Question 16: Do you plan to utilize a mercaptan removal unit in conjunction with a gasoline selective hydrotreater to meet Tier 3 gasoline sulfur requirements?
LAMBIE (KBC Advanced Technologies, Inc.)
To meet Tier 3 10 ppm sulfur in the gasoline pool, FCC naphtha will need to be treated to 10 to 35 ppm. The target FCC naphtha sulfur level is based on the sum of all the other sulfur species in the pool, as well as the percent of FCC naphtha in the pool, as indicated in the plot.
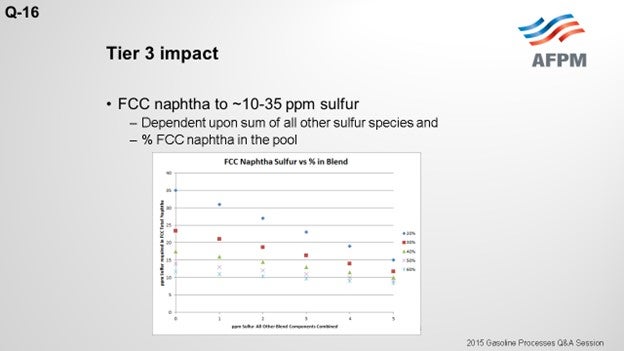
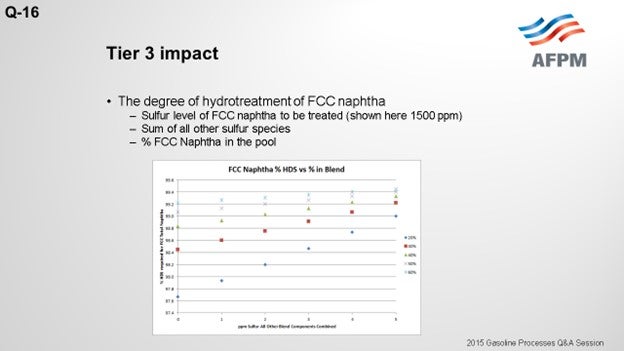
The degree of desulfurization of the naphtha is a function of the sulfur content of the FCC naphtha, the sum of all the other sulfur species, and the percent of FCC naphtha in the gasoline pool. The key takeaway from these two slides is that the lower the sulfur you can get all the other blend components, the less hydrotreatment the FCC naphtha will require and the octane loss you will experience. In any scenario, FCC light naphtha sulfur will need to be reduced. Adding a mercaptan removal unit can provide some octane preservation benefits due to reduced olefin saturation, but there are some risks.
The drawing on the next slide shows three potential applications for mercaptan removal units in conjunction with a gasoline selective hydrotreater. The first option splits the light and heavy naphtha and sends the light naphtha to the mercaptan extraction unit. The cutpoint of the light naphtha needs to be adjusted to avoid thiophene into the extraction unit feed because thiophenes are not extractable and will increase the extracted naphtha sulfur. The light naphtha will recover all of the C5 olefins and some of the C6 olefins, but some of the C6 olefins will end up in the heavy naphtha and be sent to the hydrotreating reactor
This first configuration option results in a much smaller unit overall, which is less costly. The mercaptans from the extraction unit are typically between 5 and 10 ppm, but the total sulfur content may be a little higher than that due to the disulfide re-entry loses. But as Daryl indicated, there are ways to minimize the re-entry loses with a naphtha wash, for example. The risk with this configuration is an unstable naphtha splitter operation or upstream operation that results in thiophenes in the light naphtha. In this scenario, the sulfur content of the light naphtha will increase, which will require a deeper desulfurization in the heavy naphtha hydrotreating; and hence, higher octane loss.
The second configuration option sweetens the full-range naphtha by converting the mercaptans to disulfides. The disulfides are then recovered in the bottom of the naphtha splitter, and the heavy naphtha is fed to the hydrotreater. Now the light naphtha from the naphtha splitter in this configuration has very low sulfur, 5 to maybe 10 ppm of mercaptans, and that should be consistent. The cutpoint in the tower, again, should be adjusted to avoid thiophenes in the light naphtha to keep the sulfur level low. This configuration is more costly, and a much larger unit is required because the full-range FCC naphtha is treated. The risk associated with this configuration is the potential for caustic carryover. Sodium could end up in the naphtha splitter, which could lead to tray fouling or condenser fouling issues. Also, sodium could potentially end up in the gasoline hydrotreater feed and poison the catalyst there.
The third configuration option is a sweetening unit on the backend of the hydrotreating unit. This option does not reduce the sulfur content, but it does allow you to meet the doctor sweet test by converting any mercaptans that have been recombined in the hydrotreating unit.
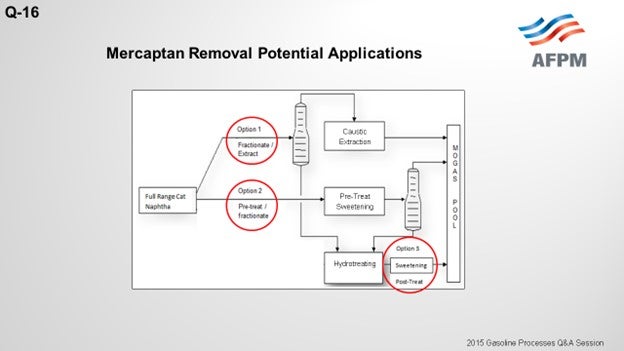
BURTON (Motiva Enterprises LLC)
We are not considering any of these options with our Tier 3 units. However, I do have a comment on the option of installing a sweetening unit downstream of a hydrotreater. This is a configuration that one of our units previously installed and operated. We did not sufficiently understand the interaction between the two units, which lead to a significant product quality event. Upsets in the upstream naphtha stabilizer in the hydrotreater adversely impacted the sweetening unit resulting in off-spec gasoline. Because of this bad experience, we are not interested in considering similar options in the future. However, we do know of other refineries that have successfully implemented similar configurations. The key to success is fully understanding the interactions between the two units and providing adequate safeguards to ensure that upstream upsets do not create bigger problems in the downstream unit.
FRY (Delek Refining Ltd)
I will just add that we do not use a mercaptan removal process. We use selective hydrogenation (SHU) with a splitter on our FCC gasoline. The SHU will shift all of the sulfurs down into a heavier sulfur, which we will then hydrotreat. We maintain very low octane loss by using that type of process.
SCOTT LAMBIE (KBC Advanced Technologies, Inc.)
To meet Tier 3 gasoline sulfur specifications of 10 ppmw (parts per million by weight), the full-range FCC naphtha (C5 at 430°F) will need to contain anywhere from 10 to 35 ppm sulfur. The exact sulfur content of the FCC naphtha product differs for each refinery but is basically a function of two factors: the percentage of FCC naphtha in the gasoline pool and the total ppm sulfur in the rest of the other blend components combined. The following graph depicts the total FCC naphtha sulfur requirement for varying percentages of the total pool and sulfur in all other components combined. Note: The graph assumes the refinery gasoline product meets 7 to 8 ppm specification for potential pipeline contamination margin.
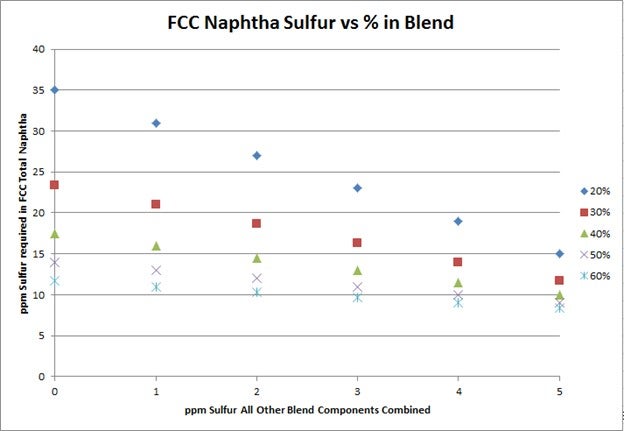
The degree of hydrotreatment of FCC naphtha is dependent upon several factors, including the sulfur content of the feed to be treated, relative amount of FCC naphtha in the pool, and combined sulfur of all other blend components.
Using a base FCC total naphtha sulfur level of 1500 ppmw, the follow plot depicts the degree of desulfurization required for varying percentages of the FCC total naphtha in the gasoline pool and sulfur in all other components combined.
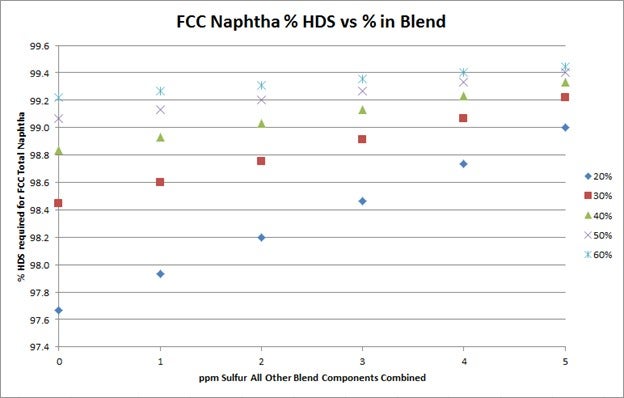
The plot above shows that the lower the sulfur of the blend components other than FCC naphtha, the lower the extent of hydrodesulfurization required for the FCC naphtha.
Treating the full-range naphtha stream to a low ppm sulfur level results in high octane loss, in large part, due to saturation of olefins. Many existing configurations for treating FCC naphtha split light and heavy naphtha and treat the streams to varying degrees to meet the desired product sulfur targets while attempting to minimize octane loss.
In the Tier 3 environment, light naphtha will require greater sulfur removal to meet the combined FCC naphtha total sulfur requirements. Heavy naphtha desulfurization rates will increase, as well, but only incrementally as desulfurization levels are already high to meet Tier 2 specifications and increased light naphtha desulfurization requirements.
Mercaptan removal units, in conjunction with gasoline selective hydrotreaters, in the Tier 3 environment, do very little to affect the overall desulfurization required in the heavy naphtha. For example, the impact of removing the mercaptans is estimated to reduce the heavy naphtha desulfurization requirements by approximately 0.1 to 0.5% depending on the sulfur level of the FCC full-range naphtha treated. The bigger incentive to adding a mercaptan removal unit in conjunction with a gasoline selective hydrotreater comes from reduced octane loss.
In Option 1 above, a naphtha splitter separates light naphtha from heavy naphtha. Light naphtha is sent to the mercaptan extraction unit while heavy naphtha is deeply desulfurized in the hydrotreating unit. Since only the light mercaptans are extractable, the cutpoint needs to be adjusted to prevent thiophenes from entering the extraction section as they are not extractable with caustic and would result in higher sulfur in the product. The resulting cutpoint recovers some of the C6 olefins in the heavy naphtha stream, and some octane loss of these components is unavoidable as they are treated in the hydrotreating unit.
The light naphtha mercaptans are extracted to less than 5 to 10 ppm, but the total sulfur can vary from 10 to 50 ppm depending on the operation of the unit and degree of disulfide oil re-entry losses to light naphtha. Extreme care must be taken to minimize re-entry losses of disulfides. Use of wash oils to minimize disulfide re-entry losses is a common practice. The sulfur level of the heavy naphtha product will need to be controlled to meet final sulfur levels. If very low FCC naphtha sulfur levels are required in the pool, due to the reasons mentioned above, the light naphtha total sulfur must be below 20 to 30 ppm in order for the heavy naphtha hydrotreating unit to be able to meet the final blend requirements. Naphtha splitter upsets resulting in high thiophenes to the extraction unit will be difficult to manage in the gasoline pool.
The benefit of the Option 1 configuration is reduced capital cost, due to the relatively low flow rate of light naphtha versus total naphtha, as well as some octane preservation.
In Option 2 above, the full-range naphtha is sweetened to reduce the mercaptan content. The boiling point of the disulfide oil produced is greater than light naphtha. As in Option 1, the cutpoint of the light naphtha is set to recover thiophenes to the naphtha splitter bottoms. The total sulfur of the heavy naphtha increases, but the degree and severity of the hydrotreating unit is essentially unaffected by the disulfide oil and more dependent on the removal of difficult sulfur species such as benzothiophene.
Option 2 results in a light naphtha stream that contains 5 to 10 ppm mercaptans and essentially no other sulfur species. Similar to Option 1, some of the C6 olefins are recovered to heavy naphtha and routed to the hydrotreating unit where they will lose some octane. The low-sulfur light naphtha allows for a higher heavy naphtha product sulfur. As a result, there is less of an octane loss across the hydrotreating unit with this configuration versus Option 1.
There are a few potential risks with the Option 2 configuration such as caustic carryover, disulfide decomposition, and possibly peroxide formation. Caustic carryover is not usually a problem; but if the unit experiences an upset, caustic can enter the fractionator. This could lead to fouling the trays and overhead condensers and possibly result in sodium going to the hydrotreating reactor, potentially poisoning the catalyst. At high temperatures in the naphtha splitter bottoms section, disulfides may decompose to form hydrogen sulfide that ends up in the overhead system and potentially corrodes the overhead condenser and equipment, if not designed to handle it. Regenerated caustic may contain dissolved oxygen that may react with olefins to produce peroxides. In the fractionator, the peroxides may react with olefins to form polymers. The polymers may foul up heat exchange surfaces such as the reboiler, condenser, and downstream hydrotreating unit.
The benefit of Option 2 is a consistent low-sulfur light naphtha product and slightly less overall octane loss than Option 1. The cost of the sweetening unit is higher than Option 1 because the entire FCC naphtha stream is being sweetened.
Option 3 post-treats the desulfurized heavy naphtha stream to remove mercaptans formed as a result of mercaptan recombination. While the tendency to form mercaptans is fairly low for heavy naphtha hydrotreating, the increase in C6 olefins as feed to the HDS unit increases the risk of mercaptan recombination reactions occurring. The mercaptans formed are not easily extracted, so the best way to convert the mercaptans and meet the doctor test is to sweeten them. Sweetening the mercaptans will not reduce the overall sulfur. If the overall sulfur is greater than 10 to 30 ppm, alternative means to reduce the overall product sulfur are required.
Option 3 is mainly an alternative to post-treating options and provides no octane benefit or desulfurization improvement. Its main function is to ensure that the product meets the doctor test. Mercaptan removal in this location will be hard to justify versus post-treating reactors.