Question 37: Silicon poisoning of NHT catalysts has been observed in refineries without coking units. In your experience, what are the potential sources of silicon and what are the best practices to manage risk of such poisoning?
Greg Harbison (Marathon Petroleum)
Marathon has had to deal with issues of non-coker silicon in naphtha’s since at least 2001. For background purposes, it is Marathon’s experience that silicon blocks the pores on hydrotreating catalyst and can impact catalyst activity. In severe cases, silicon breaks through to the reforming catalyst can occur where it can form silicon dioxide during the regeneration process which can cover the platinum sites. In general, it is our experience that this poison is permanent. Two of our CCR units experienced significant breakthrough almost simultaneously in the early 2000’s. The primary performance issues that we observed at the time was increased carbon make which limited unit capacity.
We know that silicon is present in some of the crude oils we purchase. We also suspect silicon can be contained in some our purchased naphtha’s. In the case of the silicon in crude oils, we understand that the silicon is produced via decomposition products from use of anti-foaming agents in the oil production process, and that it varies. We do believe that the amount of silicon in our crude slates has also increased over time.
Marathon uses available hydrotreating catalysts with greater silicon adsorptive capacity to minimize breakthrough of silicon from the NHT to protect the reformer downstream. We have developed guidance for capacity versus silicon slip and use those guidelines extensively; it’s important to note that silicon capacity and silicon slip to the reformers are very different functions. Some companies also market silicon trap material that could be loaded on the top section of the NHT reactor and high surface area main bed catalyst to help capture as much silicon as feasible before silicon breakthrough occurs. Obviously there can be a tradeoff here with catalyst activity. Space velocity also affects the life of the catalyst bed, and silicon uptake is not the same in all our units.
Within Marathon, we use spent catalyst contaminant information and especially silicon to help plan for the expected life of the next NHT catalyst load. As a part of our evaluation, we will also consider the use of high surface area catalysts and regenerated catalysts cascaded from other hydrotreaters in our system. Silicon rather than pressure drops builds up and/or catalyst activity is becoming the key reason for catalyst replacement in some of our NHT units. Each of our NHT units has a philosophy to pro-actively schedule catalyst replacements based on the catalyst selected, the amount of feed processed, and a post audit of the recent runs. Oftentimes this has subsequently led to off-cycle catalyst change outs, suboptimal exchanger cleanouts, heater cleanouts, and semi-regen unit catalyst regenerations.
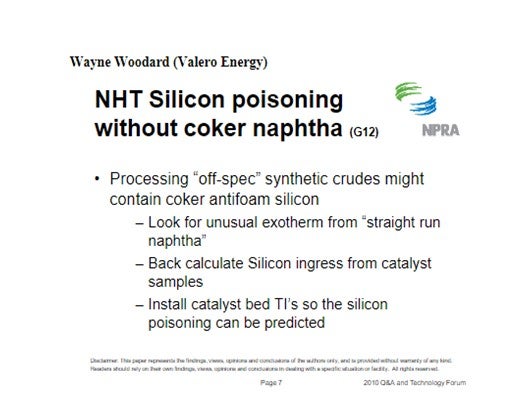
John Clower (Chevron)
Sources of silica in the naphtha boiling range are attributable to anti-foam injection, whether at the refinery (Coker/Visbreaker) or at the upstream crude production site. Management of risk is the same for any origin:
A refiner should consider the installation of a silica trap to remove the material upstream of the reactor if the silicon source cannot be removed. Also, the refiner should install NHT catalyst with a high capacity for silica uptake.
Kevin Carlson – Criterion Catalysts & Technologies)
In the past, the principal silicon (Si) source was found to be from antifoam addition to delayed cokers resulting in siloxanes being cracked into the naphtha boiling range. While this still occurs in the refinery, the shift to higher viscosity antifoams has resulted in increased levels of Si in the heavier coker streams. In addition to this shift, the increased production of coker derived synthetic crudes from Canada & Venezuela as well as the use of flow improvers for increased crude production capability has increased Si content from these hydrocarbon sources.
While eliminating the Si can be problematic, effective mitigation can be accomplished with the proper catalyst solution. Si is removed with alumina based catalysts, not by the active metals sites, but by adsorption of the Si containing molecule on the surface hydroxyl groups of the alumina support. This results in a thickening layer of Si being formed on the alumina surface. As this continues to occur, the pathways into the catalyst pellet become blocked resulting in an effect deactivation of the catalyst. Catalysts best suited for Si-removal have both high surface area and a pore characteristic well suited for minimal diffusion into the catalyst pellet.
In selecting the Si-trapping catalyst, it is important to choose the proper catalyst for the type of hydrocarbon being processed. In naphtha streams we would utilize a high surface area & high activity catalyst such as DN-140 or for increased Si capacity a specialized Si-trap with very high surface area such as MaxTrap [Si].
Gregg McAteer (Nalco Company) The major source that we are aware of is the silicon based antifoams used in oilfield production. The best practice to manage the risk of such poisoning is to (if possible) work with the producer to make them aware of the need to minimize antifoam use. The producers often see antifoam as an inexpensive solution to an operating problem, so over-use is not a problem to them.
Sam Lordo (Nalco Company) A major suspected source of a recent upswing of silicone related poisoning is the use of low molecular weight or gross overfeeds of silicone antifoams in the production of crude oils. There recent reports of some Gulf Coast and Mexican crudes that are suspected to cause accelerated NHT catalyst bed deactivations. Another potential silicon source (different from silicone) are certain Canadian syncrudes. Instead of coating the catalyst as the silicone are prone to do, the silica/silicon particulates as very small and entrained up the crude tower into the naphtha section. These very fine particulates can block the pores of NHT catalyst.