Question 22: What considerations in caustic scrubber operation or design are available to mitigate caustic carryover and corrosion? Discuss differences between various services.
MELDRUM (Phillips 66)
Let’s quickly review some concepts for good caustic scrubbing, caustic strength (not just pH, but also the weight percent sodium hydroxide), contacting of the treat stream with the caustic using pre-mixing or submerged inlets, packing within the scrubber, and caustic circulation to keep the caustic uniform in concentration. Poor circulation can cause local pockets of neutralized materials and limit removal of the heat of reaction.
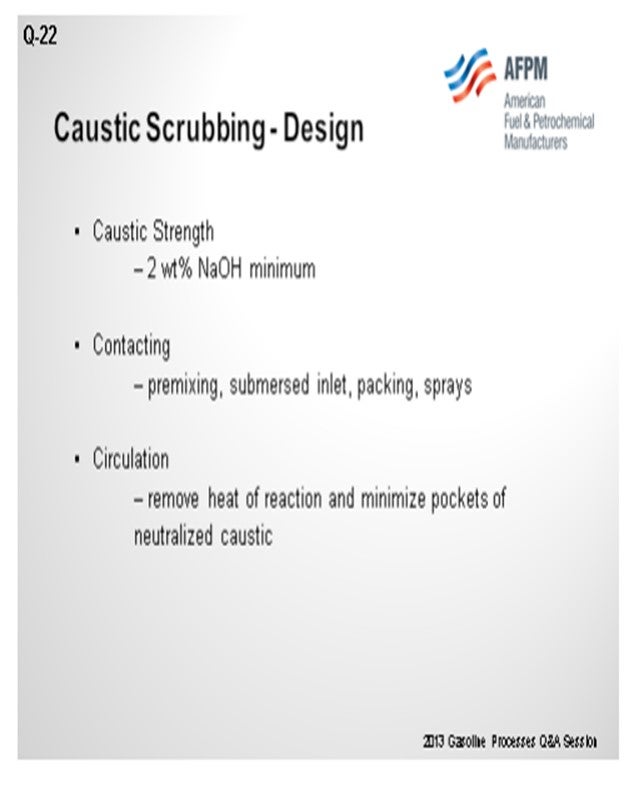
Carryover from the caustic can lead to fouling and salt deposits in the downstream areas and some caustic cracking, and in severe cases of high temperature downstream, some caustic corrosion. Beware of non-post-weld heat-treated equipment that can exceed temperature limits when steamed out. Mitigation of carryover includes minimizing of the vapor rate. It is not uncommon, as a unit increases capacity over time, that sufficient attention is not given to the additional rates occurring through the scrubber. So, review that system to make sure you have proper cross-section in the scrubber. Control foaming by keeping the caustic slightly warmer than the inlet stream to avoid hydrocarbon condensation that could contribute to the foaming. Ensure that there is a sufficient disengaging section at the top of the scrubber, maybe even considering the use of some coalescing material on the outlet of the scrubber. Finally, using a sand filter or water-washing downstream of the scrubber will help minimize caustic carryover. In the Answer Book, I have a few more details on specific applications pertaining to the reformer, the isomerization unit, and Merox™ treatment.
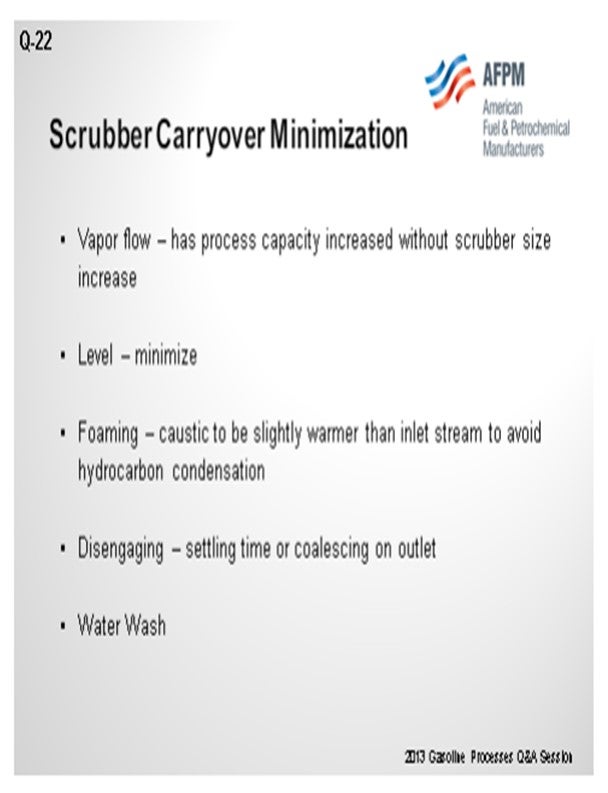
GROPP (GE Water & Process Technologies)
In addition to what Craig said, caustic towers are common in the ethylene industry and typically more problematic than those found in the refinery due to the reactive nature of the ethylene-formed polymers and foulants. GE has significant experience in helping to prevent foaming, fouling, and corrosion in those units. While we do not have a lot of experience with caustic scrubbers specifically associated with isomerization units, the Best Practices we have learned certainly apply to all caustic scrubbers. Craig mentioned some of these including controlling the vapor velocity to avoid liquid entrainment and foaming tendencies. Fouling in the tower can cause issues as well. Localized high velocities associated with fouling can cause foaming problems. Caustic management must be practiced religiously: strength, cleanliness, and recirculation rates. Corrosion can be an issue due to wet acid gas in various components of the system; so as Craig mentioned, corrosion needs to be controlled. Over the years, the application of defoamer additives, antifoulants, and caustic-resistant corrosion inhibitors have been helpful in mitigating some of these problems.
BULLEN (UOP LLC, A Honeywell Company)
UOP experience with the common cause of corrosion in caustic scrubbers in isomerization service is due to not changing out the caustic on time. Logistical issues, sampling liquids properly, issues with doing the analysis in the lab properly, and looking at free caustic versus percent spent all contribute to not changing the caustic in time. We also see corrosion in some of the units that have heaters for winter to maintain the caustic temperature warm. In those areas, sometimes the steam used is too hot or has some super-heat to it which causes corrosion due to overheating the caustic. Steam tracing can cause corrosion externally because it overheated the caustic at the tube wall.
Oversized gas inlet distributors tend to corrode due to back-filling with caustic that is trapped in the distributor pipe and then becomes highly acidic.
Some designs have a two-stage system where a water-scrubbing packed bed is arranged above the top of the caustic packing area to wash down any caustic entrainment. But generally, the idea of having downstream traps is a good for the off-gas system.
MUKESH PATEL (Reliance Industries Limited)
When you say ‘sand filter’ for this particular application, what is the design criteria that are followed?
MELDRUM (Phillips 66)
Sand filters typically are used in the Merox™ system but not as much in the isomerization scrubbing or the reforming system.
MUKESH PATEL (Reliance Industries Limited)
You said that sand filtering is considered for capturing caustic carryover. What are the design criteria that are considered?
MELDRUM (Phillips 66)
I do not have design basis available to me right now.
LUCAS BERGER (Design Criteria)
I can probably help you with that later. I do not have it off the top of my head, but I am sure I can find design basis for that kind of system.
ALLEN KAISER (Delek Refining, Ltd.)
The design basis would easily be inserted into the transcript that comes out next year.
BULLEN (UOP LLC, A Honeywell Company)
In my experience, the most important aspect of a sand filter is getting the right sand.
CRAIG MELDRUM (Phillips 66)
Caustic scrubbing is achieved with:
1. Proper caustic strength, not just pH but wt% NaOH (sodium hydroxide) greater than 2%,
2. Good contacting of the treat stream with the caustic (premixing, submersed inlet, packing and sprays), and
3. Good caustic circulation to keep the caustic uniform with no pockets of neutralized caustic and remove the heat of reaction.
Carryover of the caustic can lead to fouling from salt deposits, caustic cracking, and caustic corrosion in downstream equipment. Be aware of non-PWHT vessels exposed to caustic and later to heat from process conditions and/or steam out operation. General mitigation of carryover includes:
• Minimize the flux through the scrubber by verifying that the scrubber has sufficient cross-section area for the gas flow and asking if the unit capacity been expanded without expanding the scrubber.
• Minimize the scrubber level.
• Control foaming to ensure that the caustic is slightly warmer than the inlet stream to avoid hydrocarbon condensation and liquid buildup that can contribute to foaming.
• Use disengaging or coalescing material on the outlet of the scrubber.
• Use sand filtering and/or water-washing downstream of the scrubber. Some additional mitigation considerations for specific process units are:
1. SR Reformer Regeneration
• Minimize separator level.
• Control foaming (keep solids in control with caustic change-out).
2. CCR Reformer Vent Gas Scrubber and Isom Scrubbers
• Use and maintain a waterwash section.
• Control level with water addition to minimize caustic dehydration and salt precipitation as the dry off gas becomes saturated through the scrubber.
4. Merox™ Treatment • Use a water-wash sand filter.
RONALD GROPP (GE Water & Process Technologies)
Caustic towers are common in ethylene units and are typically more problematic than those in refineries due to the more active nature of the hydrocarbon to form polymers. GE has significant experience helping ethylene producers reduce foaming, fouling, and corrosion in these systems. While GE has limited experience treating caustic towers associated with isomerization units, we have learned the following general Best Practice rules in the petrochemical industry which should apply:
- Control vapor velocity to avoid liquid entrainment and foaming tendencies.
- Fouling in the tower can cause issues with scrubbing and lead to high local velocities that can increase foaming tendencies.
- Caustic management must be practiced (strength, hygiene, contaminants, etc.) to keep the system running well.
- Corrosion can be an issue due to wet acidic gas in various components of the process.
- Defoamer additives, antifoulants, and caustic resistant corrosion inhibitors, such as those offered by GE, can be applied and may help minimize foaming, fouling, and corrosion issues.