Question 22: Can you elaborate on the benefits, drawbacks, and trade-offs of liquid phase vs. gas phase catalyst activation in a hydrocracking unit? Is there an activity or yield difference of liquid phase or gas phase activation of 2nd stage catalyst in a 2-stage hydrocracking unit? Consider both catalyst formulation and operational factors (MPT, excursion risk, etc.)
JEFF CATON (Axens)
Activation (or sulfiding) of hydrotreating and hydrocracking catalysts can be done either ex-situ or in-situ. In both methods, the objective is to convert all the catalyst’s metal oxide sites to active metal sulfides (Refer to Figure 1 - Catalyst Sulfiding/Activation). A poor or insufficient activation will result in reduced catalyst activity and cycle length. This is applicable for nearly all hydrotreating and hydrocracking applications, including 1 and 2 stage hydrocrackers. Axens’ recommendations do not significantly differ when considering activation (or sulfiding) a hydrocracker 2nd stage over a hydrotreater or hydrocracker 1st stage.
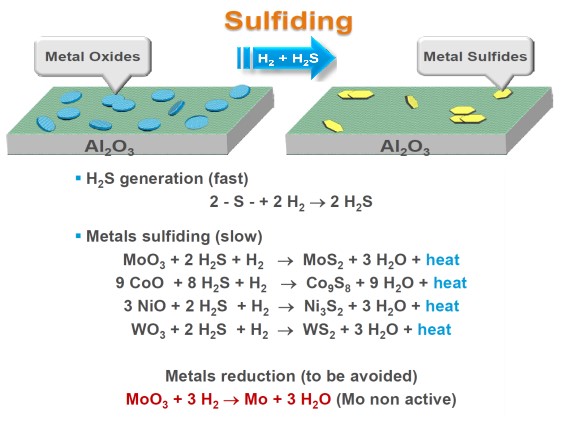
For ex-situ catalyst activation (commonly referred to as pre-activation), the catalyst is fully activated via conversion of metal oxides to active metal sulfides. Note, this is not the same as ex-situ pre-sulfiding, where the catalyst is more simply loaded with sulfur, but still requires an in-situ activation, or conversion of the metal oxide sites to active metal sulfides using the pre-loaded sulfur. Pre-activated catalyst is delivered to the site in drop-in, ready to use form. In addition to standard pre-activation, the catalyst can be additionally pre-treated to allow for immediate processing of cracked feedstock, and if applicable, can be pre-passivated in the case of hydrocracking catalysts. Additional treatment to allow for atmospheric loading of the catalyst is also available. The disadvantage to pre-activation of catalysts is relatively limited to the cost of pre-activation, however, this cost is usually offset by the decreased loss-of-production time realized through elimination of in-situ activation (sulfiding) steps, which can commonly take 24-36 hours to complete. Axens’ experience with the use of pre-activated catalysts has been exceptionally good, with most start-ups progressing quickly and smoothly followed by catalyst performing as expected.
In terms of in-situ catalyst activation (sulfiding), the sulfiding can be done in liquid phase or in gas phase. Further, the sulfiding can be done through injection of a sulfurous agent (e.g., DMDS, Sulfrzol, etc.) or via native feed/sour gas sulfiding, assuming a high enough sulfur content in the feed or sour gas. All these methods are possible, and when completed according to recommended guidelines and best industry practices, with the proper safety and emergency scenarios considered, the catalyst activity and catalyst cycle length has achieved the expectations.
Axens’ position is that liquid phase sulfiding is more controllable and robust, therefore less prone to unforeseen issues that might impact the overall catalyst activity and stability when compared with gas phase catalyst sulfiding. The primary benefit of liquid phase sulfiding is the controllability of delta temperature (dT) caused by the exothermic sulfiding reactions. Early in the in-situ sulfiding process, if the feed sulfur concentration is too high, the exotherm could result in a premature temperature increase creating a risk of coking or metal oxides reducing to the metal state. If this were to occur, this could substantially impact the catalyst activity and stability, ultimately leading to poor yields and/or a shortened cycle length. With liquid phase sulfiding, this risk is better managed as the liquid acts as a heat sink, thus dampening temperature spikes caused by the exothermic reactions. Similarly, Axens favors injection of a sulfiding agent versus native feed/sour gas due to the ability to better control the sulfur content going to the reactor through control of the sulfiding agent injection rate. If the dT is too high and excessive hot spots occur, it is relatively manageable to decrease the sulfiding injection rate to decrease dT. Conversely, with native feed/sour gas sulfiding, it is not as straightforward to monitor or control the amount of sulfur going to the reactor, so the dT is less manageable. Further, based on Axens’ experience, sulfiding in liquid phase with injection of a sulfiding agent has generally led to shorter duration of the sulfiding procedure.
A risk during in-situ sulfiding is the loss of sulfur to the reactor caused by loss of sulfiding agent injection. If there is a loss of sulfiding agent injection during the higher temperature step, there could be a resultant reduction of metal sulfides back to metal oxides and then further to the metal state. With liquid phase sulfiding, it is relatively more manageable to cool the reactor temperature to a lower temperature where the risk of reduction is minimized. With gas phase sulfiding, it is more difficult to decrease temperature of the reactor in a timely manner. As a precaution to counter the risk of loss of sulfiding agent injection, Axens recommends that the oil and/or makeup hydrogen used for sulfiding contain a minimal amount of sulfur and that the recycle gas amine scrubber be idled throughout the sulfiding process. These precautions will ensure continuous sulfur levels in the system thus minimizing the risk of catalyst reduction. Axens recommends that the recycle gas H2S content not fall below 1,000 vppm H2S when the reactor temperature is above 400 oF.
Like the ability to cooldown the reactor, it is also found to be more manageable to heat-up with liquid phase sulfiding. This can save time during the initial heat-up of the reactor to the first temperature hold and subsequently to the second temperature hold. Even when the refiner is limited to complete sulfiding in gas phase, Axens would recommend circulation of treated diesel throughout the unit to ensure wetting of the catalyst pores and to provide heat sink as discussed above.
It is important to note that in-situ liquid sulfiding should be completed with a 100% virgin (straight run) feedstock. After full completion of in-situ sulfiding, it is recommended to operate the unit with 100% straight run feedstock for a period of 3 days and then gradually introduce cracked feed stock. Further, the initial operating temperature should be maintained below the expected SOR temperature and then slowly increased as required to meet product specifications. Operating the unit with cracked feedstock within the first 3 days, increasing temperature too rapidly, and over treating may result in premature catalyst coking and resultant loss of activity and cycle length.
NEIL HOWARD (Chevron Lummus Global)
For current generation catalyst CLG has experienced comparable catalyst performance with either gas phase or liquid phase sulfiding procedures. There are some units that require gas-phase sulfiding, mostly because of the mechanical configuration – high MPT reactors, inadequate heat input, inadequate recycle compressors, etc. Chevron’s experience suggests that gas-phase sulfiding can be done safely and timely and without causing any yield differences, even in a second-stage reactor. We have observed that some older catalysts give slightly worse start-of-run performance under gas-phase sulfiding, but many of the most modern catalysts show little or no reduction in activity with gas-phase sulfiding.
Liquid phase vs. Gas phase startup
In general liquid phase sulfiding is preferred for reasons already stated above. Some of these liquid phase advantages include:
-
better heat sink during the sulfiding steps to manage temperature rise in the catalyst beds.
-
faster response to temperature increases or decreases in the event of a need to suspend sulfiding activities in the course of the startup.
-
faster heat-up to MPT on units where startup oil is introduced at low pressure under nitrogen.
-
no prolonged cool-down to feed-in temperature after high temperature sulfiding
Some of the concerns with heat release with gas phase sulfiding mentioned above can be mitigated by:
-
Maximizing recycle gas rate to improve distribution and carry heat from the catalyst beds during sulfiding
-
Limiting initial DMDS injection to maintain H2S in the recycle gas to no higher than 0.5 vol%. The reactor temperature rise should be limited to 50 degF
-
DMDS injection can be increased to 1 vol% H2S in recycled gas after the initial temperature wave passes through the reactor. But again, dT should be limited to 50 degF maximum.
-
sulfiding can be conducted at low pressure to avoid delays due to heating up to MPT and going to full pressure. 400 psia minimum H2 partial pressure is recommended, or as high as allowed by MPT.
MAUREEN BRICKER and JOHN KULACH (UOP)
This question requires some background on catalyst manufacturing and studies that we have performed utilizing both activation procedures on various hydrocracking catalyst types. As catalyst performance is being optimized to enhance yield and targeted hydrogen saturation so too are the methods employed for catalyst formulation and manufacture. Each step of the process is studied and optimized for the exploitation of the catalyst performance. Optimization techniques in manufacture and the activation of the catalyst in-situ are linked to catalyst performance. While the gas phase activation tends to maximize the metal sulfide uptake there is a clear advantage with liquid sulfiding pertaining to maximizing the yield and in many cases the activity of the catalyst system. During liquid phase sulfiding, there is some modest coke formation even at mild liquid sulfiding conditions. The type of coke formation occurring during the activation phase likely prepares the catalyst better for initial design feed by preventing initial over activity and higher rates of coke formation during early stages of the cycle. It could also attenuate the most acidic sites on the catalyst which would deactivate immediately in process feeds.
Liquid sulfiding procedures may be more difficult to enact in older units where the minimum pressurization temperature (MPT) may be higher than the potential catalyst reduction temperature in hydrogen atmosphere. Since liquid phase sulfiding is performed under hydrogen atmosphere, there is concern that heating the catalyst under hydrogen to achieve minimum pressurization temperature (MPT) could result in catalyst reduction. This is not a concern with gas phase catalyst activation. UOP has developed procedures for those reactors requiring higher minimum pressurization temperatures to enable use of liquid phase catalyst activation.
Regarding temperature excursions: In gas phase and liquid phase sulfding, the sulfding reaction results in axial rise across each bed of catalyst. In liquid phase sulfding exotherms can be seen additionally from adsorption (wetting) and from cracking. Procedures must take these possibilities into account and provide avoidance or action to be taken.