Question 33: Increased feed sulfur increases acid consumption. How does it affect alkylate yield and/or alkylate properties?
MUEHLBAUER (Valero Energy Corporation – Benicia Refinery)
In HF units, when sulfur is in the feed, it produces acid-soluble oil (ASO), organic fluorides, and polymers, which then have to be removed through the regeneration process. The light ends that are contained in this ASO can put more pressure on the regeneration system and lead to the higher acid losses. So that is the mechanism there. But within Valero, we found that higher ASO really has a minimal impact on alkylate yields. We do see that it can impact the
product sulfur concentration. In one of our facilities, we run as high as 20 ppm sulfur in the alkylate. The main reason for this is ASO entrainment.
We have seen that units which practice internal regeneration are more susceptible to this entrainment, and that is the main area it would come out. We have also found that in units designed with vertical settlers, it is really important to monitor the superficial velocity and acid quality in those separators to make sure you are getting adequate separation.
One other point, which is not on the slide, is that we do have one facility with a sulfuric acid alkylation unit that runs as high as 500 ppm to 1,000 ppm sulfur in the feed. At those levels, we have seen high acid consumption but have not really seen the impact on the distillation properties of the alkylate. In fact, the product sulfur in that alkylate is really low: less than 3ppm. We believe part of that is because of the neutralization section and acid wash that is performed in that unit.
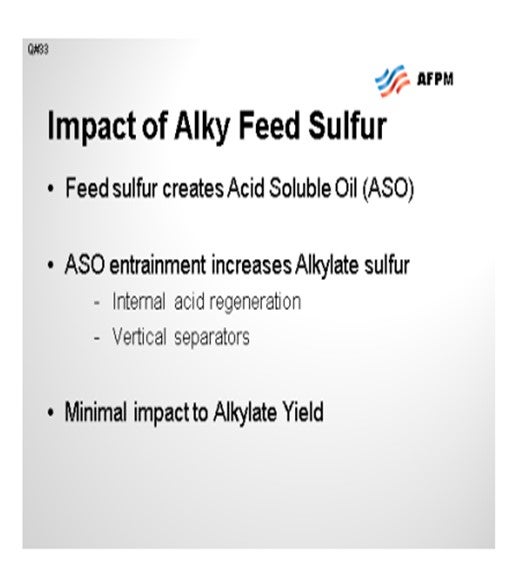
STEVES (Norton Engineering Consultants, Inc.)
I will just echo what Joe said. With normal feed sulfur levels of 10 ppm to 20 ppm maximum, the impact on alkylate yields and properties is minimal. With higher feed sulfur, the acid consumption will become more pronounced and can eventually result in a loss of alkylate yield as you make undesirable acid species.
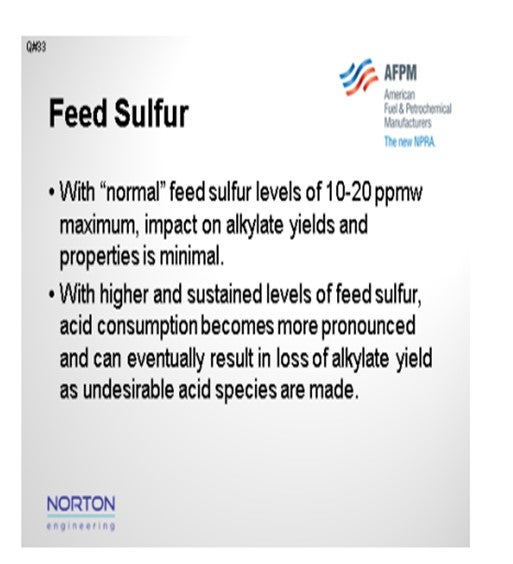
In HF units, severe sulfur contamination and feed can result in a lot of light ASO production and eventually a yellow discoloration of the alkylate, especially, as Joe said, with internal regeneration. Alkylate endpoint could also increase an octane drop. In sulfuric acid units, severe and prolonged sulfur contamination can lead to an acid runaway, in which case the alkylate yield would drop in an acid runaway situation. Octane would decrease, and the alkylate can turn purple.
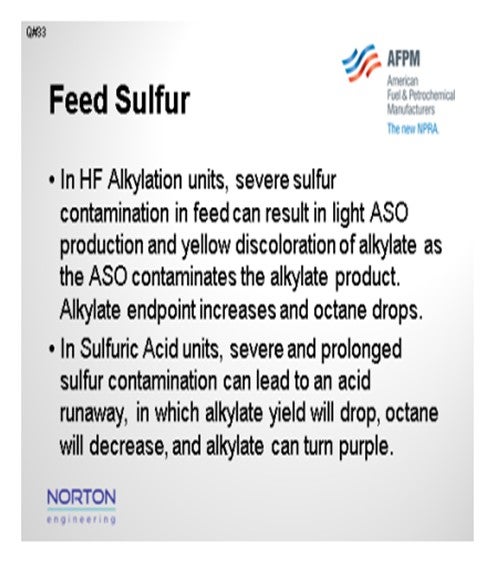
KURT DETRICK (UOP, A Honeywell Company)
Just one more comment on the alkylate properties. I think that the sulfur itself is not directly affecting the alkylate properties, such as the endpoint or the color. Rather, it is the drop in acid purity, which occurs as a result of a sulfur upset, that tends to cause these high endpoints and the color in the alkylate. The reason that happens is because the ASO that comes from the sulfur tends to be a fairly light boiling ASO. So, if you try to run the regenerator or rerun column
at about the same temperatures as normal, then you might boil it overhead. It stays in the system that way instead of getting rejected in the bottom of the rerun column or regenerator. If you know you had the sulfur upset and can drop the rerun or regenerator temperatures a little ahead of time to get that ASO out the bottom of the regenerator, then the effect on the alkylate endpoint will be minimized.
RANDY PETERSON (STRATCO® - DuPont)
We were contacted by a refiner that has very high levels of sulfur compounds in the olefin fed to their sulfuric acid alkylation unit. Most butylene feeds are treated with caustic washes or mercaptan extraction units prior to alkylation and usually contains less than 20 ppm total sulfur. However, this particular refiner’s feed typically contains approximately 500 ppm and sometimes well over 1,000 ppm of sulfur compounds. They see a strong correlation between the feed sulfur content and acid consumption which we would expect. However, they see much higher acid consumption than what we predicted.
We performed a series of pilot plant runs where we spiked the feed with various quantities of typical sulfur contaminants, such as ethyl mercaptan. In summary, we found that the sulfur components have about double the acid consumption than what we have previously published. For example, ethyl mercaptan consumes about 31 pounds of acid per pound of contaminant (99.2 wt.% to 90.0 wt.% acid spending range) versus the 15.7 pounds of acid per
pound of contaminant that STRATCO® DuPont has published in the past.
As far as alkylate product specifications, we saw no change in D-86 T90 or endpoint with changes in feed sulfur in our pilot plant. The refiner also reported that the alkylate product typically contains less than 10 ppm sulfur no matter the quantity in the feed. They have a modern effluent treating system with an Acid Wash which may help explain the low sulfur levels in their product.