Question 32: What is a typical range of HDM (hydrodemetallization; metals removal) in a gas oil hydrotreater? Can HDM decline rapidly when metals in the feed become excessive relative to catalyst system design? Is there a point when metals in the feed are so high that they “overwhelm” the demet (demetallization) and main bed catalyst, resulting in lower percent of HDM?
WATKINS [Advanced Refining Technologies (ART)]
Nickel and vanadium contamination generally come in heavy gas oils and resid hydrotreating. It is obviously not very common in diesels and light feeds. We see that it is about a 5°F to 9°F loss per weight percent combined pickup. The reason you will want to pay attention to these metals is because of their ability to actually diffuse onto the catalyst, so you will need a space to deposit them. Nickel and vanadium are generally tied up in these large porphyrin-type structures. They are fairly rigid and not easily accessible. They also require some level of saturation to be able to get out that nickel and vanadium in order to actually have it react on the catalyst surface. So, you really need not only a space to fit this large molecule, but you also need space to then put the nickel or vanadium onto the catalyst surface.
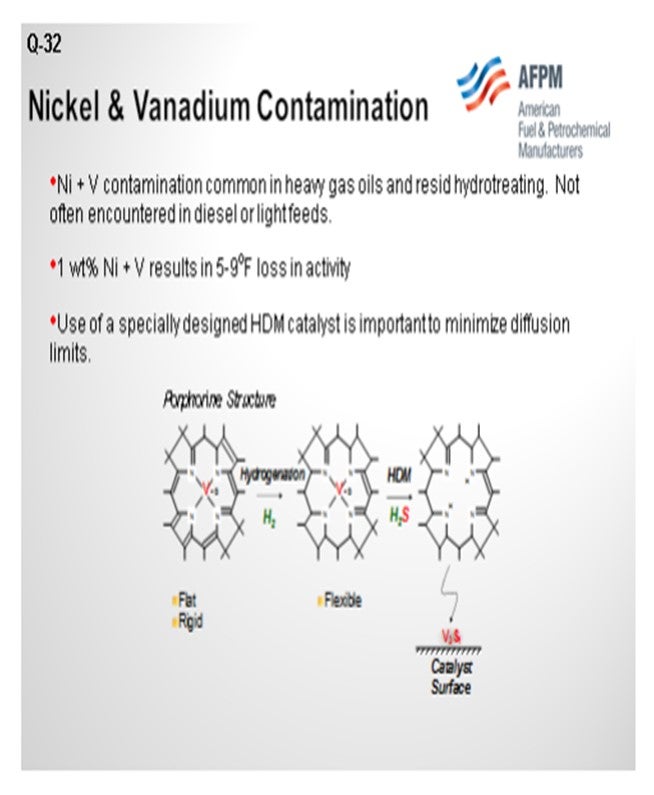
The next slide shows the comparison of a large pore diameter catalyst with a small pore diameter catalyst. With a large pore diameter, you actually can get more metals onto the surface because you are not diffusion limited. Being overwhelmed actually defines the fact that you may have a catalyst that has too small of a pore diameter. You can only get a few metal molecules in on the outside, and then you have basically covered over the available pore volume space. This is highly dependent on reactor temperature: the hotter your reactor, the more metals you can pick up. You can force diffusion into the catalyst pellets, but it can also be indicative of other molecules or poisons present that would help overwhelm the catalyst. Generally, there are specific guard catalysts found in hydrotreating. A lot of them used in resid service are also used in FCC (fluid catalytic cracking) pre-treat, hydrocracker pre-treat. They pick up greater than 100 wt% of nickel plus vanadium, which is why they are generally used. They can pick up quite a bit of nickel-vanadium and not be overwhelmed. So, a properly defined system should prevent being overwhelmed.
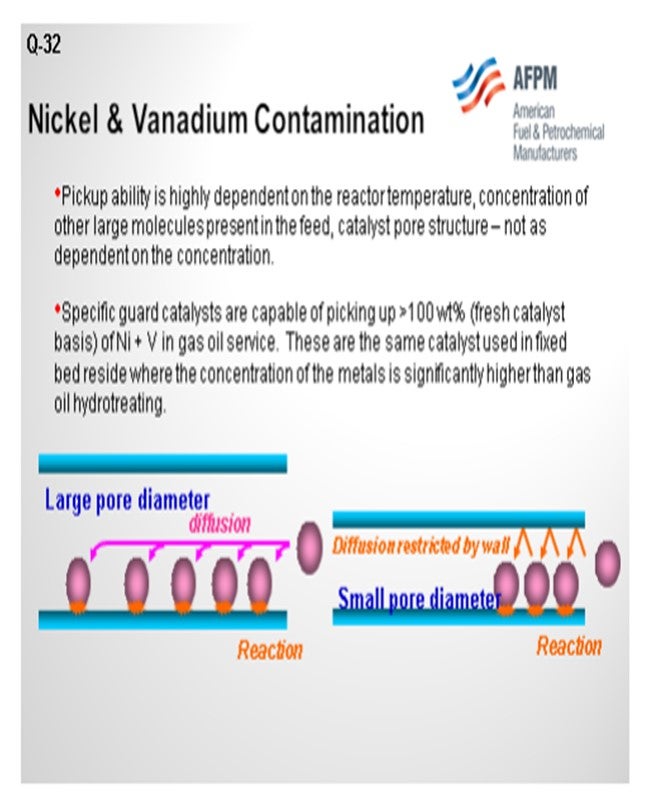
SIVADASAN (UOP LLC, A Honeywell Company)
A well-functioning VGO hydrotreating system can do an HDM function of 85 to 90% for start-of-run conditions and 80 to 85% for end-of-run conditions. This is based on the assumption that the metal’s pickup capacity for the HDM catalyst, plus 50% metals pickup capacity of the active VGO catalyst, is more than the total nickel to the nickel plus vanadium which is coming into the unit over the anticipated cycle. In our opinion, there is no specific metals content of the feed below which the catalyst will not become overwhelmed.

BRIAN WATKINS [Advanced Refining Technologies (ART)]
Traces of nickel (Ni) and vanadium (V) are present in most crudes although the amount is strongly dependant on crude type. They are concentrated in the heavier fractions, especially the bitumen and vacuum residue. Ni and V poisoning can be a significant problem in FCC pre-treat and hydrocracker pre-treat units which process heavier feeds, and they are not often encountered in diesel or lighter feeds. The primary deactivation mechanism of these poisons is pore mouth plugging (Figure 1).
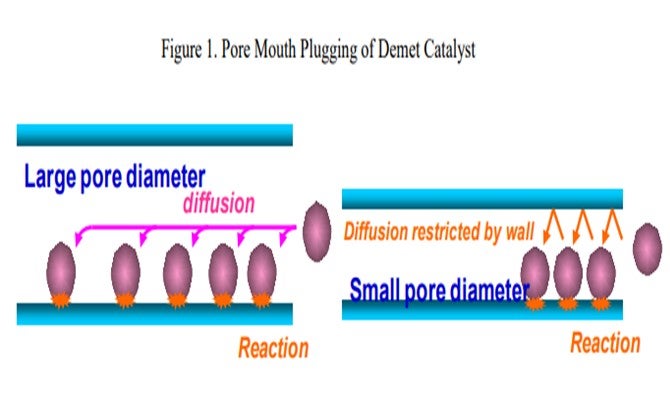
Nickel and vanadium are usually contained in large asphaltene-like molecules which are too large to penetrate into the pores of typical hydrotreating catalysts. Therefore, the nickel and vanadium end up depositing on the outside of the catalyst, ultimately blocking access to the active sites within the pores. Pilot plant testing with heavy feeds on a widely used FCC pre-treat catalyst suggests that 1 wt% Ni+V on the catalyst results in 10°F loss in activity. The activity loss will be greater for a smaller pore (diesel type/grade) catalyst (Figure 2).
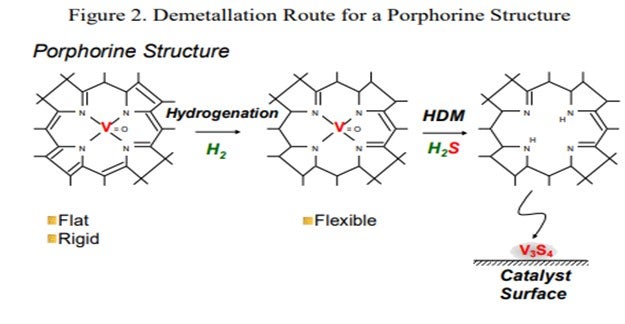
Dealing with nickel and vanadium requires specially designed catalysts for removing and storing the metals. These catalysts have very large pore size distributions which are tailored to provide very high capacities for nickel and vanadium.
There are demet catalysts available today that are capable of picking up as much as 100 wt% (fresh catalyst basis) Ni+V in a gas oil hydrotreater. Much like other contaminants, the ability to pick up these metals is highly dependent on the reactor temperature, as well as the concentration of Ni+V coming in with the feed. Generally speaking, if there is a sudden large spike in Ni+V in the feed there are other changes to the feed accompanying this (i.e., increased endpoint) that may be more detrimental to the catalyst performance.
The catalysts typically used for HDM in a gas oil hydrotreater are similar to the ones used in fixed bed resid hydrotreating where the concentration of metals is significantly higher than that found in gas oil hydrotreaters. The main bed catalysts for FCC pre-treating and hydrocracker pre-treat are generally tolerant of some level of these poisons without significant activity loss and can handle short periods of higher Ni+V levels. However, the capacity of these catalysts is typically around 10 wt%, give or take. So, if it is anticipated that Ni+V levels may fluctuate significantly, use of a demet catalyst is generally a good idea.
DAVID VANNAUKER (Haldor Topsøe, Inc.)
The HDM in a gas oil hydrotreater is a function of pressure, temperature, residence time (LHSV), catalyst, and feed. In commercial units, the metals pickup may range from a low of 50% up to 99+%. Operating pressures are fixed in commercial units; but in general, the higher pressure units have improved kinetics. The key variables for optimized metals pickup are temperature, residence time, and the proper catalyst with an optimized pore size distribution. Increasing the operating temperature and residence time provides an increase in the kinetics and removal rates. Catalyst selection, as mentioned, is a key to cycle optimal metals pickup. Demet catalysts have been specially designed to remove metals. The difference between modern demet catalysts and older generation hydrotreating catalysts can be as much as a factor of 6 in performance. Feed endpoint is also a consideration. The metals found in the lighter gas oils can be removed with relative ease. As the feed endpoint is increased, the molecular complexity increases, making the metals removal more difficult.
The HDM functionality can decline very rapidly when the catalyst system reaches the saturation level. Monitoring feed and product metals levels throughout the cycle are both key to avoiding surprises. We are aware of one unit that, about 15 years ago, had metals removal in excess of 90%, which dropped to a level of 50% in less than 60 days. Ordering and changing the catalyst had to be performed on a rush basis.
We have also observed an apparent slumping in HDM performance with large spikes in metals content. This is typically associated with another upset in the refinery, and part of the loss in performance is due to having significantly heavier molecules with metals going through the unit. Topsøe has designed demet catalysts (TK-719, TK-743 and TK-753) specifically for use in resid service and TK-453 for use in gas oil service. The pore size, pore size distribution, and porosity of these catalysts are optimized for maximum metals pickup in the specific service.