Question 3: What drives the decision to load presulfided, presulfurized, or oxidized catalyst in naphtha hydrotreaters? What are the different safety considerations for each case?
MELDRUM (Phillips 66)
I would like to begin my responses by grounding us in some definitions. Pre-sulfided catalyst is the catalyst that is delivered with an active metal sulfide site. Pre-sulfurized catalyst is catalyst in the oxide form but which then has added to it an organic sulfur compound. The metal sulfide sites are then formed in-situ during the startup process. Finally, sulfiding is the process of injecting a sulfur compound into the reactor for in-situ sulfiding after the catalyst is loaded.
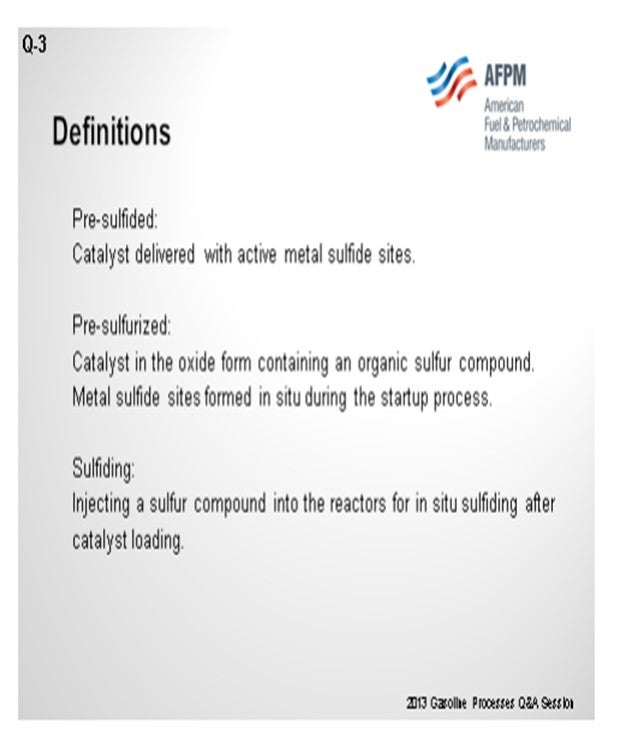
At Phillips 66, we use pre-sulfided catalyst in naphtha units when there is no off-test product line or tankage or where we want to save our startup time. We plan for about one to two days to complete an in-situ sulfiding step which can be eliminated using the pre-sulfided catalyst. We will also use pre-sulfided catalyst if we skim and replace a portion of a catalyst bed. If we are skimming more than 20 to 25% of the bed, we will come in with the pre-sulfided catalyst. If we are only skimming and replacing about 15% of the bed, then non-sulfided catalyst will be used; so there will be no need to do a separate sulfiding step during startup.
We generally do not use pre-sulfurized catalyst in naphtha service based on a slight concern about how the passivating agent might come off causing a sulfur slip to the reformer. This is not a major issue, but it might impact the downstream reformer for a couple of days.
Most of our naphtha high-treating catalysts are loaded in the oxide form and then sulfided in-situ as part of the startup process. When we do use pre-sulfided or pre-sulfurized catalysts, we make it a practice to order some of the inventory in the oxide form so that it can be returned if it is deemed surplus material. Once the catalyst has been sulfided or treated with the sulfurization chemical, then any surplus catalyst will be difficult to return. As precaution, we load sulfided and pre-sulfurized catalysts under inert conditions to prevent self-heating. We also use respiratory protection, usually supplied air, regardless of the catalyst condition to protect against any of the dust.
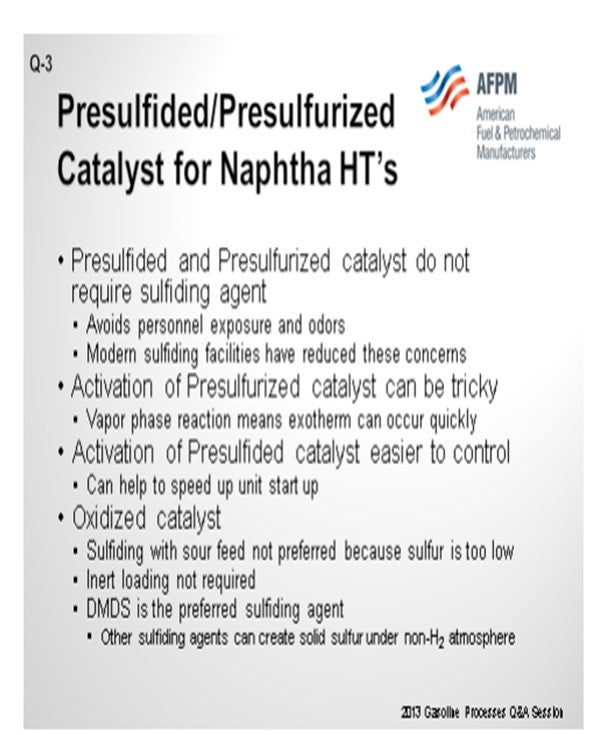
STREIT (KBC Advanced Technologies, Inc.)
I will mostly confirm what Craig just said. Pre-sulfided and pre-sulfurized catalysts do not require sulfiding agents. That is really one of the drivers for why you might want to purchase that material. Also, it avoids personal exposure and odors. It is less of a problem than it was in the past with the modern injection facilities and sulfiding agents, but still a concern.
Pre-sulfurized catalyst: One point that should be noted on a naphtha unit is that because of the vapor phase and the reaction, you can end up with some temperature issues when you are activating it. So be a little wary of this when using pre-sulfurized catalyst in this service. The activation of pre-sulfided catalyst is a lot easier to control, and the typical driver is just startup time. You can get the unit up a lot more quickly.
Oxidized Catalyst: If you decide to go with oxidized catalyst and have to go through the sulfiding step, then you will need to use some solid sulfurizing agent. In other services, you could use the feed sulfur to sulfurize a catalyst. In naphtha service, that is usually not high enough to be the case. The advantage of oxided catalyst is that you do not need inert loading facilities.
ERIC STREIT (KBC Advanced Technologies, Inc.)
Sulfiding with sour feed is usually not preferred in naphtha hydrotreaters because the low feed sulfur results in an H2S partial pressure too low to adequately activate the catalyst. So, the catalyst does need to be sulfided in some way.
If oxidized catalyst is used, the refiner must use a stream with a high H2S content or add a sulfiding agent of some type to activate the catalyst. DMDS (dimethyl disulfide) is the best sulfiding agent for this service. Other sulfiding agents, like polysulfides, have the potential to produce solid sulfur when no hydrogen is present. There are concerns with personnel exposure and odors with any sulfiding agent. Many refiners choose to avoid these issues by ordering catalyst with the sulfur already on the catalyst. With modern injection systems, leakage of sulfiding agents is usually a minor issue.
Presulfurized catalyst, where the sulfur has added to the catalyst but has not been activated, can cause problems in naphtha hydrotreater service. Because the reactions are occurring in the vapor phase, temperature control during the sulfiding step can be difficult, and the operator may experience a temperature excursion that could damage the catalyst. This is exacerbated by the fact that most naphtha hydrotreaters do not have bed thermocouples, so it is particularly difficult to control the heat release.
Adding presulfurized catalyst as makeup from a reactor skim can usually be done without major problems. In this case, only a small portion of the bed is being replaced; so, the exotherm during activation is not great. Loading presulfided catalyst, where the catalyst has been fully sulfided and activated by the supplier, provides the fastest way to bring the unit online. Presulfided catalyst is more expensive but can be justified in some instances. Examples of where presulfided catalyst may be justified include 1) units where pre-heat is limited and proper activation temperatures are hard to reach and 2) units where a fast startup is required, such as when the only hydrogen source in the refinery is the reformer.
Using catalyst with sulfur already on it should be done in an inert environment. Loading oxidized catalyst does not require an inert atmosphere, so operators who want to avoid loading under these conditions should choose oxidized catalyst.
STEVE TREESE (Phillips 66)
The following are a few definitions to establish a foundation for the answer.
• Presulfided: Catalyst manufactured and delivered with active metal sulfide sites on the catalyst.
• Presulfurized: Catalyst in the oxide form that has an organic sulfur compound added in the manufacturing step then passivated with a heavy organic material. Sulfiding occurs in-situ as part of the startup process, but the sulfur compound does not need to be injected onsite.
• Sulfiding: The process of injecting a sulfur compound into the reactors after catalyst loading for in-situ sulfiding as part of the startup process.
We use presulfided catalyst in naphtha units where there is no off-spec product line or tankage or where we need to save startup time (one to two days to sulfide in-situ). We also use it if we have skimmed and replaced more than about 20 to 25% of the bed (~15% of the bed can be skimmed and replaced with non-sulfided catalyst and without sulfiding as a separate startup step). The presulfided catalyst is handled under inert conditions as a precaution.
We generally do not used presulfurized catalyst in naphtha services based on slight concerns over the heavy, high endpoint passivation material going to the reformer and the amount of sulfur slip to the reformer. This is not a big issue, but it may hit the reformer for a couple of days. Most of our naphtha hydrotreating catalysts are loaded in the oxide form and then sulfided in-situ as part of the startup process.
When presulfided or presulfurized catalyst is used, we order some of the catalyst in the oxide form so it can be returned if there is surplus material. Once catalyst has been sulfided or loaded with sulfurization chemicals, then any surplus catalyst will be difficult to return. +
For presulfided and presulfurized catalysts in any service, we load under inert conditions to prevent self-heating. In theory, the catalysts are often passivated so they can be handled in air, but we are concerned about how long that protection lasts (one to two days) compared to how long it takes to load the beds (should be one to two days; but if delayed, it could be three to four days). In all cases, respiratory protection (usually supplied air) is used, regardless of the catalyst condition to protect against the dust