Question 31: What is the panel’s experience with temperature excursions (regeneration and otherwise) leading to the catalyst or equipment damage in reforming and isomerization units?
STEVES (Norton Engineering Consultants, Inc.)
In a refinery where I used to work, our moving-bed reformer experienced a severe temperature excursion in the chlorination zone of the regenerator. After a prolonged outage on the regenerator, the unit was put back into white burns sooner than would have been recommended. On introduction of air/oxygen into the chlorination zone, temperature indicators in the drying zone spiked over 2,000°F, and one of the temperature indicators burned out. Although operation was attempted for a few days beyond the temperature excursion, the unit eventually had to be shut down and the regenerator inspected.
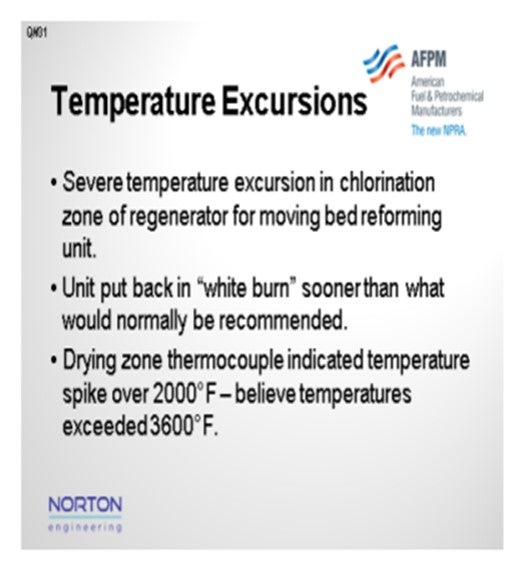
Upon inspection, it was found that the center screen had failed, as shown on the slide.
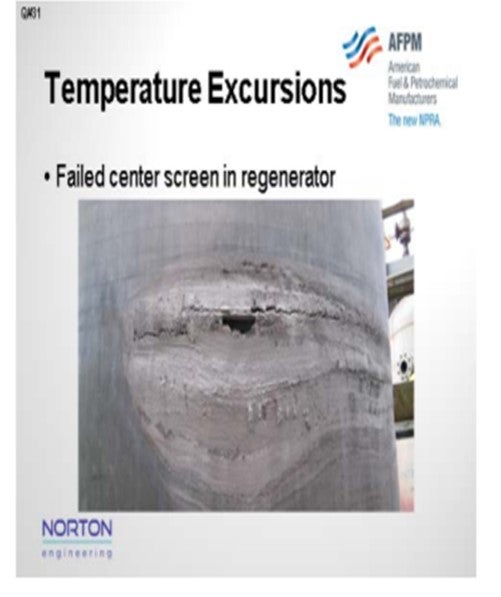
Also, fused catalyst was discovered in the unit. It is believed that temperatures exceeded 3,600°F during the excursion.
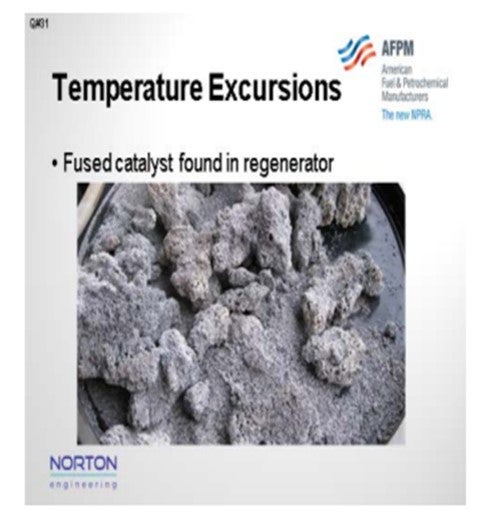
During the subsequent incident investigation, a number of issues were discovered that all seemed to come together in a perfect storm that led to the temperature excursion. Issues included:
• The regeneration section, as I mentioned, had been taken out of service for screen cleaning, and weather delays had prolonged the outage from a targeted three days to six. As a result, the coke level was extremely high.
• Key instrumentation had been modified during the regeneration section outage, which had been planned, including the regeneration thermocouples and the regeneration O2analyzer. However, during the modification of this instrumentation, human error led to a chlorination zone thermocouple being cut, and there were no replacement parts available to try and make the repair before the regenerator needed to be placed back in service.
• The oxygen analyzer sample system was modified during the outage and, upon restart, was not pulling a representative sample of the system.
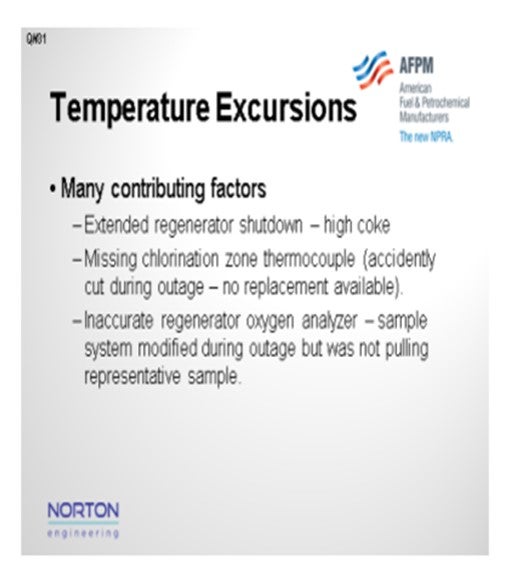
• Operating guidelines had not been modified during a prior outage to take into account a larger catalyst volume within the regeneration system that needed to be circulated before attempting a white burn.
• The unit was demonstrating severe deterioration of performance with the extended regeneration system outage; however, there was no technical guidance that was provided to the operators upon the restart of this regenerator.
• Finally, due to the extended outage and the deteriorating unit performance, there was a desire to get back to “normal” as quickly as possible, which led to poor decision-making when evaluating at what time to put the unit back into white burn.
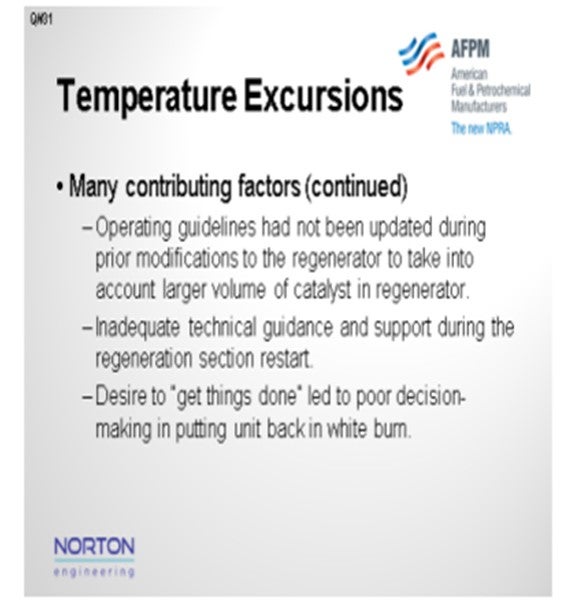
PIZZINI (Phillips 66)
I have three examples of temperature excursions on cyclic reformers. Only the first led to damage, so I will open with that one. This temperature excursion occurred on a spherical cyclic reformer which was going into regeneration about every 10 days. The catalyst section on this reactor has a two-inch layer of refractory. Once we understood the cause of this incident, we realized that coke, over time, had formed between the refractory and the vessel wall. This refractory has a certain number of cracks: not large cracks, but large enough that the hydrocarbon could get behind it and form coke. Also at that time, we were very aggressive with the oxygen target during oxychlorination. That was an actual reactor damage event. Thankfully, it occurred during the regen, so the reactor could be depressured and repaired without any significant safety issue. The follow-up to that, at least in this case, was to limit the O2. Even though we could get better catalyst rejuvenation with high oxygen, we limited it to 2.5%. Our rule of thumb for high temperature burning is that for every one-tenth of a percent of oxygen, we can get another 25°Fof burn temperature. So, imagine that if you are up to 8% or 10% oxygen and there is still coke present, it could get very hot.
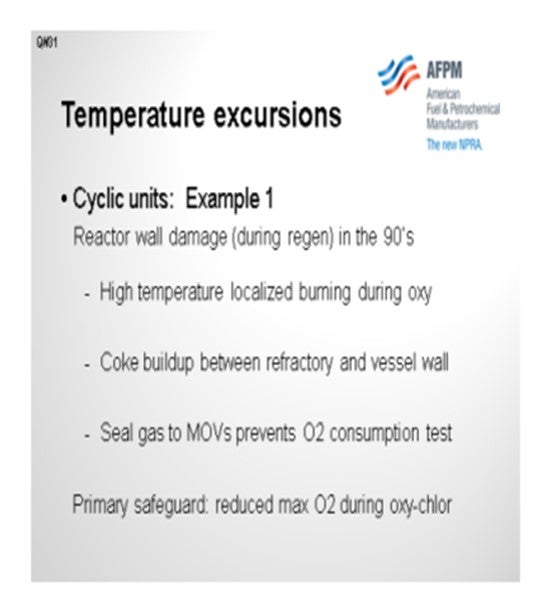
This next example was also on a cyclic spherical reactor. It only happened with new catalyst for the first five or six switches. Just picture a six-foot bed of catalyst with a vertical thermocouple. About five feet down (about 80%) in the bed, for the first 15 minutes after the reactor came out of regen and back into the process loop, we saw some exotherms from 100ºF to 200ºF. When we switched on a cyclic reactor, it was already at 900ºF; so we could really afford
to go much hotter. The strategy there was to increase the sulfide in target; but I can tell you that after about 10 regens, the problem went away. My third example is when a reactor got switched before it was reduced. That error created about an 80°F to 100°F exotherm that lasted 30 to 45 minutes. This was a procedural issue. We did not have the hydrogen lined up properly.
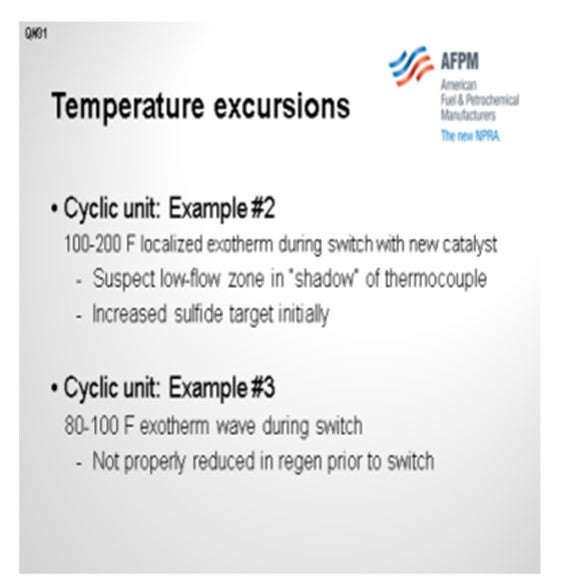
We have seen localized damage on catalyst screens on our semi-regen radial flow reactors. To prevent that problem, we limit the maximum ∆T (delta T; temperature differential) and maximum oxygen during the burn. I am sure everyone else does that as well. Another step to give us that confidence of being able can raise temperatures and O2 levels is what we call the Oxygen Consumption Test. We completely block in the air and nitrogen, and then watch the oxygen analyzer. The criteria are less than one-tenth of a percent of O2 drop over 20 or 30 minutes, and then you know you have burned out everything before you start raising temps.
We also have a couple of CCRs in our system in which we have seen some center screen damage in the regeneration section due to high oxygen and high temperature, as well as some damage to the oxychlorination section when coke was still present on the catalyst. So, we have made it clear, procedurally, when we need to switch from the white burn to the black burn.
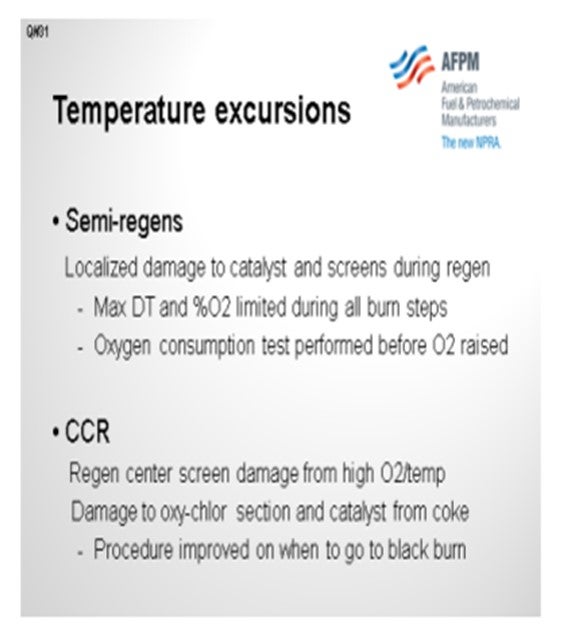
PATRICK BULLEN (UOP, A Honeywell Company)
In the isomerization area with an optimized UOP Penex unit, the lead reactor bottom is typically the hottest point in the system and the place where most temperature excursions occur. Most of the time, the excursions are localized and only the catalyst gets damaged, usually due to coking.
PIZZINI (Phillips 66)
I have a follow-up about our isomerization units. We have experience with temperature excursions on several units. All of those are protected with high temperature shutdowns. I do not know if that has always been the case, but it is the case now. Each of the protective shutdown systems is reviewed in terms of its effectiveness. We put each of those shutdowns through a LOPA because the risk is higher on an isomerization unit.
PIZZINI (Phillips 66)
In semi-regeneration units, we maintain maximum ∆T and O2 concentrations to ensure we do not damage catalyst or equipment during regeneration. We do an O2 consumption test before moving into oxychlorination to help ensure no coke balls are burning. We have not experienced semi-regeneration temperature excursions during operation but have experienced localized damage to catalyst and equipment from regeneration.
One of the Phillips 66’s cyclic reformers experienced a temperature excursion and reactor damage in the 1990s due to overheating on a spherical reactor. This hot-wall reactor has2" of refractory in the catalyst zone. Review of the failure indicated that coke had built up over time between cracks in the refractory and the vessel wall, and that this localized coke reached high temperatures during the oxy-chlorination step. Since an oxygen consumption test is impractical given the nitrogen purged isolation valves on this unit, a lower maximum % oxygen was established for all future regenerations.
In CCRs, we have had regenerator center screen damage if the O2/temperatures get too high at the top of the regeneration section. We have also damaged equipment in the oxychlorination section, along with catalyst when coke has entered the oxychlorination zone. We have improved our operating procedures for white burn and black burn to insure this does not occur.
For isomerization units, we have experienced several temperature excursions. In all cases, the high temperature shutdown systems have worked to prevent damage. In each case, an RCFA was completed to determine the cause and resolve the design or operating issue that allowed the excursion to occur in the first place. Consequently, we have instituted a recommended practice for evaluation of all Isomerization High Temperature Shutdown Systems, including LOPA to determine if safety systems are adequate. Where deficiencies are found, safety systems have and continue to be improved. Common causes of isomerization excursions have included: maldistribution of flow, high feed benzene, heat integration and control with new benzene saturation reactors and less than adequate attention to catalyst loading.
ILYA ARANOVICH (GTC Technology)
Typically, in the isomerization process, the hottest reactor is the one in the lag position as it receives the feed that has gone through the first reactor where exothermic reactions of benzene saturation and naphthene ring opening occur. The isomerization reaction itself is exothermic and leads to a positive delta T in the second reactor. With feed excursion containing high X factor having large amounts of benzene and naphthenes and other operational flaws; for example, for the SI-2TM which is the core of the Isomalk-2TM process you can have big temperature excursions and even emergency situations in case the temperature goes over 200oC in the second reactor. The problem with this is at the latter temperature auto hydrocracking reactions begin to occur which lead to a very rapid increase in the reactor temperature. If not noticed and handled properly, the temperature can reach over 400°C and ruin the catalyst. Proper operation and feed control according to the operating guidelines and good practices in analyzing the feed will prevent these temperature excursions from happening and allow operators to reach a minimum10 years of SI-2 service lifetime.
SUBHASH SINGHAL (Kuwait National Petroleum Company)
In semi-regenerative fixed-bed reactors, if the catalyst was sulfur poisoned, temperature excursion is likely during regeneration if O2 is not controlled in the regeneration gas.