Question 13: What are the typical causes for failing JFTOT and aviation turbine (AVTUR) specifications?
GROPP (GE Water & Process Technologies)
Assuming the jet fuel is on-spec with regard to other quality parameters, with the exception of perhaps copper strip corrosion and mercaptan sulfur, we have found that instability reaction precursors and catalysts are typically the root causes of JFTOT failures. These precursors include reactive hydrocarbons, especially olefins and aromatics, that might be found in coker distillates; sulfur compounds including H2S (hydrogen sulfide), mercaptans, and thiophenols; cyclical nitrogen compounds including indoles, pyrroles, and carbazoles; phenols; some acids, primarily naphthenic acids and light carboxylic acids; and then finally, catalysts in the form of transition metals, particularly copper and iron. Parts per billion (ppb) levels of copper are known to initiate and accelerate instability reactions that can cause jet fuel to fail the JFTOT. The sources are the crude oil itself, as well as refinery slops, heat exchanger leaks, and reactive blend components.
What are solutions to the problem? Source control is always the first line of defense, so careful attention to crude selection and blending, refinery slop management and minimization, and reactive blend component management are very important. Finally, good maintenance programs are essential to ensure that there are no leaks in exchangers that can cross-contaminate the product.
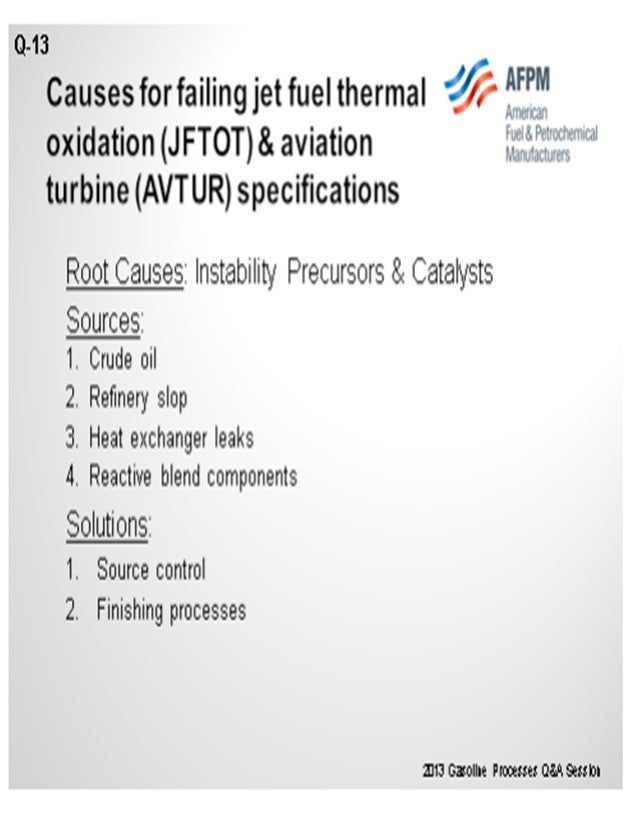
Even with good source control, trace contaminants in the fuel can cause problems. As a result, most of the refiners with whom we work utilize some kind of hydrotreating and/or caustic extraction and/or sweetening process in combination with a variety of waterwashes, drying equipment, and filtration steps. I cannot remember seeing two systems that contain exactly the same combination of equipment; so, from memory, I drew what might be a common or typical flow diagram. The equipment in my drawing includes a caustic extraction/sweetening unit, waterwash, water coalescer, salt dryer, and clay filter.
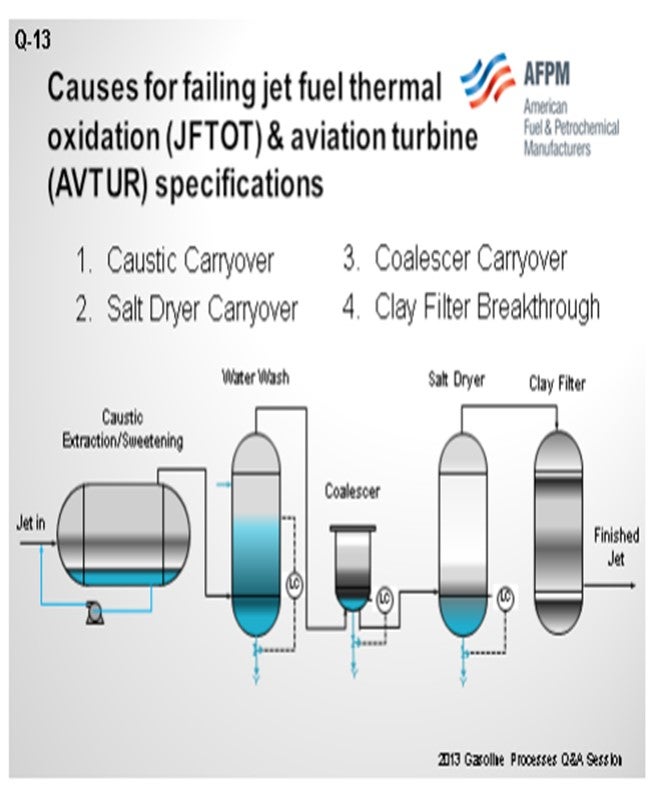
The number one cause of JFTOT failures that we see is caustic and contaminant carryover from the caustic extraction unit due to overspending the caustic and buildup of acid-suspended oils as measured in the UOP 743 test. When the level gets to about 30 to 40% acid-suspended oils, the caustic tends to emulsify with the jet fuel and carryover into the filtering and drying equipment. Sometimes contaminants end up in the jet fuel, and then the contaminated fuel fails the test. The key to preventing carryover is good caustic maintenance in the units to keep the suspended oils at a lower level: in the 30 to 40% spending range. That is our experience.
In addition, salt dryers can be a problem. There are two typical issues that we see. One is that the salt dryers are initially undersized, which results in carryover. The other is that the dryers have been in place and in service for many years, and throughput has increased compared to the initial design flow, resulting in carryover.
Other troubles associated with salt dryers include inlet fuel temperatures above design specifications, level control problems, and poor salt maintenance. I have seen a lot of salt dryers that do not have salt in them; and believe it or not, you must have salt in the vessels for them to work.
We have seen a few problems with the coalescer units. Typically, the concerns are associated with failed coalescer elements or level control.
Finally, the clay filter units can be problematic. The clay filter unit is designed to polish off the final trace contaminants in the fuel. Contaminants will build up in the filters and eventually break through if the clay is not replaced at the proper intervals. Even during normal operations, the caustic and clay must be replaced in proportion to the amount of contaminant loading in a jet fuel stream. Caustic unit, waterwash, coalescer, and salt dryer carryovers can also result in clay breakthrough and contamination.
Even with great source control and operation of the finishing processes, jet fuel sometimes still will not pass the JFTOT. In some of these cases, we have found approved antioxidants and metal deactivators to be effective in bringing the fuel back on-spec.
FRANKLIN WHEELER (Tesoro Corporation)
Going forward, the refining industry will have increased pressure to make jet and distillate versus gasoline as we biofuels have more market share. There are indications of that now throughout the U.S. The refining industry needs to be cognizant of operating windows in our fractionators, especially where you have hot drums on the overhead reflux system in your crude towers. They must be kept hot. Do not violate those operating windows at the expense of a jet production. Water can start to get reintroduced through the reflux system and cause corrosion. Several refiners began seeing the formation of copper corrosion after being overzealous to make increased jet yield. So, ensuring that operating windows are being met is a really critical part of making sure of your JFTOT quality stays on test. Also, the airlines do not like to use the metal deactivator; that is not the salvation. After a while, they will become concerned.
JESSY TRUCKO (UOP LLC, A Honeywell Company)
Keep in mind that if you have this recent change in any kind of corrosion inhibitors upstream, it can sometimes throw off your JFTOT. Mixing delta pressure across your mixing valves for your electrostatic precipitator or too high-percent spent caustic will increase emulsions; and once you start forming emulsions in that electrostatic precipitator, you will end up carrying caustic or naphthenic acids downstream. So if the unit is operating correctly, all of the hydrocarbon coming out of that electrostatic precipitator should look basically like water: totally clear. If you have any sodium naphthenates carrying over, you will have problems downstream.
CHRISTINE SHOROKEY (Monroe Energy, LLC)
We do not have a caustic treating unit. We send our jet directly to our coalescer, salt dryer, and clay filter. We are able to make JFTOT. I want to add to your PFD (process flow diagram) that perhaps a pre-filter like what we added in front of our coalescer. It stops the DP from accelerating through your filter elements to the coalescer. It quickly coalesces your water droplets. A salt dryer works, and then you do not have water carried over to the clay filter.
GROPP (GE Water & Process Technologies)
I also put quite a few details into my Answer Book response, although I am sure it is not complete. This is just a compilation of what I have seen over the years, so I appreciate your comments as well. If you are interested in the subject, there are details in the Answer Book response.
RONALD GROPP (GE Water & Process Technologies)
Assuming all other fuel parameters are apparently within specifications except Copper Corrosion (ASTM D130) and Mercaptan Sulfur (ASTM D3227), our experience indicates that instability reaction precursors and catalysts in the jet fuel are major root causes of JFTOT (ASTM D3241) specification failures. Instability precursors and catalysts include, but are not limited to:
1. Reactive olefins and some aromatics (precursors);
2. Sulfur compounds including H2S, thiols (mercaptans), and thiophenols (precursors);
3. Cyclical nitrogen compounds including pyrroles, indoles, and carbazoles (precursors);
4. Phenols (precursor);
5. Acids, primarily naphthenic and lighter carboxylic acids (precursors and catalysts); and,
6. Transition metals, especially copper and iron (catalysts).
In the refinery, typical sources of the precursors and catalysts include:
1. Crude oil charged to the crude unit,
2. Refinery slop oils that find their way into the crude charge or finished fuel tanks,
3. Heat exchanger leaks and associated product contamination, and
4. Reactive blend components such as coker distillates. Source control is the first line of defense against the troublesome precursors and catalysts. Focused attention on crude selection and blending, slop oil minimization and management, blend component optimization, and process equipment maintenance will minimize precursors and catalysts in the fuel. Beyond source control, instability precursors and catalysts are typically removed from jet fuel components and/or blended products through a variety of finishing processes in combinations specific to each refinery. Common processes include caustic extraction and/or sweetening, hydrotreating, and drying and filtering equipment including:
a. Strippers (dry and steam),
b. Water coalescers,
c. Salt dryers, and
d. Clay filters (polishing unit to remove trace precursors and metals).
The primary cause of JFTOT failure we see is instability precursor and catalyst breakthrough due to upsets or improper operation of caustic processes and associated drying and polishing equipment. In these cases, extensive reviews of the entire process from the distillation towers to the finished tanks are required to identify and correct problems. System reviews have uncovered the following problems (in order of frequency):
1. Caustic carryover from extraction and sweetening units due to overspent caustic as measured by the UOP 743 Acid Suspended Oils (ASO) test: The suspended oils generated in this test consist of the weakly acidic instability precursors mentioned earlier. The caustic in these units has a greater tendency to form emulsions and carryover with the fuel as the ASO measurements reach and exceed the 30 to 40% level.
2. Salt dryer carryover due to the following conditions: a. Inlet temperature is too high, exchangers are bypassed, or fin fans are closed in the summer. b. Vertical velocity in the dryer is too high [>~40 fph (feet per hour)]) due to operation above the original vessel design flow or the vessel being undersized in the first place. c. Calcium deposits cause channeling in the dryer. d. There is a faulty brine level controller. e. There is no salt in the vessel. f. Flooding occurs due to coalescer carryover.
3. Coalescer carryover due to waterwash, level control and/or coalescing element issues.
4. Clay filter breakthrough due to contaminate overload or carryover from upstream units (salt dryer, coalescer) and/or caustic unit. Despite good processing operations, some fuels fail the JFTOT specification. In a number of these cases, approved antioxidant and metal deactivators are effective in eliminating failures.
CHRIS STEVES (Norton Engineering)
The Jet Fuel Thermal Oxidation Test (JFTOT) can be adversely impacted by peroxides and trace metals, especially copper, iron, and zinc. When diagnosing persistent JFTOT problems, sources of contaminant metals (including possible impact from treatment chemicals that may transport these contaminants) must be explored so that facilities can be properly designed to ensure on-spec finished product.