Question 18: Vacuum Gas Oil (VGO) Hydrotreaters are being pushed to process heavier feeds while maximizing Fluidized Catalytic Cracking Unit (FCCU) performance while meeting Tier III gasoline specifications. How are you balancing increased severity and cycle length? What considerations do you give to feed quality and upstream unit operations?
JEFF CATON (Axens)
The FCC unit has long been the workhorse in the refinery to achieve relatively low-cost conversion of heavy crude components (VGO, HCGO and some atmospheric residue) into gasoline, butenes for high-octane alkylate production, propylene and LCO diesel blend components (Refer to Figure 1 - FCC Pretreatment Primary Objectives). The benefits of FCC feed pretreatment or VGO hydrotreating (CFHT) are well known; improved FCC performance and yields, decreased FCC product sulfur (with the potential to produce ultra-low sulfur gasoline), increased volume swell through aromatics saturation, and decreased FCC SOx and NOx emissions. When considering the importance of environmental compliance, crude slate flexibility, and optimizing product yields, the CFHT performance and reliability plays a tremendous role in the overall profitability of the refinery.
Figure 1 - FCC Pretreatment Primary Objectives
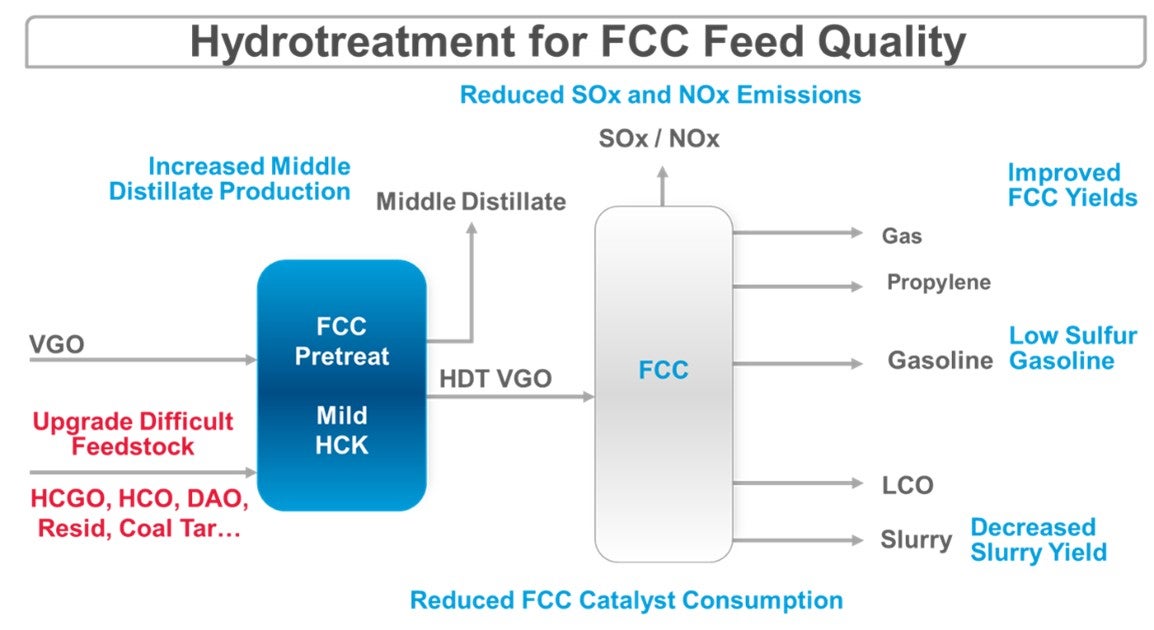
With increased sweet-sour spreads, the onset of Tier 3 gasoline regulations, and strong gasoline export demand, there has been a resulted decrease in CFHT feed quality primarily via increases in deasphalted oil (DAO), heavy coker gasoil (HCGO), and higher sulfur feedstocks coming to the CFHT. These feedstocks contain significant amounts of hydrogen-deficient compounds, refractive sulfur and nitrogen species, and metals, which need to be hydrotreated by the CFHT before being fed to the FCC. If not properly treated in the CFHT, the FCC performance, FCC yields, and FCC gasoline sulfur will suffer. To treat properly, requires a careful selection of the CFHT catalytic system to consider the potential for higher metals (nickel, vanadium, arsenic, silicon) and asphaltenes, along with the higher fouling propensity of these aromatic-rich feeds. In addition, a high activity and high stability active catalyst will be required to achieve the desired HDS, HDN, and HDA levels while maximizing cycle length. Even with a carefully selected catalytic system, the CFHT will likely have to be run at a higher operational severity, thus yielding a shortened CFHT cycle length. It is not uncommon that the CFHT cycle length cannot be stretched to coincide with the FCC turnaround interval, thus becoming necessary to have a CFHT catalyst changeout mid-FCC turnaround cycle. The refiner will need to consider possible scenarios for mid-FCC turnaround cycle CFHT full catalyst changeouts. Alternatively, it may be possible to span the FCC turnaround cycle with one or multiple CFHT catalyst skims, including replacement of top bed grading, activity grading, and demetallization catalyst (Refer to Figure 2 - Skim of Top Bed Grading/Activity Grading/Demet).
Figure 2 - Skim of Top Bed Grading/Activity Grading/Demet
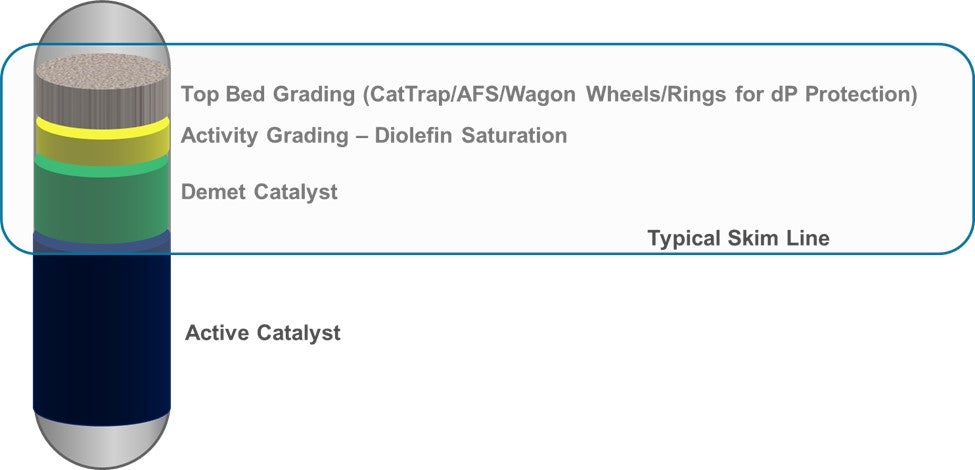
For refiners with a CFHT and FCC gasoline post-treatment unit, there is a possibility to gain a distinct advantage by optimizing the balance between CFHT and post-treatment severity to maximize cycle lengths and FCC yields while minimizing pool octane loss. In addition, a refiner should consider if it is economically optimal to run the CFHT in maximum HDA mode (higher temperature leading to over treating of sulfur) early in the cycle followed by operations in HDS mode later in the cycle. This will be highly dependent on the hydrogen supply affordability and availability and the CFHT catalytic system utilized. Optimization of the CFHT, FCC, and post-treatment units has been accomplished via rigorous simulation of incremental DAO lift-barrels, CFHT severity vs. cycle length, the corresponding FCC yields, and post-treatment octane loss. A deep understanding of the feedstocks and the chemical reactions involved in CFHT (kinetics, thermodynamics, contamination/poisoning) is of key importance. As many of these factors’ responses are non-linear, utilizing existing LP models is not always the solution, and dedicated optimization work has provided the most complete solution. Process technology licensors and catalyst suppliers may act as consultants in this optimization effort. Further, catalyst suppliers can provide regular unit and catalyst health monitoring support to enable better utilization of the full catalyst life. As illustrated in this example (Refer to Figure 3 - Monetizing Full Catalyst Life), knowing that there would be unused catalyst life remaining at the scheduled changeout time, the refiner was able to increase CFHT operating severity first decreasing product sulfur and subsequently increasing DAO feed rate and LVGO/HVGO feed endpoint in order to monetize the full catalyst life.
Figure 3 - Monetizing Full Catalyst Life
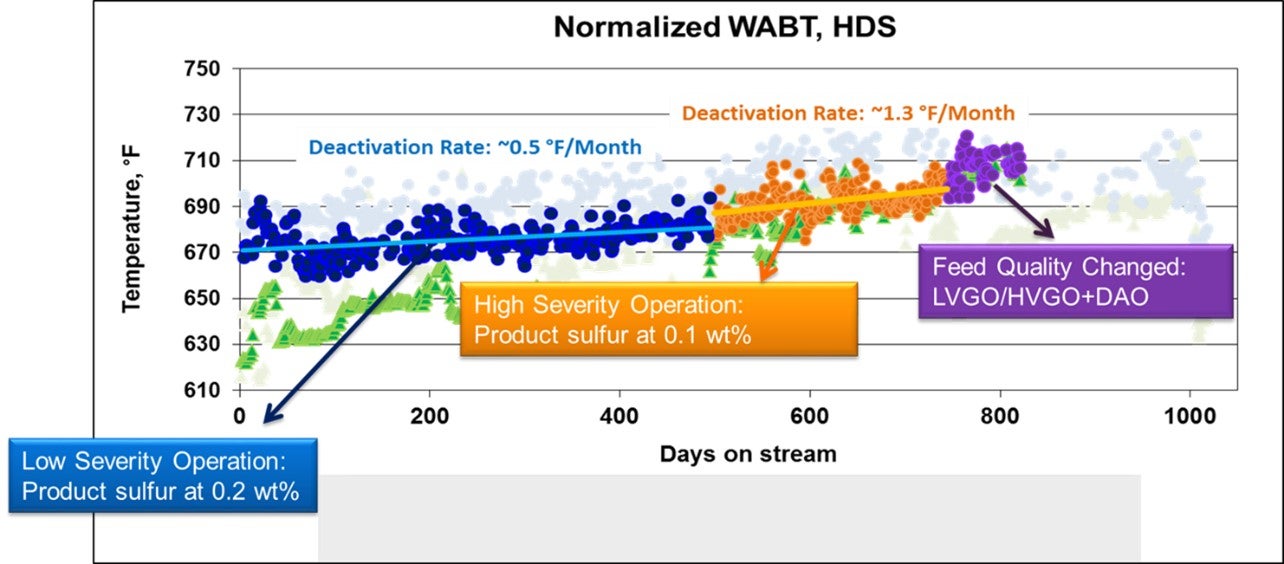
There may also be an opportunity to increase the severity of the CFHT, not only to meet sulfur targets and increase volume swell, but also to change the diesel-to-gasoline ratio by operating the CFHT in mild hydrocracking (MHC) mode (Refer to Figure 4 - Mild Hydrocracking in a CFHT). Given the pending IMO 2020 regulations, increasing diesel-to-gasoline ratio for increased production of low-sulfur diesel for (LSD), which could be used for blending bunker to low-sulfur fuel oil (LFSO), or production of ultra-low sulfur diesel (ULSD) may be highly profitable. These adjustments will require some modifications to the operating conditions, selection of the optimum catalytic system and distributor internals, increased hydrogen consumption and likely upgrades throughout the unit. One of the challenges of operating in the MHC mode is the ability to meet ULSD specifications throughout the MHC cycle. Moderate-pressure MHC units generally do not meet the required ULSD specifications, therefore post-treatment is typically required. Production of LSD may be a more economical target.
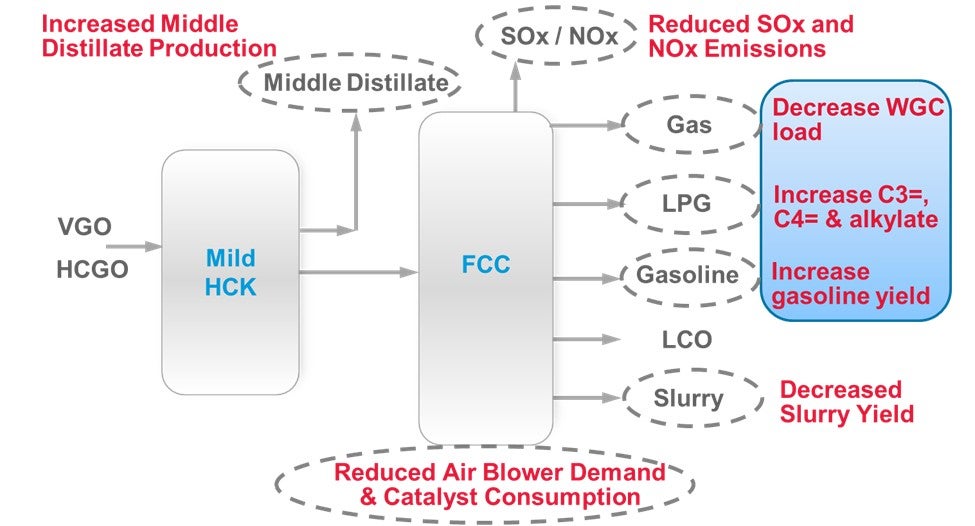
ROBERT STEINBERG (Motiva Enterprises)
If only a portion of the FCCU feed is hydrotreated it can be helpful to increase VGO hydrotreater charge rate to minimize high sulfur feeds to the FCCU. Reducing VGO hydrotreater severity may be required at higher charge rates, especially if you are trying to maintain a reasonable catalyst life. Lower severity at higher charge rates will generally mean more total pounds of sulfur is removed which minimizes total sulfur to the FCCU. Removing more total sulfur will also generally remove more nitrogen and saturate more aromatics which will increase FCCU conversion as well as making it easier to meet Tier III requirements.
For example, if a VGO hydrotreater was removing 93% of the feed sulfur and the charge rate was increased 20% with the same feed quality while the reactor temperature was adjusted to maintain run life, the desulfurization would be expected to be reduced to about 88%. This would remove about 14% more pounds of sulfur from the FCCU feed while maintaining CFH catalyst life.
The same concept would apply if the hydrotreater needed to process heavier feeds. If more difficult feeds were routed to the same hydrotreater without increasing charge rate or adjusting reactor temperature, the percent desulfurization would stay about the same. Even though the product sulfur would increase, more sulfur would be removed, and catalyst life would be about the same. If the some of the FCCU feed is hydrotreated and some goes to the FCCU without pretreatment, the heaviest highest sulfur feeds should be sent to the hydrotreater.
Balancing hydrotreater severity and cycle length is site specific. Ideally, the hydrotreater catalyst life should match the FCCU turnaround cycle to avoid having to shutdown the hydrotreater while the FCCU operates. This will often not be feasible at reasonable severities. But adjusting severity to do one or two cat changes during between turnarounds may be practical. When doing this it can be helpful to establish a temperature budget for the hydrotreater cycle and stick to that budget even if feed conditions change, provided enough sulfur is being removed to keep the FCCU naphtha sulfur on target. Product sulfur may fluctuate from day to day but will be reasonably constant and as low as reasonably practical throughout the cycle.
Alternatively, the CFH WABT can be maintained at the aromatic saturation limit to maximize aromatic saturation throughout the run. By not exceeding the temperature at which aromatic saturation starts to decrease, rapid catalyst aging is avoided. This will tend to give the maximum FCCU conversion throughout the cycle but FCCU feed sulfur will start low at SOR and gradually increase through the run as the CFH catalyst ages. This can be particularly attractive if the FCCU sulfur stays low enough to meet Tier III requirements without penalty throughout the run.
During hydrotreater catalyst changes it may be necessary to reduce the FCCU charge rate to still be able to make Tier III gasoline. Temperature budgets can be adjusted to have the hydrotreater catalyst changes occur at desired times such as when refinery throughput and FCCU charge rates are reduced for other reasons or during months when there is lower gasoline demand.
ARAVINDAN KANDASAMY (UOP)
Cycle length of typical Vacuum Gas Oil (VGO) Hydrotreating unit is shorter (ranging from one to two years) than that of typical FCC unit. Performance of FCC impacts the profitability of most refineries around the world. Therefore, refineries alter the Vacuum Gas Oil (VGO) Hydrotreating operation to match with FCC turnaround schedules and will have limited scope to compromise cycle length of VGO HT.
The metal contaminants and asphaltenes in the feed to a Vacuum Gas Oil (VGO) Hydrotreating Unit can limit the cycle length more than the product quality specification. Though the catalyst technology used in VGO hydrotreating units have improved continuously & considerably over the years, the refiners frequently balance the increased operating severity with some operational changes to maintain the required cycle length. Some of the operational changes widely used are.
-
Marginally reducing endpoint of VGO to keep metals and asphaltenes under control (or)
-
Increasing the use of deasphalting unit to increase endpoint of VGO HT feed.
-
Adding lead-lag mode of demetallization catalyst beds
-
Optimizing mix of Demet with Active hydrotreating catalysts
-
Increasing hydrogen purity across the Vacuum Gas Oil (VGO) Hydrotreating unit with Pressure Swing Adsorption (PSA) membrane technologies
-
Improved stacking of hydrotreating activity based on prevailing H2 partial pressure.
While the capacity of demetalization catalysts to trap more variety and quantity of metals has increased appreciably, handling asphaltenes and Conradson Carbon remains a challenge for a unit operating at a limited hydrogen partial pressure. Feeds derived from opportunistic crudes have more asphaltene and Conradson Carbon than typical crudes. Moreover, asphaltenes and Conradson Carbon from various sources differ in their impact. For example, asphaltenes and Conradson Carbon of from Heavy Coker Gas Oil (HCGO) is more difficult to handle than those from Heavy Vacuum Gas Oil (HVGO). So appropriately adjusting the cut points of individual feed components are essential to maintain overall feed quality. Refineries are rapidly adapting advanced feed characterization with data analytics to continuously optimize feed blend (crude source & unit source) to get the best out of Vacuum Gas Oil Hydrotreating units while achieving desired cycle length.
Overall refinery specific & cycle specific objectives and constraints must be considered to select the appropriate catalyst solution for VGO HT units.