Question 34: When processing cracked naphtha, what is done to ensure that polymerization of the diolefins/olefins will not result in pressure drop problems in a reactor or upstream equipment?
GATES (Motiva Enterprises LLC)
Again, we are trying to prevent the polymerization of the olefin/diolefin. The primary concern is trying to prevent contact with oxygen because that will ultimately lead to gum formation. So the preference would be, if possible, to feed this hot to all the downstream units and avoid intermediate storage. If you will have to put it into tankage, the preference would be to use an internal floating roof tank and add some type of chemical stabilization. So typically, some kind of oxygen scavenger would be put in there. The length of time that material will be staying in tankage may dictate the level of treatment that will be done.
The other concern is that if this material contains diolefin/olefins, as it goes into your feed/effluent exchangers, prior to entering the reactors, it could potentially foul those exchangers. Often, you want to add soak hydrogen or hydrogen upstream of that exchanger. It may need to be considerably upstream to ensure that as the material is going into the exchanger and getting hot, there will be some hydrogen present to prevent that gum formation.
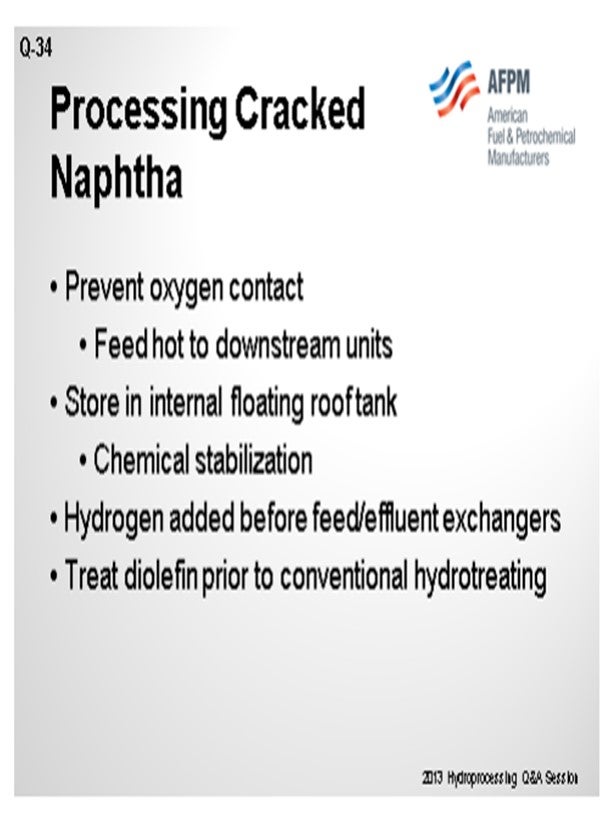
If you are actually going to try and treat cracked naphtha, you will typically want a separate diolefin reactor that will be run at lower temperatures to avoid the polymerization. You will use catalytic hydrogen to eliminate the diolefin and operate it in a regime such that you will not saturate too many of the olefins. You are ultimately trying to put the naphtha into gasoline, so you want to minimize your octane loss for the gasoline pool. As far as the catalyst, look for a catalyst with sufficient surface area and large enough pore volume – going back to Sal’s comment – to manage any silicon or arsenic that might be coming with that cracked naphtha.
WATKINS [Advanced Refining Technologies (ART)]
Two of the reasons we are worried about olefins and cracked naphtha in our naphtha hydrotreater are that they are a large consumer of hydrogen and also because the reactions occur quickly. Once the reaction with olefins starts and we have enough temperature, it is hard to stop. We do not want excess temperature to coke up at the top of our hydrotreater. Like David said, with coker feeds, we would like to see them brought in straight from the coker while still hot. They should not be sent to tankage; and if they are, you should blanket the tank somehow and keep it protected from oxygen.
The top of the hydrotreater is where we are worried about excess exotherm. We want to spread out that heat and do the reaction somewhat slowly, if possible. We do not want to have it occur all at once. Generally, we will recommend a graded bed to mitigate that pressure drop and start olefin saturation to avoid worrying about anything else like HDS and HDN or aromatics. In that case, we will be using a low-metals guard material at the top of our hydrotreaters, which also gives us the ability to pick up silicon.
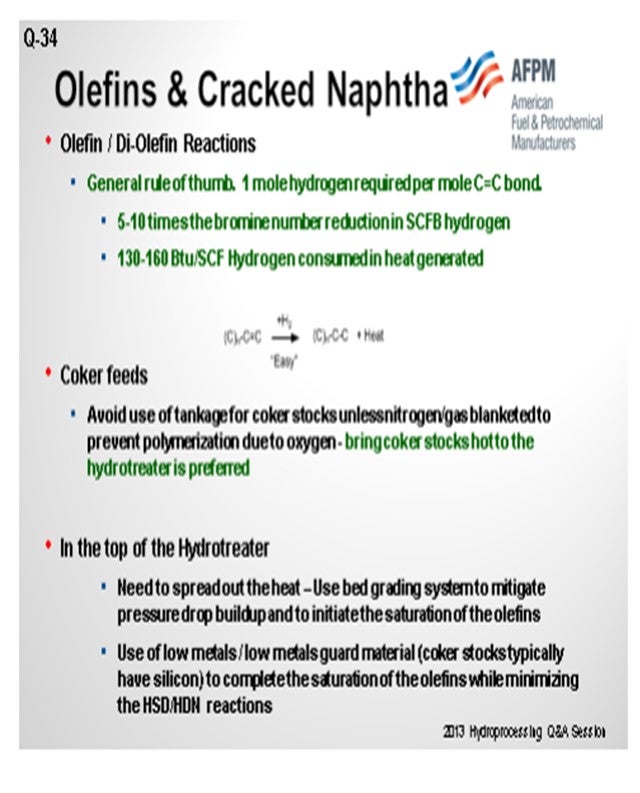
If your system has a high amount of diolefins, again, a dedicated diolefin reactor is important. At a much lower temperature, you can actually control just the diolefin reaction and avoid doing everything all at once by either controlling how much hydrogen goes to the hydrotreater or by keeping the temperature fairly low.
In the top of the main reactor of a coker naphtha unit, again, low metals, a guard material, is recommended. We generally then recommend avoiding the placement of very high-metals, high-active catalysts at the top, if at all possible, so we can try and do the reactions one at the time.
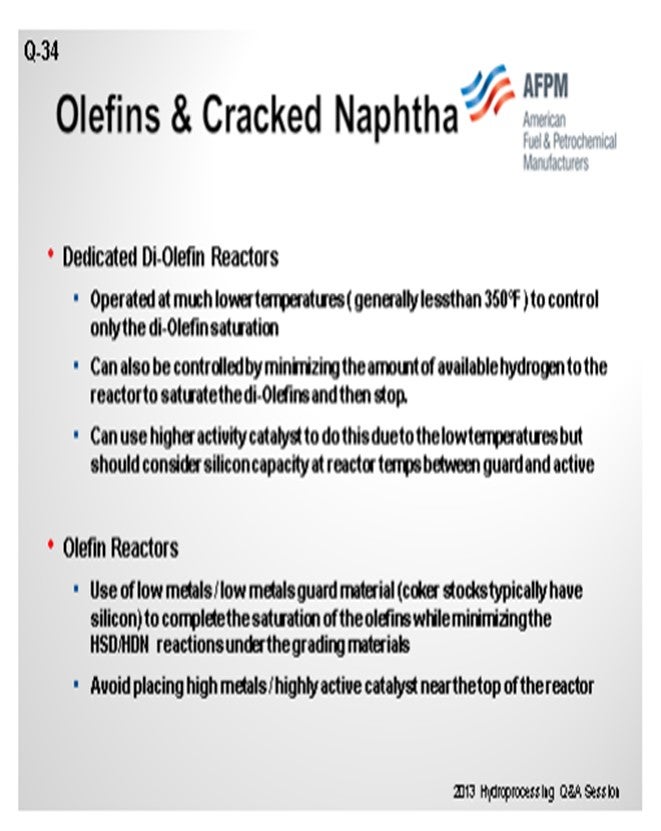
MUKESH PATEL (Reliance Industries Ltd.)
When we have to enable storage of naphtha, if necessary, which is the parameter we should monitor or what type of analysis should be carried out to determine if any gum formation has happened?
GATES (Motiva Enterprises LLC)
Off the top of my head, I do not know the ASTM (American Society for Testing and Materials) methods for that, but there are gums and then there are potential gums a
We run diolefin saturation tests, and I will put the ASTM method in my Answer Book response. We typically shoot for 60 to 80% diolefin saturation.
SHARPE (Flint Hills Resources, LP)
We run diolefin saturation tests, and I will put the ASTM method in my Answer Book response. We typically shoot for 60 to 80% diolefin saturation.
BRIAN WATKINS [Advanced Refining Technologies (ART)]
Processing coker naphtha can have several undesirable effects on the performance of the hydrotreater and the catalyst if the system was not properly designed to handle it. In general, coker stocks have a higher level of olefins present from the coking process. Once in the hydrotreater, these olefins will quickly get saturated (Figure 1), resulting in high hydrogen consumption and generation of a lot of heat. As a general rule of thumb, one mole of hydrogen is required per mole of carbon-carbon double bonds, or between five and 10 times the Bromine number reduction in standard cubic feet per barrel (scfb) of hydrogen. This additional heat [130 Btu/scf (British thermal unit per standard cubic foot) to 160 Btu/scf hydrogen consumed], if not managed properly, will initiate additional reactions, quickly creating a very high temperature rise. The high temperatures can accelerate coking and can lead to olefin polymerization, resulting in a dramatic increase in pressure drop. This can set an upper limit on how much coker naphtha can be processed based on the need to limit the heat rise or hydrogen consumption.
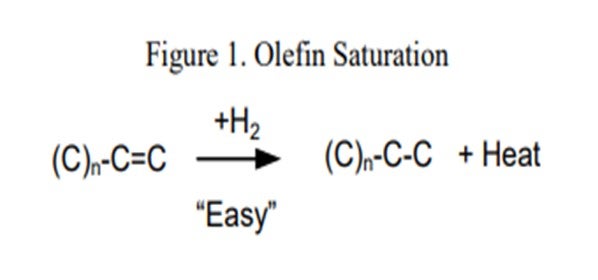
A system that is properly size and activity graded is extremely important when processing coker naphtha. ART recommends utilizing a grading system to help mitigate pressure drop buildup. A large inert hold down ring (GSK-19) with a very high void fraction used for trapping large particulates is placed at the top of the catalyst bed. A smaller diameter macroporous ring (GSK-9) that traps iron, as well as other fine particulates, is typically used in the next layer. After that, two types of smaller rings are used as active grading. These materials have a low level of active metals which help begin olefin saturation reactions, as well as provide additional particulate space at the top part of the catalyst bed. Avoiding the use of any highly active catalyst at this point is also recommended. Below the grading system, it is recommended to use a layer of larger size (1/10” or 1/12”) catalyst which provides activity for olefin saturation and additional void space for pressure drop mitigation. This layer is often a catalyst that is suitable for trapping silicon (and arsenic), which is another concern when processing coker naphtha.
An additional recommended practice to help prevent fouling and pressure drop buildup in coker naphtha units is to avoid contact of the coker feedstock with oxygen. It is preferred to bring the feed to the processing unit directly from the coker and avoid use of tankage. If this is not an option, then the alternative is to use a floating roof tank and purge the system to keep a nitrogen-blanket over the feed in order to keep oxygen out. Use of a diolefin treating reactor can also be considered. A diolefin reactor is operated at a much lower temperature in order to selectively catalyze the diolefin saturation reaction and avoid any excess heat generation from sulfur and nitrogen removal.
RAJESH SIVADSAN (UOP LLC, A Honeywell Company)
When processing cracked naphtha, plugging in feed exchangers and heaters may be caused by coking or polymer formation. Polymer formation can be caused by oxygen in the feed with cracked feedstocks. It is preferred to have cracked feeds fed to the hydroprocessing units directly from the upstream unit. Cracked feedstocks that do not come directly from the upstream unit should be stored in nitrogen-blanketed tankage. For units that process straight-run feeds from tankage, as well as cracked feeds, this straight-run feed should also be stored in nitrogen-blanketed tanks as this feed could provide the source of oxygen for polymer formation.
Processing these streams by themselves usually requires a two-reactor system with the first reactor operating at lower temperature to saturate the diolefins and a small portion of the olefins. The second reactor completes the olefin saturation and removes the sulfur and the nitrogen.
DENNIS HAYNES (Nalco Champion Energy Services)
Some issues may arise regarding polymerization. Polymerization in the feed stream may lead to fouling of heat transfer equipment and plugging of the reactor bed. A first step would be to minimize any potential for oxygen contamination as oxygen would act to accelerate fouling reactions. In addition, consideration may be given regarding the implementation of additive chemistries to inhibit polymerization rate (antioxidants) and minimize the potential for foulant (dispersants).
CHRIS CLAESEN (Nalco Champion Energy Services)
There are special low temperature reactor designs utilized to saturate the diolefins before they can thermally polymerize. Chemical programs with antipolymerants and dispersants can also help control polymerization and ∆P (delta P; pressure differential) increase. Reactor bed cleaning programs have been used successfully to reduce reactor ∆P caused by fouling with polymerized olefins and corrosion products.
RAJ PATEL (Haldor Topsøe, Inc.)
Designing a unit for processing coker naphtha can be challenging. The challenge comes from the silica in the feed which can poison the catalyst, high nitrogen in the feed which may be difficult to remove in low pressure units, and high quantity of olefin which can cause large temperature rises in the reactor, as well as very reactive molecules which are the conjugated diolefins. In the presence of small amounts of oxygen, or at elevated temperatures above 450°F, these molecules will radially polymerize to form gum that can foul exchangers or reactors causing poor heat transfer, as well as high rector pressure drop. If the feed contains a significant quantity of coker naphtha, then these diolefins must be removed at low temperatures to prevent gum formation.
The coker naphtha should preferentially be sent directly from the coking unit to the hydrotreater to prevent oxygen contamination. Even straight-run stock, which may be part of the feed component, must be prevented from contacting oxygen by storing the feed in a nitrogen-blanketed storage tank.
Even with strict adherence to avoiding feed contact with oxygen, the diolefins in the coker naphtha can polymerize at elevated temperatures. A dedicated diolefins reactor operating in the range of 300°F to 450°F will ensure that these highly reactive species are removed from the feed before polymerization can take place. Once the diolefins are removed from the feed, then the feed can be heated to the required temperature for silicon and/or sulfur/nitrogen removal. Topsøe has designed a large number of coker naphtha units with dedicated diolefin saturation units to mitigate the polymerization issues.
MIKE ROGERS (Criterion Catalysts & Technologies)
Hydrotreatment of cracked naphtha derived from FCCU, coker, or thermal cracking is a common refinery requirement. In some cases, refineries process these naphthas in a downstream catalytic reformer; while in others, hydrotreatment is necessary to meet gasoline blending sulfur requirements. Treatment of cracked naphtha can pose special challenges due to the presence of diolefins that are produced by the cracking reactions.
Diolefins in cracked naphtha streams from the FCCU and the coker will polymerize when heated, producing gums that foul the pre-heat equipment and main hydrotreater catalyst. To prevent polymerization, these naphtha streams are treated in a diolefin reactor operating at low but sufficient temperature to hydrogenate the diolefins. Typically, the diolefin reactor operates in a down-flow bubble phase with an LHSV of 2 hr-1 to 5 hr-1 and within temperatures between 180°C and 220°C (350°F to 420°F).
The effectiveness of diolefin saturation and protection against polymerization is monitored by measurement of the diene number in the reactor effluent. Typically, method UOP 326-08 (Diene Value by Maleic Anhydride Addition Reaction) is used to generate a MAV (maleic anhydride value) number representing approximately double the diene content in weight percent. Conversion of MAV in the diolefin reactor is in the range of 90 to 95%, and a target MAV number of less than 1 in the product stream from the diolefin reactor typically ensures protection against polymerization.
Catalysts loaded into a diolefin reactor should have a moderate but stable activity to selectively convert diolefins at low temperatures. For units processing coker naphtha containing silicon, a large surface area and high pore volume provide resistance to poisoning. Lastly, for units processing FCCU naphthas, catalysts with a low hydrogenation activity are favorable to minimize olefin saturation and octane loss.