability to operate at varying severities and different modes to create margin. Post-treat units can be designed with some feed and product sulfur flexibility but cannot create margin opportunity.
Comparing the cycle life objectives to the capabilities of existing FCCU pre-treaters and post-treaters is an important exercise. Elongated cycle life objectives for a new FCCU pre-treater designed for low-sulfur FCCU feed production will increase capital cost. Increasing severity of an existing FCC pre-treater will shorten catalyst cycle life with more frequent refinery interruptions and catalyst replacements. These penalties are weighed against the benefits of increased yields and crude flexibility when considering the pre-treatment option. Higher FCCU post-treatment severity will increase capital expenditure for a new unit and shorten cycle life for an existing unit to a lesser extent but without margin generation to counter the effects.
FCC pre-treatment can be a successful strategy for achieving Tier 3 gasoline targets, but it is not always the attractive option. Although it can be utilized alone, considering a combination approach with post-treatment may offer an optimized solution to capital investment and cycle life.