Question 40: What process options are available for U.S. refiners to economically make 10 ppm sulfur gasoline? Discuss impacts to other product qualities (such as octane and vapor pressure) and how these secondary effects impact the gasoline pool.
DUBIN (Axens North America)
There are several routes to Tier 3 gasoline: post-treating, pre-treating, or a combination of the two. For Tier 2, we saw that about 80% of refineries invested in post-treaters. At the time, octane barrels were valuable, gasoline was in demand, and the capital cost was justified for installing a post-treater. As we move to Tier 3, we see a more stagnant gasoline market. Ethanol, as well as increased jet kerosene production, is limiting the amount of FCC naphtha available. There is not a strong demand for gasoline, and it does not appear to be changing.
For Tier 3, we will likely need to meet 10 wppm sulfur in the gasoline pool. This may entail 10 wppm to 20 or 25 wppm sulfur out of the FCC naphtha to meet the pool specs. Co-processing of orphaned gasoline streams will also be critical, like straight-run, unprocessed light cat (catalytic) naphtha, and any other raffinates. Those orphaned streams will need to be treated to help meet the 10 wppm in the pool.
Some of the Tier 2 units do have additional capacity available. Due to undercutting the FCC naphtha, there are additional barrels available to co-process in those units; however, not every unit is in that position. What may be required for these Tier 2 units is to increase the severity to get to Tier 3. This severity increase may be accomplished through elevated reactor temperatures or the addition of catalyst volume. Other revamp options to overcome hydraulic bottlenecks or product octane limitations include:
• adding a second HDS (hydrodesulfurization) reactor,
• choosing a more selective catalyst,
• adding a splitter to fractionate the light cat naphtha from the heavy cat naphtha if you are processing full-range naphtha,
• polishing catalyst to help control recombinant mercaptans, or
• adding of a complete second stage to your existing post-treater.
For those refiners who did not invest in a post-treater, there are fewer knobs to turn. Getting a cat feed unit to operate for a four- or five-year cycle is unlikely. Deeper desulfurization out of the cat feed hydrotreater may be a challenge. It could be entirely possible that the existing pressure level of the cat feed hydrotreater does not allow for the significantly deeper desulfurization needed to meet a Tier 3 direct gasoline off of the FCC main fractionator.
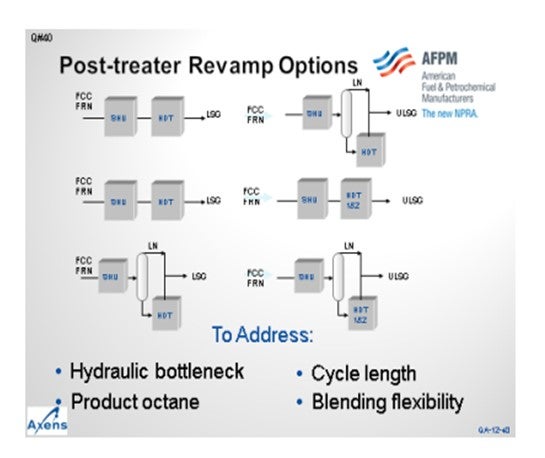
There are also some revamp ideas for cat feed hydrotreater units. A conversion of the cat feed to a mild hydrocracker has the benefit of increasing distillate production while meeting direct Tier 3 gasoline. Axens offers a permutable guard bed reactor system called PRS, which is a lead-lag guard bed for the cat feed hydrotreater. The PRS system allows for a continuous operation of the cat feed hydrotreater to help match your FCC cycle. The PRS system is an
interesting option for a capital-intensive unit like a cat feed hydrotreater.
However, there are still concerns for producing Tier 3 gasoline directly from the FCC main fractionator. Without a post-treater, you do not have any final control over the product sulfur meaning that any upsets in either the cat feed hydrotreater or the FCC main fractionator can have an impact on whether you can meet your gasoline pool sulfur requirement. For the cat feed hydrotreater, of concern would be the desulfurization level. On the FCC main fractionator, you need to maintain distillation control on the tail end of the heavy cat naphtha to ensure that you are pulling more sulfur into the naphtha tail during a main fractionator upset. Having a post-treater allows you to play catch-up with sulfur if there is an upset, as well as to operate with your cat feed hydrotreater down.
On the overall pool octane, we have seen that many refiners are octane-long right now due to ethanol. Reformers are operating at lower severity than they have historically operated, so there appears to be some room for octane loss in FCC gasoline desulfurization while still meeting the overall pool requirements.
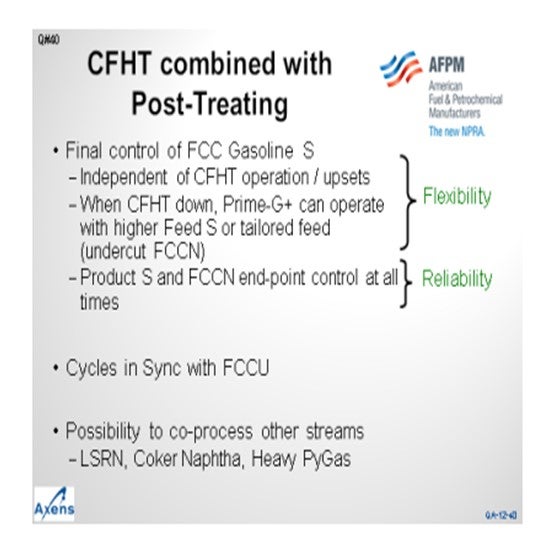
PIZZINI (Phillips 66)
Phillips 66 has experience with almost all of the major sulfur removal technologies that can be used to meet the 30-ppm spec, including conventional hydrotreatings, scan finding, S-Sorb, ISAL, catalytic distillation, Prime-G+, and caustic treating. Now the government wants us to ratchet that down to 10 ppm. So, for 10 ppm, we will have to treat additional streams. The slide lists several: butanes, pentanes, light cat naphtha, and light straight-run gasoline. So, our strategy, at least right now, is to look at treating those streams I mentioned using regenerative caustic treating and also revamping some existing hydrotreaters or conventional hydrotreaters to the newer technology.
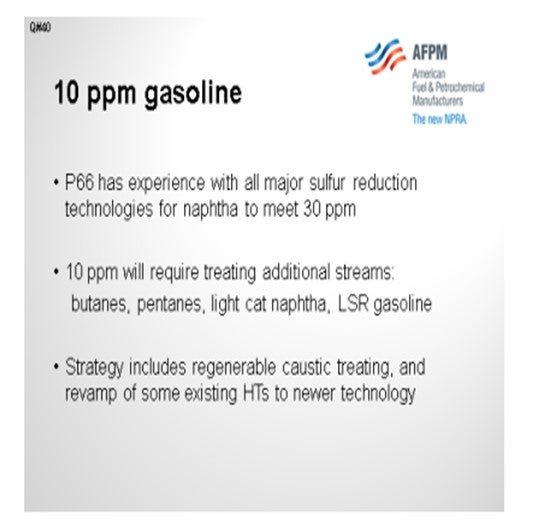
This example might be unique to this one location, but we do have a benzene extraction unit that removes the benzene from light reformate. That extraction is done with sulfolane, a solvent which contains some sulfur. There is a certain amount of solvent lost with the raffinate from that process, averaging about 10 ppm to 15 ppm. So, with a 10 ppm gasoline target, even that stream needs to be addressed. Right now, our plan is to put in a better solvent waterwash column. We currently have that in our scope for the Tier 3 project.
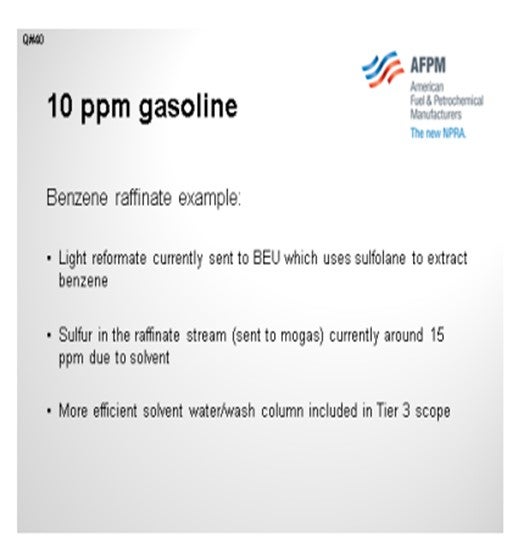
DUBIN (Axens North America)
There are several paths to meeting 10 wppm (Tier 3) ultra-low sulfur gasoline. Depending on site specifics, FCC pre-treatment, FCC gasoline post-treatment, or a combination of the two options can help refiners meet the Tier 3 regulations.
In the early to mid-2000s, approximately 80% of U.S. refiners addressed the Tier 2 regulations through the installation of FCC gasoline post-treatment. At the time of Tier 2, gasoline demand was strong, and the retention of octane barrels was key, which justified the cost of installing a new unit. Ahead of Tier 3, we see that the overall gasoline market is stagnant and octane barrels are not as valuable due to a number of reasons: ethanol, increased jet/kerosene production, etc.
For Tier 3, refiners will likely need to meet 10 wppm to 30 wppm in the FCC gasoline to meet the overall blending requirements. However, the processing of just the FCC gasoline streams may not be enough. Processing of orphaned gasoline streams will also be critical to meeting the Tier 3 pool levels. Those who invested for Tier 2 may have additional capacity in their existing units to co-process orphaned streams as many refiners are undercutting the FCC gasoline to maximize distillate production. Due to available capacity, as well as other factors, these Tier 2 units can likely meet Tier 3 through operating severity increases. Other units will need to be revamped. The primary drivers for the revamp of the post-treater all aim at addressing cycle length, hydraulic bottlenecks, product octane, hydrogen consumption, and increased blending flexibility. The main options for post-treater revamp are to add HDS catalyst volume, use the most selective catalysts, add a splitter, add polishing catalyst volume, or add an independent second HDS stage.
For those refiners who handled the Tier 2 requirements through adjustments to their FCC pre-treatment, they have fewer knobs to turn for Tier 3. Revamping the FCC pre-treater to desulfurize deeper can be difficult as a four- to five-year cycle life at a high desulfurization level is challenging. The existing CFHT pressure level also may not be compatible with desulfurizing the FCC feed to a level that will allow for direct Tier 3 gasoline. One option for those units with
a CFHT is to revamp the existing CFHT unit into a mild hydrocracker. This revamp scenario offers improved middle distillate production while helping to meet the Tier 3 ULSG (ultra-low sulfur gasoline) requirements. While this revamp scenario has a number of improvements that look attractive, a key concern when making ULSG direct from the FCC is that there is little margin for error on unit operation and FCC fractionation. This is due the lack of post-treatment to stabilize the sulfur levels before the gasoline material goes to the pool. The addition of an FCC gasoline post-treater allows for catch up on sulfur levels in the gasoline should the pre-treater suffer an upset. As well, the use of an FCC gasoline post-treater offers the ability to bring down the CFHT and replace the pre-treater catalyst while still maintaining gasoline production.
As to overall octane for the pool, further treatment of the FCC gasoline should not impact the pool significantly. While deeper desulfurization will result in lower FCC gasoline octane, that is certain, catalytic reformers are generally operating at very low severity and there is often room to increase octane barrels from the reformer.