Question 35: What are possible causes do you see of high product nitrogen in a naphtha hydrotreater processing coker naphtha? Please include monitoring, identification, and troubleshooting techniques, inside and outside battery limit considerations, and mitigation options.
SERGIO A. ROBLEDO (Haldor Topsoe, Inc.)
There are a number of possible causes of high product nitrogen in a naphtha hydrotreater. The list below details some of the most common.
1.Higher and/ or more difficult feed nitrogen,
2.Hidden tails not caught by ASTMD-86 method,
3.Lower outlet hydrogen partial pressure (as a result of lower hydrogen purity and /or lower hydrogen makeup/ recyclerate
4.Poor or incorrect lab analysis,
5.Amine injection downstream of the reactor for corrosion control,
6.Co-mixing of high-nitrogen product from another unit upstream of the sample point, and /or
7.Silicon poisoning of catalyst (i.e., either unexpected slugs or unknown).
Daily monitoring of feed nitrogen and distillation, via the Sim Dist (simulated distillation) method, will allow the refiner to adjust reactor temperature or control the final boiling point to meet the desired product nitrogen. Daily monitoring of product nitrogen is also key to establishing the percent of HDN (hydro denitrification) removal across the reactor system. Monitoring the treat gas hydrogen purity on a daily basis, and maintaining the right amount of hydrogenrate, are also key to ensuring that there is proper hydrogen partial pressure in the system to meet the expected level of nitrogen removal.
There have been a number of instances where poor lab analysis was responsible for a perceived under performance of a catalyst system. In a particular unit, start -of- run %HDN levels were the highest they had ever been – greater than 90% –after the installation of Haldor Topsoe’s highly succesful BRIM® catalyst. After a few months at this level, the % HDN suddenly dropped to the range of 30 to 50%, while the % HDS remained quite high. Even though the % HDS was still at or above 90%, silicon poisoning was suspected, as silicon impacts the HDN activity to a greater extent. However, the % HDN suddenly recovered top revious levels above 90%, which would not have occured if silicon poisoining had taken place. The lower % HDN turned out to be an analytical issue.
It is also always important to be aware of which streams are being injected into the product of the naphtha hydrotreater as they could artificially raise the product nitrogen.
ARTURO CONTI (Criterion Catalysts & Technologies)
High product nitrogen from a naphtha hydrotreater (NHT) processing some coker naphtha and providing feed to a catalytic reformer is of concern since nitrogen affects the performance of high value reforming catalyst. The naphtha hydrotreater product specifications are typically less than 0.5 ppm sulfur and nitrogen in the feed to the reformer. When higher product nitrogen is measured, it is critical to identify and correct the issue as quickly as possible. When product nitrogen is high, there are many possible causes. The fishbone diagram below describes many of these causes that need to be reviewed in order to narrow down the potential reasons. Coker naphtha specifically lowers the feed quality with cracked components and brings higher level of contaminants.
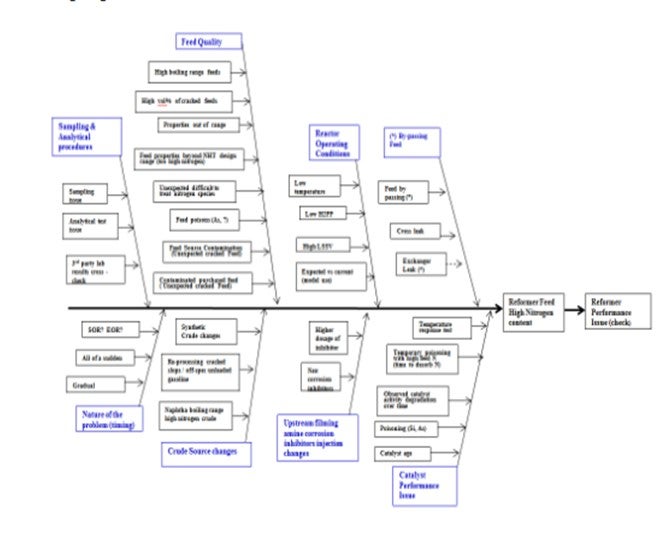
In a recent customer troubleshooting effort, the product naphtha from a NHT went off-test at same time as some new feeds were being processed in the refinery. Samples were analyzed at the refinery lab and various outside labs, as well as at our Shell Technology Center labs. It was surprising how variable the results were for the same samples. Results varied from 0.3 ppm to 2.5 to 3 ppm for each of the samples. The refinery analyses were in the middle, and the Shell Technology Center results indicated that all the samples were on-spec at less than 0.5 ppm.
After reviewing the possible causes and not identifying anything to explain the results, we recognized two other key pieces of information:
1.The other NHT unit processing SR feeds was also off-test, as was the naphtha from the ULSD unit, and
2.The reformer was not showing any signs of high feed nitrogen.
After reanalyzing samples to confirm the low product nitrogen, it was decided that analytical lab error was the likely cause, and the product nitrogen actually was within specification. Although it could have been any of the potential items which led to a high nitrogen product, analytical error was the issue here.