Question 39: What procedures and techniques are you currently using to monitor and control cyanide corrosion on coker overhead circuit and light ends units?
SOLOMON (Athlon Solutions)
Not being a refiner, we do not run any cokers; however, we do monitor them. Cyanide corrosion is a hydrogen permeation phenomenon. It can cause cracking on high-stress zones and possibly blistering on dirty middle surfaces. So, we recommend the use of devices like hydro-steel or corrosion probes to monitor and understand what is occurring. These are good pieces of equipment that we use, and we rely on them quite heavily just to understand corrosion rates. So, if you do see cyanide corrosion or suspect it, we recommend using ammonium polysulfide (APS) and ensuring that you are using a good waterwash of the vapors. You may also want to do a supplemental application into the unsaturated gas plants, just as a precaution. And then, as with any chemical application, confirm you are using the proper dosage.
Filming inhibitors have been used, but they are just not as effective in coating as APS is in removing any of this corrosion. So, that is what we recommend. You can also use quaternary amines. They are very effective in blocking hydrogen permeation, but the key is to use these devices. You can also run a Prussian blue test to see what is going on, but that will really just give you a measure of corrosion that has already occurred or is ongoing. We rely very heavily on these two devices as an indicator for cyanide corrosion.
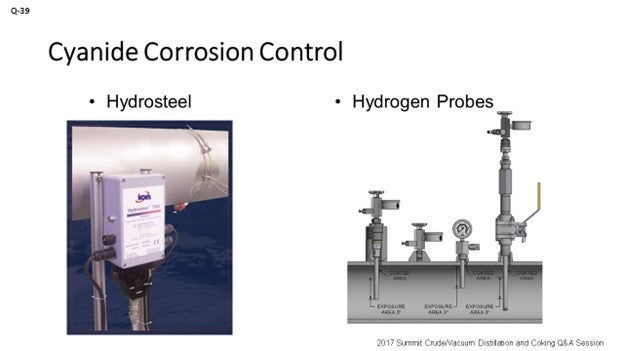
GAMBOA-ARIZPE (CITGO Refining & Chemicals, LP)
Kevin’s answer was fairly complete. I have to make sure I say Kevin, because you know we have a ‘Kevin’ and a ‘Darwin’ on the panel. In my mind, I thought, “Do not confuse their names.” I was once on a panel in Middle School. There was a Victor on the panel, and everyone kept getting our names confused. Victor and Héctor sound similar, so I understand.
Kevin talked about how one would want to monitor the coker overhead system. In our experience at CITGO, the overhead water boots of CITGO’s delayed coker fractionators are routinely monitored for pH, sulfides, ammonium chlorides, and iron. Collectively, however, there are only a handful of spot samples available that have measured cyanide content. Aside from those spot samples, the presence of cyanide can be inferred because some of the compressor coolers have shown a slight coloration of Prussian blue. Once you see indications of this color on the metal surfaces of system equipment, it can be assumed that cyanides are present in the chemistry.
The chemistry is complex, depending on the pH and temperature. The cyanide ion will readily react with other ions that are typically present in the coker overhead circuit and will produce many different salts and complexes. It is believed that if sulfides, chlorides, and ammonia are kept sufficiently diluted by managing wash water rates to the overhead condensers, then – by proxy – it is assumed that cyanide content will also remain within the acceptable limits of operation, from a controlled corrosion management standpoint. However, the wash water may or may not provide sufficient dilution. Hydrogen flux rate may be of value when we are using that technique (the hydrogen permeation that Kevin discussed), but CITGO currently does not utilize that process. It should be noted that bulk cyanide content in the sour water – independent of the concentration – can pose challenges to the wastewater treatment operation. This broader issue can be addressed by managing the total nitrogen content of delayed coker feed, which, in turn, is the function of total nitrogen in the crude feed. As you increase the crude nitrogen, you will intrinsically increase the cyanide content. So, if at some point you cannot manage the corrosion, just understanding the nitrogen/cyanide relationship will allow the Logistics Departments in your respective facilities to buy more appropriate feedstocks.
KEVIN SOLOMON (Athlon Solutions)
Cyanide corrosion is a hydrogen permeation phenomenon on steel that tends to cause cracking, commonly at high stress zones, and possible blistering on “dirty” base steel. Finding cyanide in an overhead circuit does not mean there is a problem. When it is suspected, the best option is to use a good wash of the vapors with ammonium polysulfide (APS) as far upstream as possible. Since cyanide partitions and concentrates into the gas phase, a supplemental application into the unsaturated gas plant feed is justifiable. APS should be fed to excess, and the normal way of confirming proper dosage is that water samples pulled should have a slight yellow tint: the color of contaminant-free APS.
Filming inhibitors are simply not as effective at coating as APS is at removing, and elimination at the source is always preferable, if possible. If APS is not an option and a filmer is needed, properly applied quaternary amines have been shown to be more effective at blocking hydrogen permeation. One common misconception is that the Prussian Blue Spot Test is a test for cyanide. In point of fact, it is a measure of corrosion that has already occurred and is ongoing. So, using both APS and the Spot Test have been demonstrated to be a useful approach.
CHRIS CLAESEN (NALCO Champion)
A proven way to control cyanides is with the use of APS. APS is dosed to have a slight excess, which is monitored by measuring residual APS in the sour waters from the different overhead boots. In some regions, APS is not readily available. In those areas, the monitoring can be done by measuring free and total cyanide and by using a Prussian blue spot test. The corrosion control is done with a passivator or a proprietary program. Further corrosion monitoring can be done with hydrogen probes, ER probes, and fixed ultrasound.
GREG SAVAGE (NALCO Champion)
Like FCC units, delayed cokers are susceptible to hydrogen charging from cyanide attack, particularly when processing high nitrogen feed slates and high coker severity. An inexpensive, quick field test to evaluate cyanide risk is the Prussian Blue Spot test, which can be used to monitor the amount of ferrocyanide and free cyanide in the condensed water. Hydrogen charging resulting from cyanide attack can be effectively mitigated using ammonium polysulfide, which can be controlled by using a simple color comparison residual test. Additionally, the risk of salting, blistering, and cracking can be reduced through effective waterwash. The waterwash rates in the wet gas compressor system and the overhead should be reviewed against industry Best Practices, laboratory results, and the calculated minimum.
DENNIS HAYNES (NALCO Champion)
Cyanides can be monitored quantitatively by chromatography methods. Specialized consultant companies offer the analysis where refinery labs are not set up to perform it. A quantitative Prussian blue spot test method has been used to confirm the existence of cyanides. Ammonium polysulfide may be used if active cyanide corrosion is a concern. Process unit monitoring may be done with hydrogen probes.
SAM LORDO (NALCO Champion)
Besides monitoring through testing (for example, spot test or IC for cyanide or color test for ammonium polysulfide), one can use hydrogen meters to track the H2 permeation, which is the outfall of cyanide-induced corrosion.