Question 3: What are your Best Practices for unloading solid phosphoric acid (SPA) catalyst from a catalytic polymerization unit, and what safety issues do they address?
KINDERMAN (Clariant Corporation)
The Best Practices for unloading solid phosphoric acid catalyst from a cat-poly unit include neutralization using hydrocarbon-free nitrogen, performing a pulse purse with nitrogen, and then releasing it through the bottom of the reactor. It is relatively simple unless there is some caking or building up of a solid material. The pH can be neutralized with soda ash if water drilling is used. Tarps are placed around the bottom of the catalyst to collect the fines if they come out in dust and scatters. That is the simple answer of how to unload the reactor.
SHARON (Valero)
From our perspective, the most important piece is really to do a quality JSA (Job Safety Analysis). That is what you want to knock out first. Bryan touched on quite few Best Practices, so I will just add a couple additional important safety procedures. One is that because you have the catalyst/support fall hazard, you will want to barricade about 150 feet around it and maintain limited access inside that barricade. Since you have the low pH runoff issue, you will want to have sodium carbonate available to neutralize any low pH material or excess water. Also, be prepared to contain the run-off material to avoid off-site impacts. Additionally, there is hot catalyst present which can auto-oxidize or glow a little. Be prepared to wet the catalyst; and again, be prepared for low pH runoff. Lastly, you have the catalyst fines, which are inhalation and skin irritation concerns, thereby necessitating the installation of the canvas curtain at the base of the reactor to protect personnel from dust.
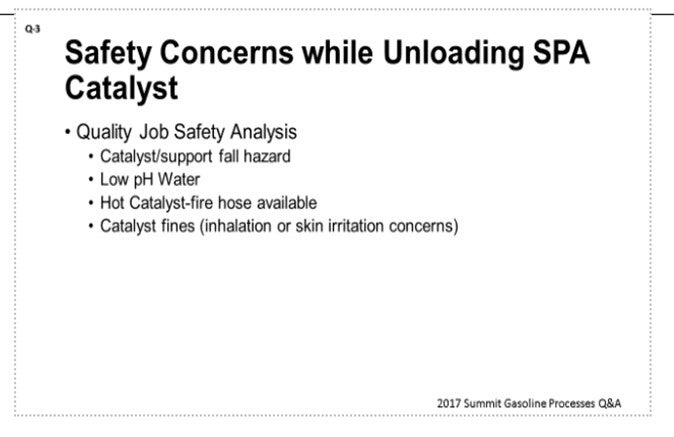
SABITOV (Phillips 66)
I think we still have one and a half units in operation, so we typically rely on the catalyst-loading contractor for handling catalyst. As far as I know, they are using a hydro-blasting method.
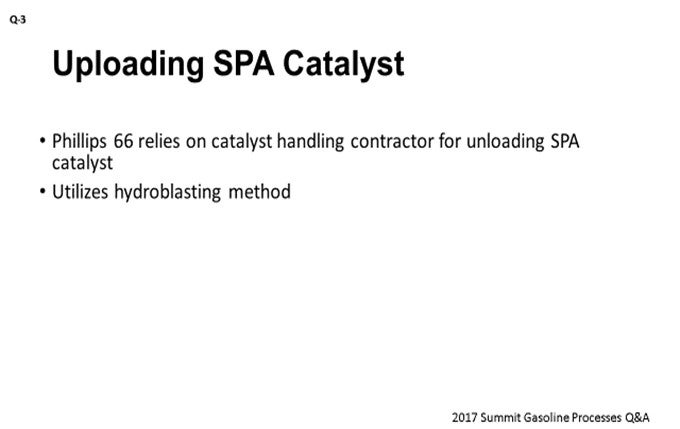
HEIDI FRASER (Honeywell UOP)
There are two types of Honeywell UOP Cat Poly reactors: chamber and tubular. Each has different unloading concerns, and there are several different unloading options available for each.
Chamber Reactors
The basic method is to remove the locking pins from the bottom support plate and allow the catalyst from the bottom bed to drop out of the reactor by gravity. After the bottom catalyst bed has dropped and been shoveled out of the collection bin at the base of the reactor, the locking pins for the next support bed are released and the grid can fall so that the next bed of catalyst will drop out of the reactor. Continue unloading one bed at a time. However, if the pressure drop across the reactor was allowed to get too high during the catalyst run, the catalyst will be coked up and/or carbon-fused together and will not drop. This is most common in the bottom bed as the pressure drop will be highest at this point: The higher the pressure drops, the more difficulty there will be unloading. In such an event, it becomes extremely difficult and dangerous to enter the reactor to break up the catalyst. The bridged catalyst could collapse and bring the person in the reactor into danger. As a result, alternate methods have been developed.
In water drilling or hydroblasting, the catalyst can be removed by cutting holes through the bed from the bottom using a high-pressure, low-volume water lance. This technique is helpful if the catalyst bed has partially dropped but the remaining catalyst is bridged. Cutting holes in the catalyst may break up the bridge and allow the remainder of the catalyst to fall. If the catalyst still does not fall, open the manway above the bed and use short bursts of fire water directed at the catalyst to remove the remaining catalyst. Only one manway should be opened at a time to prevent air from circulating through the spent catalyst. The oxygen could react with the tar on the catalyst to produce carbon monoxide. Another disadvantage of this method is that the water reacts with the SPA catalyst and becomes corrosive. Use no more water than is needed. Runoff should be neutralized with sodium carbonate or calcium carbonate to reduce its acidity.
In pressuring out the catalyst with steam, as each grid is released, a steam line is connected to the quench connection above the bed to be unloaded. This approach allows the pressure in the void space above the catalyst to build up gradually to pressure the catalyst out the opening rather than relying on gravity. This approach is more effective for catalyst beds that are solidly coked up so that the pressure can build in the void space. A variation calls for opening the grids and then bracing the bottom head closed while the reactor is pressured up with steam to 5 to 7 psig (pounds per square inch gauge). Then the brace is removed remotely, and the catalyst is expelled violently. These methods eliminate the need for a person to enter the reactor to break up the fused catalyst to start catalyst flowing but will result in a great deal of dust in the area. Both are described in the UOP General Operating Manual.
The controlled detonation technique uses small explosive charges to dislodge the catalyst so it will drop out the bottom manway. The intent is not to use charges with such size as to force the catalyst from the reactor; but rather, to break up the solidified catalyst mass into smaller pieces that are easier to dislodge. This approach was developed by a Texas company and has not been quantitatively analyzed by UOP, so it is not officially recommended. However, we are aware that many of our North American customers routinely use this technique successfully. There have been some reports of damage to the grid screens from shrapnel from the conduits to which the explosives are taped. There has also been some concern about stress on the reactor vessel from the explosions, but no damage has been reported to a reactor vessel so far, including cracking or bulging, except the grid screens. This method is much quicker and more effective at emptying the catalyst from the reactor but results in a great deal of dust in the area.
The vacuuming and CARDOX technique were introduced by one of the catalyst handling companies and is a cleaner system. Catalyst is vacuumed from the top bed downward. The support grids will only be opened after all catalyst has been removed from the bed above. If the catalyst is agglomerated, it cannot be removed by vacuuming only. The catalyst could be broken up with small jackhammers. If the catalyst is tightly sintered together, CARDOX would be used to break it apart. CARDOX is a modern blasting device that uses CO2 for dislodging coal and other mining materials. The CO2 is released under pressure from cylinders drilled into the catalyst bed. The explosive discharge (like a fire extinguisher) breaks up the catalyst. CO2 is a non-supporter of combustion. During the unloading step, the reactor is kept under a nitrogen blanket to prevent dust explosions. The benefits claimed by this method are that there is no dust or corrosive water to clean up, so the work area is cleaner.
Tubular Reactors
Tubular reactors can be unloaded using either dry or wet drilling. The reactor tubes are drilled individually from the top using an air-driven turbine drill. Different augers or bits may be required to drill the catalyst out of the tubes. Dry drilling requires a catalyst collection system and may have trouble in gummy spots. Cold water in the jacket helps to harden the gummy spot and allow it to be drilled out more easily. Care must be taken to be certain that the tubes are clean, especially in those sticky spots. Some refiners have reported signs of etching in the tubes from dry drilling.
Use of a wet drill is typically better than a dry drilling at removing all deposits, and a cold shell also enables better catalyst removal. The disadvantage is that a considerable amount of acidic water is created from the reaction of the water with the SPA catalyst fines. Runoff should be neutralized with sodium carbonate or calcium carbonate to reduce its acidity. Some units have experienced corrosion in the lower part of some tubes. It may be that water is getting into undrilled tubes.
Both methods require that reactor tubes should be cleaned with an air-driven wire brush to remove any remaining catalyst, scale, or coke deposits. Catalyst fines should be cleaned from all exposed surfaces to prevent corrosion.