Question 42: What water sources are you using for desalter waterwash, and what are the advantages and disadvantages of each? What role does desalter waterwash source and injection location play in desalter performance?
SOLOMON (Athlon Solutions)
As Gordon said, these were throwback questions that Chris McDowell answered a while ago. It would have been great to see those actual answers. I am sure they are very similar to what we have now; but still, just to see how much the desalting process may or may not have changed.
In the years that some of my other colleagues and I have been working on desalter waterwash practices, we have some Best Practices we think work well with all varieties of crude. First is wash water. Yes, wash water. More wash water: whatever you can get. Typically, 5 to 8% of the crude charge is what we recommend. Heavy crudes may be even a little higher, if we can get it.
Wash water quality is also another very important aspect. We look for wash water somewhere between 6 and 8, in terms of pH, which contains less than 50 ppm of ammonia; is low in chlorides; and, has low hardness, low oil content, and – obviously – low oxygen content.
Preferred sources: There are a variety of sources we like to see. Stripped sour water is usually our best source. Sour water from the overhead systems, such as the vacuum overhead, is very good, too, as are non-scaling freshwater and steam condensate. Steam condensate is obviously an expensive alternative, but it can be used.
Over the years, we have experimented in a technical sense and looked at different ways of injecting wash water. What we found, at least at Athlon, is that we try to get as much of the wash water upstream as possible. This is actually upstream of the crude charge pump. We want to get some very good mixing and improve our contact time. After that, just a little ahead of the crude preheat is the next best source. Finally, at the mix valve where we typically see a problem is that when we inject water and chemical at the mix valve, and we just do not have a lot of contact time. I cannot tell you how many operations I have seen where, well, the mix valve really is not the mix valve. It is a control valve or something else; or it is wide open. So, inject wash water as far upstream as possible.
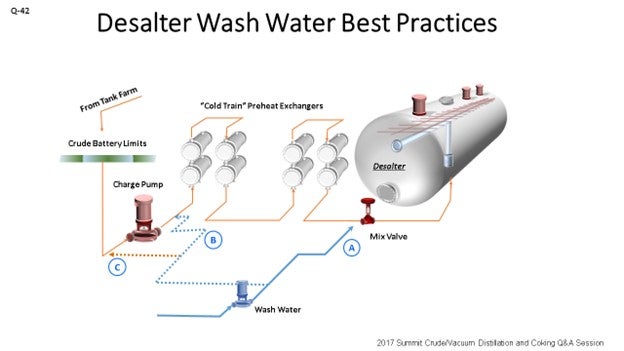
There are some advantages of the different sources of overhead water. Vacuum overhead tends to be fairly light in hydrocarbons and low in pH, but there are some disadvantages as well. It can result in recycling of any tramp amines that are in the system, so we want to be careful of that.
These are some pictures of basically what is going on, in terms of crude oil and then desalted crude. In the picture on the very left, we see raw crude – just filtered with toluene and not washed with water – containing about 85.5 ptb (pounds per 1,000 barrels) of salt. You can see those crystalline forms. The top right photo shows what happens when we do it just ahead of the desalter. At that point, you still start to see some good work. We are getting most of the salts out, but still about 3.5 ptb remains there. Finally, what we have seen when we move it into the suction of the charge pump is that, again, we have 0.9 ptb. We are contacting a lot of the salts and really doing a good job removing them in the water.
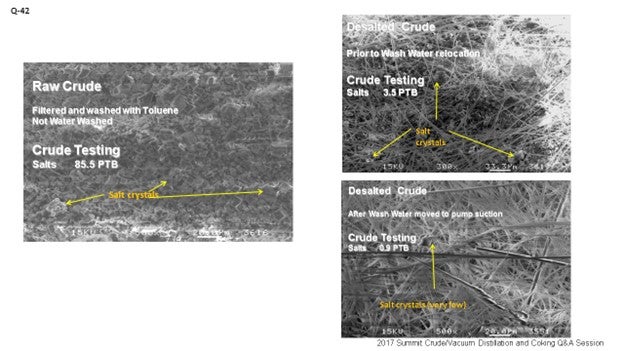
Some people might say, “Well, are we creating a very stable emulsion by doing that?” That is a possibility; it can happen. But crude charge pumps tend to be good devices for moving fluid and not necessarily very high shear mixing apparatus; so, most of the time, we are seeing very good results from this operation.
Sometimes we have talked about water that is soluble in the oil. When that happens, though, just the water goes into the oil. The salts stay behind and end up in this more crystalline form. We want to be careful that we are not getting a lot of the soluble water out of the crude and just leaving salts behind; because by that time, we have already lost the opportunity to contact the salt and get it out of the system. That is why we try to continue to move it as far upstream of the water injection as possible. The pictograph below shows the solid salts that can be left behind in the crude oil.
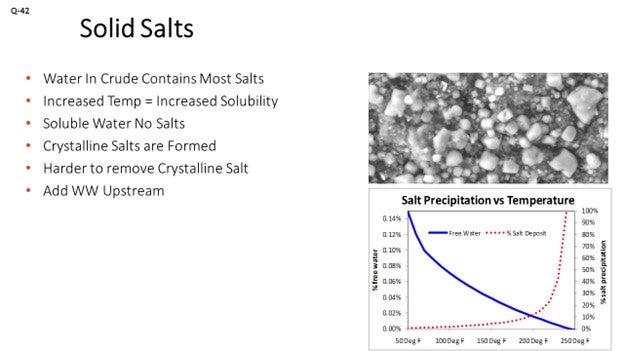
So, those are basically the Best Practices. I do not think they have changed in a long time, since Chris gave the response several years ago. It would have been great to have some of the throwback response, but perhaps the next time.
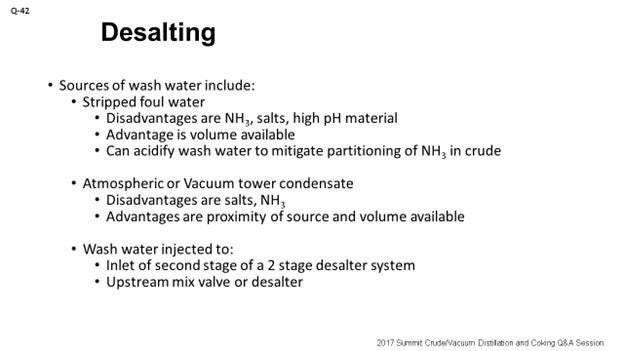
LÉGARÉ (Andeavor Martinez Refinery)
I do not really have much to add after that discussion. I will say, though, that is there is a difference between what is ideal – as far as makeup wash water is concerned – and what you actually get in a refinery. So, it is probably best to put some thought into how you are going to mitigate your deficiencies in your gaps, as far as pH and ammonia content are concerned. One of the techniques we have looked at in the past is acidifying the wash water to deal with high amounts of ammonia. That technique has been effective for us in the past.
Hydraulic limits: If you are trying to get your stripped foul water over to a crude unit and the sources are not close by, then those hydraulic limits can also limit the amount of makeup you have at the desalters. It becomes a juggling act between what you have and what you would like to have. Then, you have to come up with the proper justification to put in these new projects or new facilities to move forward to get closer to Best Practice.
BILL CATES (Hunt Refining Company)
One subject the panelists did not discuss, which is one of our considerations, is wash water percentage. One of the ways to get it up is to do recycle off the bottom of the desalter. There are pros and cons to that method; because obviously, the water is hot. The other fact is that it actually contains some salt; meaning, it has a heavier density, which helps the water get it back out. Very seldom are you super-saturated with that amount of salt. So, do you have any comments about using recycle to supplement wash water in front of the mix valve?
SOLOMON (Athlon Solutions)
Just like Eric said, usually what you have to use is what you can get. Certainly, we have seen recycled wash water. Of course, we have a two-stage of desalting that is always occurring. Yes, you just have to be careful. Use the best quality. But often, as Eric mentioned, you just use what you have there.
KEVIN SOLOMON (Athlon Solutions)
Wash Water Best Practices
Over the years, we have established several Best Practices concerning desalter wash water rates, quality, injection locations, and sources that – when utilized – help ensure optimum crude oil desalting.
We have found that wash water rates of 5 to 8% of crude charge is sufficient for light- to mid-API crudes and that heavier crude need slightly higher rates. Wash water quality is equally as important as wash water rates. Ideal wash water specifications are:
-
pH level of 6 to 8,
-
Contain less than 50 ppm ammonia,
-
Contain less than 50 ppm chlorides, and
-
Have low hardness, low oil content, and low oxygen content.
Our preferred wash water sources are stripped sour water, sour water from overhead systems (such as vacuum overhead condensate), and non-scaling fresh water and steam condensate. The advantages of overhead water are:
-
It removes light hydrocarbons from the vacuum overhead water (less hydrocarbons to sour water stripper), and
-
The lower pH helps lower total wash water pH, especially if there is a higher pH wash water source in use.
The disadvantages of atmospheric or vacuum overhead water are that there is the possibility of recycling tramp amines back into crude oil.
The location of wash water injection is also important. Our Best Practice is to inject wash water far upstream of the desalters to provide sufficient time to contact any water (and thereby salt) in the crude oil. Our preferred injection points (in order of preference) are:
-
At the suction to the crude charge pump,
-
Ahead of the pretreat train, and
-
Ahead of the mix valve.
There are several advantages to injecting wash water ahead of the crude charge pump. First is the improved contact of wash water with crude oil, thereby improving desalting. Injecting ahead of the preheat helps to heat up desalter wash water, which minimizes formation of crystalline salts in cold preheat train and therefore results in less fouling and higher desalter temperature. This injection location can permit running desalter mix valve lower with equal or better desalter salt removal; hence, lower desalter pressure which – in some instances – can lead to slightly higher crude throughput.
There are some disadvantages of injecting wash water upstream of crude charge pump. It is possible that the increased shear stress resulting from the pump can create a tighter emulsion in some cases. Without the right EB and low oil/water residence time, this emulsion may be hard to resolve. If the desalter wash water is coming from the second stage, it will be 250°F, which will then be injected into the cold crude. On a single-stage, the brine water exchanger never gets the feed water up to desalter temperature; so, it is not as bad a problem. Using cold, fresh water as part of the charge pump wash water can help, even if only a portion of the total water is going to the pump suction.
ERIC LÉGARÉ (Andeavor Martinez Refinery)
Stripped sour water is commonly used as makeup water to a desalter. Disadvantages of stripped foul water include NH3 in the wash water as it can cycle up and increase the risk of chloride salts in your tower/overhead system at high pH levels. Acidifying wash water with high NH3 content can be a solution to reduce the partitioning of NH3 into the crude phase. The advantage of this water source are the high volumes available at low cost as this stream is normally routed to the wastewater plant.
Alternatives would be condensate from the atmospheric or vacuum fractionator overhead systems. The advantages of this stream are both its availability and proximity to the desalter. The disadvantage would be the chloride salt content in this water stream, if there was no supplemental waterwash in this system, pH, and the increased potential for amines.
Injection of wash water goes to the second stage of a two-stage system. Alternately, some or all of the water can also be injected upstream the mix valve to maximize mixing with the crude upstream of the desalters.
CHRIS CLAESEN (NALCO Champion)
The best desalter wash water sources are stripped sour water with low salt and solids content or BFW, but this material is expensive. Try to avoid waters containing oxygen, hardness, tramp amine, and high salt levels. Water injection location has a significant impact when very low salt levels are required. Injecting part of the water in the cold preheat will help remove some of the crystalline salt and prevent drying out of the crude. The amount of water that needs to be injected at each specific location will depend on the unit design and the feed properties.
DENNIS HAYNES (NALCO Champion)
The list of potential desalter wash water sources is long. An important factor to consider when choosing a source is to review which contaminants are in the water. Oxygenated sources, such as industrial water, may cause an increase in SOx to the distillation column. Stripped sour water is a common source and has been used effectively in many cases; yet, caution is needed when the pH is high, especially if the pH is due to caustic addition at the SWS. Atmospheric column overhead water may or may not be acceptable, depending on the amine content and the pH of the desalter wash water blend. Vacuum overhead hotwell water is typically a good source; yet it needs to be monitored to make sure it does not bring a large amount of emulsified hydrocarbon condensate to the desalter. Moderate to slightly lower pH wash water typically results in better emulsion resolution and contaminant removal. Injection of wash water to points that facilitate good yet controlled mixing will also result in better contaminant removal. Each system needs to be optimized based on feed quality and characteristics and system mechanical design characteristics.
PHIL THORNTHWAITE (NALCO Champion)
The provision of adequate, good quality desalter wash water can present a significant challenge to some refineries; some sources of water are good, and some not so good. Utilizing poor quality wash water can result in processing issues, contributing to desalter upsets, corrosion, fouling, and wastewater treatment plant issues. So, the choice of the water source is critical to good desalter performance. Ultimately, the best way to identify whether a water source can be added to the desalter wash water is to analyze the contaminants that are present in that particular source and in the overall wash water charge, followed by an assessment of the risk that these incur.
The best water sources, and the ones more commonly utilized, are overhead sour waters from the crude and vacuum units and good quality stripped sour water. There are considerations, though, in that the amine content of the overhead sour waters, whether it be from neutralizers or tramp amines, should not present an amine recycle risk that could increase the risks of salt formation. Likewise, the amine content of the VDU sour water should be considered, as well as well the level of hydrocarbons in this stream, as this can potentially lead to desalter upsets and/or impact on desalter effluent quality. If stripped sour waters are used, ideally, they should be low in ammonia and also phenols, while bottoms from an SWS that injects caustic to increase ammonia stripping is best avoided. High ammonia levels can elevate the pH of the water that can increase emulsion formation; and depending on the pH, it will readily partition into the oil phase, passing to the crude unit overheads where it can increase the risk of salt formation. Phenols can impact on effluent water quality and have a huge detrimental impact on the secondary processes of the wastewater treatment plant, while they can also contribute to emulsion formation and stabilization.
For those refiners limited in the amount of wash water available, a brine recycle can be an effective means of boosting available wash water and improving desalter performance. However, care has to be taken when utilizing desalter brine in this way; if there is a deterioration in effluent water quality, recycling this stream can precipitate a much larger desalter upset.
With respect to wash water injection locations, it is typical to inject a portion of the total wash water in front of the cold preheat exchangers with the remainder just before the mix valve. The portion injected before the cold preheat dilutes the scaling salts present in the crude, reducing the risk of exchanger fouling. However, varying the ratio of water injected at these two locations can improve salt removal since the cold preheat exchangers can help improve mixing with dispersed brine droplets and potentially crystalline salts. This ratio can be easily determined through a desalter optimization study using the correct analytical methodology.
GLEN SCATTERGOOD (NALCO Champion)
We use primarily stripped sour water along with vacuum overhead condensate. Ammonia content of the stripped sour water must be controlled in order to manage the combined wash water pH. An elevated wash water pH is caused by increased ammonia in the stripped sour water, which lead to degraded dehydration of the desalted crude inside the desalter vessel.
We use stripped sour water as the source for desalter wash water. A brine recycle is in place to increase the total wash water volume greater than 7% based on crude charge. The addition of the recycle and increase in total wash water has reduced atmospheric distillation tower overhead chlorides by 20%.
SAM LORDO (NALCO Champion)
The typical desalter wash water sources are:
-
Stripped sour water and
-
Condensates.
The typical desalter wash water quality is:
pH |
6-8 |
NH3 |
< 10 ppm |
Cl- |
< 25 ppm |
Temperature |
> 180°F (82°C) |
Oil |
Nil |
Oxygen |
ppb (parts per billion) |
Stripped sour water tends to run high in pH and ammonia. The high pH increases the potential to stabilize emulsions. It is also possible that the stripped sour water could have other contaminates present, like cyanide, organic acids, and amines (tramp and internally generated).
Condensates from the CDU tend to be better to use overall; however, they, too, can contain amines (from neutralizers being applied and from crude oil sources, organic acids, H2S, ammonia, etc.) Condensates from other units – like delayed cokers, fluid catalytic crackers (FCCs), hydroprocessing unit stabilizer/stripper towers, etc. – can introduce other contaminates not normally found in the CDU or they can increase the concentration of other contaminates. For example, an FCC condensate can easily have more than 2,000 to 4,000 ppm ammonia present, compared to a typical CDU overhead of 40 to 100 ppm.
Solids, high pH, and other contaminates present in the wash water can result in the stabilization of desalter emulsions or can change the solubility of contaminates in crude oil, which could result in unwanted contaminates going out of the desalter to the downstream equipment.