Question 21: When operating with one or more catalyst coolers on a regenerator, what control philosophy do you employ (e.g., constant heat duty, constant regenerator temperature, etc.)? What are the advantages and disadvantages for each approach? How does operating in full- or partial-burn impact the control decision?
WALKER (UOP)
First of all, what is a catalyst cooler? A catalyst cooler is basically a vertical shell-and-tube heat exchanger attached to the regenerator. The cooler extracts high quality heat from the catalyst in the regenerator to produce high pressure steam. UOP’s design uses a bayonet-tubed catalyst cooler. Catalyst flows down through the shell. Fluidization air, which comes in, is used to control the duty, as well as the catalyst flow rate, which comes down and exits through a cooled catalyst standpipe. A slide valve (that is not shown) is installed in the cooled catalyst standpipe, which is used to control the flow rate of the catalyst, and the duty-fluidization air is also used to adjust the duty.
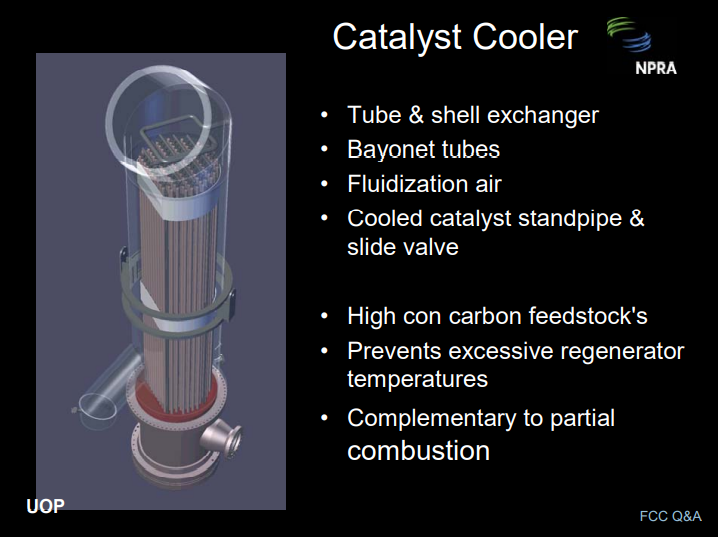
Increasing the coke yield for high concarbon feedstocks is necessary to increase the conversion, but we also need to prevent excessive regenerator temperatures. Installing a catalyst cooler is one way to increase the coke yield from the unit. There are two other primary ways to do this: reduce the feed temperature or reduce the CO2-to-CO ratio for units operating in partial-burn.
The question has two parts. The first part has to do with the control strategy. I have seen a number of strategies used. On two-stage regenerators, we typically control the second-stage temperature by adjusting the cooled catalyst slide valve position. Another common strategy is to manually set the cooled catalyst slide valve position and the fluidization airflow rate. This is similar to a fixed-duty strategy, but not exactly, because the regenerator temperature can also shift for other reasons, such as feed quality changes. This can change the MTD and the heat transfer.
The second part of the question has to do with how you pick the regenerator temperature or how you pick your cat cooler duty. Let’s say it is a constant heat-duty strategy. Like any other process variable, the heat duty of the catalyst cooler should be dictated by the refinery economics—for example, the LP model—and subject to constraints. The benefits of increasing the cat cooler duty are to reduce the regenerator temperature, increase the cat-to-oil ratio, and conversion. The lower regen temperature will reduce the catalyst consumption rate and will reduce the dry gas yield. The downside is that it will increase the coke yield, reducing the liquid product yields, but at increased conversion.
The coke is converted to steam in the catalyst cooler, and so it may impact the refinery steam balance. Also, more air is required when the coke yield increases. If the regen temperature is quite high—for example, 1375°F—your catalyst costs will rise dramatically compared to an operation at 1325°F, especially if you have resid feed causing high metals on the e-cat. Thus, there is a favorable regenerator temperature-operating window that can be achieved by using a cat cooler for control. But as typical with FCC units, there is a balance between the process variables used to optimize the unit.
WARDINSKY (ConocoPhillips)
The most common approach for full-burn cat cooler operations we have experience with is to allow the heat removal duty be an operating variable at a cat circulation limit and/or an air blower limit. Setting the cat cooler duty at some established minimum provides a more consistent steam generation rate to the plant’s steam system. This may be advantageous for units relying on steam to power rotating equipment or for plants that are short on high pressure steam. In our experience, most partial-burn units would operate using the same philosophy. Again, you are going to want to run up against a catalyst circulation limit to increase conversion.
Keep in mind that the use of a cat cooler is going to result in increased coke combustion in order to satisfy the heat balance; and thus, you are going to consume feedstock that could otherwise be converted to product.
THOMPSON (Chevron) We have four units that operate with cat coolers. They are either on the single-stage regenerators or the full-burn stage of a two-stage regenerator. We do not have any experience using a cat cooler on a partial-combustion unit.
Cat coolers are operated to minimize the regenerator bed temperature to a limit, which is usually either air supply or cat circulation. That optimization is an advanced control application that we have implemented on those units. We only use straight-duty control if we reach a cooler or steam system limit. The benefits for minimizing regenerator temperature include maximizing cat circulation, minimizing dry gas production, minimizing swings during feed changes, and, of course, reduction of cat deactivation.
PHILLIP NICCUM (KBR)
For a complete combustion operation, it is usually pretty straight-forward for the operators. For instance, with a KBR Dense-Based Catalyst Cooler, you can control the regenerator bed temperature by adjusting the catalyst circulation rate using the TIC very carefully. But in a partial-burn unit, you have a couple of other options. One option would be to just base-load the cooler steam production and use the air rate to adjust the regenerator temperature, like some people are used to doing in a partial-burn operation. Another way to do it would be to actually control the heat removal to control the temperature and use your CO composition and the flue gas to figure out how much air rate you need to put in the regenerator.
REZA SADEGHBEIGI (RMS Engineering)
I have to share with you this sad story. I was in a unit about a month ago. They run resid and they have a cat cooler, so you would think that they should use the cat cooler to minimize the bed temperature and all the good stuff that we just mentioned. Well, they cannot use it because their minimum bed temperature that they need to hold is 1360°F. Why? Because if they go below 1360°F, then the afterburn takes off and they have to add promoter. And when they add a promoter, NOx takes off. So a lot of times, when we shove more feed through this type of a unit, we like to have a nice low bed temperature. But if your regenerator is not designed properly, you do not have a good air and spent catalyst distribution or enough residence time in the regenerator, so the cat cooler does not do anything for you. It is just sitting there. So when you go through that, you really need to look at the total picture: Where am I on my regenerator in terms of keeping the bed temperature down and at a reasonable number?
WALKER (UOP)
The air distribution and coke distribution are key. You have to have those in place in order to drive the temperature down.
WARDINSKY (ConocoPhillips)
You want to consider where that return air from the cat cooler is coming into the regenerator because that can lead to CO excursions. And if that air is not being distributed in an area, you can have problems with afterburn.