Question 14: What is industry experience of using tri-metal (platinum-rhenium with promoter) catalysts?
MELDRUM (Phillips 66)
Promoted or multi-metallic reformer catalysts have been a topic of research since at least the early 1970s. They have been tried commercially in various forms over the years, all with the objective of improving yields by suppressing the demetallization reactions. The current promoted catalysts have advanced the formulation of manufacturing techniques to new levels of performance. Recently, Phillips 66 has selected promoted catalysts for future reloads in at least three of our sites. The additional cost of the catalyst is justified when considering increased product yield and improved activity that allows a lower reactor temperature requirement, which both provide for a very quick payback on the additional catalyst cost.
The example shown on the slide indicates the additional yields – both in the C5+, as well as hydrogen – and some improved activity that might be expected with a promoted catalyst. When selecting the promoted catalyst, regeneration procedures should be reviewed with the catalyst vendor to ensure that maximum catalyst performance from regeneration to regeneration is achieved, particularly in the area of reduction and dryout steps.
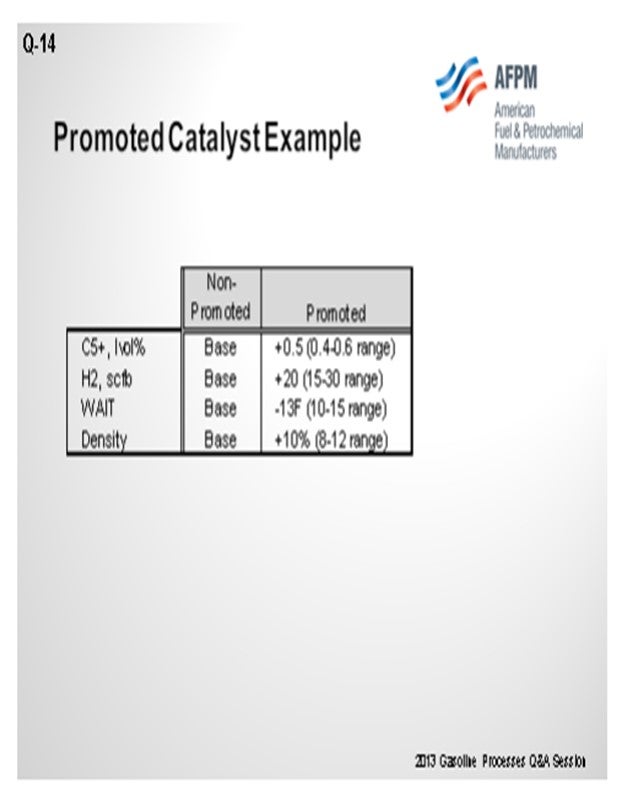
BULLEN (UOP LLC, A Honeywell Company)
We have two catalysts that we offer in the semi-regenerator market and also for cyclic reforming applications. One of them is the R-98 catalyst that was introduced in 2005 and which has over 50 installed applications. We have a new catalyst called R500 that has better activity and stability, and we have put it in 10 units. As Craig said, proper regeneration procedures are very important for any semi-regeneration unit, and maybe even more so for these tri-metallic systems, because of the issues related to dryout and reduction. It is important to get consistency with this procedure because you will lose the advantage of the tri-metallic system if you do not do the dryout and reduction correctly. Getting that repeatability is very important.
CRAIG MELDRUM (Phillips 66)
Regeneration procedures should be reviewed with the catalyst vendor to ensure maximum catalyst performance from regeneration to regeneration. For example, UOP R-72 was a promoted catalyst offered about 15 years ago and required a different reduction procedure than the non-promoted catalyst for hydrogen concentration, pressure, temperature, and dry-down schedule.
PATRICK BULLEN (UOP LLC, A Honeywell Company)
Trimetallic catalysts containing rhenium are typical for use in fixed-bed reforming applications, both semi-regenerative and cyclic reforming applications. In recent years, both additional metals and oxides have been added to platinum-rhenium reforming catalysts. Metal promoters have been added to increase selectivity and product yields. The additional metal partially suppresses platinum-rhenium activity, reducing metal-catalyzed hydrogenolysis that lowers selectivity.
Over the past decade, UOP successfully developed the proper catalyst base, formulations (including promoter type), and manufacturing techniques needed to generate catalysts that demonstrate excellent yield stability and regenerability. UOP’s R-98 catalyst was introduced in 2005 and has over 50 successful applications with many regeneration cycles, and our customers are benefiting from the higher yields. UOP recently introduced a new product, R-500, that shows even great activity and stability, with over 10 commercial applications. It is well suited for reforming units where even longer cycle lengths are desirable or where higher activity is needed to push more barrels. The gradual acceptance of promoted catalysts is analogous to that of the bimetallic catalysts having higher rhenium content that preceded them in this market.
Proper regeneration procedures are critical for the success of any semi-regeneration catalyst; and in particular, promoted formulations that have reduced metal activity. One Best Practice is to ensure proper dry-down, reduction, and sulfiding. Cyclic reforming applications are a little more demanding due to the regeneration environment (higher moisture and sulfur, for example), but new promoted formulations have been demonstrated in these applications as well.
SONI OYEKAN (Prafis Energy Solutions)
This question needs some more definition to elicit appropriate responses with respect to what is truly a “trimetallic” catalyst. My initial response is that my experiences in the use of “trimetallic” platinum-rhenium catalysts for fixed-bed cyclic regeneration reformer operations were good. The catalysts performed as projected by the catalyst and technology supplier for catalysts containing a third metal that was specifically added for modifying the acidic functionality of the catalysts.
Having written that, it is important to understand the type of catalysts commonly referred to as “trimetallic” catalysts. The term could cover Pt/Re (platinum/rhenium) catalysts with a third metal as a modifier for the alumina to moderate the acidic functionality of the catalysts or those in which the third metals are added to modify the hydrogenation functionality of the platinum or to moderate rhenium hydrocracking activity. In other trimetallic catalyst formulations, the third metal can work in conjunction with the rhenium as co-promoters for the platinum functionality.
The performance objective of the third metal is crucial in order to assess long-term performance and benefits of the third metal. Metals on catalytic reformer catalysts typically undergo varying degrees of reduction to different oxidation states at different temperatures and adequate metals redispersion are achieved at different oxidative conditions. Trimetallic catalysts’ expected performances and potential limitations should be well understood by oil refiners before acquiring them for use. Catalyst suppliers should provide test data to show multiple regenerations and adequate reactivations of the three metals, even if the other two metals are acting as co-promoters for the platinum. Another key factor is to ensure that optimal metals distributions are achieved during catalyst manufacture. There are other factors to consider that are beyond inclusion in this short response on trimetallic catalysts.
If the third metal has been added to moderate catalyst acidic functionality and reactivation of that third metal is not an important factor other than decoking, then the refiners’ challenges are lessened to some extent. It should be recalled, however, that the history of catalytic reforming is dotted with an oil refiner’s experiences with second metals that had been added to the platinum and which led to significant performance problems. The problems were related to inadequate metals activation, especially poor redispersion of the promoter metals, and these problems led to poor catalyst performance for subsequent cycles after the first cycle for fixed-bed catalytic reforming systems. Furthermore, in reforming catalyst development programs, the addition of metals to Pt/Re catalysts led to increased feed sulfur sensitivity challenges for the resultant trimetallic catalysts. Feed sulfur sensitivity and catalyst regeneration challenges should be studied sufficiently by the catalyst and technology supplier during that supplier’s catalyst development studies leading to the production of “trimetallic” catalysts.