Question 35: When processing tight oil crudes, are lower bed pressure drop problems in VGO/resid hydrotreater reactors a concern? If so, what mechanisms explain this issue?
LIOLIOS (DuPont Clean Technologies)
The highly paraffinic nature of the tight crudes and the destabilization of asphaltene molecules can cause precipitation and agglomeration. One of our customers with a gas oil mild hydrocracker switched feedstock to increase amounts of black wax crude. This was a five-reactor system. A guard bed reactor was first, followed by four other reactor beds. In the polishing reactor bed, this customer saw an increase in pressure drop. It was theorized that this pressure drop was caused by asphaltene precipitation and polymerization in the bed.

The following graphs show some of what was happening at this unit. It is a constant feedstock. They raised the temperature to get some additional cracking. You will notice an elevated pressure drop in the last bed shortly after they increased the severity of the unit. If you look at the next chart, you can see where they decreased the severity of operation of the unit and the pressure drop recovered. Our theory is that there was a recombination of those asphaltenes.

SHARPE (Flint Hills Resources, LP)
We have had no second and third bed ∆T problems when running high rates of Eagle Ford crude. When there were high bed ∆Ps in the lower treating beds, they were usually a result of coke fouling due to hydrogen starvation, and low hydrogen partial pressure.
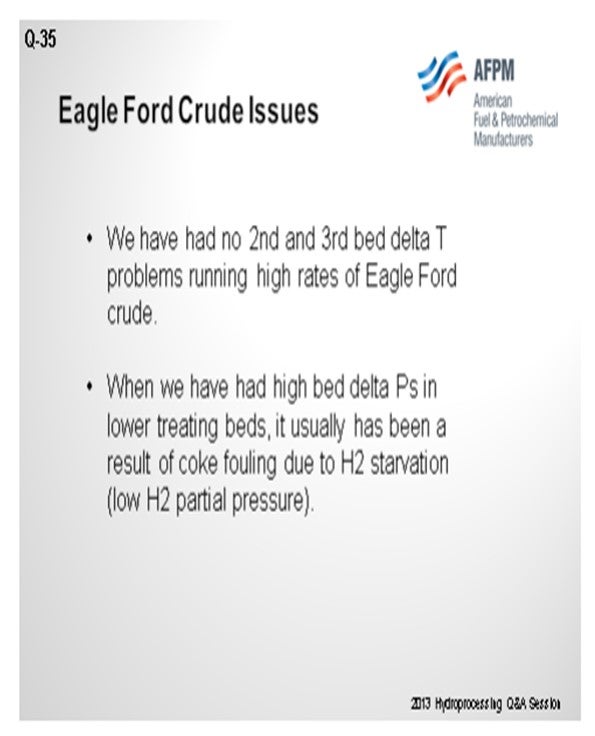
GLENN LIOLIOS (DuPont Clean Technologies)
The highly paraffinic nature of tight oil crudes, and the potential increase in asphaltene precipitation when these crudes or cuts of these are mixed with polar asphaltenic oils or cuts, has been well documented. The increase in paraffin content can lead to destabilization of the asphaltene core which can then agglomerate to form larger macromolecules that may precipitate out under hydrotreating conditions.
A number of published documents2 detail the causes and reactions behind this phenomenon and outline methods to determine which crude type and cuts are compatible and what ratios are required to minimize the chance of this phenomenon occurring.
Much of the industry experience indicates that asphaltene precipitation and fouling in process units normally occurs in regions of high heat flux when agglomerated asphaltenes easily crack or dehydrogenate leaving coke-like deposits such as feed/effluent exchangers or where hydrotreater reactions are initiated; i.e., the top bed of a hydrotreating reactor. However, it was observed that a gas oil mild hydrocracking unit experienced a noticeable increase in pressure in a final polishing reactor after the feed to the unit was switched to process a feed that had been mixed with an increased percentage of highly paraffinic (black wax crude) feedstock. At the same time, the severity was increased by lowering the throughput without reducing inlet temperatures. The polishing reactor was the last in a series of five reactor beds, the bed being a separate bed reactor. During the observed increased pressure drop in the polishing reactor, no appreciable pressure drop was observed in the guard bed or main reactor beds. It is important to point out that after the space velocity and feedstock to the system were normalized, the pressure drop decreased almost to the baseline range prior to the event.
It is theorized that the observed bed pressure drop increase in the last bed was a result of asphaltene precipitation and polymerization on the bed that occurred after increased severity reactions cracked the smaller molecules that kept the increased asphaltenes in solution. According to work conducted by Wiehe on asphaltene precipitation3 , asphaltenes are maintained in solution in oil by a micelle type of configuration. This theory has been also explained by other authors4 . The asphaltene core is surrounded by a solvated shell that consists of resins. Resins are molecules with aromatic and naphthenic rings.
Under high severity conditions such as those experienced in this mild hydrocracker operation, the resins can crack into smaller molecules. This can disrupt the micelle type configurations at which asphaltenes are kept in solution, and the asphaltenes can precipitate upon cooling.
Analytical tests carried out on the hydrocarbon feed samples indicated that the asphaltene content (heptane insolubles), although low in comparison with a heavy residue5, was found to be approximately three times higher than the one on the sweet GO FCC feed sample that was being recirculated to the unit and the regular GO sample fed to the GHC.
This theory explains why the upstream reactor beds did not experience a corresponding increase in pressure drop. If it were due to deposits, catalyst fines, or simply rust from upstream units, the first two reactors should have acted as filters preventing the last bed from getting plugged-up.
JUAN ESTRADA (Criterion Catalysts & Technologies)
Two primary mechanisms for pressure drop in bottom beds are coking and asphaltene precipitation. Coking results from operation at elevated temperatures and hydrogen deficiency. Asphaltene precipitation results from a reduction in liquid solvency. The design of VGO hydrotreaters with elevated pressure, low space velocity, and high treat gas rates helps minimize coking; however, elevated saturation of aromatics reduces the solvency of the oil, increasing the potential for asphaltene precipitation in the catalyst bed.
Processing tight oils in the crude diet reduces the aromatic content of the gas oils. For this reason, the coking potential of the feed is lowered, but the potential for asphaltene precipitation increases. With lower feed aromatics and severe hydrotreatment, the solvency change may be sufficient in the lower catalyst beds to precipitate asphaltenes introduced with the other gas oil components from conventional or synthetic-derived crude sources.
The mechanism of asphaltene precipitation from a reduction in liquid solvency has been connected to many historical pressure drop problems involving changes in operation and feedstock qualities such as aromatic and C7/C9 asphaltene contents and the distillation tail. Applying this accepted mechanism to lower bed pressure drop problems in units processing tight oil derived gas oils logically explains recent pressure drop problems in a few VGO hydrotreaters. Refiners continue to learn compatibility limitations of co-processing tight oils in the crude diet, including impacts on VGO reactor pressure drop growth has become a consideration.