Question 25: What issues are encountered when introducing cracked naphthas into units that were not originally designed for the higher olefin content? What other contaminants should be considered when making this change in operation, e.g., silicon, nitrogen, and sulfur?
STREIT (KBC Advanced Technologies, Inc.)
There are many potential issues. The single most obvious one is the heat released due to the olefins. You must make sure you can handle the heat release without coking up the reactor. You also have a higher risk of furnace fouling or coking in the furnace. The higher outlet temperature from the combined feed exchangers, due to the heat release from the olefins, can result in the feed reaching a dry point prior to the furnace, which will be a big problem. You can also get more fouling in the feed exchangers, particularly if there is oxygen in the naphtha. The oxygen and olefins will form gums and lay out into your exchangers. That is a common problem when processing olefinic stocks.
You also have a higher risk of mercaptan reversion in the reactor. With the higher ∆T (temperature rise) you will get across the reactor, the reactor outlet temperature will be higher, which could result in mercaptan recombination in the outlet of the reactor. The hydrogen demand will increase as the olefins consume more hydrogen; potentially increasing coke make on the reactor. The increased hydrogen demand may get to the point where you cannot get enough hydrogen into the unit.
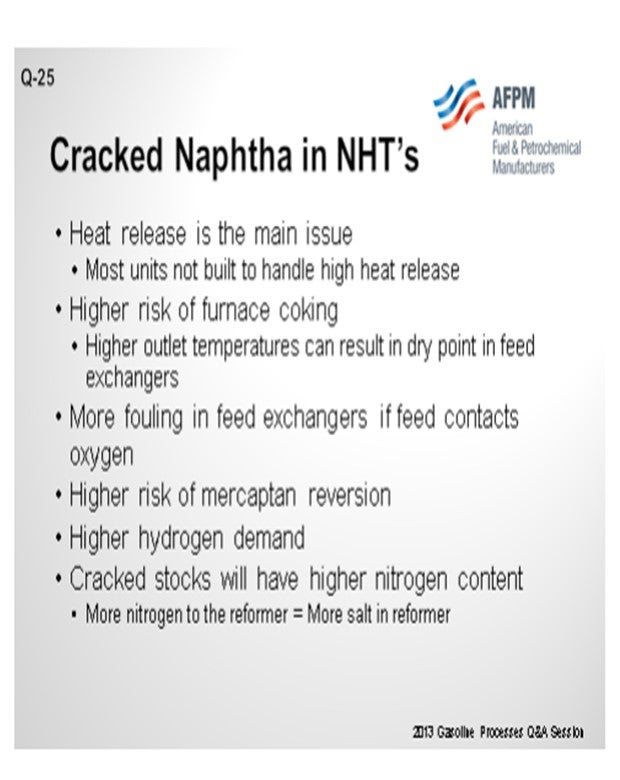
Frequently, cracked stocks will contain high levels of nitrogen. If you are going to process more olefinic material, you will probably process higher nitrogen as well. That will result in a higher nitrogen content in the outlet of the naphtha hydrotreater, which will then convert to ammonium chloride salts in the reformer.
Ammonium chloride deposition can also occur in the naphtha hydrotreater. Most naphtha hydrotreaters get their hydrogen from a reformer. If you do not have a chloride guard bed on your reformer hydrogen, you will have chlorides in it. Those chlorides can find this ammonia that is produced in the naphtha hydrotreater because of the higher nitrogen content. This can result in more ammonium chloride fouling in the naphtha hydrotreater itself.
You also have a higher risk of H2S-based corrosion; again, due to the olefins. You are also likely to get some catalyst poisons along with the olefins. Silicon is the most common one because it is used in antifoam in cokers. So, if we are talking about olefins from coker naphtha in particular, you must make sure you have an idea of how much silicon is in that naphtha. The naphtha hydrotreater needs to be designed to handle that silicon. The catalyst must be changed out before the silicon breaks through because it is very expensive if you start putting silicon into a catalytic reformer. The silicon will deposit catalyst. You want to make sure it deposits on the cheap hydrotreating catalyst (or silicon guard bed), not on the expensive reforming catalyst.
You also may have some additional sulfur species that you are not used to dealing with if you get more cracked stocks in the naphtha hydrotreater. Generally, that is not much of an issue. these days with low gasoline endpoints. However, if you are running at higher endpoints, you can actually get some harder-to-remove sulfurs that your naphtha hydrotreater may not have the ability to remove.
Finally, all of those olefins that entered the naphtha hydrotreater are going to become paraffins, so you can usually count on a low naphtha reformer feed quality from processing cracked stocks. You will probably end up with lower N+2A material going into your reformer.
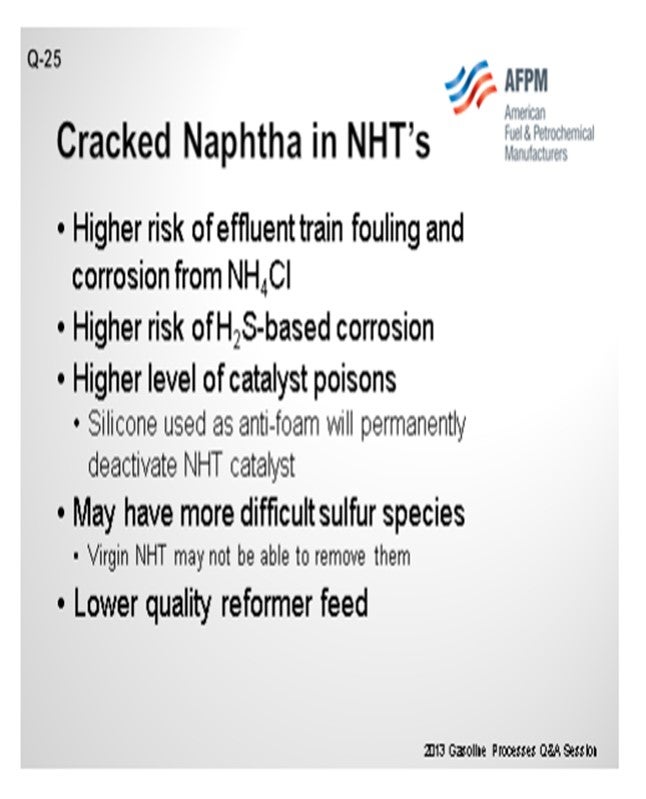
ADAMS (HollyFrontier Corporation)
That was a really complete answer, so I will just say that there is going to be a bigger exotherm in the reactor, as well as polymerization and plugging in the reactor. The silicon from the coker antifoam is going to kill the catalyst. If there is slippage of the nitrogen in the effluent into the reformer, then you are going to salt up the compressor, as Eric discussed.
BULLEN (UOP LLC, A Honeywell Company)
Additionally, if you have a splitter downstream, it is possible that some of these nitrogen species could end up in the isomerization unit and kill it as well. Generally speaking, a low-pressure hydrotreater will only be able to handle about 1 ppm or so of nitrogen; so, you will get breakthrough.
There are some traps available that you can put on top of the hydrotreater bed. The traps are specific for silicon, so they lay down more efficiently compared to the catalyst. That is an option if you are going to get a steady diet, so you do not have to change out your hydrotreating catalysts as often. The previous speakers covered the rest of the topic well.
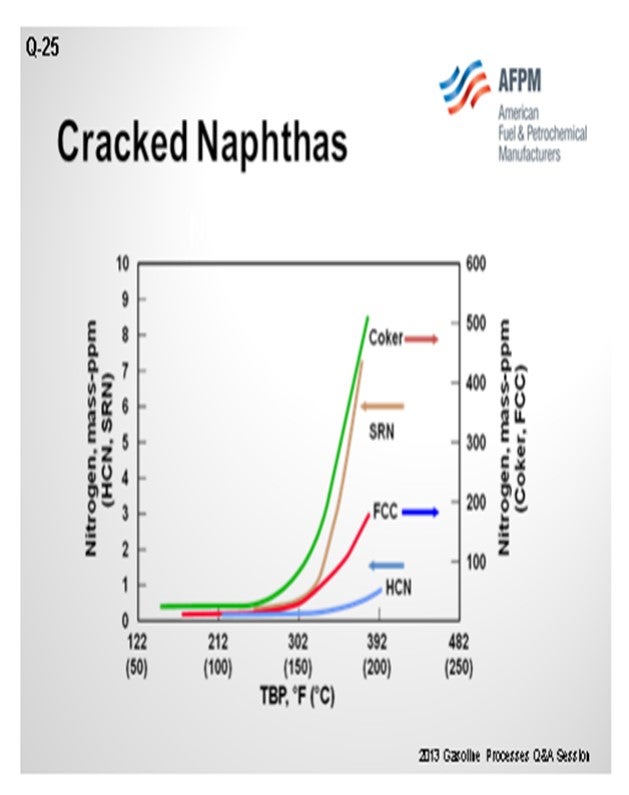
MARK ADAMS (HollyFrontier Corporation)
Generally, the exotherm is higher as hydrogen saturation and sulfur removal occur. Polymerization of conjugated diolefins occurs at normal hydrotreating conditions and causes fouling of the reactor and increased pressure drop. Silicon from coker antifoam kills the desulfurization catalyst. High nitrogen streams generate ammonia. Ammonium chloride can form and foul the reformer recycle compressor if some of the nitrogen slips through the naphtha hydrotreater into the reformer.
PATRICK BULLEN (UOP LLC, A Honeywell Company)
Cracked naphtha typically contains much higher olefin concentrations than straight-run naphtha (SRN). Olefins saturate quickly and easily in naphtha hydrotreating units (NHT). In addition to consuming hydrogen, the saturation reactions are exothermic. Depending on the concentration of olefins in the blended feed to the NHT, the temperature rise across the NHT reactor bed can exceed the design reactor delta temperature. For this reason, NHT units, which are designed to handle high olefin-containing feeds, are typically equipped to provide quench to remove the heat of reaction generated from the olefin saturation reactions.
In units that are processing higher olefin-containing cracked naphtha but which are not equipped with the ability to quench the heat generated from the olefin saturation reactions, a higher reactor outlet temperature will occur. The higher reactor outlet temperature can cause sulfur recombination resulting in off-specification high sulfur products. To avoid reaching the sulfur recombination temperature, the NHT reactor inlet temperature could potentially be decreased. However, care is required to maintain the reactor inlet temperature significantly above the dew point of the feed as to not allow for two-phase flow to the charge heater, which could negatively impact the operation and charge heater service life.
In addition to the concerns of processing olefinic feeds produced from cracked naphtha, there is also a significantly greater potential for increased feed contaminants. As seen in the chart below, full boiling range cracked naphtha has a significantly greater level of organic nitrogen in the higher boiling range relative to straight-run or hydrocracked naphthas. As a result, processing cracked naphtha can produce increased levels of organic nitrogen into the NHT. Denitrification reactions are difficult reactions to promote and are favored by high reaction pressure. If the organic nitrogen contaminate level in the feed exceeds the design criteria of the NHT reactor pressure, then the NHT product will become off-spec due to increased nitrogen. Nitrogen slipped to downstream operating units can result in both lost production and potential mechanical impact on operating equipment from the deposition of ammonium chloride in a reforming unit. For all types of isomerization units, the catalyst acid sites are deactivated by nitrogen species.
Cracked naphtha can also have high contaminate levels of organic metals: silicon (Si) and arsenic (As). These metals can be converted in the NHT at various levels of efficiency. However, the NHT catalyst will have a finite contaminate metals capacity. Once this capacity has been exceeded, breakthrough to the downstream process should be anticipated. In addition, the upstream process that produces cracked naphtha may also utilize chemical injection(s), such antifoulant and anticorrosion inhibitors. Some chemical injection compounds can contain Si that will boil in the naphtha boiling range resulting in increased contaminants being sent to the NHT.
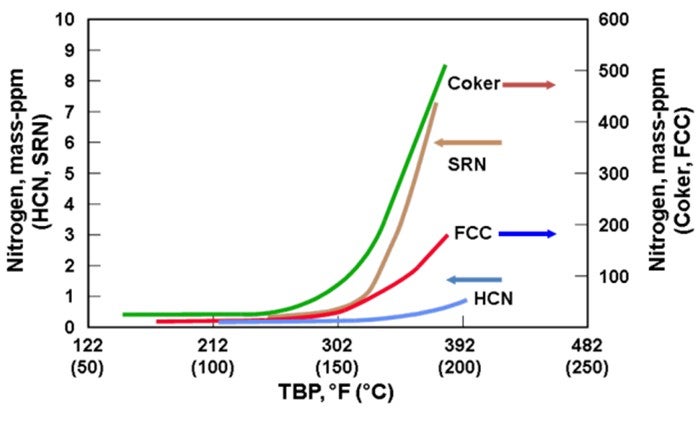
ERIC STREIT (KBC Advanced Technologies, Inc.)
There are a number of issues with introducing cracked stocks to a naphtha hydrotreater that is not designed to handle it. These include:
1. High Reactor Exotherms and High Hydrogen Consumption: Probably the biggest issues are the increased heat release and hydrogen consumption that come from saturating olefins. Units not designed to process cracked naphthas do not have any way to control the temperature rise across the bed. As a result, the units may be limited by how high the reactor outlet temperature is allowed to go. Naphtha hydrotreaters processing virgin stocks have extremely low hydrogen consumption rates. Many units designed for virgin stock will not have enough capacity in the makeup compressors to handle a large increase in hydrogen consumption. Also, higher olefins in the feed can increase the hydrogen consumption to the point where there is no hydrogen available at the reactor outlet, causing coking and sulfur slip. As a result of the lower hydrogen partial pressure and the higher temperature at the outlet of the reactor, cracked stocks can greatly accelerate coking of the catalyst, reducing unit run length.
2. Higher Risk of Coking in the Furnace if the Higher Reactor Outlet Temperature Results in the Feed Reaching Dry Point in the Exchangers: The higher outlet temperature of the reactor can cause the unit to reach the dry point in the feed exchangers. This can increase fouling in the feed exchangers, furnace and/or reactor.
3. Higher Fouling in Exchanger Train if the Feed Comes in Contact with Oxygen: The olefins in cracked stocks will react with oxygen to form gums that can foul the feed exchangers and reactor bed. This can occur if the cracked stock is stored in tankage or if it comes in contact with other feeds that have been stored in tankage. This problem can be mitigated by ensuring that the cracked naphtha is fed directly to the unit and that any other feed that is stored in tankage is stripped to remove the oxygen. If the cracked stocks come in contact with oxygen, the fouling can become quite severe.
4. Higher Risk of Mercaptan Reversion Due to the Presence of Olefins: Adding cracked stocks to a naphtha hydrotreater will also increase the risk of mercaptan recombination. Mercaptans at the bottom of the reactor can combine with olefins to reform sulfur species that are not removed in the stripper. As a result, the sulfur level to the reformer will increase. Mercaptan recombination is more of an issue with cracked stocks due to the high reactor outlet temperature created by the heat release of the olefins in the feed and the lower hydrogen partial pressure.
5. Higher Hydrogen Demand due to the Saturation of Olefins and Potentially Diolefins: Saturation of olefins and diolefins increases hydrogen consumption in the reactor. Units designed for very low hydrogen consumption may not have the compression capacity to supply enough hydrogen to the unit when processing cracked stocks.
6. Higher Nitrogen in Product due to Higher Nitrogen in Feed and Reduced Hydrogen Partial Pressure: Many cracked stocks contain more nitrogen than virgin stocks. In addition, the lower hydrogen partial pressure that can occur due to the saturation of olefins will reduce the denitrogenation ability of the unit. The result can be a significantly higher nitrogen content in the product, which will result in increased salt formation in the reforming unit.
7. Higher Risk of Effluent Train Fouling and Corrosion from Ammonium Chloride: Higher nitrogen contents will result in higher ammonia concentration in the effluent. The result can be increased formation of ammonium chloride in the naphtha hydrotreaters, which will increase fouling and corrosion in the effluent train.
8. Higher Risk of Corrosion due to Higher H2S Partial Pressure: The lower hydrogen partial pressure and potentially higher sulfur levels in the feed increase the H2S partial pressure in the effluent. This can increase the risk of corrosion in the effluent train or the naphtha hydrotreater.
9. Higher Levels of Catalyst Poisons: Coker naphtha, in particular, can cause major problems in units that are not designed to handle it. Cokers use silicone as antifoam. The silicone breaks down into components that boil in the naphtha range. These components contain silicon, which is a permanent poison for hydrotreating catalyst. Not only will it kill the desulfurizer; but if the silicon makes it through the hydrotreater bed, it will permanently poison the very expensive reforming catalyst. Silicon trap catalyst should be installed in any unit that plans to process any coker naphtha. In addition to silicon, depending on the source, cracked naphthas may contain high levels of heavy metals and other catalyst poisons. These contaminants present the same type of problems as silicon. Demetalization catalyst should be included in the reactor bed configuration.
10. More Difficult to Desulfurize: Cracked naphthas may contain sulfur species that are more difficult to desulfurize. These may be able to be controlled with good cutpoint control.
11. Changes to Reformer Feed Quality (More Paraffinic or More Aromatic than Crude Naphtha): Coker and visbreaker material is highly paraffinic once it has been hydrotreated. FCC material will be more aromatic. The effect of these changes to the reformer needs to be considered if any cracked stock is added to the naphtha hydrotreater.
STEVE TREESE (Phillips 66)
Adding cracked naphtha to a reformer pre-treat unit designed for straight-run naphtha will result in higher hydrogen consumption and increased temperature rises. Often units that previously saw no rise or a temperature loss across the hydrotreating reactor will see a much bigger exotherm. The operating conditions for SR naphtha hydrotreaters are generally much milder than you need for cracked stocks. The more severe conditions for cracked stocks are driven by the generally higher levels of sulfur and nitrogen with more difficult-to-treat types of compounds present. The presence of olefins will greatly increase hydrogen consumption, which will diminish the hydrogen partial pressure and thus decrease the high severity conditions needed for cracked naphtha treating. Some typical operating conditions for straight-run, mixed, and cracked feeds in our system are shown below. The conditions vary widely depending on the actual feedstock and the tolerable cycle length.
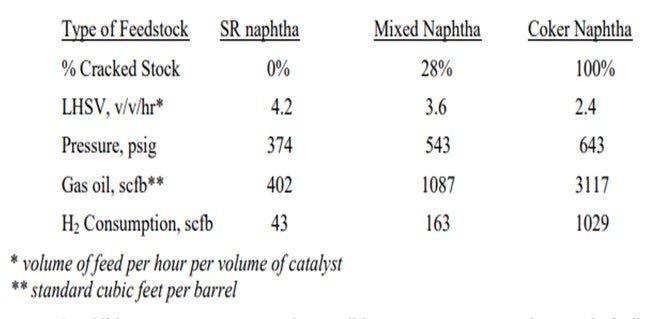
In addition to more severe operating conditions, you can expect an increase in fouling of the pre-heat exchangers, charge heater, and reactor(s). The fouling generally comes from polymers and gums accumulating in the exchangers or reactor and subsequently coking or further polymerizing. Exposure of the feed to oxygen or CO/CO2 (even at ppm levels) and the presence of polymer initiators in the feed lead to the gum/polymer formation. The gums/polymers deposit wherever the last feed vaporizes. It is critical that you ensure that all feed is vaporized before it enters the charge heater to avoid leaving deposits in the tubes. Such deposits have resulted in several tube failures over the years. The impact is worse with cracked stocks, which more readily make deposits and will have more heavy sulfur species that can more easily lead to sulfidic corrosion.
The cracked feeds also bring in contaminants, like silicon or arsenic, which have to be managed with catalyst choices. In a unit designed for straight-run feed only, the total catalyst volume often limits the amount of space available for the contaminant traps and hence limits possible run-length before slippage of contaminants occurs. Generally, you can run some cracked stock in a unit designed for straight-run feeds, but you have to be prepared and plan for the impacts.
CHRIS CLAESEN (Nalco Champion Energy Services)
The fouling tendency in the pre-heat and reactor can increase significantly due to polymerization of the olefins and diolefins. Chemical programs with antipolymerants, dispersants, and reactor bed cleaners can help control polymerization and delta P. Nitrogen and sulfur content will mainly depend on the type of feeds that are processed by the cracking units. Silicon can be a contaminant when coker gasoline is processed due to contamination with antifoam breakdown products. In such a case, the coker antifoam program should be carefully controlled and Si contamination minimized.
GREG SAVAGE (Nalco Champion Energy Services)
The instability or reactivity of an HDS feedstock will relate directly to its fouling potential. For refinery streams, the processing history of a stream plays a significant part in defining its instability. Streams produced in thermal cracking processes, such as cokers and visbreakers, will contain high levels of olefins, diolefins, and other fouling precursors that make these stream the most unstable in the refinery. Streams produced in the catalytic cracking units will contain moderate levels of olefinic species. Straight-run streams, those coming directly from the crude unit, will not naturally contain olefins and are Therefore, usually very stable. (If unstable streams are reprocessed in the crude charge, the straight-run streams may contain some reactive material.) The presence of intermediate storage must also be considered, as dissolved oxygen contamination will greatly increase the fouling potential of a normally stable feedstock.
The propagation of the olefin polymerization involves the reaction of an olefin with a radical, which results in the formation of another radical. This reaction path continues and results in molecular enlargement of the polymeric foulant. Eventually, the molecule will become too large to remain buoyant in the process stream and will precipitate out onto the equipment surfaces. These reactions are accelerated with the higher temperatures found in the pre-heat exchangers of an HDS.
Carbonyls are often initially formed by the presence of free oxygen contamination in a process stream. Further reaction of the carbonyls can lead to a variety of polymeric species that can contribute to fouling. As more oxygen is incorporated into a polymer, it will eventually become insoluble in the hydrocarbon stream and precipitate onto equipment surfaces.
Metals (particularly iron) are almost always present in significant quantities in most refinery streams. The role of metals in the physical and chemical fouling mechanisms must be considered when considering fouling deposit and stream characterizations. Metals catalyze decomposition of peroxides to reactive radicals, which promotes polymerization (gum forming) reactions.
Higher sulfur, nitrogen, and olefin content in cracked naphtha and mid-distillate streams have resulted in the need for increased HDS severity, which accelerates polymerization reactions.
For limiting polymeric gums formation, it must be known whether the polymerization is the result of oxidation reactions, metals or unstable feedstocks, or some combination of these mechanisms.
For oxidation reactions, the most effective corrective measure is to reduce or eliminate the free oxygen that is contaminating the feedstock. The application of antioxidants is also applied to prevent oxidation reactions.
Metals contamination is addressed first by determining and then eliminating the source of the metal foulants. Metal deactivators and dispersants can be applied to limit the adverse effects of metal in HDS feedstocks.
For highly reactive streams, antipolymerants can be applied to limit the gums-forming potential of these unstable feedstocks, and dispersants can be used to prevent the agglomeration of foulant particles, keeping them in a finely divided state.