Question 15: What is the Best Practice process for sampling, handling, and measuring research octane (RONC) and naphthene content in reformer feed and product? Are refiners considering online RONC and/or other property monitoring?
MELDRUM (Phillips 66)
If you have a poor octane result, the Best Practice is to blame the lab. Isn’t that what we do? The reality is that there are at least four key components of a sample system that all need some attention: sample conditioning, container contamination, sample degradation between collection and analysis, and the analysis method. The Best Practice for sample conditioning uses a fast loop to keep a fresh representative sample of the process at the sample point and minimize emissions that come from open-purging methods. As it pertains to reformer units, the container is typically a glass bottle, and standard bottle washing and air drying is adequate for contamination control.
Sample degradation can occur through the autoxidation of gasoline to peroxides when exposed to UV (ultraviolet) light, which can lower the octane number. One study found that samples exposed to sunlight in clear bottles for five hours resulted in a half to a full number drop in the octane number. Samples collected in amber bottles did not show a significant change in he octane number. Air in the free space from a half-filled bottle will also degrade the octane, though not as much as sunlight. To avoid the octane loss in a reformate sample, it is recommended to use amber bottles filled 80% full, capped with a clean cork or stopper, and held out of direct sunlight. They should also be analyzed in a timely manner.
Octane analysis is based on knock engine methods. Some sites may use laboratory infrared analysis to calibrate to the knock engine results; and in some cases, an online analysis might be done with the reformer unit. That is a valid technology; but for Phillips 66, it is not widely employed. That also directs attention back to Question 12 on blending from my previous comments on online analysis.
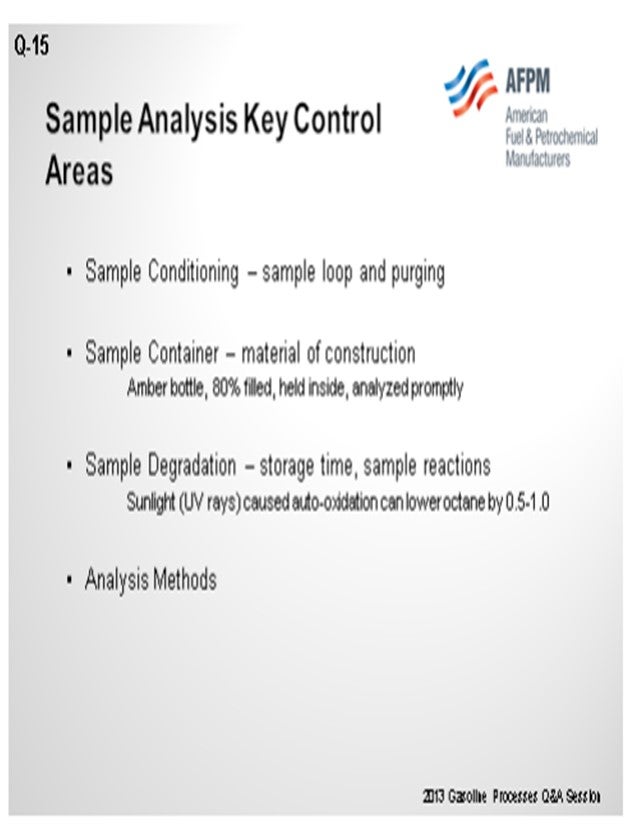
STREIT (KBC Advanced Technologies, Inc.)
I want to point out that NIR analysis online for reformer feed and product is fairly widespread now. It is good for measuring bulk properties. It correlates well for RON (research octane number), MON (motor octane number), aromatics, naphthenes, gravity, and some distillation points. In those cases, the same sample conditioning is required for that analyzer as basically for any other. You need good filtration. You need to get a hot fast loop on the sample point and make sure that the temperature and pressure are reasonable at the sample point. You might need to dry the material, but this is not usually an issue with reformer feed or reformate.
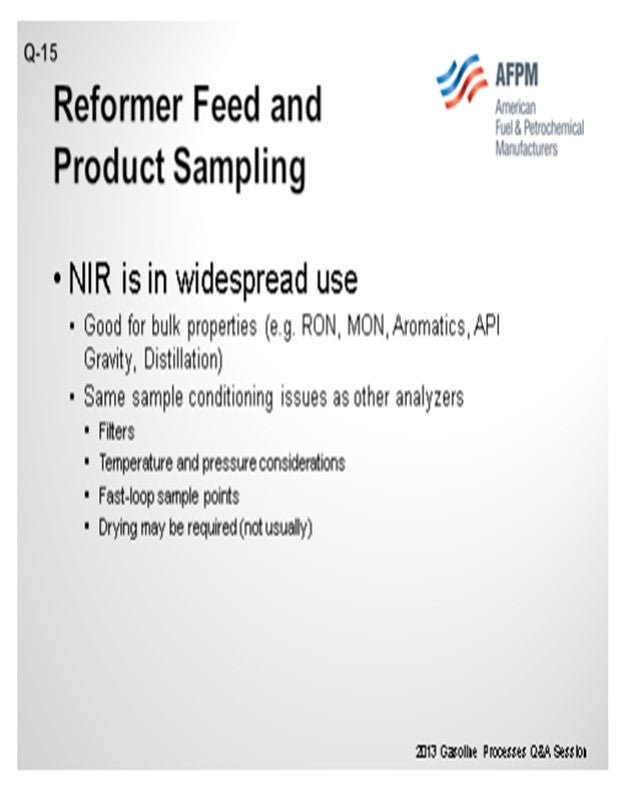
BULLEN (UOP LLC, A Honeywell Company)
One additional comment about the Best Practice for sampling: If you are not able to get to the samples quickly, refrigerating them allows them to remain stable longer. We have used that technique as a Best Practice. Related to online analyzers, it is not unusual for UOP to design online analyzers for our customers for product stream. We typically recommend a guided wave NIR analyzer. We recognize there are other analyzers available in the market. The costliest portion in these NIR analyzer systems is the calibration, which can take quite a while for these multi-component streams. The feedback from our customers has been generally positive. Once the calibration is done, people rely on them.
JAMES BROWN (Applied Instrument Technologies)
I would like to say that the NIR analyzers for this type of application are probably one of the earliest successful applications of the technology. We have had units in this application since the early 1990s. Although they are relatively expensive to install, they have relatively long lives. We had units that were operating for over 10 years with essentially the same instrumentation, so the payback over the scope of the instrument life is fairly good. Unlike blending where we seem to always change targets and continually have to update calibration models, once the calibration model is established for one of these systems, they are fairly stable and do not really require much updating with time. It is actually one of the easier applications to use.
CURTIS NEIL (Intertek Pilot Plant Services)
Does the panel have any experience with DHA (detailed hydrocarbon analysis)? I know that DHA is starting to become more prevalent. How does it correlate to the knock engines? And if you see octane values that you trust out of that correlation, is there any added benefit to, say, doing a DHA instead of a knock engine test? So I am curious if anyone on the panel trusts the detailed hydrocarbon analysis. Since that is a GC (gas chromatography) method compared to the results that you get from the knock engine, is there any correlation there that you feel that gives you any added value to possibly do that instead of running a knock engine?
MELDRUM (Phillips 66)
The DHA analysis has proven effective and does not require much sample volume like that of a knock engine. Pilot operations tend to use a DHA, and we do find them to be acceptable.
STREIT (KBC Advanced Technologies, Inc.)
With a lot of the NIR analyzers, the analysis time is fairly fast. You can manifold up multiple sample points to the same analyzer. We are talking about the payback that you mentioned before. Another way to mitigate some of the costs of the system is to have it analyze multiple streams.
CRAIG MELDRUM (Phillips 66)
Accurate sample analysis involves attention to four key areas:
• sample conditioning (such as purging of the sample station),
• container contamination,
• sample degradation (storage time, storage conditions, reaction with sample container material), and
• analysis methods.
Best Practices for sample conditioning involve fast loops to keep a fresh, representative sample at the sample point and to minimize emissions compared to open purging.
Container contamination is adequately handled with bottle washing and air drying.
Reformate sample degradation can occur.
• Auto-oxidation of gasoline to peroxides through exposure to sunlight (UV rays) will lower the sample octane number. One study found that samples exposed to sunlight in clear bottles for five hours resulted in 0.5 to 1.0 lower octane numbers. Samples in amber bottles did not see significant change in octane.
• Air in the free space from a half-filled bottle will degrade the octane, though not as much as sunlight.
• To avoid octane loss in a reformate sample, it is recommended to use amber bottles filled about 80%, closed with a cap with a clean cork or stopper. The bottles are held out of direct sunlight and analyzed in a timely manner.
• Antioxidant additives are only marginally effective in limiting peroxide formation through sunlight exposure.
Octane analysis is based on knock engine methods. Some sites may use IR analyzers calibrated to the knock engine results. Use of online GC analyzers for reformate octane is a valid technology, but one that is not widely used. See previous comments on Question 12 for blending.
PATRICK BULLEN (UOP LLC, A Honeywell Company)
A Best Practice for reformate sampling is to refrigerate the sample in a brown bottle to minimize the interactions of the chemical species in the sample.
It is not uncommon for refiners to request an online octane analyzer specification with a new CCR Platforming™ Process unit design. UOP recommends the Guided Wave NIR (near infrared spectroscopy) analyzer for product samples. There are other NIR analyzers available on the market. The costly portion of the NIR analyzer system is the time and labor to calibrate the analyzer for a given stream. Once they are calibrated, the customer feedback on performance has been positive.
ERIC STREIT (KBC Advanced Technologies, Inc.)
Near infrared spectroscopy (NIR) is in reasonably common operation use for analysis of gasoline for RON, MON, gravity, distillation, aromatics, and benzene. The analyzer is calibrated versus known standards for most properties. Octane analyses are calibrated against octane engine results. Repeatability for these analyzers is generally good. Because NIR can be used for a number of properties, it is normally the analyzer of choice.
Sample conditioning issues for NIR analyzers are the same as for any online analyzer (filter, temperature and pressure considerations, fast-loop sample point, etc.). Drying may be required, but this is not normally an issue for gasoline.