Question 17: What is the importance of water content in reformer feed and recycle gas on the performance of the catalyst? What are your desired water concentrations in each of these streams?
SABITOV (Phillips 66)
Water levels in the reformer are an important variable impacting water/Cl balance and should be maintained in the reactors within optimum range. I am not going to talk about water impact on Cl on the catalyst because I would rather focus on water impact on the metal function of the catalyst. We consider water as a metal function attenuator. While on one hand, a little bit of water helps to take the edge off Pt-cracking activity; in general, an excessively wet unit would always be a bad performer, from a yields and stability standpoint. A little less water would be better than too much water.
Different types of units are getting their water in different ways. All of them, however, should be running with dry hydrotreated feed containing not more than 1 to 3 ppmw of H2O. The semi-regen unit will inject 3 to 5 ppmw of water on feed, resulting in about 15 to 25 ppmw of H2O in the recycle gas. Cyclic units and CCR units receive sufficient moisture from catalyst coming out of regeneration and do not inject water to the feed. Cyclic unit recycle gas moisture may vary within the range of 5 to 50 ppm, sometimes higher right after bringing reactor in service after regeneration. CCR units recycle gas moisture typically stays between 10 and 20 ppm.
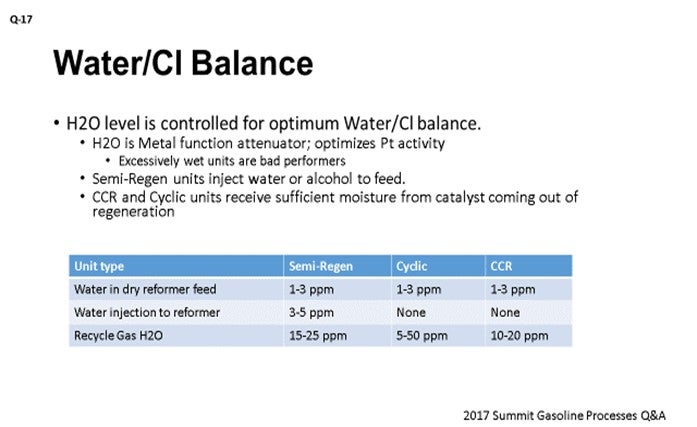
High water upsets are not uncommon in the industry, so I want to spend some time on the case where the unit is not getting enough water. P66 operates semi-regen reformer where we do not inject any moisture into the feed. So, ultimately, as cycle progresses after regeneration, it becomes very dry with recycle gas moisture falling below 5 ppm. To demonstrate the shift in metal function activity versus acid function activity in time, I am showing this LEP (local environmental plan) ratio trend. For those unfamiliar with that terminology, the LEP ratio is calculated as product moles of C1+C2 divided by product moles of C3+C4, which is reflecting balance between cracking on metal function over cracking on acid function. An increase in the LEP ratio will indicate an increase in metal function activity over acid function activity. The graph demonstrates that the LEP ratio starts not too far away from predictions for an ideal SOR catalyst when the system still has reasonable levels of moisture after regeneration. As the system dries out, the LEP ratio increases, evidencing an increase in metal function activity over acid function activity. At some point, as catalyst builds up the coke impacting catalyst metal function activity, the LEP ratio trend turns around and starts falling; however, it remains above the SOR catalyst prediction.
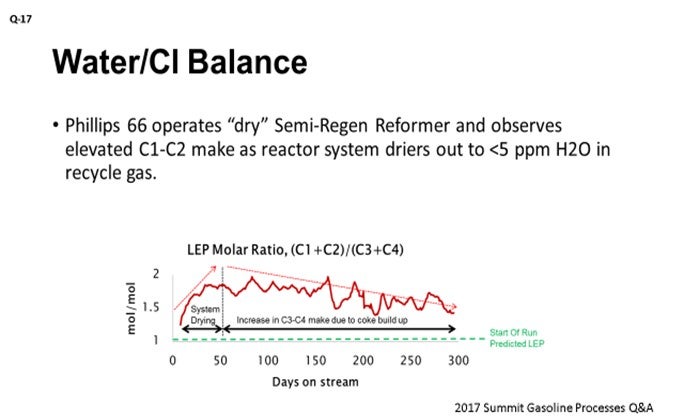
GEOFFREY DUBIN (Axens North America, Inc.)
Managing the water content in the reactive environment is critical for the overall performance of the reformer unit and catalyst. The content of water (H2O) must be controlled to allow for a sufficient quantity of hydroxyl [AlOH (aluminum hydroxide)] sites while simultaneously controlling the hydrogen chloride (HCl) levels to have the right balance of H2O/HCl to set the catalyst HCl content (Al-Cl). The overall level of OH and Cl (chloride) sites determines the overall acidity level of the catalyst, which needs to be in balance with the metal activity to maximize catalyst performances. By maintaining the appropriate balance, yields of desired products (reformate, aromatics, and hydrogen) are maximized. Additionally, the optimization of the catalyst performance will extend catalyst life and minimize potential corrosion and fouling in equipment.
As the water content of the reactive environment is the combination of the water content in the hydrotreated feed and the unit recycle gas, the measurement and follow-up of each is necessary for the overall health of the unit. For most unit operations (both feed qualities and product octane targets), a target concentration of 20 ± 5 parts per million by volume (ppmv) H2O in the recycle gas is desired. For more paraffinic feeds at higher octane targets, a slightly lower recycle gas H2O content can improve yields.
For reformer feed, the moisture content can depend on the quality of stripping in the upstream hydrotreater; but often, the reformer feed H2O content is in the 3 to 4 ppmw range. Typical rules of thumb say that a 1 ppmw increase in reformer feed H2O content will increase the H2O content of the recycle gas by 2 to 3 ppmv. The need to further increase the water content can depend on the type of reformer in operation. With cyclic and moving-bed-type reformers, the frequent regeneration of the catalyst generally introduces enough moisture into the system to maintain the recycle gas water levels at the targeted levels. Should a cyclic or moving-bed reformer operate in a non-continuous, infrequent regeneration operation, a reformer feed water injection may be required to maintain the proper acidity level on the catalyst. For fixed-bed reformers, water injections to maintain the targeted recycle gas moisture level is common.
VIKAS SANKALIA (Honeywell UOP)
CCR Platforming™ Units:
For the CCR Platforming unit, Honeywell UOP seeks to minimize the water content in the reformer feed as low as possible. Due to continuous catalyst regeneration, an equilibrium moisture level will be established between the catalyst circulation loop and the recycle gas loop. Since the moisture level is already established, there is no need for extra moisture in the platforming feed affecting the moisture chloride balance in the CCR unit. The typical value of feed moisture for CCR unit is less than 2 ppmw due to upstream fractionation. The typical value of recycle gas moisture in CCR unit is 15 to 20 ppmv (parts per million by volume) and should not be greater than 30 ppmv.
Semi-Regen Platforming Unit:
Unlike CCR units, there is no continuous catalyst regeneration; and as a result, continuous water injection into the reformer feed is required to maintain the proper water/chloride balance on the catalyst. The water injection varies based on catalyst type, but a typical value of water injection is 4 ppmw (assuming 1 ppmw feed water coming from upstream unit). Typical values of the recycle gas moisture for a semi-regen unit are in the range of 10 to 20 ppmv.
Quick increases in recycle gas moisture above acceptable ranges tend to act as a metal function poison, enhancing the acid function of the catalyst and facilitating the formation of coke. If the high moisture content continues for an extended period, chloride is stripped off the catalyst, which reduces the acid function. Under-chlorided catalyst will reduce the overall activity of the reactors. Some of the observable effects on the system are listed below:
-
Decreased hydrogen production,
-
Decreased recycle gas hydrogen purity,
-
Increased LPG make,
-
Lower C5+ yields,
-
Increased HCl in recycle gas,
-
Increased rate of coke production, and
-
Reduced reactor ∆Ts (delta Ts; temperature differentials).
For CCR units, increased coke make will affect the CCR burn zone operating parameters; and if not adjusted, it increases the likelihood of coke slipping to lower sections of the regeneration tower leading to catalyst and/or equipment damage. For fixed bed units, increased coking will lead to shorter cycle lengths. Regenerations of highly coked catalyst can also damage reactor internals of the semi-regen units.