Question 41: In an effort to increase margins on hydrotreating units, what strategies and/or new technologies are refiners employing to minimize utility usage? What are the economics and reliability of adding a power recovery turbine?
LIOLIOS (DuPont Clean Technologies)
In the IsoTherming® liquid hydrotreating process, there is a substantial reduction in utilities on a unit we just started up with 40% straight-run/60% light cycle oil. The customer reported a 60% reduction in overall utilities in operating that unit compared to a trickle-bed unit. I show some percentages on the slide. The savings are mainly in fuel gas and power. Directionally, that could be one way could consider if you want a substantial reduction in energy cost.
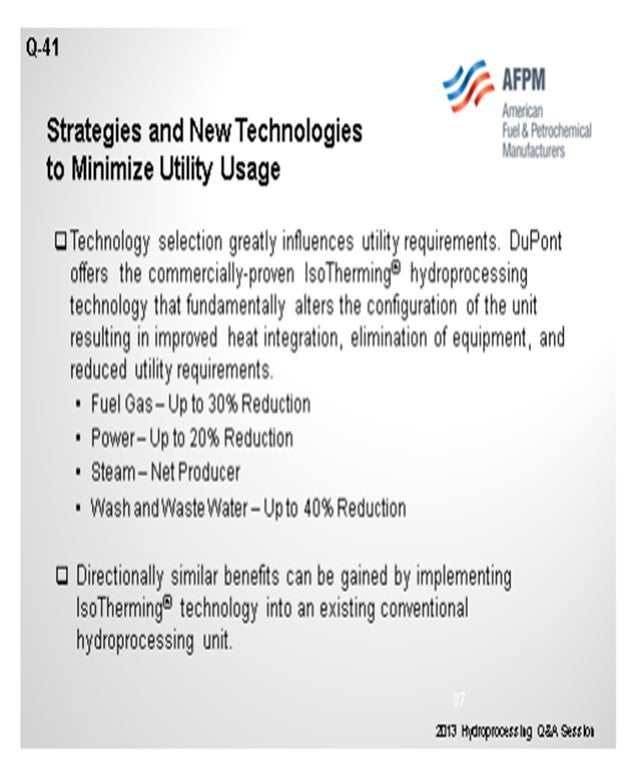
The second strategy is to add a power recovery turbine. While certainly presenting the opportunity to save money, these turbines do tend to be unreliable and can cause issues due to their unreliability. Finally, for older units without hot high-pressure separators, there is an opportunity for some minor energy consumption savings. However, again, the capital costs have to be weighed against the economic incentives and utility savings.
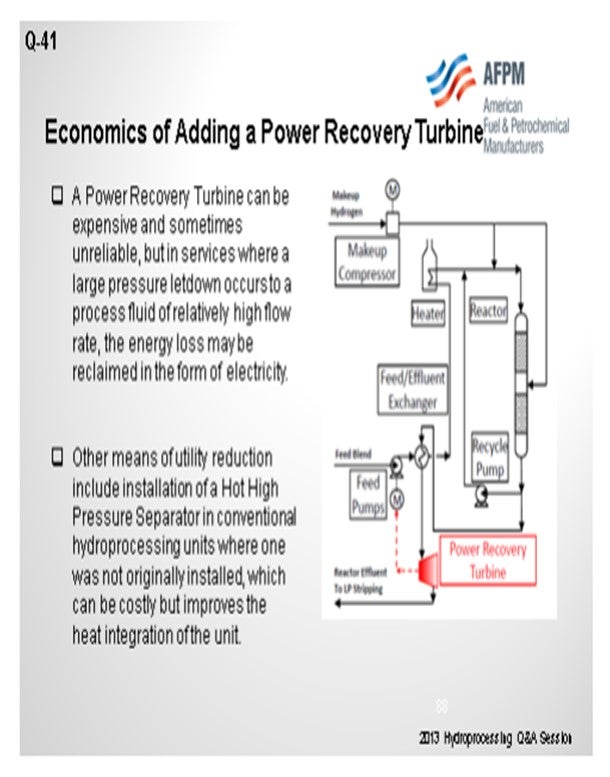
SHARPE (Flint Hills Resources, LP)
We have the ghost of many power recovery turbines in our refineries. We have had power recovery turbines on our gas oil hydrotreater and on our naphtha hydrotreater charge pumps. The power recovery turbine and the clutch were removed from service on the GOHT (gas oil hydrotreater) due to reliability issues with the seals. The naphtha hydrotreater power recovery turbine was taken out of service due to LDAR (leak detection and repair). We do not have any power recovery turbines planned in our current capital project scopes. In our Pine Bend refinery, we have also had power recovery turbines, both on the high-pressure separator letdown to drive the charge pump and the rich amine letdown to drive the booster pumps. The amine booster pumps worked a little better, but all of them had steel issues and were bad actors from a reliability standpoint.
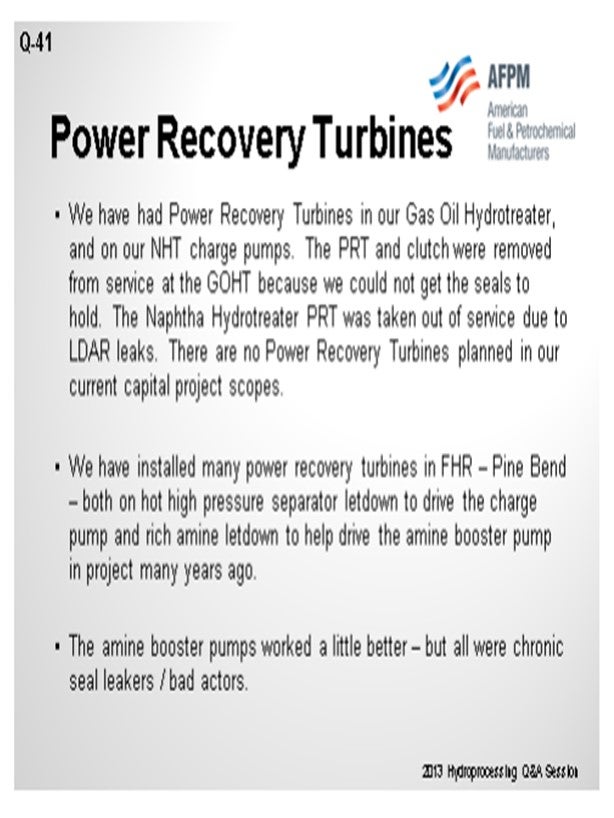
Doing the math on the energy saved versus maintenance cost plus the cost of upgrades for the safety systems has led to all but one of them being shut down permanently with piping having been removed to eliminate diplegs. The energy savings are small, and the repair costs were high. The power recovery turbine needs to have a correct seal design. Probably some more of the modern ones might have better luck. We just did not have them, and I think we lost a lot of enthusiasm for them over the years. To avoid over-speed and meet industry standards, instrumented safety systems need to be maintained and upgraded. One of the most important points mentioned on this slide is a big factor to be considered as well, and that is the fact that your relief design requirements for vapor blow-through are substantial.
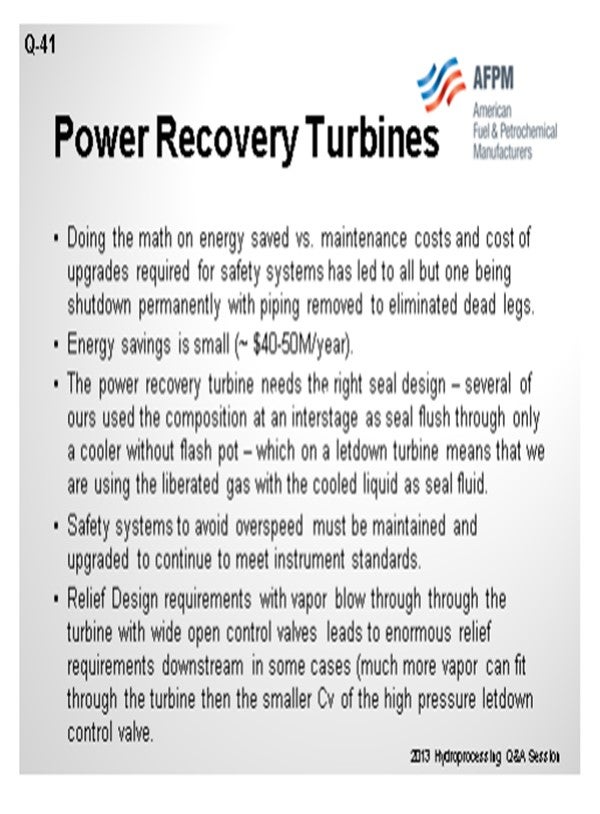
GLENN LIOLIOS (DuPont Clean Technologies)
Because refiners are continuously exposed to changing crude and product market values, margins fluctuate along with those market values. Each unit within the refinery must consider its available options to minimize the operating costs associated with changing crude and product market values, both in terms of energy requirements and frequent maintenance. For the hydroprocessing unit, minimizing hydrogen requirements and extending catalyst run length have traditionally been the targets of reduced operating costs. While maximizing catalyst run length continues to be a challenge, refiners in the U.S. have recently benefitted from a decrease in natural gas pricing, in turn resulting in lower hydrogen costs and lower operating costs for the hydroprocessing unit. But further reducing the unit’s operating costs through minimizing utility consumption has proven either too costly or the improvement projects do not result in significant utility reduction. Ultimately, the effort to minimize utility costs begins with technology selection. While most conventional hydroprocessing units consisting of trickle bed reactors are differentiated by performance of the reactor system, including catalyst and internals, the difference in utility costs are relatively minor. However, DuPont offers a commercially-proven hydroprocessing technology – IsoTherming® – that fundamentally alters the configuration of the unit and results in improved heat integration, elimination of equipment, and reduced utility requirements. By eliminating the hydrogen-rich recycle gas loop present in all conventional hydroprocessing units, IsoTherming® technology offers the following utility savings, as seen in Table 1.
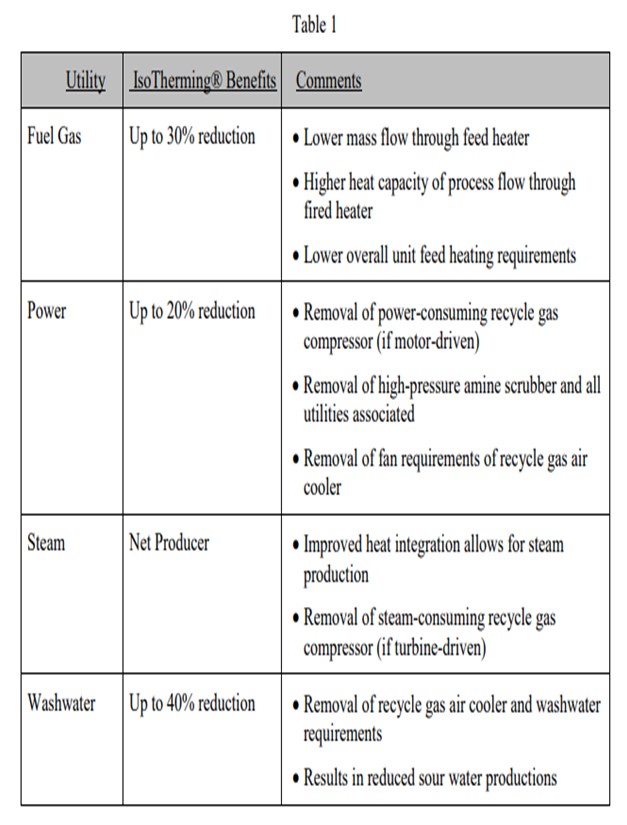
Directionally similar benefits can be gained by implementing IsoTherming® technology into an existing conventional hydroprocessing unit. The resulting configuration may be similar to that shown in Figure 1 where the IsoTherming® reactor may be new or its operation converted from an existing reactor. The revamped solution allows for a reduced recycle gas circulation since the IsoTherming® reactor would receive its recycle hydrogen via the liquid effluent recycle. The reduced recycle gas circulation allows the refiner to reduce recycle gas compressor and feed heater requirements due to the reduced mass flow though each. Thus, power and fuel gas requirements may be reduced. In practice, as a result of a debottlenecked recycle gas loop, a refiner may rather choose to increase throughput or product quality in this revamp configuration as opposed to settling for reduced utility requirements.
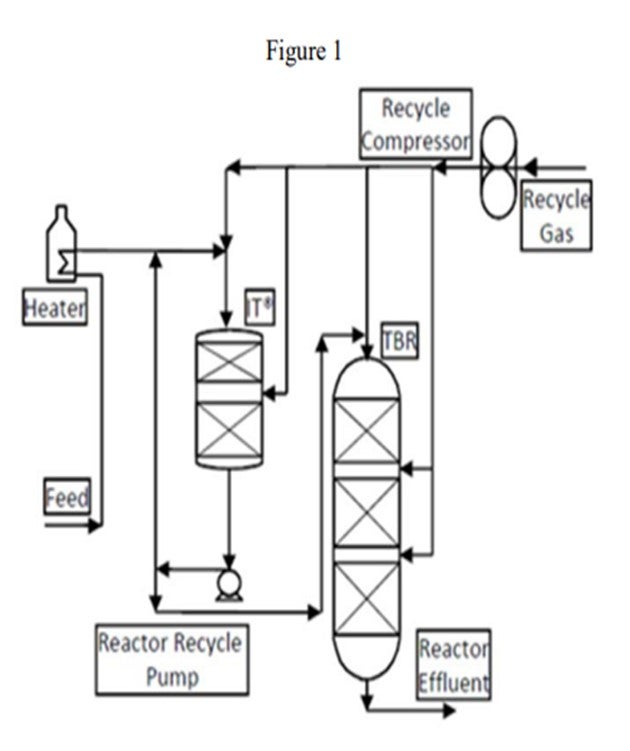
Another means of utility reduction involves installation of a power recovery turbine (PRT). The PRT can be expensive and sometimes unreliable. However, in services where a large pressure letdown occurs to a process fluid of relatively high flow rate, the energy loss may be reclaimed in the form of electricity, which can be used to power other equipment within the unit. If the pressure letdown is small and/or the process fluid flow rate is small, then the electricity recovered will be minimal; and often, the price of the PRT is not justified. Each refiner should evaluate the payback potential of installing a PRT for each case independently.
Other means of utility reduction include installation of a hot high-pressure separator (HHPS) in conventional hydroprocessing units where one was not originally installed. A HHPS can also be costly but improves the heat integration of the unit and reduces the requirement to reheat the reactor effluent liquid prior to entering the stripper. Directionally, any improvement in the heat integration of the hydroprocessing unit will typically result in reduced utility costs, so each refiner should consider how the operation of each specific unit may be altered to improve the efficiency of its operation.