Question 40: As it relates to overall catalyst cycle life management, please address the following issues: What are typical cascading practices for catalyst reuse after regeneration and eventual disposal that you employ? What quality control, catalyst properties and performance specifications, and/or warranties do you have in place for regenerated catalysts? What are some of the key decision criteria you use in determining whether to send a catalyst for metals reclamation, r
JAMES “TIM” CAMPBELL(Eurecat U.S., Inc.)
First, a response to the question: What are typical cascading practices that you employ for catalyst reuse after regeneration and eventual disposal? As the leading catalyst regenerator, Eurecat sees NiMo and CoMo hydrotreated catalysts (regenerated and regenerated plus rejuvenation) in ULSD, jet, kerosene, naphtha, and gas oil hydrotreating units. There is growing use of regenerated hydrocracking catalyst. These regenerated catalysts, or those regenerated and rejuvenated, may be used as an entire load or a partial load, depending on the specific application. Catalyst reuse management can provide substantial savings to the refining organization.
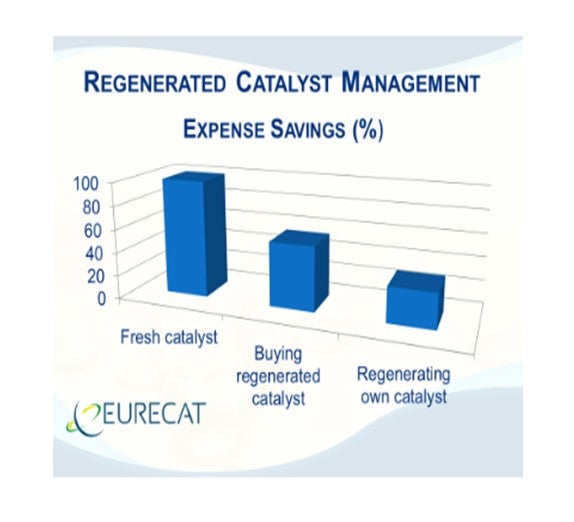
The second question concerned quality control, catalyst properties and performance specifications for regenerated catalysts. Eurecat has specific catalyst regeneration specifications for:
*Contamination metals (such as Si, As, Fe, Ni, V, Ca, Na),Physical (length/diameter, length distribution, and crush strength),
*Pressure Drop (measurement regenerated catalyst pressure drop versus fresh catalyst), and
*Activity (measurement of HDS activity versus fresh catalyst).
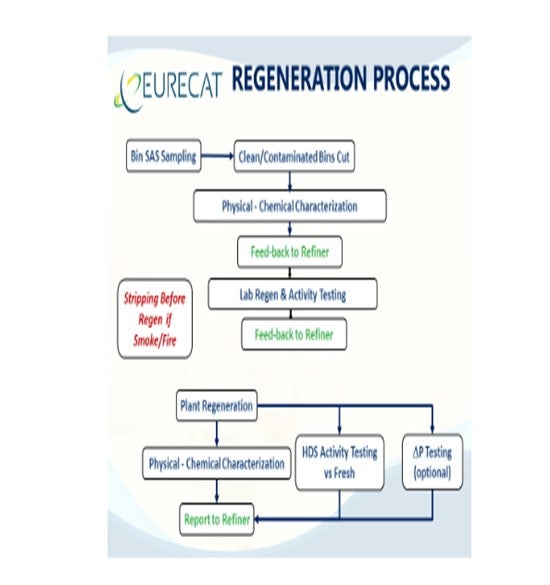
LIFENG ZHENG (Criterion Catalysts & Technologies)
Depending on the condition of the catalyst post regeneration, the catalyst can be cascaded to a less severe service [USLD to kero (kerosene), kero to naphtha, etc.] where the catalyst performance is less sensitive to activity. Regen can also be used on non-activity-constrained higher performance units or in units slated for a short cycle due to turnaround planning in, for example, the top bed of ULSD unit. In certain instances, it may be necessary to install some fresh catalyst to make up for a potential loss of activity and volume of the regenerated catalyst.
After a conventional regeneration and depending on the type of catalyst (Type I or II), the catalyst will typically regain anywhere from 70 to 95% of its fresh catalyst activity. Here your catalyst vendor can give guidance on the expected recovery for the particular catalyst. There will be physical catalyst loss due to breakage and attrition of pellets during unloading and regeneration that will need to be taken into account. Part of a catalyst bed that is unloaded may not be suitable for regen depending on the feed poisons and physical condition of the spent catalyst. Contact the regen vendor for additional details regarding warranties and catalyst properties on regenerated catalyst.
Some refiners actively manage a pool of their own regenerated catalyst because they can keep track of the condition of the catalyst based on the service and feed contaminants to allow cascading. Where it makes sense, Criterion works with the refiner to incorporate the regenerated catalyst into the planned loading for the next cycle. In a recent example, we successfully helped a customer transition catalyst from the bottom bed of a ULSD unit which was prematurely shut down into the top bed of a medium severity FCCPT unit in order to assist the customer with maximizing catalyst utilization.
The business case for selecting metals reclamation, regeneration, or disposal is ultimately based on economics. Regeneration is chosen when a use for the regen catalyst is identified within the refinery, if it is needed in the shared regen pool, or if there is a known market for this particular catalyst load and a third party is willing to purchase it. Service history is critical as catalysts with suspected high poison levels are not suitable for reuse. The catalyst cannot be vacuum-dumped, caustic-washed, or otherwise mishandled if it is going to be regenerated.
If the catalyst is not going to be regenerated, then it must either be reclaimed or disposed. Pricing and yield of precious metal could impact returns on metal reclamation. Reclamation companies usually charge a service fee for processing spent catalyst and give a credit for a portion of the metal reclaimed. Depending on the metals market, the metals credit can cover the processing fee; but with current depressed metals pricing, the credits usually do not offset the costs.
Disposal of spent catalyst is rarely done due to cost and potential environmental impacts. The transportation and disposal of spentcatalysts are governed by DOT (Department of Transportation) and RCRA (Resource Conservation and Recovery Act) regulations. The hazardous waste must be properly disposed of at an approved treatment, storage, and disposal facility.
HENRIK RASMUSSEN (Haldor Topsoe, Inc.)
For many years, refiners have cascaded used catalyst from a high severity to a lower severity service within their refinery. In order to do so, the catalyst needs to be regenerated and properly evaluated to make sure the level of poisons on the catalyst is acceptable for reuse in any service. Topsoe has, for many years, offered our proprietary ReFRESH™ technology, which is an add-on to the regeneration procedure. The ReFRESH™ process will restore the catalyst to 95+% of its original fresh activity, thus enabling the refiner to use the ReFRESH™ catalyst in the same service from which it was removed without any noticeable penalty in performance or cycle length.
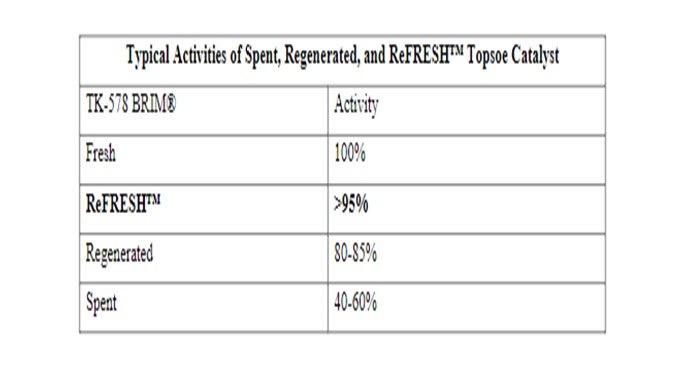
In order to ensure that the spent catalyst is a good candidate for regeneration, as well as a candidate for the ReFRESH™ technology, we have generated the following guidelines. The spent catalyst should meet the following criteria:
*Surface area greater than 80% of fresh catalyst surface area,
*As(arsenic)lessthan0.1wt%,
*Pb (lead) less than 0.15 wt%,
*Na (sodium) less than 0.3 wt%,
*Si (silicon) less than 1.0 wt%,
*Fe (iron) less than 1.0 wt%,
*No other metal [Ni(nickle), V(vanadium), etc.] higher than 1.0 wt%,
*Total contaminant level less than 2.0wt %,
*Average length of particle higher than 3.0 mm(milliliters) for 1/20” TL (transferline), and
*SCS(syntheticcatalysticscavenger)higherthan2.5lbf/mm (pound-force foot to Newton millimeter).
Catalyst with contaminant levels higher than shown above should be set aside and sent for reclamation, because it is not economically justifiable to spend money on regenerating and investing in ReFRESH™ technology for this material. Every year, Topsoe applies our ReFRESH™ technology to millions of pounds of regenerated catalyst, which are used again in high severity hydro treating applications such as ultra-low sulfur diesel and FCC pretreatment. Many of our clients have used the same catalyst up to three times.