Question 20: Several refiners are considering continuous operation of the combustion air heater to maintain a minimum regenerator temperature when processing light, severely hydrotreated feedstocks. What control systems, design features, and other general precautions should be considered?
HOWELL (Holly Refining)
As I previously mentioned, Holly is constructing mild hydrocrackers at both of their refineries. Of obvious concern to Operations and Engineering is where the FCC heat elements will settle out. Since we do not yet have experience operating the FCC on the severely hydrotreated feeds, when we saw this question, our immediate thought was, “My, that is creative and perhaps we ought to consider that.” We do have some experience with our TCC unit at Woods Cross. There are still a number of individuals who remember running that. We did have a combustion air preheater that we continuously ran for that process. However before we would consider this, we would obviously have to address reliability and safety issues of that combustion air preheater to make sure that the safety shutdown systems or safety interlock systems were correctly designed and installed. We also need to have an assurance of reliability for that combustion air preheater and for the controls on that, which were also a little bit of problem on our TCC unit.
HEATER (BASF Catalysts) Design of the air distributor and nozzles must be checked for continuous operation at higher temperatures. This will result in higher nozzle velocities due to actual acfm of air flow. For this reason, as well as for smoothing out of the heat balance, an automatic temperature control scheme is highly recommended. A better option is to increase the e-cat activity with higher ppb additions and/or higher activity with fresh catalysts.
This chart shows data from our model: air in the temperature versus the regenerator temperature. You can see about a 400°F increase in air temperature gives you about 30°F increase in regenerator temperature.
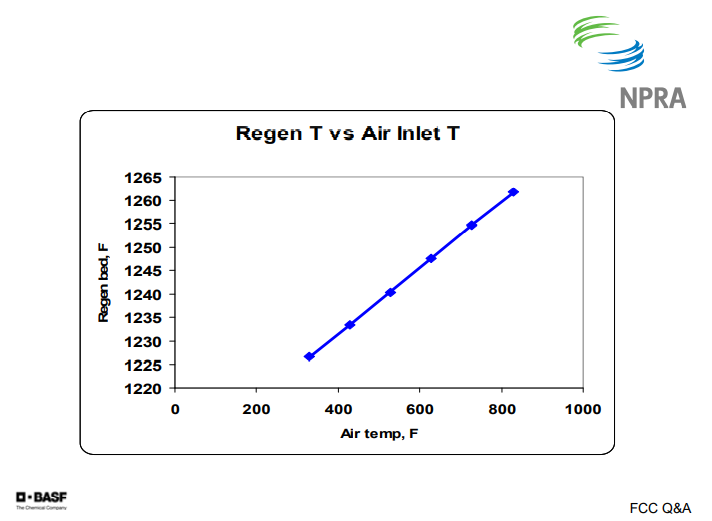
This next chart shows regenerator temperature versus e-cat activity. In this case, about six numbers of activity gives you about 35°F of regenerator temperature. So for our customers with severely hydrotreated feeds, we typically recommend a quite high e-cat activity level.
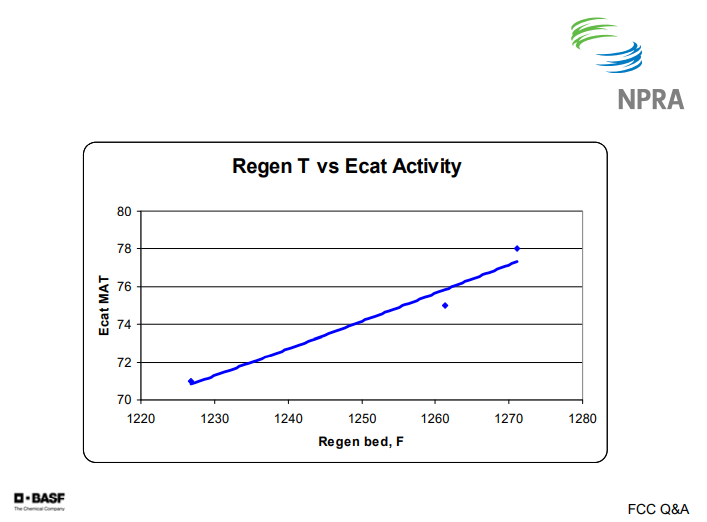
WARDINSKY (ConocoPhillips)
Two of our FCCs that are processing severely heated feedstocks have operated their preheaters for extended periods. On these units, we implemented calculations in the DCS system to monitor the air distributor nozzle exit velocities. With a 1000°F air temperature, the nozzle exit velocities approached 300 fps, which obviously can lead to catalyst attrition and potential air distributor damage. Igniting air preheaters is always a challenge, as is keeping the burner tips from plugging the scale. Several steps can be taken to ensure that the air preheaters are available during a run, including increasing air preheater inspection and cleaning scope during the turnaround, installing a strainer in the fuel gas line to prevent scale from plugging nozzle tips, and implementing state-of-the-air ignition and flame monitoring systems.
I will say that this was an issue we were looking at for these two units. We have since modified the catalyst. Basically, we took out the matrix component and it is just pretty much all zeolite. Those units are now running with pretty reasonable regen dense bed temperatures. So, we have been able to turn off the air heaters.
PHILLIP NICCUM (KBR)
One of the things to bear in mind with regard to the safety of the air heater is that temperature and flame monitors only go so far. Many of you, I am sure, have seen cases where if you have a fuel that may want to be liquid, such as an LPG or even an LCO. And if your vaporizer is not working properly, these materials can run down the line in a liquid state and burn downstream of your TIs. If some of it burned downstream of your TIs, you could find your air distributor destroyed.