Question 42: Occasionally we make off-color jet (pink, blue, or green). What are the causes, and what can be done to correct this?
GATES (Motiva Enterprises LLC)
The question was specific to off-color jet, but we can have other off-color material. We have seen red, yellow, green, and brown. Most typically, the yellow and green tend to be associated with the lighter products; red and brown with the heavier ones. But again, you can get various colors throughout the spectrum. The color itself can be influenced by both the feed and the operating conditions. We processed some cracked kerosene that did cause us a color issue. Most commonly, I would say the high reactor temperatures can be the reason for color particularly in the jet. So if you are running a hydrotreater that has lower hydrogen partial pressure and you have to increase your temperatures while trying to make ultra-low sulfur kerosene, you could end up in a situation where you are no longer saturating the aromatics and then run into an equilibrium temperature limitation. When that happens, those aromatics can cause color bodies. The consequence is that even very small amounts of material can, in fact, create a color problem with the jet. There is the potential that you may be able to remove those color bodies, either using clay or potentially a resin.
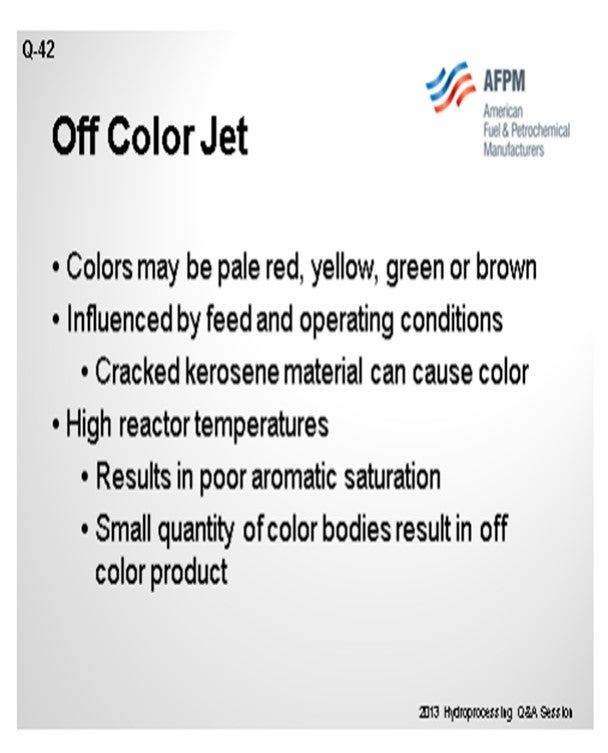
SHARPE (Flint Hills Resources, LP)
We have experienced pink jet from certain crudes. Also, higher bed temperatures of 650°F+ encountered towards the end-of-run can cause recombination reactions, which can then form color bodies. Phenolic compounds often display a pink color when impure, and phenols can create color bodies by reacting with each other. We have seen an oxide scale from tanks cause a pink color. My Answer Book response contains additional information on the causes of jet color.
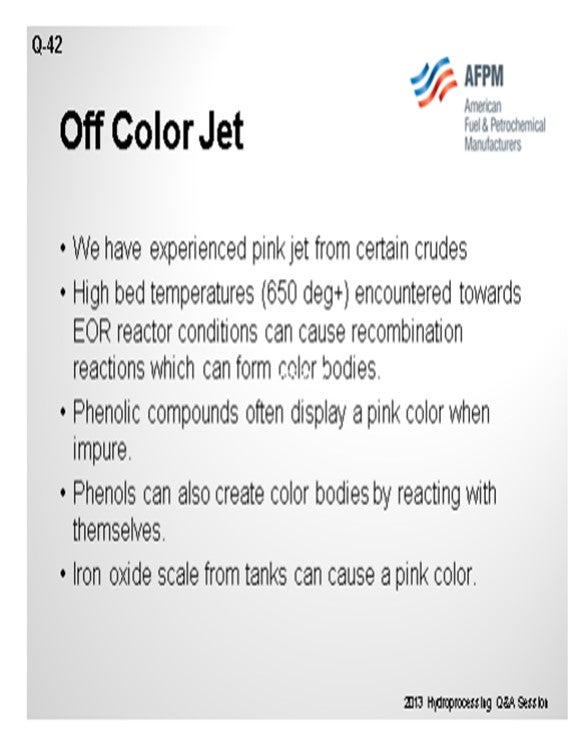
JEFF JOHNS (Chevron Products Company)
I have a couple of comments and a question. One cause of off-test jet I have seen is a small amount of crude contamination coming from a crude unit cooler that carries into the hydrotreater. If you get high molecular weight, especially if you observe multi-ring compounds, it can take just one part per million to turn it into color. My question is if any of the panelists has implemented any additional testing, beyond the normal jet final product testing, to help detect color issues and prevent them from the final product.
GATES (Motiva Enterprises LLC)
The answer is no, we have not. But you do bring up a good point, which is that you can also wind up with color if you have, for instance, an exchange or leak where a very, very small amount of material has been known to throw the JFTOT (jet fuel thermal oxidation tester) off spec.
SHARPE (Flint Hills Resources, LP)
We have what we call a UV (ultraviolet) color test. It is a homegrown, non-ASTM test. We just put a sample of jet into a clear jar that is in a box, and then we illuminate it with UV light. Over the years, we have standardized the timeframe for the test to be two hours. This test is just a simple indicator of whether your jet will make it up the pipeline looking like it did when it left the refinery. So that has been one of the issues. With regard to the leaks in the crude exchangers, when we have seen them, we have learned that the least of your problems will be color because usually other properties go off spec quickly on jet fuel as well. But yes, you definitely see color when you have a leak.
JAMES ESTEBAN (Criterion Catalysts & Technologies)
In a former position prior to working for Criterion, I experienced an issue with a crude unit in the refinery which had a kero (kerosene) draw on the side of our preflash column. We actually drew everything from vacuum resid to kerosene all the way into the kero stream which fed a kero hydrotreating unit. It was quite a challenge to recover from the event. We found that while operating the hydrotreating reactor, it took us quite a while to get all of the color bodies washed through the reactor. Then when we raised the temperature targeting ULSK (ultra-low sulfur kerosene) mode operation, we saw a release of those color bodies again. So in some cases, you may think you have washed everything away; and then ultimately, you have to continue washing. Even in some high-temperature stages, you may have to do the same step to maintain that color in ULSK operation.
WENDY WILDENBERG (Flint Hills Resources, LP)
We have a refinery capable of making ULSD #1 fuel, as well as jet fuel. One time, we learned the hard way that if we change-out catalyst and ramp up temperature too quickly afterward, we can create quite a bit of color, which takes a while to wash back out. In that unit, we implemented a procedure for jet fuel production. We let the sulfur be a little higher for the first several weeks and then slowly ramp up the temperatures.
PAUL YON-HIN (Nalco Champion Energy Services)
Naturally occurring phenolics in crude oils are usually the cause of color formation of jet fuel. When exposed to air, any phenolic compounds not substituted at positions 2, 4, or 6 in the parent molecule are highly prone to oxidation to generated quinones that are colored compounds. For example, phenol is oxidized to a pink color in the presence of a trace number of metallic impurities, such as iron and copper. One way to prevent such color formation during processing and storage is to Merox™-treat the fuel if it has a high phenolic content or to just subject the jet fuel to a caustic wash.
MUTHU SRINIVASA (Criterion Catalysts & Technologies)
Jet color issues are complex and explainable only on a molecular level. Unfortunately, identifying the complete molecular composition of a stream is not possible in practice; so the term “color bodies” lumps certain molecules which impact the absorbance and transmission of light. Outside of particulates, nitrogen and aromatics species are the two molecular groupings which result in color changes.
Feedstock aromaticity, which includes the breakdown into larger, more complex and even isomeric multi-ring molecules, can influence product color. Although crude sources can impact the feed aromaticity, most often, jet color issues result from increasing the feed EP combined with a changing cracked feed concentration and/or quality. In general, increasing EP introduces larger aromatics which may saturate insufficiently at hydrotreater conditions for color improvement. With cracked stocks, the complexity of the aromatic species increases, resulting in molecules of higher initial color and lower saturation effectiveness in the hydrotreater.
Operationally, off spec jet color is often associated with elevated temperature operation resulting in poor saturation of aromatics. Since the thermodynamic limitations of aromatic saturation are dependent on hydrogen partial pressure, jet hydrotreaters operating at low hydrogen partial pressure, either by design or due to low hydrogen treat gas purity, can experience color issues at moderate temperatures. Dehydrogenation of saturated aromatics can give the product greenish color directly from the unit or a red/brown color if processing a higher endpoint feed.
Insufficient nitrogen removal can leave certain refractive nitrogen species in the jet product which create color stability issues. Although initially appearing clear, the jet product may fail color stability and turn greenish when exposed to light. Insufficient denitrification can result from operating at low temperatures which satisfy product sulfur requirements, high space velocity, low hydrogen partial pressure, or low catalyst activity.
Blue jet is unique and may be associated with azulene, a kerosene boiling range isomer of naphthalene that reflects a blue color. One potential source of these molecules is the synthetic crudes which have undergone severe high-pressure hydrotreatment before being distilled into fractions at the refinery. Dehydrogenation of these molecules in the jet hydrotreater will turn the jet product blue.
Operationally, reversing jet color issues involves increasing and maintaining sufficient hydrogenation and denitrification. Increasing temperature may benefit both to a point, after which further temperature addition may promote additional color issues through aromatic condensation. Improving the feed quality or hydrogen partial pressure or replacing the catalyst to improve activity at lower temperature will improve color issues. Higher hydrogenation and denitrification activities of a NiMo catalyst system should be considered.