Question 31: What is the threshold concentration of arsenic and phosphorus requiring a dedicated trap system? How are the arsenic and phosphorus trap systems specified,and what are the controlling mechanisms?
WATKINS [Advanced Refining Technologies (ART)]
Arsenic is a big concern because it is a permanent poison that causes fairly significant activity. We generally see around a 60° Floss per weight percent pickup; so you will want to pay attention to it. As a side note, it is also common in most fractions of hydrotreating: so anything from naphtha to heavy gas oil. Since there are a large number of process variables, catalysts, and operating conditions, the level that would define where a dedicated trap is actually needed will really depend on how much arsenic is coming into your reactor and possibly what other catalyst is present there as well. Generally, we like to monitor how many pounds of arsenic per day are coming into your hydrotreater; then, we look at the controlling mechanisms for deactivation.
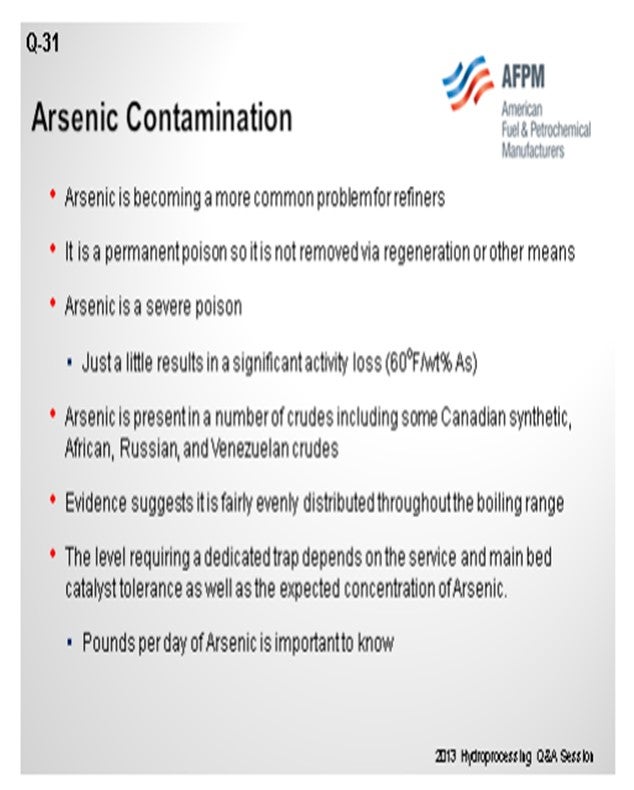
The chart on the left side of the slide compares relative arsenic pickup on the catalyst to the actual amount of nickel present in the reactor. One of the major factors for how much arsenic your reactor can hold is how much nickel is sitting at the top of your reactor, or even in the whole reactor. So, as you go from left to right, you can see you can pick up quite a bit more arsenic.
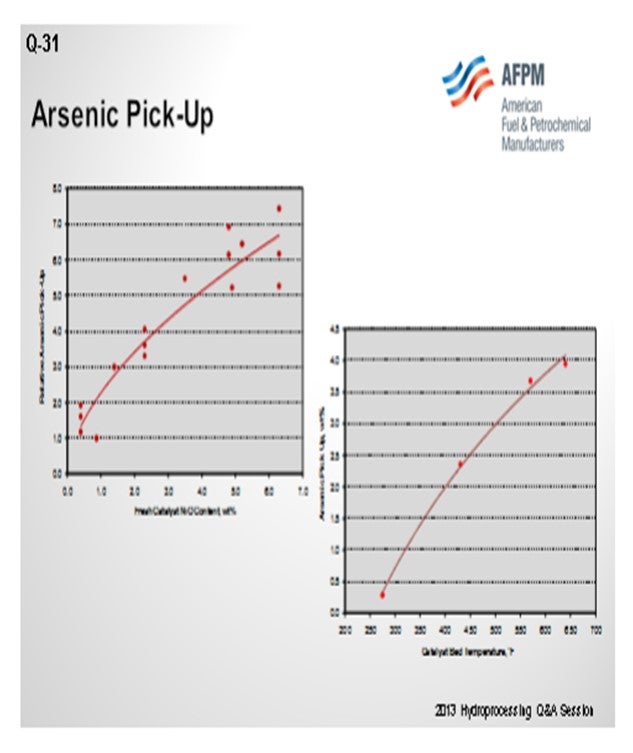
What also controls arsenic pickup is the operating temperature of your hydrotreater. You can generally look at the weighted average bed temperature or the actual temperature of where the catalyst is located. Something like a diolefin reactor down at 250°F to 300°F will pick up a very low level of arsenic. Whereas if you get up into the 650°F to 700°F range, that same catalyst can pick up a significant amount if it is in the right location. So, these two factors will really define how much volume we need to place, in terms of a guard catalyst in your reactor.
With phosphorus, there is the same problem. In this case, at about 1 wt% (weight percent) pickup, we see somewhere in the order of 10°F loss in activity. That number goes up as you get significant levels of phosphorus on the catalyst, but the first amount is not necessarily as important. On the bottom of the slide is a table showing a spent catalyst analysis from a reactor. You can see that this unit was able to pick up phosphorus even on some of our guard material. So, in some of our rings and support, you can actually pick up quite a bit of phosphorus. Again, that is related to temperature. It is also related to alumina surface area, similar to silicon trappings. So that should be your focus. Really, the amount of catalyst in your hydrotreater will determine where you define your need for dedicated trap material. We recommend spent catalyst analysis for looking at things like that.
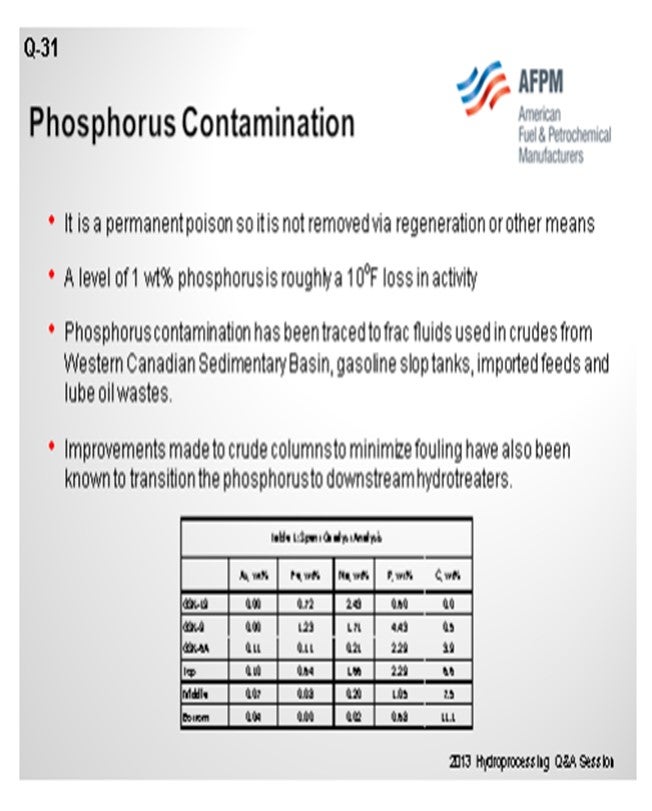
SIVADASAN (UOP LLC, A Honeywell Company)
Arsenic is a poison for hydroprocessing catalysts and tends to be specific to crude sources. We have seen that how they apply to catalysts is mainly determined by the type of reactions being carried out. So for example, in a ULSD (ultra-low sulfur diesel) unit, if you see where an indirect hydrogenation route is the preferred part, then concentrations as low as 500 to 1,000 ppm (parts per million) of arsenic can affect the activity of the catalyst by more than 50%. But in a unit that is processing around 500 ppm of diesel, the catalyst will be able to withstand up to 1 wt% of arsenic before you see a 50% reduction of the life. Due to the broad range of arsenic concentrations, electro, and cycle lengths, we believe that it is not possible to confidentially cite a specific threshold concentration above where its dedicated arsenic trap system may be required.
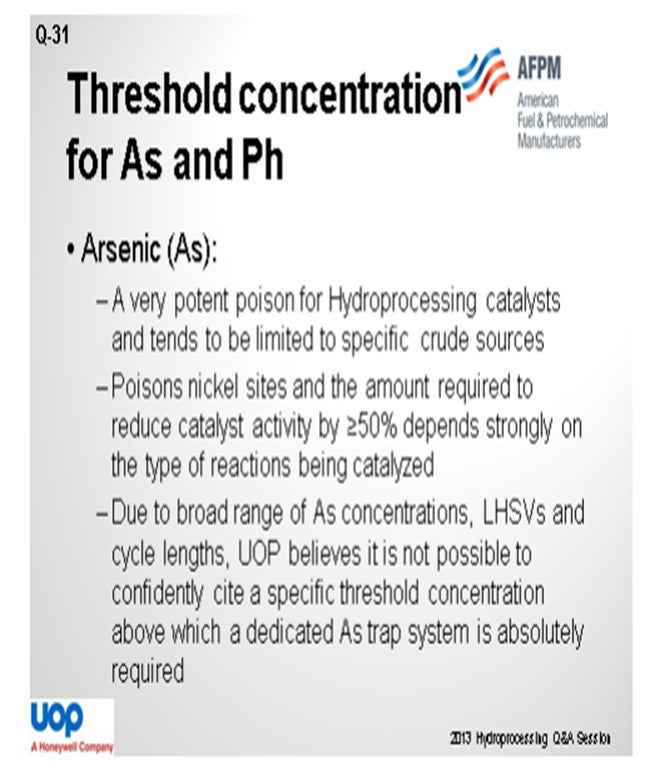
Phosphorus, again, can enter into the hydrotreater unit from various sources like crudes, drilling fluids, and phosphated trendsetters. They are the same biofeeds. We believe that the phosphorus generally tends to be quite similar to the sodium. Around 1 wt% of sodium may affect the activity of the catalyst by more than 50%. The catalyst performance and maximum allowable limit are highly dependent on the source and form of the phosphorus.
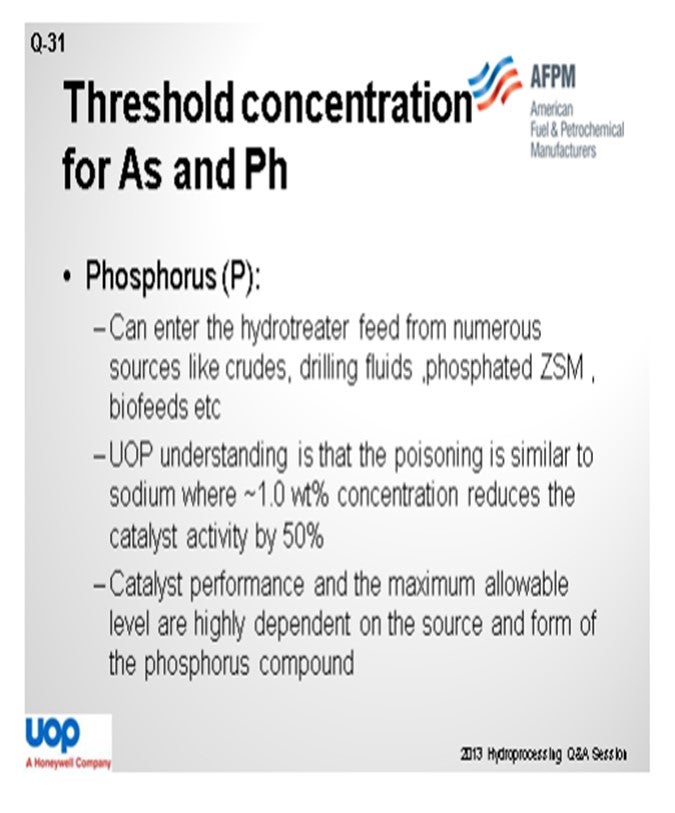
MUKESH PATEL (Reliance Industries Ltd.)
What is the Best Practice for analyzing arsenic and phosphorus? Should it be done weekly or on some other frequency? Because arsenic is very important when the crudes are changing every now and then, what should be the frequency and what is the industrial experience?
SIVADASAN (UOP LLC, A Honeywell Company)
The determination of arsenic is a bit difficult, as you pointed out, because it interferes a lot with the lab analysis. What people generally do is run a cycle, do a spent catalyst analysis, and then back-calculate how much amount of arsenic is in the feed.
MUKESH PATEL (Reliance Industries Ltd.)
When we say spent catalyst analysis, it is some sort of analysis of used catalyst, right? But what is a better predictive estimate we can do? Because when you want to capture, you can decide on some limit on the arsenic and then put in an arsenic trap. But if you keep putting on an arsenic trap, you will ultimately have a challenge because you will be compromising on cycle life. What I mean to say is that spent catalyst analysis is done after the completion of the cycles, which tells you what the true level of arsenic was in your feed. For example, suppose you are deciding about some loading for the new cycle and how to capture arsenic. Once you start putting in more and more arsenic traps or any demetallizing catalyst, you will be compromising the cycle because your volume will be less in the main catalyst. So, has there been any development where the conventional arsenic traps have a certain capacity for absorbing the arsenic? Is there any new development to help us capture three or four times the arsenic with the same type of volumes?
WATKINS [Advanced Refining Technologies (ART)]
The amount of trap will really depend on your main bed catalyst and your guard catalyst up at the top. If using a high-nickel catalyst, you could actually trade off and balance that activity; so you will maximize your cycle. If you have nickel catalyst in your entire reactor, you could extend your cycling because you can actually pick up a lot more arsenic that way. It is a constant battle, though, to define your cycle length and the amount of arsenic you can pick up. It is all dependent on temperature and how many pounds per day you are going to put in. I recommend that you work with your catalyst supplier to figure out an optimum system and what their products can actually hold without losing any activity or cycle length.
BRIAN WATKINS [Advanced Refining Technologies (ART)]
Arsenic
Arsenic (As) is found in many crudes including some from West Africa and Russia, as well as many synthetic crudes. It is becoming a common contaminant as use of these crudes, especially synthetic crudes, has been increasing in recent years. The arsenic is believed to bind with the metal sulfide sites (and in particular, the active nickel on the catalyst) forming nickel arsenide. This has a dramatic impact on catalyst activity. To demonstrate the effect of arsenic on catalyst activity, ART obtained a series of spent catalysts containing different levels of arsenic. These samples were carefully regenerated in the laboratory and were then activity tested using a diesel feed containing 50% cracked stocks under conditions producing less than 500 ppm sulfur. Figure 1 summarizes the results of that work. At 1,000 ppm, arsenic on the catalyst shows 5°F HDS (hydrodesulfurization) activity loss and nearly 15°F loss in HDN (hydrodenitrogenation) activity. The activity loss quickly increases to over 50°F with 1 wt% arsenic on the catalyst.
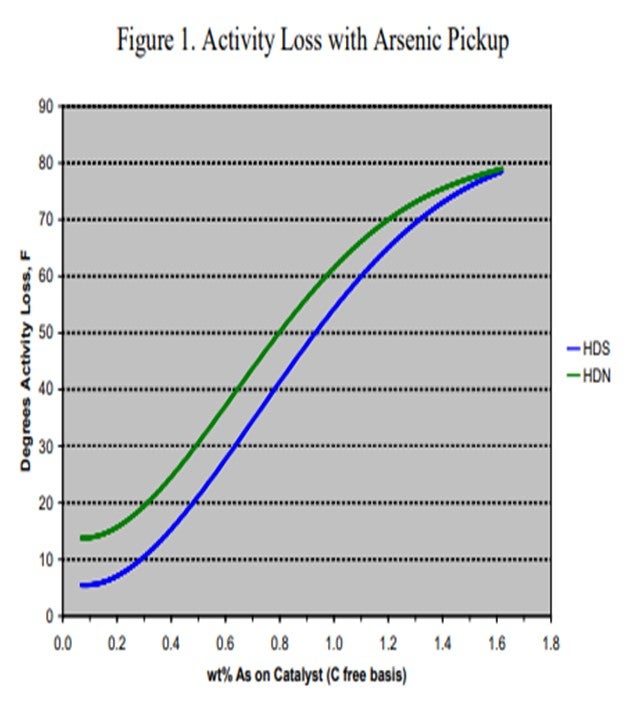
Canister data for a variety of catalysts also indicates that catalysts containing nickel are more effective for trapping arsenic. Figure 2 summarizes the arsenic pickup values for several NiMo (nickel molybdenum) catalysts. As this data shows, both high metals ULSD catalyst NDXi and AT580 as compared to our recent guard catalysts AT724G and AT734G, which are quite effective for trapping arsenic. The data also indicates that the active ring materials and demetallization catalysts used are also effective for trapping arsenic.
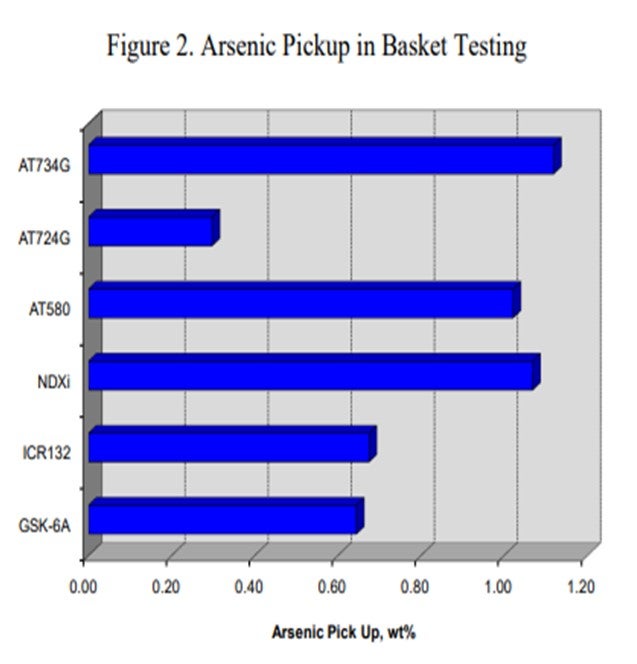
Other canister data also shows that the ultimate arsenic pickup is heavily dependent on temperature. Figure 3 shows the arsenic pickup as a function of temperature for a NiMo catalyst. These results were obtained by analyzing spent samples of a high metals NiMo catalyst from a three-reactor unit processing 100% cracked naphtha from a synthetic crude source. The first reactor was operated at very low temperature (about 275°F) in order to saturate diolefins. The second reactor was designed to saturate mono-olefins and operated at about 430°F. The last reactor had an inlet of 570°F and an outlet temperature of approximately 650°F. The arsenic content on the catalyst correlated with the temperature of the reactor as depicted in the figure. The data demonstrates that a high nickel catalyst can pick up very high arsenic levels if the operating temperature and feed concentration are high enough.
Noting that there are a wide range of arsenic levels, unit operating conditions, and expected cycle lengths, the ability to define a single-set threshold for when a trap is needed is difficult. It is recommended that if arsenic is found to be a problem contaminant, you will need to consult your supplier to determine if it is impacting the cycle and if and how much guard catalyst is needed.
Phosphorous
Phosphorous contamination in oil has been traced to fracturing fluids that are often used in crudes from the Western Canadian Sedimentary Basin. The source is diphosphate esters which are soluble in the crude oil. Refineries that run large percentages of light Western Canadian crude have reported crude column and crude furnace fouling for many years. Improvements made to crude columns to minimize fouling have transitioned the depositing of phosphorous to the downstream hydrotreaters.
Other sources of phosphorous include gasoline slop tanks, imported feeds, and lube oil wastes. If phosphorous does manage to make its way into the hydrotreater, it will poison the active sites of the catalyst causing a loss in activity. A level of 1 wt% of phosphorous on the catalyst results in roughly 10°F loss in activity. ART recommends that a feed content of less than 0.5 wppm (weight parts per million) be maintained whenever possible, as well as the use of feed filters to assist in trapping of phosphorous sediment.
An ART catalyst case study of the detrimental impacts of feed poisons on hydrotreater performance involved a ULSD unit which had recently started up with ART catalysts. Shortly after startup, the unit began to experience extremely rapid catalyst deactivation. It was so severe that within a couple months, the unit required an unplanned turnaround and the installation of fresh catalyst. Samples of spent catalyst representing the whole catalyst charge were collected and analyzed in the laboratory. The results are summarized in Table 1. It is apparent from these results that the catalysts were exposed to high levels of several poisons including arsenic, sodium, phosphorous, and iron. The contaminants penetrated well into the catalyst bed. Catalyst at the bottom of the reactor was not yet poisoned, but the coke content was extremely high for catalyst which had been onstream such a short time. The level of contaminants indicates the catalyst in the top half of the bed lost over 60°F of activity while the bottom was providing most of the HDS conversion. This required very high temperatures, which is reflected in the high carbon content at the bottom of the bed.
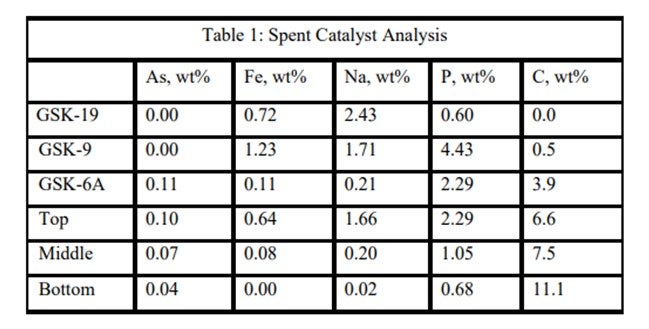
ART has a suite of options in order to protect the main bed from these and other contaminants which may be present in the feed to a typical hydrotreater. The use of several of these materials combined together can adequately provide protection and extend the cycle life of your hydrotreater.
RAJESH SIVADSAN (UOP LLC, A Honeywell Company)
Arsenic (As) is a very potent poison for hydroprocessing catalysts. Although As tends to be limited to specific crude sources (e.g., crudes from the U.S. and Canadian Rocky Mountains, Russian Urals, specific Chinese and West African sources, and “synthetic crudes” from Canada and Venezuela), it is usually present in all boiling fractions of those crudes.
Arsenic tends to poison the nickel sites of hydroprocessing catalyst, and the amount required to reduce catalyst activity by ≥50% depends strongly on the type of reactions being catalyzed. For instance, in diesel hydrotreating where ULSD is produced and product quality depends heavily on hydrogenation route desulfurization, as little as 500 to 1,000 wppm arsenic on catalyst can reduce HDS activity by 50%. On the other hand, for hydroprocessing applications where direct desulfurization is the primary mechanism for reaching product targets, higher levels of arsenic contamination on catalyst (about 1 wt% As) may be tolerated while retaining HDS activity greater than 50% of fresh catalyst activity.
Because of the broad range of as concentrations on catalyst that will poison the catalyst, as well as the broad ranges of LHSVs (liquid hourly space velocities) and cycle lengths for various hydroprocessing applications, UOP believes it is not possible to confidently cite a specific threshold concentration for as in feed above which a dedicated as trap system is absolutely required.
Phosphorus (P) can enter the hydrotreater feed from numerous sources: crudes, drilling fluids, phosphated ZSM (Zeolite Socony Mobil), phosphorus-based corrosion inhibitors and flow improvers, and biofeeds.
In one UOP commercial experience, about 3 wt% phosphorus on the catalyst terminated all the exotherm in the catalyst bed. Organic phosphorous can penetrate into catalyst pores. In general, our understanding is that the poisoning is similar to sodium where about 1.0 wt% concentration reduces the catalyst activity by 50%.
Based on UOP’s experience, we have found that the quantitative effects of phosphorus on hydroprocessing catalyst performance and the maximum allowable level are highly dependent on the source and form of the phosphorus compound, catalyst properties, and the process application, which all need to be considered when designing a trap system. Thus, UOP believes it is not really possible to confidently cite an absolute threshold concentration for phosphorus in feed above which a dedicated trap system is definitely required.
PER ZEUTHEN (Haldor Topsøe, Inc.)
Arsenic and phosphorous compounds are both known as permanent catalyst poisons; however, they each have very different deactivation mechanisms. Arsenic species found in the crude oil, particularly in the heavy ends, act as a true catalyst poison during titration of the nickel- or cobalt-promoted catalytically active sites. Although the concentration typically is rather low in ppb (parts per billion) levels, content of more than 50 ppb, for example, will have a significant negative impact on the catalyst performance. Arsenic compounds are very poisonous to the working catalysts, a typical high-activity catalyst has lost most activity after accumulation of as little as 1% As. Besides, shale oil and other new crude types (Russian and Canadian crudes) contain significant arsenic levels.
Haldor Topsøe has developed a number of dedicated arsenic pickup catalysts to protect the downstream bulk catalyst from very severe poison. The arsenic pickup capacity of this catalyst, TK-45, is as high as 10 wt%, but the actual pickup capacity will depend on the arsenic level in the feed and the operating temperature. With improved diffusion and preparation, Topsøe has recently launched a new dedicated arsenic trap, TK-49, with improved arsenic pickup for all hydrotreating applications.
Phosphorous species are rarely found in typical crudes; however, some opportunity crudes (and in particular, renewable feeds) often contain significant amounts of phosphorous. Moreover, phosphorous containing anti-corrosion additives can be found in the diesel and VGO (vacuum gas oil) fractions. The phosphorous compounds are decomposed in the hydrotreater, and the phosphates react with the alumina support, forming very stable alumina phosphates. Accumulated amounts of phosphates will reduce the accessibility to the active sites of hydrotreating catalysts and lower the activity accordingly.
Topsøe has a specialty product, TK-31, with a capacity of more than 5 to 6 wt% phosphorus, where reaction sites for phosphates have been improved the most. Topsøe recommends installing this phosphorous trap if the feed level is higher than 2 ppm phosphorus for protecting the downstream bulk catalyst from contamination.