Question 30: How are water drains routed in alkylation units; for instance, in waterwash or propane drying services? What options exist for separation of the water and entrained light hydrocarbons? How can enclosed systems be monitored?
STEVES (Norton Engineering Consultants, Inc.)
In many units, including both HF (hydrogen fluoride) and sulfuric acid alkylation units, there may be opportunity to drain water from vessels that contain hydrocarbon. Obviously, this can create quite a bit of risk associated with draining hydrocarbons into a sewer system. It is important to control and manage this draining process to avoid getting those hydrocarbons there, especially the lighter hydrocarbons which can travel extensively through sewer systems and
result in fires in remote locations.
In some refineries for batch removal of water from hydrocarbons, such as what is done on an HF unit from a KOH (potassium hydroxide) treater, the draining is managed by having an operator directly perform the task and stop as soon as he detects hydrocarbon. Sometimes the use of a spring-operated dead-man valve can help ensure that the valve cannot be left open and unattended during the draining process. This activity process can also be done in a remote
location by using a pneumatically operated push-button valve. The valve will only open as long as the operator has his finger on the push button and will close once he let go. However, even with the remote draining, I have seen sewers erupt with a stream of caustic brine as a small number of light hydrocarbons entered the sewer hub.
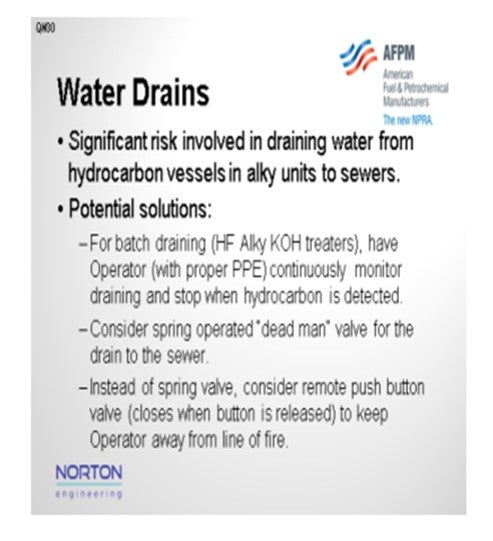
The best solution I have seen is to use a degassing pot for draining the hydrocarbons and caustic mixture from the KOH pot. In this type of operation, you can degas the water stream to either a vent gas recovery system or a flare such that the hydrocarbons have been vented off to allow for the material to then be drained safely to a sewer. Sulfuric unit acids are designed with a degassing pot on the water, leaving the waterwash column to prevent light hydrocarbon from entering the sewer. On HF alkylation units, I have seen the water drains from KOH treaters, in both propane and butane service, routed to a degassing pot like this one shown. The pot is then manually depressured to the flare before the water is discharged to the sewer. The use of this pot reduces the risk associated with light hydrocarbons in the sewer.
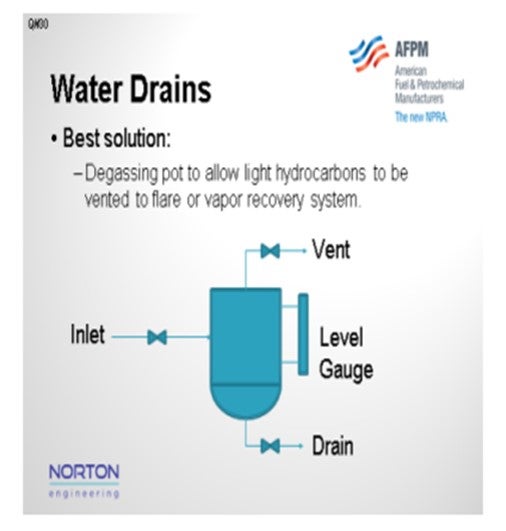
PIZZINI (Phillips 66)
First of all, I would like to second what Chris said about having a disengaging pot. The best option is for that pot to ride on the flare to give the propane or light hydrocarbons a chance to weather while leaving the water that remains at low pressure to go safely to the sewer. One example is that it is a good idea to drain the KOH treater every shift to avoid getting pluggage with salt. We even have some sites which purge that valve with water to prevent the pluggage.
And again, similar to what Chris said, operator attendance is required. In some cases, we do recommend having that dead-man or spring-loaded valve, so there is no chance of the valve being left open and the hydrocarbons escaping.
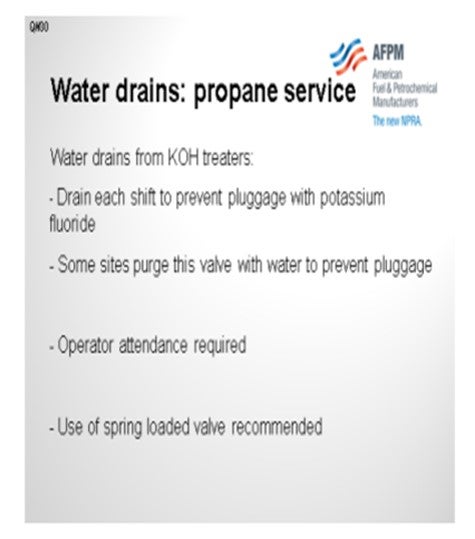
PIZZINI (Phillips 66)
KOH treaters are recommended to be “blown down” to a disengaging KO pot with the vapor vented off to the flare. The depressured liquid is gravity drained to the sewer with a frequency determined by operator experience. Drain once/shift, or at least once/day to prevent potassium fluoride from setting up. One site injects some water at this valve to keep it from plugging. The operator is required to stay in attendance while draining. Risk can also be reduced by using spring-loaded valve (dead-man valve) designed to close when not held open.