Question 30: What are your design practices for reactor skin thermocouple requirements in a hydrotreater and a hydrocracker for startups and safe operation?
VICHAILAK (Marathon Petroleum Corporation)
Our minimal requirement for a hydrotreater is three skin thermocouples at the top and bottom heads of the reactors and a full skin thermocouple at the bottom shell of the reactor just about at the tangent line. The option now is a full skin thermocouple at the top of the shell and the middle of the shell.
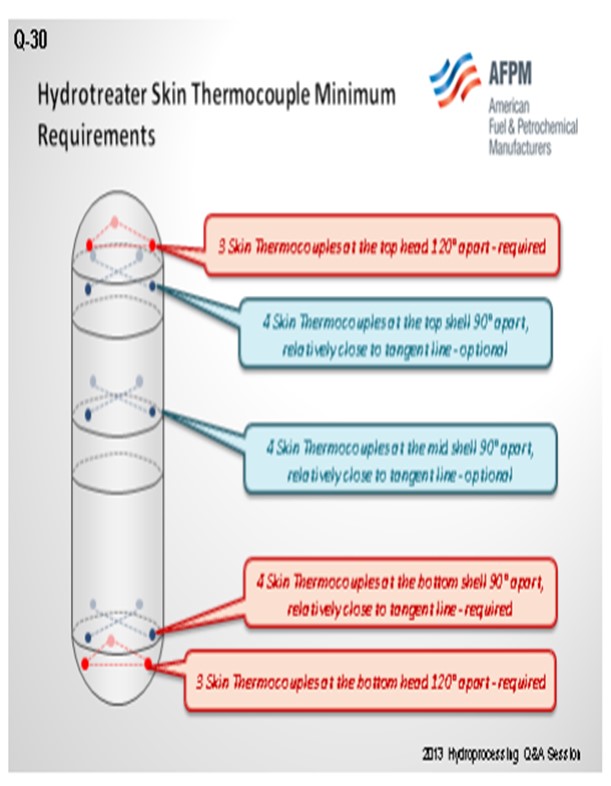
For a hydrocracker, we have one skin thermocouple at the inlet and outlet nozzles of the reactors. This slide shows a typical hydrotreater. It has just three skins at the top and bottom heads and then four skins at the bottoms shell; the other two are optional. For a hydrocracker, we have an additional one at the inlet and outlet nozzles; plus four at the top and bottom heads and four at the bottom of each bed. Those are all of the required thermocouples. These are the minimum requirements, but you can have more. Most of our reactors have four skin thermocouples.
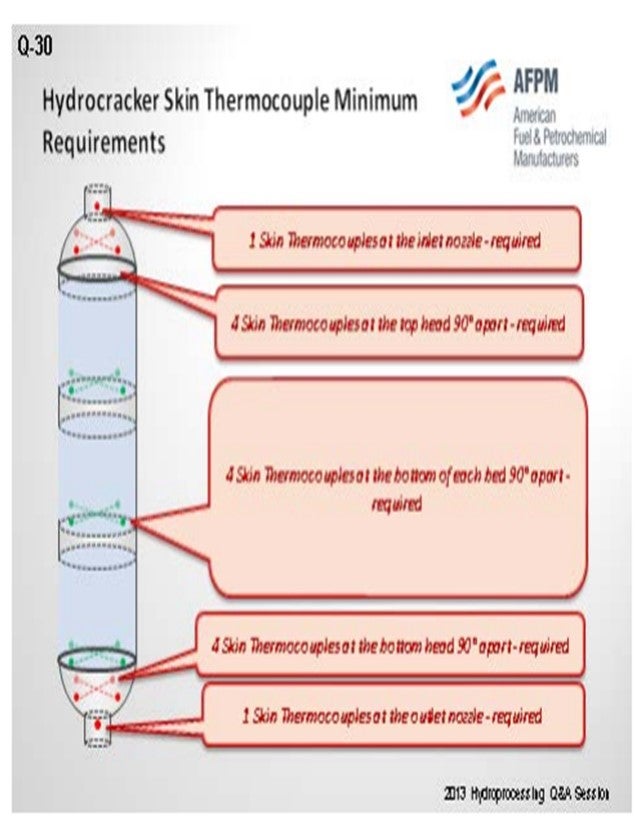
The skin thermocouple should be provided to ensure the attainment of minimum pressurization temperature (MPT) on both startup and shutdown. I must emphasize that when doing the startup, you have to look at the bottom of the reactors for the MPT. And then when shutting down, your perspective is reversed: The top of the reactor becomes the MPT limit. You have to depressure the unit before you hit that temperature. The location of the thermocouples should be sufficient to safely start up and shut down the hydrotreater. High pressure hot separator may be required to have skin thermocouples as well.
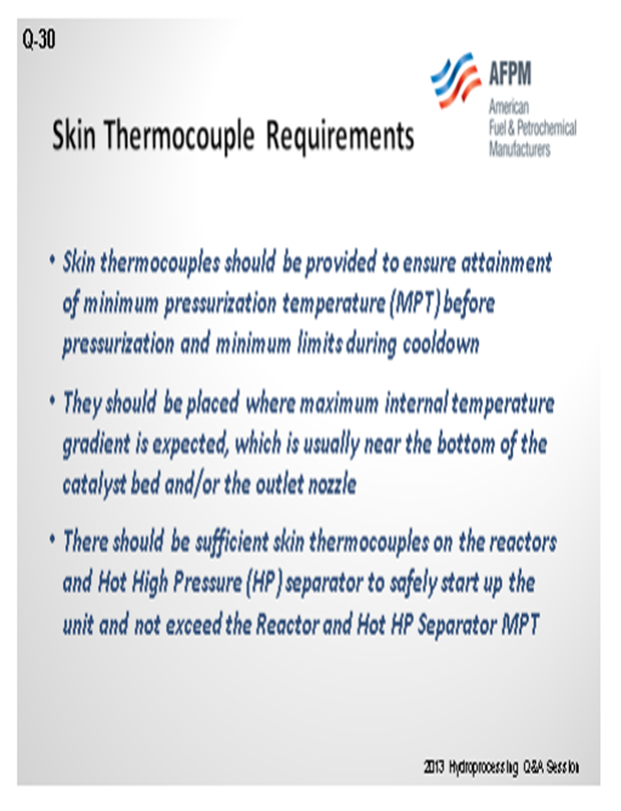
Additional critical requirements are a quench nozzle and skin thermocouple. It can be helpful to determine the temperature differences inside the reactor, which we have seen. We have seen a 50° difference in the skin thermocouples, which confirms what happened inside of reactors. However, we do not use reactor skin thermocouple as part of the Safety Instrument System.
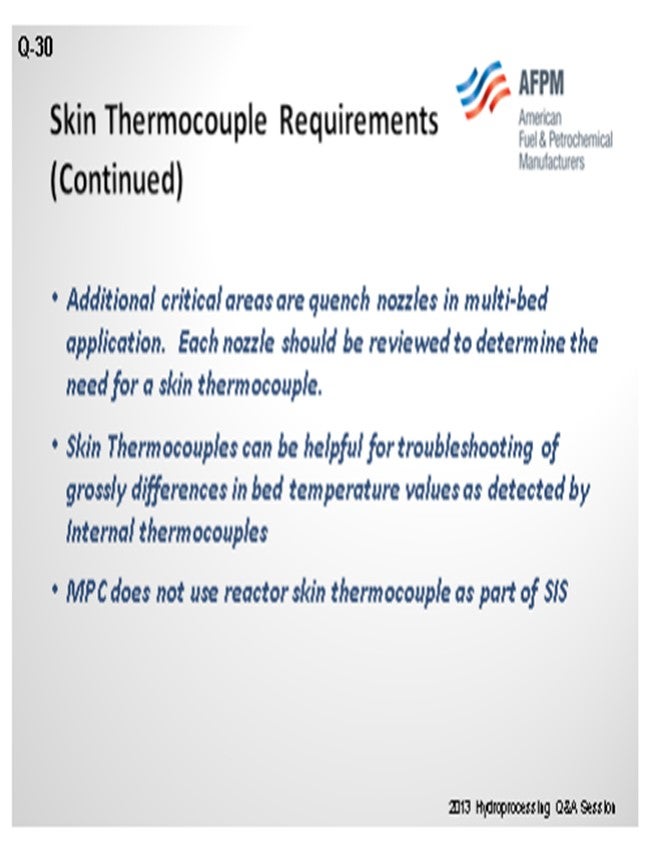
SIVADASAN (UOP LLC, A Honeywell Company)
UOP generally designs all of their Unionfining™ and Unicracking™ reactors with skin thermocouples. These skin thermocouples are mainly provided to ensure that the vessel temperatures are above their ductile-to-brittle transition temperature and that the vessels do not exceed their maximum design temperatures during their end-of-the-run. These thermocouples also detect some localized wall heating due to the hotspots in the catalyst bed. Sometimes these reactor skin temperatures are also used to put a limit on the ∆T (delta T; temperature differential) between the reactor skin and the catalyst beds.
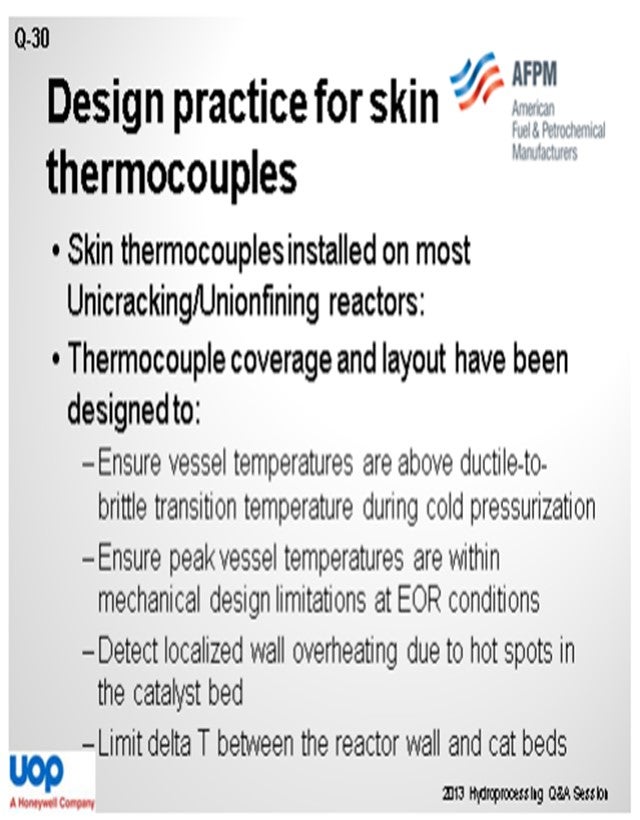
So, most of the Unionfining™ reactors have a ring of thermocouples at the bottom of the bed, and one more ring is provided at the bottom of the reactor shell.
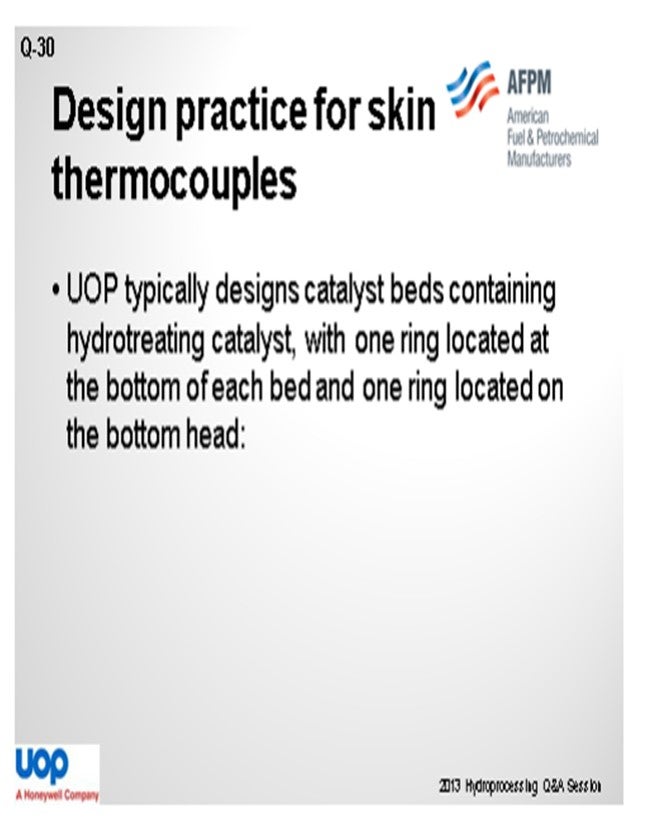
For hydrocracking units, the design is more or less similar to the Unionfining™ unit; except that this in case, there is an additional ring provided on top of the bottom bed and spaced four feet apart from the bottom ring. Also, the thermocouples are staggered in such a way, so they are in between the thermocouples on the bottom ring.
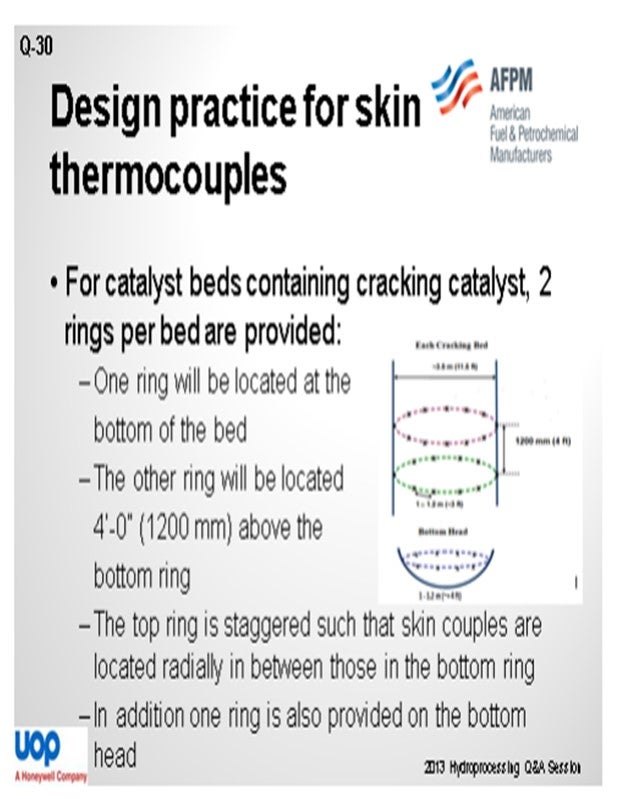
GATES (Motiva Enterprises LLC)
The skin thermocouples are placed on the vessel head and then on the thicker part of the shell itself. They are there to monitor the temperature of the vessel in order for us to understand when pressurization is allowed or when depressuring is required during shutdown. Your primary concerns are the temper embrittlement and hydrogen embrittlement of the low-chrome vessel itself. As an additional comment, at Shell, we do not use this as part of the automated depressuring system.
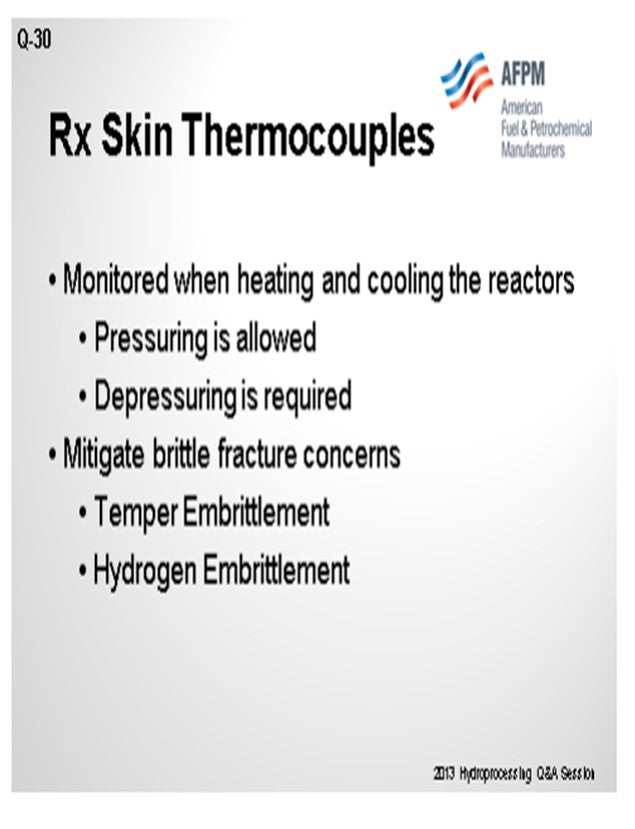
JON PRUDHOM (UOP LLC, A Honeywell Company)
What do you do if the reactor has a skirt? Do you tend to put thermocouples on the skirt?
VICHAILAK (Marathon Petroleum Corporation)
Right now, it is not required for us to put a thermocouple on the reactor skirt. For MPT, we normally look at the shell at the bottom head, mostly when starting up. I have talked to our metallurgists about whether we should have a skin thermocouple at the nozzle which is exposed to air. Most of the time, that part is not really covered; so it will be cooler. We do use IR (infrared) to shoot the skin temperature at the flanges, but we do not have actual skin thermocouples on the skirt or at the flanges.
ROBERT TORGERSON (Gayesco International)
Over the last year and a half, we have seen the requirements go up tremendously for this type of instrumentation. We literally have customers ordering hundreds at a time, which is probably leading to some of the questions here. What is interesting for us, though, is that there has been a significant change in the type of thermocouple. This transition has moved away from the traditional versions to one that is removable and online, which seems to help the reliability. If it is easy to replace, it tends to get replaced. With this design, the thermocouples are accessible as opposed to some of the traditional designs. When the points go out and are not changed out, the measuring point is lost.
MONTRI VICHAILAK (Marathon Petroleum Corporation)
Skin thermocouples should be provided to ensure attainment of minimum pressurization temperature (MPT) before pressurization. They should be placed where maximum internal temperature gradient is expected, which is usually near the bottom of the catalyst bed and/or the outlet nozzle.
MPC minimum recommendations for skin thermocouples on hydrotreating reactors are:
• 3 skin thermocouples at the top head 120° apart (required),
• 3 skin thermocouples at the bottom head 120° apart (required),
• 4 skin thermocouples at the top shell 90° apart, relatively close to the tangent line (optional),
• 4 skin thermocouples at the mid-shell 90° apart (optional), and
• 4 skin thermocouples at the bottom shell 90° apart, relatively close to the tangent line (required).
An additional critical area is the quench nozzles in multi-bed application. Each nozzle should be reviewed to determine the need for a skin thermo couple.
For the hydrocracking reactors, we installed the following skin thermocouples:
• 1 skin thermocouple reactor inlet nozzle,
• 4 skin thermocouples per reactor bed located 90° apart,
• 4 skin thermocouples on the bottom reactor head located 90° apart, and
• 1 skin thermocouple on the reactor outlet nozzle.
There should be sufficient skin thermocouples on the reactors and hot HP separator to safely startup the unit and not exceed the reactor and hot HP separator minimum pressurization temperature (MPT). In some situations, skin thermocouples can be helpful for troubleshooting gross differences in bed temperature values as detected by internal thermocouples.
RAJESH SIVADSAN (UOP LLC, A Honeywell Company)
Skin thermocouples have been installed on most Unicracker™/Unifiner reactors. The thermocouple coverage and layout have been designed to:
• Ensure vessel temperatures are above ductile-to-brittle transition temperature during cold pressurization,
• Ensure peak vessel temperatures are within mechanical design limitations at EOR conditions,
• Detect localized wall overheating due to hot spots in the catalyst bed, and
• Detect the ∆T between the Rx (reactor) wall and the catalyst bed.
The number of the skin thermocouples depends on the reactor diameter.
UOP typically designs catalyst beds containing hydrotreating catalyst, with one ring located at the bottom of each bed and one ring located on the bottom head.
For catalyst beds containing cracking catalyst, two rings per bed are provided. One ring will be located at the bottom of the bed. The other ring will be located 4 feet (1200 mm) above the bottom ring. The top ring is staggered such that skin couples are located radially in between those in the bottom ring. In addition, one ring is also provided on the bottom head.
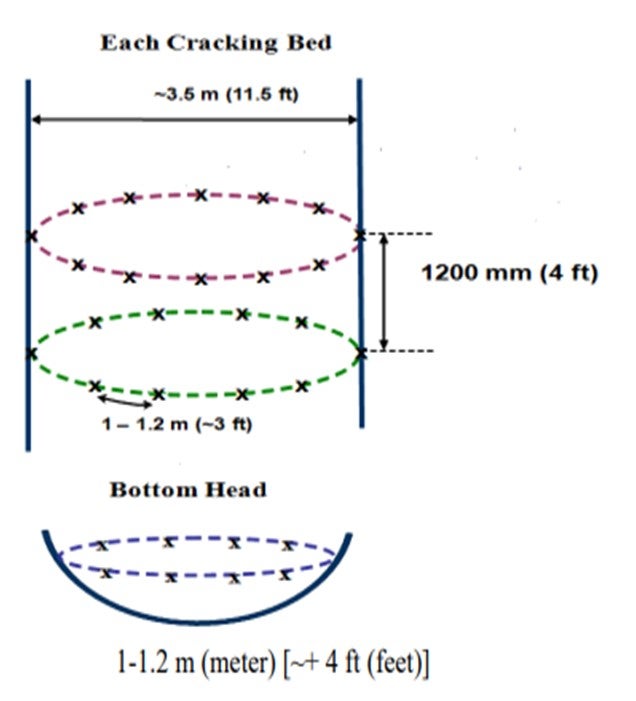
ROBERT TORGERSON and SYDNEY GARRETT (Gayesco International)
Online availability and reliability of skin temperature measurement for reactor skins is critical. This importance has caused many refiners to transition from traditional washer and stud style skin thermocouples and unreliable magnetic skin thermocouples to much more maintenance friendly “ski slope” guide tube designs.
The washer style thermocouple is a standard for many refiners, but it requires a variety of crafts (and associated permits) for replacement, which can be time-consuming. Commonly, this may include the following personnel:
1. Sheet Metal worker (for removal of protective skin),
2. Insulator (for verification and removal of insulation),
3. Mechanical/maintenance staff (for removal of nut),
4. Welder (for reattachment or repair of bolt stud),
5. Instrument tech (for replacement of washer thermocouple),
6. Insulator (for reinsulating of site), and
7. Sheet Metal worker (for repair of protective skin).
On the other hand, magnetic thermocouples can be problematic in that they lose magnetic force as the magnet rises in temperature, making them susceptible to detachment from the reactor.
The “ski slope” guide tube designs involve a specially designed temperature pad connected to a guide tube that gently curves up and away from the reactor and penetrates through the insulation and protective sheet metal skin. The thermocouple or RTD (riser termination device) is held in place by a fitting on the end of the tube which allows for a single craft (single permit) replacement of the thermocouple, thereby saving time and money. Because it becomes so quick and easy to replace a thermocouple with the ski slope design, they are more likely to be replaced when necessary, allowing the reactor to operate with a full complement of skin thermocouples for protection.
One of the “basic rules of thumb” for temperature measurement is to have 10 thermocouple diameters in parallel contact with the surface being measured. This allows for a consistent reading that eliminates any false impression due to temperature wicking through the metal of the probe itself. The “ski slope” design has this built into it, as does the aforementioned washer style thermocouples, but it is much more difficult to accomplish with magnetic style reactor skin thermocouples or other tip sensitive designs.