Question 23: How do you operate mid-distillate selective recycle hydrocracking units to generate more naphtha while minimizing fuel gas/liquefied petroleum gas without catalyst replacement?
JEFFREY MUELLER (Marathon Petroleum Company)
Maintaining flexibility to make gasoline versus ULSD (ultra-low sulfur diesel) is very important to most refiners today due to the volatile nature of the market. Understanding the economic goals of your process unit and building in the flexibility through your catalyst selection process is the best way to set up your process for flexibility in the coming run. This question is very specific in nature but could probably be simplified to: How do I maximize naphtha production in my unit while minimizing light ends production? Simplistically, you need to increase conversion. KBC assisted in development of this answer by running some kinetic models on a recycle hydrocracking unit. Figure 1 shows that increasing conversion will result in a higher naphtha yield.
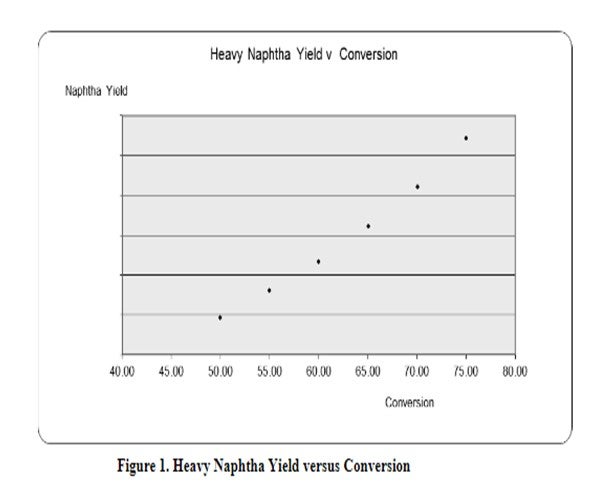
How to increase conversion is key. From a process variable perspective, there are three actions that will help maximize your naphtha yield and minimize light-end production from over-cracking:
*Maximizing your recycle rate,
*Minimizing your peak reactor temperatures, and
*Reduce your UCO (unconverted oil)/distillate cut point.
Maximizing the recycle rate will decrease your per-pass conversion. You will be able to achieve the same naphtha yield at lower WABT, thereby allowing the process to be more selective to naphtha versus light-end production. A combination of maximizing recycle rate and optimizing WABT will allow you to increase overall conversion without overcracking.
High reactor temperatures directly increase reactor rate. The higher the temperatures, the more “overcracking” of naphtha into gas/LPG that will occur, and the more undesirable light ends which will be produced. Therefore, it is imperative to minimize peak temperatures in your hydrocracking reactors. This goal can be achieved by balancing your reaction across all of your catalyst beds and using quench to control your axial temperatures. In addition, you should ensure radial temperature spread is tight, if possible. Maldistribution across a reactor bed, either from underperforming distribution trays or uneven catalyst loading, can cause high radial peak temperatures and overcracking.
Reducing your UCO cut point results in recycling more distillate material through the hydrocracker reactors which will increase naphtha yield. As you can see from Figure 2, there is a direct relationship between the naphtha yield and the amount of diesel that is dropped into the reactor feed (either by dropping lighter material into the recycle or, if economical, dropping diesel down into your hydrocracker feed at the crude unit).
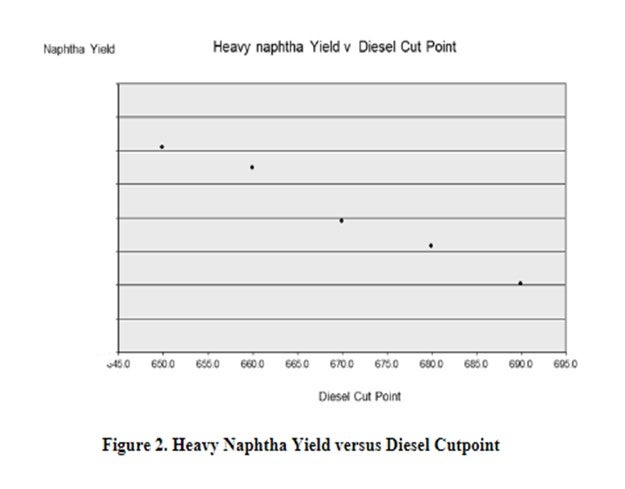
Finally, do not forget to turn on all fractionation knobs on the back end of the fractionator. Increasing naphtha endpoint by adjusting fractionation is a way to produce more naphtha, assuming that the higher endpoint material can be managed by the reformer or blender.
DAVID VANNAUKER (Haldor Topsoe, Inc.)
In general, mid-distillate (middle distillate) [J+D (jet plus distillate)] selective hydrocracking catalysts contain lower-activity (content and/or acidity) zeolite and/or specialty zeolite as compared to naphtha-selective hydrocracking catalysts. Depending on the specific types and quantity of hydrocracking catalysts, the specific operating changes can vary considerably. Several techniques are recommended to modify these changes.
*Increase pretreat conversion (i.e., aromatic saturation) to produce easier-to-crack molecules.
*Raise HDC WABT (weighted average bed) to increase naphtha make; and/or
*Increase recycles to reduce crack per pass (CPP) to increase selectivity of naphtha over fuel gas/LPG (liquefied petroleum gas) make.
*Adjust the hydrocracking beds to be in a descending temperature profile to minimize secondary and tertiary hydrocracking reactions.
*Lower the endpoint of the distillate product (reduce diesel/UCO cutpoint).
JOE FLORES (Criterion Catalysts & Technologies/Zeolyst)
In a hydrocracker unit with recycle, reducing the recycle product cutpoint IBP (initial boiling point) of bottoms or FBP (final boiling point) of final product before bottoms will increase the conversion per pass (at same overall conversion), which will result in more naphtha.
Higher recycle rates operated with the same conversion level increase middle distillate selectivity. Lowering recycle rates, operated with similar conversion, increase the naphtha production. Up to a certain conversion, the amount of gas make can be controlled based on changes in recycle rates: higher recycle rates reduce WABT and catalyst severity and make fewer light ends and less gas.
In general, when there is an increase in naphtha, there will be an increase in gas make. The volume makes from the fractionator bottoms and middle distillates converting to light ends offset the naphtha volume lost into making additional gas make until a certain optimum conversion is achieved. Hence, additional gas make depends on the targeted conversion, and the conversion distribution between the first stage and the second stage (for two-stage units), as well as the type of catalyst and feeds.
Refiners should also consider recycling/feeding some diesel to make more naphtha as long as they are not above a conversion point where they would make more gas and the net C5+ would decrease.