Question 30: What technologies do you use for mild hydrocracking of heavy gas oil over a range of conversions and product selectivity? Please elaborate on commercial experiences.
PATRICK GRIPKA (Criterion Catalysts & Technologies)
The theory and key considerations in utilizing mild hydrocracking (MHC) in an FCCPT unit were covered very thoroughly in Question 77 in the 2009 Answer Book, so I will not repeat what I consider to be the basic background information. Instead, I will try to compare the actual results achieved commercially from the various options. Several different technologies are available, and I will only highlight the keys.
A traditional FCCPT unit with heavy gas oils operating in HDS (hydrodesulfurization) mode to meet a sulfur level specification of 1,000 to 2,000 ppm sulfur in the hydrotreated gas oil being sent to the FCC typically has 650°F+ conversion levels of 5 to 10 wt%. This conversion level can typically be increased another 3 to 5 wt% by operating at higher WABTs to improve aromatic saturation. In addition, the FCC feed quality will be improved, and FCC conversion will increase.
An excellent example of this level of improvement is a unit going from typical 1,000 ppm product sulfur to an aromatic saturation operating mode with a 300-ppm product sulfur. This improvement allows Tier 3 specifications to be achieved as shown in the table below, as well as an increase in VGO (vacuum gas oil) conversion to distillate of 4.1 wt%, as seen in the graph below. This success was achieved with our latest generation CENTERA™ catalysts. Cycle life has still been excellent at greater than 36 months. The performance benefits are illustrated below in the following table and plot. A FCCPT unit can be operated at even higher temperatures to further increase conversion, but this operation is usually not attractive due to reduction in cycle life.
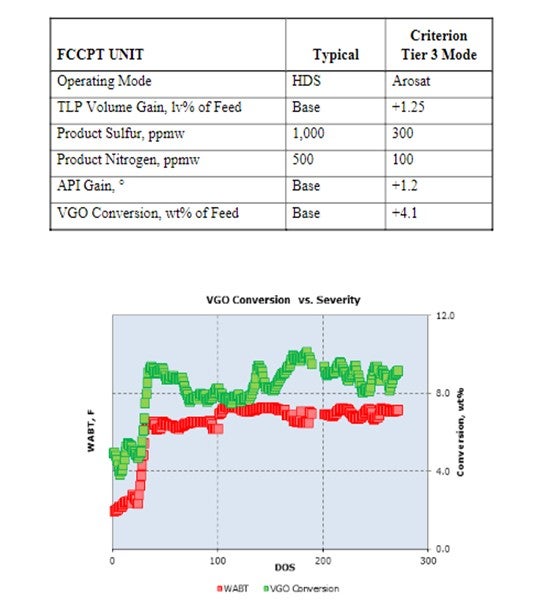
When higher levels of conversion are desired, addition of a catalyst to provide mild hydrocracking is needed. Our customers are operating many units with MHC catalysts in this mode. When higher distillate selectivity is desired, an alumina/ASA catalyst system can be considered. If even higher conversions are required and some additional naphtha and light ends can be accommodated, then alumina/zeolite stacks can be used.
Units operating in MHC mode with an alumina/ASA stack of CENTERA™ NiMo / Zeolyst ASA catalysts will have 650°F+ conversion levels of 20 to 50%. An example of the VGO conversion levels of one of our customer’s operating units (along with the excellent catalyst stability) is shown in the figure below. Middle distillate selectivity is consistently in the 80 to 90% range with this catalyst system.
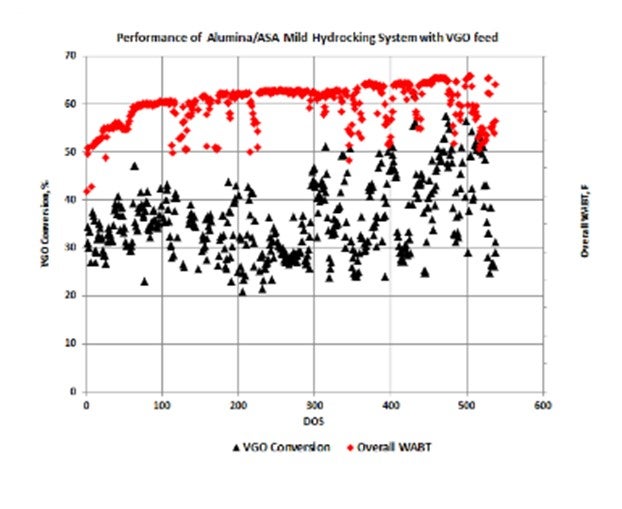
The following is an example of a higher conversion unit operating with alumina/zeolite cracking system operating in the 70 to 80% conversion range.Conversion levels beyond 50% are well within the capacity of an appropriately designed unit and catalyst system operating in once-through fashion. Applying an advanced hydrocracking pretreat and full zeolite cracking system can extend unit operations to the 70 to 80% conversion range with stable yields and exceptional selectivity. While this conversion level is on the border of what might be considered MHC operation, there are several benefits to once-through operations, even in units designed for higher conversion. Once-through operations provide consistent high conversion levels at elevated unit rates, as well as a significantly upgraded unconverted oil product stream ideal for FCC operations. The following plot illustrates a unit operating for 48 months consistently providing VGO conversion levels in the 70 to80% range.
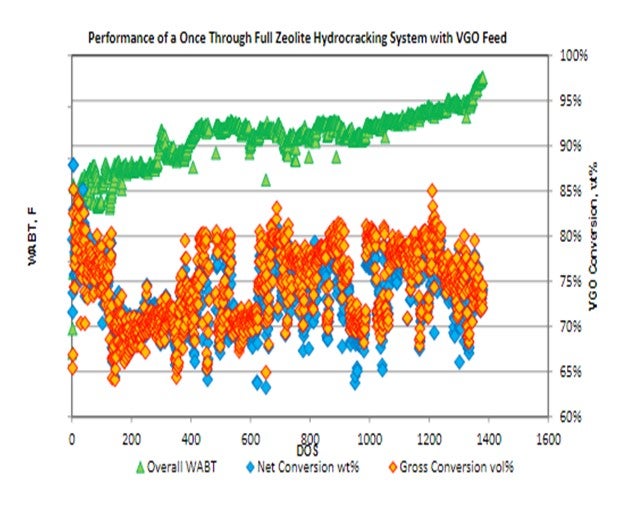
In summary, technologies are available for hydrotreating VGO to a range of conversions. The simplest is a standard FCCPT unit operating primarily to provide high quality hydrotreated feed to an FCC. Operating the FCCPT unit for improved aromatics saturation will result in even better FCC field quality and will reduce the impact on downstream FCC gasoline hydrotreaters or eliminate the need altogether.
The mild hydrocracking operation with an alumina/ASA catalyst or an alumina/zeolite-based catalyst system will produce a high-quality bottoms product and a good to excellent quality ULSD product. Depending on unit capabilities and feed qualities, catalyst options and know-how are available to meet refiner’s objectives.
This table summarizes the technology options and the typical conversion levels.
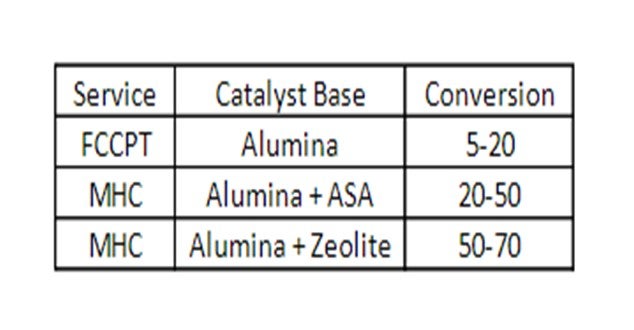
DAVID VANNAUKER (Haldor Topsoe, Inc.)
MHC can be utilized to process either heavy gas oil or heavy gas oil blended with DAO. The unit typically has demetallization (HDM) catalysts, in addition tohigh-powered/high-activity HDT catalysts. The primary Topsoe technology for mild hydrocracking of heavy gasoil is the Haldor Topsoe Staged Partial Conversion™(SPC). Additionally, catalyst selection will have a large impact on MHC operation. At low pressure operations,we suggest usingTK-947™, Haldor Topsoe’s NiMo/zeolitic HDC catalyst. At moderate pressure operations, select a NiMo version of a higher zeolite HDC catalyst.The range of conversion and product selectivities is highly dependent upon the HDCcatalysts selected. MHC is performed in units with pressures ranging from 850 to 1600 psig(pounds per square inch gauge). Conversions range from 15 to 50%.