Question 34: The cycle life of a high-pressure ULSD unit operating for maximum aromatic saturation and liquid yield is limited by aromatics equilibrium at elevated temperatures. What strategies or solutions do you employ to extend operation with maximum liquid yield?
PATRICK GRIPKA (Criterion Catalysts & Technologies)
Methods to reduce aromatics levels in ULSD product streams were discussed in detail in Question 52 at the 2015 AFPM Q&A. The key factors to maximize aromatic saturation highlighted were:
*Maximization of hydrogen partial pressure (H2 pp),
*Utilization of full catalyst activity,
*Optimization of bed temperature profiles,Selection of highest hydrogenation catalysts, and
*Application of Enhanced Aromatic Saturation options.
This question is more related to EOR conditions when you have employed all of the operational techniques but wish to further optimize the EOR performance without yield decline. If you are already maximizing H2 pp (partial pressure), achieving full catalyst utilization with state-of-the art reactor internals, and adjusting bed profiles at MOR/EOR (middle-of-run/end-of-run) to remain in region of optimum aromatic saturation, the following example illustrates the benefits of optimizing the nickel-molybdenum catalyst for your application.
In this example, a high-pressure (HP) ULSD unit which processes mostly cracked stock (primarily very high endpoint LCO) was using a high activity NiMo ULSD catalyst. This unit was initially commissioned in 2006; and over the years, it has experienced a significant increase in feed rate and difficulty of the cracked stocks processed. The increased severity was balanced with advances in Criterion’s catalyst technology to maintain arobust cycle life.
Last cycle, the customer used Criterion’s high activity NiMo CENTERA™ ULSD catalyst (Cat 1 in the figure below), but additional aromatics saturation was desired for anticipated feed quality changes to further maximize volume gain again next cycle. The challenge of processing 20% more feed containing 22% higher LCO of increased endpoint required improved feed and product diffusion to facilitate increased hydrogen addition. Under the new conditions, a different Criterion CENTERA™ NiMo catalyst (Cat 2 in the table below), having a wider pore carrier technology, was employed in the current cycle with additional improvement in performance realized.
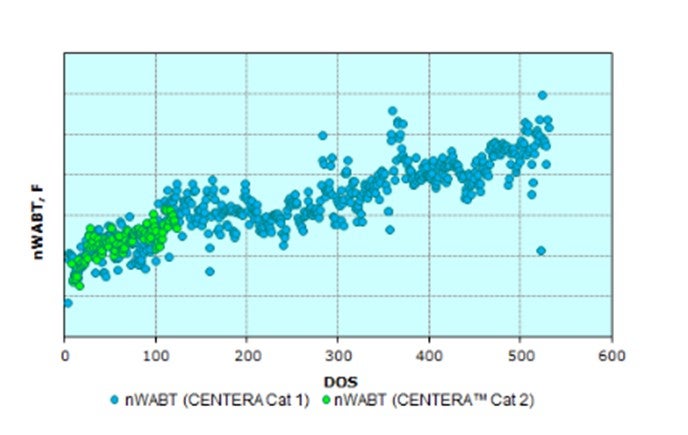
The overall normalized WABT performance has been similar, but the table below shows that asignificantly higher amount of very heavy LCO was processed; in addition, the overall feed rate was increased by another 20% compared to the previous cycle. This difference highlights the significant improvements in performance and yield maximization gained by using catalysts designed to process feeds with a higher than typical endpoint in ULSD; and ultimately, maximize the yield of ULSD.
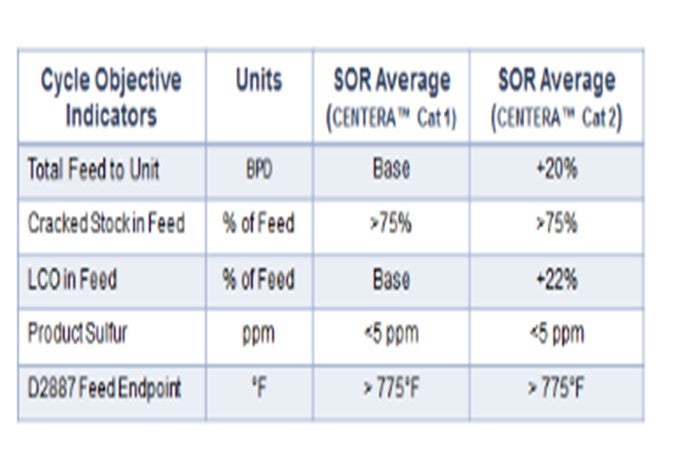
In addition, the catalyst system exhibited increased aromatic saturation capability, and the unit exhibited maximum volume gain by utilizing all makeup hydrogen available to the unit.
The incorporation of mild hydrocracking functionality into a catalyst system can provide additional improvement at EOR. Of course, one could reduce T-95 EP of the most difficult feed stream(s), but this will result in a reduction in overall distillate yield. In order to maintain liquid yields at higher temperature conditions which are present as the cycle gets near EOR, the appropriate use of mild hydrocracking catalysts in the catalyst system will allow the conversion of the higher boiling molecules while still meeting product specifications.
Utilization of a mild hydrocracking (MHC) mode of operation will first have to be evaluated for equipment and unit compatibility. Question 18 in the2011 Q&A specifically dealt, in detail, with the considerations needed to include MHC catalysts in a ULSD unit. The key considerations are:
*Safety: The unit must have a sufficient number of beds with sufficient quench to handle any potential exotherms from incorporation of MHC catalysts into the catalyst system. Depressuring systems may also be required.
*Sufficient H2Supply: The unit must have sufficient H2supply to accommodate the additional H2consumption when operating in MHC mode.
*Product Separation Capacity: It must be verified that the ULSD unit product separation system is able to manage the additional naphtha production that will result.
Once concluding these considerations have been met, then inclusion of MHC catalysts can be beneficial. One example is a ULSD unit in which the operatortook advantage of advances in catalyst activity improvements by incorporating MHC catalysts in the upgrading zone to process heavier feeds and increase the overall diesel yield. The customer challenged us to provide more T-95shift to allow them to upgrade heavier feeds while still maintaining overall diesel yield.
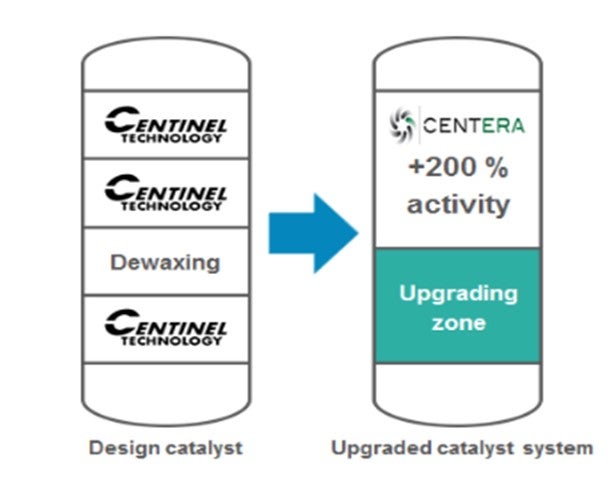
With the base T-95shift as the design catalyst cycle, the upgraded catalyst cycle in two subsequent cycles has shown the ability to process a significantly heavier T-95feed (about a 15°F increase in T-95shift in Cycle 2). With further improvements to the catalyst system employed in the Cycle 3, an even heavier feed has been processed (about a 30°F increase in T-95shift compared to the original cycle). After the first cycle, the customer challenged us to provide even more T-95shift to allow them to upgrade heavier feeds.
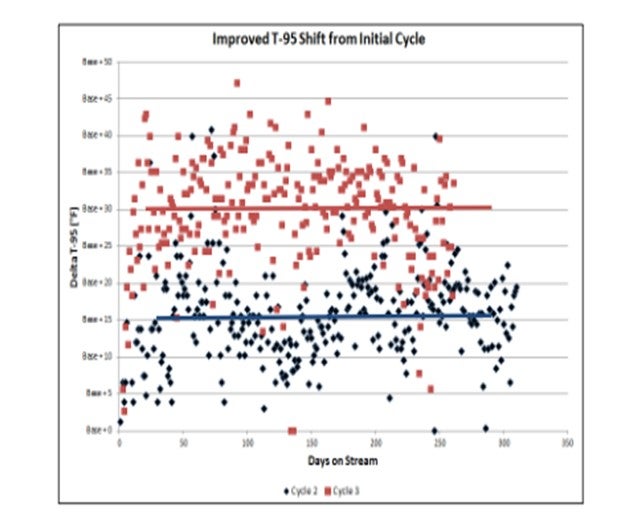
The greater T-95shift has also allowed the diesel yield to be not only be maintained but actually increased from cycle to cycle.
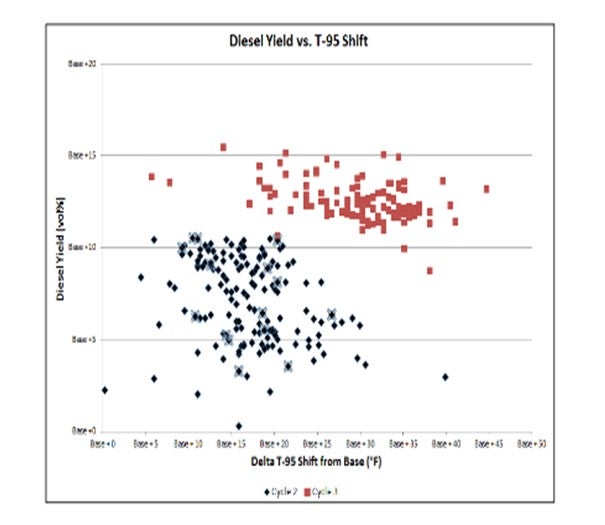
Overall, the T-95has been increased by about 30°F, and diesel yield has increased about 12 vol% compared to the base cycle. This improvement was achieved by optimizing the catalyst configuration and taking advantage of the combination of excellent pretreat hydrogenation power and the desired hydrocracking selectivity.
This higher diesel yields and processing heavier feedstocks has resulted in increased unit profitability of $6.5 to 9.1 million per year, as summarized below.
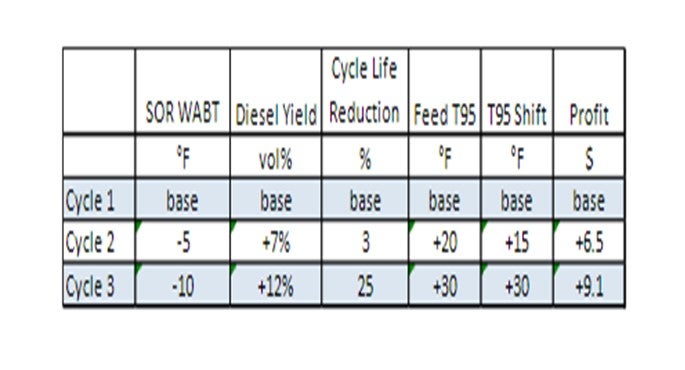
Incorporation of MHC catalysts into a ULSD unit can provide significant additional diesel yield due to endpoint conversion. The enhanced functionality and stability of MHC catalysts allows them to extend performance beyond the thermodynamic equilibrium limitations which impact conventional hydrotreating catalysts at EOR. In conclusion, there are strategies to maximize ULSD liquid yield by utilizing the optimum catalyst for the desired objectives; and where unit capabilities allow, incorporate MHC catalysts into the unit.
SERGIO A. ROBLEDO (Haldor Topsoe, Inc.)
The strategies for extending the operation of a high-pressure ULSD unit, with maximum yield, depends on a number of factors. The hydrogen partial pressure, LHSV, and hydrogen availability along with the layout of the unit are key factors. Catalyst design and type are also key to maximizing yield. Improving aromatic saturation, specifically monoaromatic saturation, is a driving factor for maximizing yield. Generally speaking, NiMo catalysts will improve the amount of monoaromatic saturation over CoMo catalysts; however, this is dependent on both hydrogen partial pressure and feed nitrogen content. The potential level of aromatic saturation will also depend on the LHS V of the unit.
Therefore, a NiMo catalyst with unmatched hydrogenation activity, much like Haldor Topsoe’sTK-611HyBRIM™ catalyst, is the first strategy for extending operation above a certain yield level. TK-611HyBRIM™ will provide approximately an additional 0.5% increase in liquid yield over top -tier catalystTK-609HyBRIM™. This additional 0.5% yield on a 40,000 bpd unit is an additional 200 bpd on top of the existing volume swell. This incremental swell alone is worth about $3 million per year and will easily pay for the entire catalyst load in three to six months. Depending on the reactor system design, the possibility of raising the front-end temperatures higher to accomplish the HDS reactions, while lowering the reactor outlet temperature to maximize aromatic saturation is a viable strategy. This operation can be accomplished by raising furnace outlet temperature to raise reactor inlet, while removing inter-bed quenches. The quench to the final bed should be maximized to lower reactor outlet temperature to the peak aromatic saturation temperature. Haldor Topsoe also offers their ULSD Polyshift™ and FCC Aeroshift™ technologies to maximize aromatic saturation and, in turn, volume swell. Please contact your Haldor Topsoe representative for more information on these technologies.