Question 27: What do you do to predict Silicon breakthrough in a naphtha hydrotreater? What are the consequences to the downstream units if breakthrough occurs?
JOE RYDBERG (CITGO)
CITGO refineries basically operate in the full coking mode which means that on our usual crude blends we do no net VTB for outside sales nor we are a player in the Bunker fuels supply market. Having said that, we have to be watchful of the demand shift that will follow with the implementation of the IMO-2020 specification on Bunker. Some low sulfur or untreated Gas oils (< 0.5% S) may displace the HSFO which will put pressure of the sweet gas oils for FCCU feed. This may specially be the case with refineries which change their crude slates to lower the crude blend sulfur. Some short term demand will be created on the ULSD product as a blend medium for bunker but likely will not be a long term economical solution. Ship operators will not be able to pay for ULSD type fuel as bunker.
We do not think that in the long run the diesel or the gas oil hydrotreaters will be impacted by the implementation of the IMO2020 compliant Bunker fuel as a result of the shale revolution in the US. We did not execute any IMO2020 driven projects in the hydrotreating area.
ROBERT STEINBERG (Motiva Enterprises)
The impact of the IMO 2020 low sulfur fuel oil specifications on hydroprocessing units is refinery specific. This is dependent on the refinery configuration and crudes processed. While some refineries may need to make major changes to their operations, others will not be impacted. If a refinery will start making lower sulfur fuel oil, additional hydrotreating of atmospheric resid, vacuum resid or other low value products may be required. If all residual materials are cracked, there may be additional coker gasoils or other products that require hydrotreating.
A sophisticated refinery with sufficient coker capacity for all its vacuum resid that does not normally make fuel oil would not be impacted much by IMO 2020. There may be opportunities to purchase low cost high sulfur fuel oil to keep the cokers full. The price of high sulfur crudes may decline which could lead to more opportunity crudes being run. These opportunities will likely mean an increase in production of coker gasoils and naphtha, as these are generally the hardest feeds to hydrotreat it may be necessary to somewhat increase hydrotreater severity. This will mean more hydrogen is needed and somewhat shorter catalyst lengths could be expected. But unless units are maxed out, the overall impact on the hydrotreaters is likely to be minimal and within the ability of operations to handle with routine adjustments.
YOGA AYAR and MARION BURLAK (Honeywell UOP)
With the MARPOL regulations in effect from 2020, Refiners have a few options for how to respond to these changes. One is to continue producing high sulfur bunker fuels and cope with the poor margins. In this case, a refiner might be able to soften the impact of low margins by adjusting crude slate, unit rates, and strategically reloading catalyst to maximize diesel production. For refiners looking to convert HSFO to lower sulfur or lighter fuels, many options exist and the optimal solution depends on existing refinery configuration and feedstock solutions to produce fuels that match the new demands. Examples of these beneficial options are shown in Figure 3.
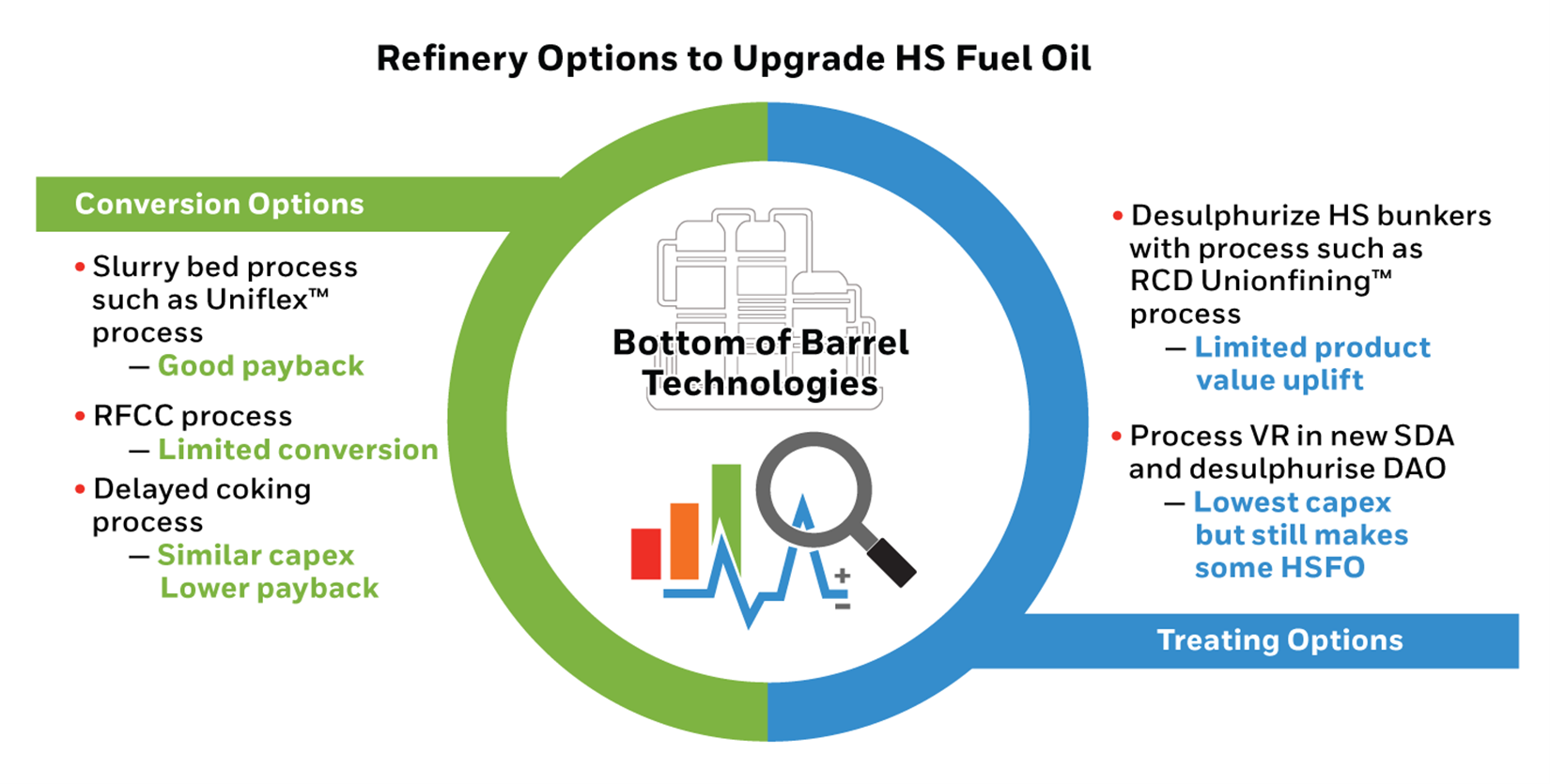
Figure 3
UOP Uniflex™ Process
The Uniflex process is a slurry hydrocracking process that converts feedstocks heavier than vacuum gas oil (VGO) into diesel and some VGO. It can accept both vacuum residue and pitch as feedstocks. Unlike delayed coking, Uniflex provides 98% conversion, higher liquid yields and no coke by-product. Installing a Uniflex unit would allow a refiner to move out of the fuel oil market entirely.
• Residue Fluidized Catalytic Cracking
A residue fluidized catalytic cracking (RFCC) unit converts heavy fractions such as vacuum residue and vacuum gas oil into lighter products such as light cycle oil, gasoline and light olefins. RFCC can be used to process deasphalted oil as well as heavy oil from a UOP RCD Unionfining™ unit.
• Delayed Coking
The delayed coking process thermally cracks residue into coker gas oil and petroleum coke. Delayed coking is used in many refineries to convert the heaviest materials into lighter liquid products with petroleum coke as a by-product. Light coker gas oil and naphtha are then hydrotreated to remove sulfur, while heavy coker gas oil may be routed to the UOP UnicrackingTM Process (hydrocracking unit) for conversion to distillate and/or naphtha products.
• Residue Hydrotreating
Honeywell UOP reduced crude desulfurization (RCD) Unionfining process may be used to produce a hydrotreated residue along with small amounts of distillate and naphtha. The desulfurized RCD product is typically routed to an RFCC unit for conversion. Very high levels of metals and carbon residue in the feed can make RCD technology uneconomical, so a refinery considering RCD/RFCC technology should consider the limitations that would consequently be placed on refinery crude selection.
• UOP/Foster Wheeler Solvent Deasphalting Process
A solvent deasphalting (SDA) unit is a relatively low cost option to reduce feed to residue-converting units and increase the amount of material that is upgraded. An SDA unit processes vacuum residue and through separation produces deasphalted oil (DAO), pitch, and bitumen. The DAO can be upgraded in either a unit Unicracking Process or an RFCC unit. Pitch can be sent to either a Uniflex unit or a delayed coking unit, or used for asphalt production.
Important to note is that the gas oils and distillates produced from residue conversion processes contain high levels of feed contaminants and require further processing to meet fuel specifications. Table 1 compares typical properties of straight run vacuum gas oil (VGO) with those of products from different residue conversion units.
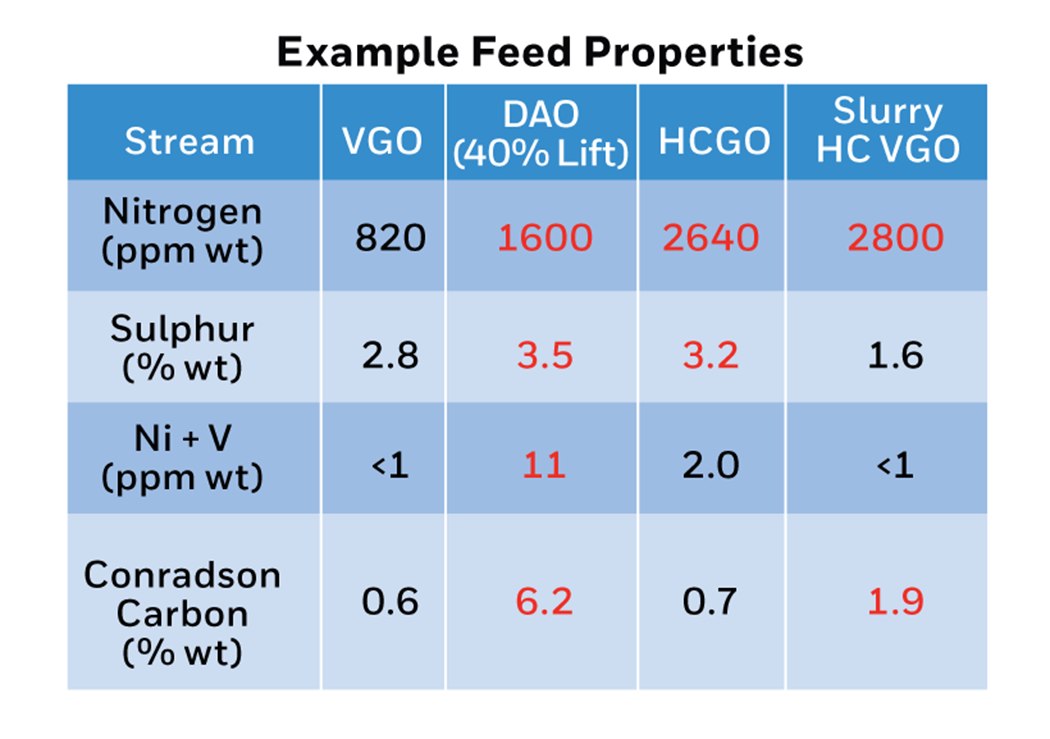
Table 1
All of these residue conversion products have higher levels of sulfur and nitrogen which have an impact on the design of the downstream hydrocracking unit. Deasphalted oil also contains high levels of conradson carbon residue (concarbon), poly-aromatics, and metals. DAO can be processed in the Unicracking Process, but the quantity may be limited to manage the unit cost and the catalyst cycle length. Honeywell UOP has extensive experience hydrocracking residue conversion products and utilizes commercially proven heavy polynuclear aromatics (HPNA) management technology to maximize conversion with these heavy feeds.
REFERENCES
1. 2020 – IMO Driving Opportunities for Refiners: Addressing with Unicracking™ Process Technology and Catalyst
2. IHS Market
HENRIK RASMUSSEN (Haldor Tospoe, Inc.)
The impact of IMO will depend on the configuration of each refinery. The higher complexity of the refinery, the smaller amount of high sulfur fuel oil (HSFO) which will be produced. Most refineries will only produce a very small amount of HSFO (single digits percentage of their total crude capacity) and can choose to deal with it in several ways.
It is possible to blend the HSFO with low or ultra-low sulfur diesel to meet the IMO specification. That will require more ULSD production and as a result, increase the operating severity of the ULSD hydrotreating units. Another disposition for the HSFO is feed to the coker unit resulting in more barrels of cracked stocks, which will have to be processed in the downstream coker naphtha, coker diesel and coker gas oil hydrotreating units. The severity of these units will increase resulting in shorter cycles and higher hydrogen consumptions.
Overall the IMO specifications will increase the operating severity of the refinery unless the HSFO is exported to a third party facility where is it hydrotreated to low sulfur fuel oil. Very few units are being built for this purpose and it is unlikely that any such facilities will be ready before the IMO specification are in effect in early 2020.