Question 26: How will the ISO 8217 Marine Fuel Oil Hydrogen Sulfide (H2S) specification (less than 2 ppm H2S in the liquid phase) affect refiners? Do any refiners plan to implement the standard, and what procedural or equipment changes are likely needed in order to meet the specification?
GROPP (GE Water & Process Technologies)
Simply put, refiners will be required to meet the ISO 8217 2 ppm H2S specification if they are going to sell fuel oil to customers who have requirements to meet this specification. ISO 8217 is a fuel specification, not a regulation. A regulation is enforced by some regulatory organization. Ironically, in 2008 the International Maritime Organization (IMO), which is an international regulatory body, approached the ISO (International Organization for Standardization). IMO asked the ISO to review the ISO 8217 Marine Fuel Oil specification and make recommendations to ISO regarding specific fuel parameters, including H2S levels. ISO commissioned a task force; and after a lot of work, the task force produced a test method and 2 ppm H2S specification for marine fuel oils. Analyzers are now available to measure H2S in the liquid phase of fuel oil. After reviewing the method and specification, IMO decided not to adopt the ISO recommended 2 ppm specification stating their decision that H2S levels are a contractual matter between buyer and seller. Therefore, at least at this point, they did not include H2S in their marine fuel regulation.
From GE’s point of view, we are seeing a number of our refining and marine fuel oil trading customers adopt the specification. In some cases, refiners must reduce H2S in their liquid streams, particularly the heavy resid fuels, to meet the specification. The options available include capital equipment upgrades in the form of additional hydrotreating capacity and/or stripper modifications, blending with low H2S components, and the use of H2S scavengers to tieup the H2S. Our experience to date indicates that most refiners are tweaking their existing processes, paying particular attention to blend compositions, and then utilizing H2S scavengers whenever it makes sense to meet the specification.
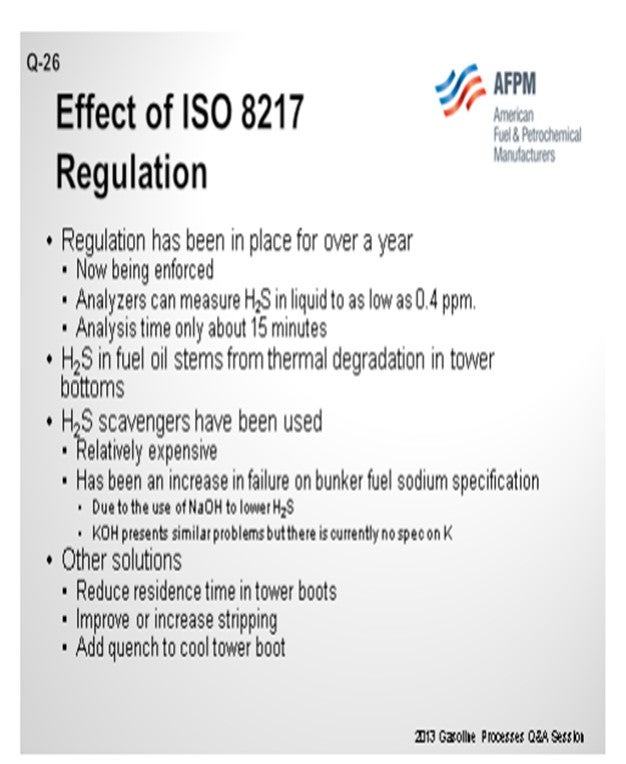
STREIT (KBC Advanced Technologies, Inc.)
When I first saw this question, I thought, this is the Gasoline panel, right? because I am not used to dealing with this black oil stuff. So, I had to study up on this myself. I learned a lot of the information that Ron discussed. At KBC, the places we have seen this being an issue are where there is H2S in the fuel oil. It is generally caused by thermal degradation in the tower bottoms. So, you hit high temperatures in vacuum tower bottoms or in main fractionator bottoms, H2S is formed at these high temperatures and not stripped from the tower bottoms. The tower bottoms are then blended to bunker fuel.
In my reading, there was discussion about the scavenger use, which can be relatively expensive depending on how much fuel are you making. The industry has recently had a lot of excursions on sodium in bunker fuel, so it appears that some places are using sodium hydroxide to neutralize the H2S in the stream. Potassium hydroxide is also being used. Although there is no spec on potassium, it does cause much of the same problems in the scrubbers as the sodium does. So, it would not surprise me if there was some pushback on the potassium levels in the future.
So how do you prevent the bunker fuel from containing H2S in the first place? One operational adjustment you can do is reduce the residence time in the boots of those hot towers. Reducing the time that the bottoms material sees the high temperatures reduces the likelihood that it will degrade and form the H2S. In some cases, the problem may be in the ability to strip the H2S out of the bottom's material. Improving your stripping trays or increasing the number of stripping trays in the bottom of a hot tower can increase the ability to strip H2S. Another possibility is to add a quench to the boot to keep the temperature of the boot down lower and avoid creating H2S.
GROPP (GE Water & Process Technologies)
I want to build on what Eric said a little. You do have to be careful which H2S scavengers you employ, particularly if you are going to use a simple inorganic base compound like sodium hydroxide or potassium hydroxide. The reason is the inorganic base forms an ionic bond with the H2S, and the reaction is very much reversible in the presence of strong acids and/or high temperatures. So the treated fuel can be a hazard aboard ships or wherever the fuel is used. If the treated fuel comes into contact with a strong acid or high temperature, the base may release the H2S. We recommend H2S scavengers that produce non-reversible reactions.
JESSY TRUCKO (UOP LLC, A Honeywell Company)
As a UOP treating specialist, I do not usually deal with this. I imagine that using sodium hydroxide in this service would really look like a mess to me because of all the kinds of organic acids in there that will end up causing emulsions. My comment is that it is really no surprise that you are getting sodium hydroxide carryover due to those emulsions. I mean, that has to be a mess. If you were going to try it, you would have to use a weak sodium hydroxide. You would probably also have a lot of sodium hydroxide to try to minimize those emulsions, as well as probably having some kind of electrostatic precipitator downstream of it to coalesce out the sodium hydroxide.
STREIT (KBC Advanced Technologies, Inc.)
I think that is a good part of the reason why the sodium levels are so much higher. All of these sodium excursions are happening now that did not occur in the past just because people are trying to get on-spec on H2S and maybe do not know how..
RONALD GROPP (GE Water & Process Technologies)
Simply put, refiners will be required to meet ISO 8217 Marine Fuel Oil Hydrogen Sulfide (H2S) specifications if they sell fuel oil to customers who have requirements to meet the 2 ppm H2S specification. ISO 8217 is a specification, not a regulation. Regulatory and enforcement agencies must adopt and enforce the specification for it to have any “teeth”. For example, in 2008, the IMO (International Maritime Organization) asked the ISO (International Organization for Standardization) to review the ISO 8217 Marine Fuel Oil specification and make recommendations to IMO regarding specific fuel parameters, including H2S levels. In 2011, IMO elected not to adopt the ISO recommended 2 ppm maximum H2S level established in the latest Marine Fuel Oil specification (ISO 8217:10) for the latest version of MARPOL (International Convention for the Prevention of Pollution from Ships) 73/78, Annex VI Regulation 18 (Fuel Availability and Quality). In fact, MARPOL elected not to include an H2S limit in the regulation. In summary, regulatory agencies and their constituents make decisions to adopt specifications and enforce them or not.
From GE’s point of view, several of our refining and fuel trader customers are producing fuel to meet the 2 ppm H2S specification. We do not have detailed geographic survey information regarding ISO 8217 adoption.
To meet the 2-ppm specification, many refiners must reduce the H2S content of their fuels, especially heavy fuels. Options available to accomplish this include:
1. Capital equipment upgrades, such as increased hydrotreating and/or stripper modifications,
2. Blending with low H2S content streams, or
3. The use of H2S scavenging additives. Our experience indicates that most refiners are tweaking existing process equipment, paying close attention to blend compositions, and employing H2S scavenger additive programs such as those offered by GE.
ERIC STREIT (KBC Advanced Technologies, Inc.)
The 2 ppm H2S limit for marine fuel oils associated with ISO 8217 was put in place in July of 2012. However, it has been difficult to enforce due, at least in part, to the inability to accurately measure these low levels of H2S in the liquid fuel oil. Analyzers have been developed that can purportedly measure H2S down to 0.4 ppm levels with only a 15-minute processing time. With this new analyzer ability, ISO 8217 is more likely to be enforced.
In refineries where we have seen a problem with H2S in the fuel oil, the issue has stemmed from H2S being created by thermal degradation in hot tower bottoms, mainly vacuum towers. H2S scavengers have been added to meet the specification; but this can be expensive, so other longer-term solutions have been examined as well.
In wet vacuum towers and visbreaker columns, stripping steam can be increased to remove H2S from the tower bottoms. Crude tower stripping steam has been increased as well, but with a lesser effect. Installing a steam sparger in the bottom of the vacuum tower can help improve stripping and thus lower H2S in the bottom's product.
Reducing the pressure in the vacuum column can also help strip more of the H2S. These solutions focus on stripping the H2S rather than preventing it from forming in the first place. Reducing the residence time in the vacuum tower bottom sump can help reduce the amount of H2S that forms due to thermal degradation. Adding a quench to the vacuum tower boot can be used to reduce the vacuum tower bottoms temperature, which also reduces thermal degradation.
Another potential source of H2S in fuel oil is a leaking exchanger. If H2S is detected in the fuel oil, refiners should look for other symptoms that may indicate an exchanger leak and repair any leaks that are detected.
PAUL YON-HIN (Nalco Champion Energy Services)
In principle, the ISO 8217 Marine Fuel Oil Hydrogen Sulfide specification of less than 2 ppm in the liquid phase is to be practiced by refiners, but that is not necessary the case since they may just manufacture components of the marine fuel. It then then becomes the blender’s responsibility to manufacture a finished marine product that meets the ISO 8217 specification. With the introduction of the ISO 8217 specification for H2S level for health and safety reasons, refiners are now monitoring their H2S level in their products. Typically, they want to have products that have less than 10 ppm of H2S level in the vapor phase in their storage tank at the refinery. Such fuel will easily pass the 2 ppm H2S level in the liquid phase. To implement the ISO 8217 H2S specification, a new and rapid method has been developed and introduced to measure H2S level in the fuel oil as described in IP 570 Method. At the refinery or blender locations, if the H2S level is higher than the limit of 2 ppm, then a H2S scavenger use is the best way to bring the fuel on-spec for H2S level in the most economical way. No equipment changes were needed to implement this new H2S specification at the refinery. Some refiners have acquired the instrument to run the IP 570 test method.