Question 12: For units originally designed as naphtha selective HCUs, what are the considerations for shifting selectivity to distillate production?
LEICHTY (Chevron USA, Inc.)
There have been many inquiries into shifting naphtha hydrocrackers to distillate mode over the last couple of years. The optimal solution is dependent on feed qualities, hydrocracker configuration, distillation, and gas recovery hardware, as well as the value of volume expansion across the hydrocracker.
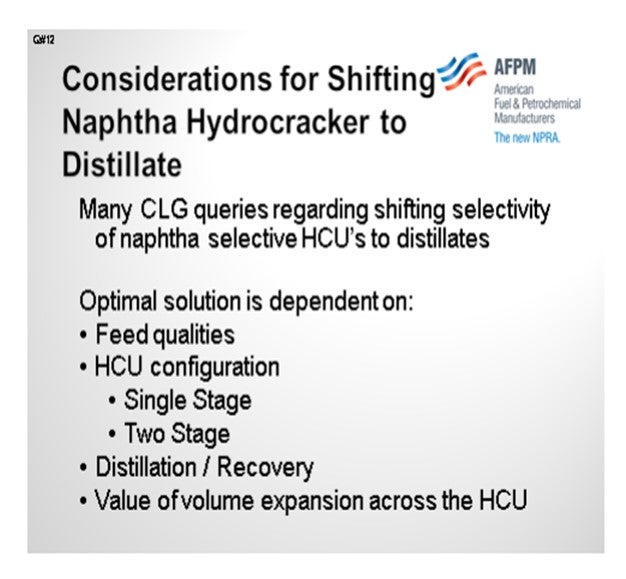
When it comes to feed qualities, higher distillate yield can be achieved by shifting away from paraffinic feeds to more naphthenic feeds because of the improved cold properties. Another way to enhance distillate yield in a hydrocracker is to feed stocks that are rich in diesel boiling range material, such as FCC LCO. LCO boils almost entirely in the distillate range and contains around 80% aromatics, which translates into high volume expansion when saturated with hydrogen. Minimizing feed overlap will also increase distillate yield against a cold flow property constraint since this material has higher amounts of n-paraffins than the material derived from cracking.
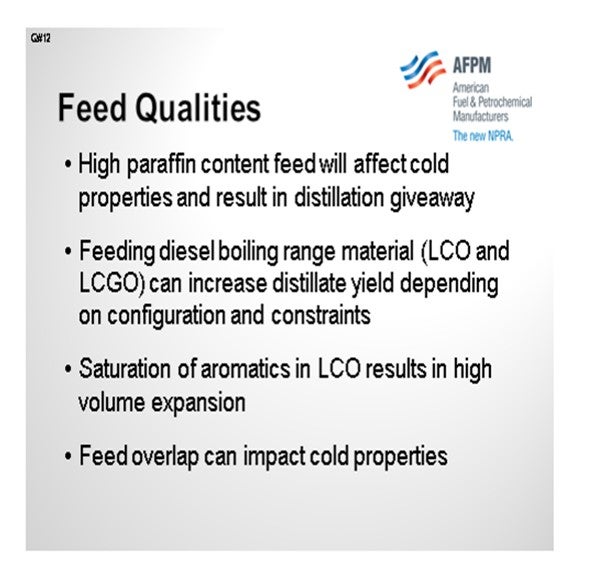
The strategy for maximizing distillate will also depend on hydrocracker configuration. For a single-stage hydrocracking unit, option one would be to maximize the more-difficult-toprocess cracked feeds already in the diesel boiling range and minimize hydrocracking to lighter products. Option two involves switching to a heavy VGO feed and then to a maximum distillate and cold flow property selective catalyst. In either case, it is best to configure the reactor temperature profiles to be flat or only moderately ascending in order to minimize over-cracking.
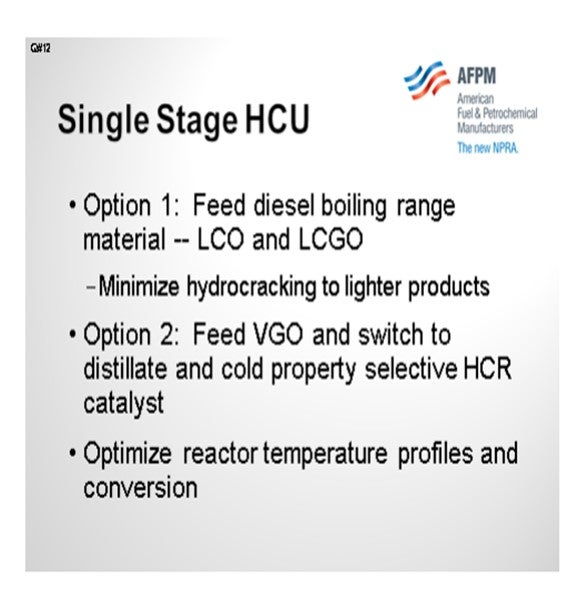
The next slide illustrates the second option and shows how switching from a more naphtha selective catalyst like ICR183 to ICR 185 in a single-stage hydrocracker not only gives you the cold property improvement shown in Question 8, but also results in improved distillate yield.
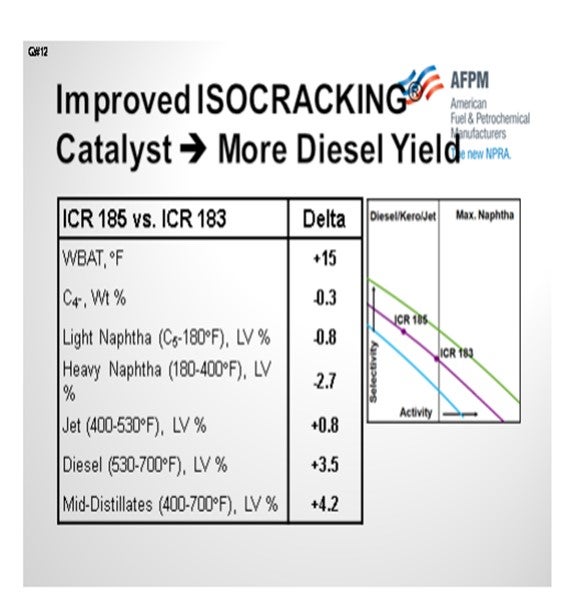
Now let’s look at a two-stage hydrocracker with intermediate distillation. The same strategy of increasing distillate yield by feeding cracked or otherwise-difficult-to-process diesel boiling range materials can have additional benefit. In addition to the high first-stage yield we observed with a single-stage unit, these materials also help a two-stage unit make more distillate because they can reduce the per-pass conversion required in the second-stage reactors. Lower per-pass conversion results in higher second-stage distillate selectivity because there is less potential for over-cracking. If the two-stage hydrocracker has tail-end distillation, flat second-stage temperature profiles, coupled with a distillate selective catalyst, provide the best opportunity to increase distillate yield.
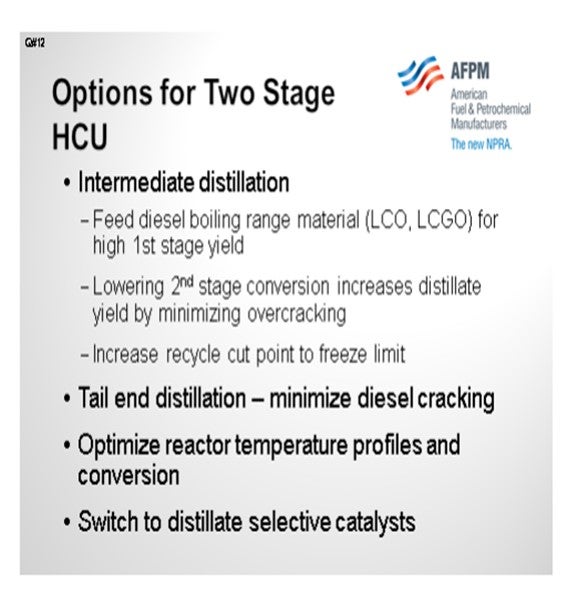
Whether the two-stage unit is intermediate distillation or tail-end distillation, there are some new improvements that can be made to the second-stage catalyst. The next slide shows the difference between two newer base-metal catalysts relative to the previous generation distillate selective catalyst: ICR 240. With ICR 250, you can choose to make more diesel at the expense of gasoline, or you can employ ICR 255 for a more jet-selective catalyst with a significant drop in start-of-run temperature.
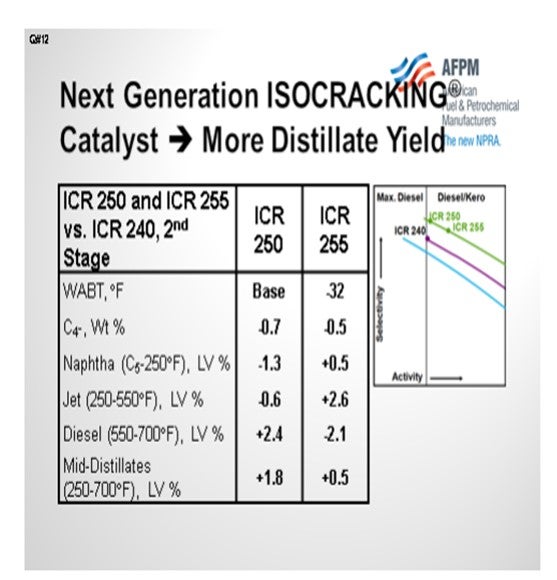
When it comes to distillation and recovery, the principles are the same as those we discussed for improving cold flow properties. Maximizing internal reflux prevents heavy tails from impacting cold properties, and good stripping of the bottom's product minimizes distillate lost to unconverted oil. On the front end of the distillation, dropping lighter product down to a distillate flash limit will provide some cold property carry and allow additional heavy molecules to be pulled, thereby maximizing the width of the cut. If the fractionator only has a jet draw, it may be possible to increase the recycle cutpoint of your jet draw, and then route it to diesel. Doing this would require changing to a diesel flash specification but may result in more overall distillate. Another option would be to add a separate diesel draw and side stripper to the hydrocracker main fractionator. This option could require upgraded metallurgy in the bottom system because the temperatures will go up. Alternatively, a vacuum column could be added to remove diesel from the unconverted oil.
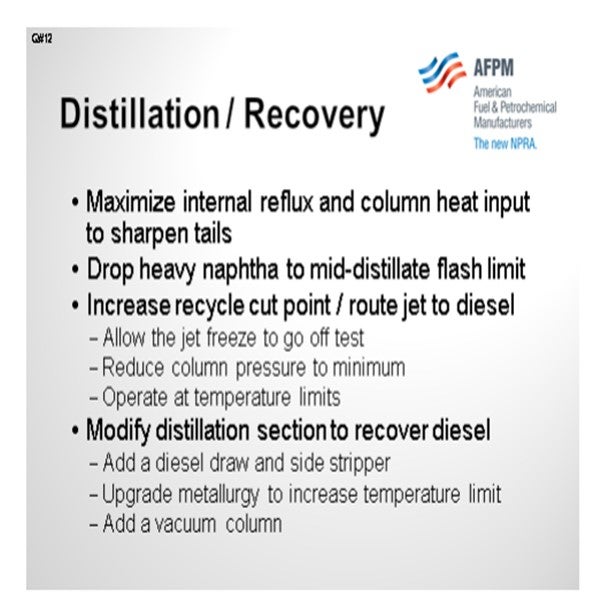
Last, but most important, to consider when switching from maximum naphtha mode to maximum distillate mode is the value of volume expansion. Shifting the hydrocracker to distillate mode will result in a loss of volume expansion. Since products are generally sold on a volume basis, the loss of volume can overwhelm the price difference between distillate and gasoline, especially if the hydrogen being added to the oil is derived from inexpensive natural gas, as is the case in North America.
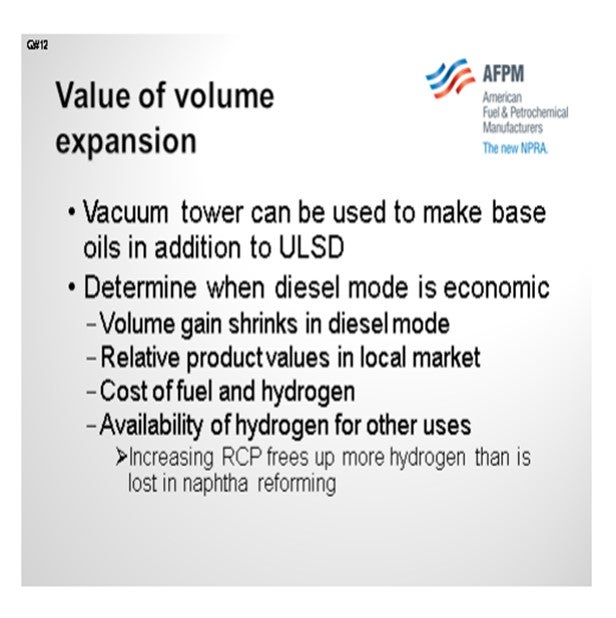
BODOLUS (CVR Energy)
Steve did a good job covering a lot of the issues and concerns. As he mentioned, the concerns are similar to those of Question 7, but they come at it from the other higher conversion end. We have a list of procedures to follow when trying to improve the distillate slate with diesel being over gasoline, but I think probably the biggest recommendation is to rationalize the changes in the naphtha production, the impact it has on the hydrogen balance at your refinery, and also how competitive it will be to switch to diesel, in terms of FCC economics.
CARLSON (Criterion Catalysts & Technologies)
You two covered it really well, so I will minimize my response. Most of the conversion capacity of the approximately 60 operating hydrocrackers in North America is geared to the gasoline market. Nevertheless, many still have the flexibility of switching from gasoline mode to distillate mode (by adjusting process operating parameters such as cracking conversion, liquid recycle rate, and product cut points) without requiring capital expense.
Just as a reminder, this topic is fully discussed in NPRA Paper AM-09-10, “Dieselization in North America: Flexible Solutions for Diesel Production” by Robert Karlin.
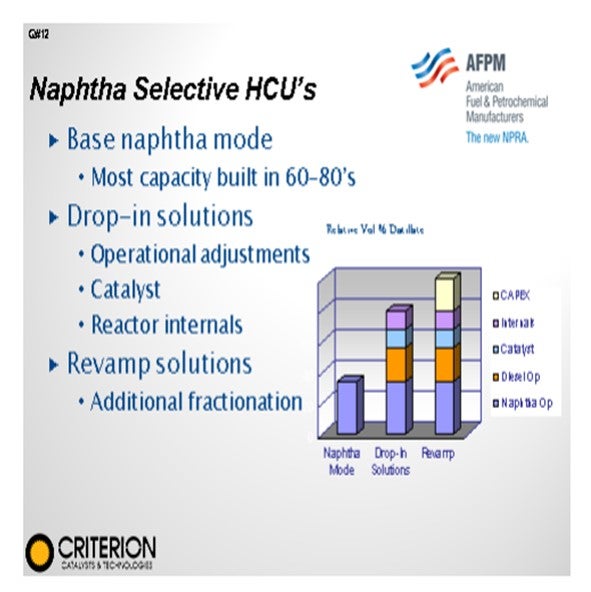
Operational adjustment changes: Shifting to a distillate mode operation is typically achieved by switching from a recycle operation to a once-through operation while lowering conversion, which increases diesel production. When reducing conversion to increase diesel yield, a lower overall conversion level may result in lower distillate quality due an increase in aromatics and resultant drop in API gravity.
A drop in product quality can be overcome through the use of a more distillate selective catalyst that will improve distillate quality via higher hydrogenation activity while improving distillate yields.
Lowering conversion also results in reduced hydrogen consumption. Increasing feed rate to utilize the available hydrogen can recover the losses in volume gain across the hydrocracker. Therefore, one primary modification to gasoline hydrocrackers for the improvement of distillate yield and throughput involves revamping the fractionation section to enable higher feed rates.
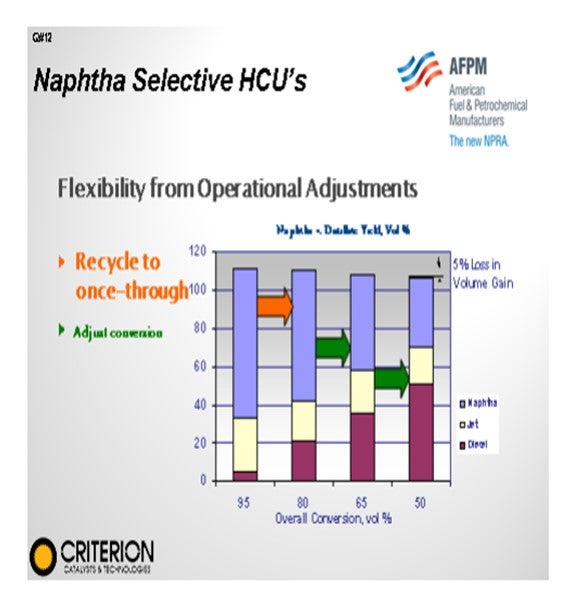
BODOLUS (CVR Energy)
Considerations start with feed slate and catalyst selection. For shifting to distillate production, the feed slate will need to be heavier to produce a higher yield of distillate range materials. Catalysts are also specific to feed and product distribution. Catalyst vendors can offer yield projections for various feed slates to match desired product distributions. It is important to get assurances from the catalyst vendor that produced diesel will meet local specification for sulfur, distillation and cold flow properties.
Once the feed slate has been selected and product yields have been determined, hydrogen consumption and distribution within the reactor need to be evaluated to assure compressors and control valves are sized to deliver the required quench streams. Downstream distillation equipment and product rundown may also have to be modified to accommodate the changes in product slate. Key assurances need to be obtained on the distillate product qualities to make sure they will be compatible with prevailing specifications on sulfur, cetane, and cold flow properties.
Shifting hydrocracker selectivity to distillate production has wide ranging implications to other units in the refinery. Overall changes in economics need to consider if the hydrocracker is competing for FCC feed and if the drop in naphtha production impacts hydrogen supply from the reformer operation.
CARLSON (Criterion Catalysts & Technologies)
As global diesel demand has risen and is forecasted to continue its growth, North American refiners have been compelled to evaluate their processing options to expand diesel production. Most of the conversion capacity of the approximately 60 operating hydrocrackers in North America is geared to the gasoline market. Nevertheless, Shell Global Solutions has helped refiners discover their flexibility for switching from gasoline mode to distillate mode by adjusting process operating parameters such as cracking conversion, liquid recycle rate, and product cutpoints without requiring CAPEX (capital expense).
Further increases of diesel production and quality from existing assets can be achieved through changes in catalyst to a distillate selective system from Criterion/Zeolyst, as well as through unit revamp projects. Clearly, each hydrocracker is unique and requires a detailed analysis of feed diet, operating constraints, and desired yield to adjust and optimize operations. Maintaining flexibility to adjust to diesel market conditions and building in the capability to handle a variety of feeds will allow for increased hydrocracker profitability.
Hydrocracker distillate mode operation is typically achieved by switching from a recycle operation to once-through operation while lowering conversion, which increases diesel (bottoms) production. When reducing conversion in an HCU to increase diesel yield, a lower overall conversion level may result in lower distillate quality due an increase in aromatics and resultant drop in API gravity. A reduction in product quality can be overcome through the use of a more distillate selective catalyst that will improve distillate quality via higher hydrogenation activity while improving distillate yields.
Lowering conversion to increase distillate yield will also result in reduced hydrogen consumption. Increasing feed rate to utilize the available hydrogen can recover the losses in volume gain across the hydrocracker. Therefore, one primary modification to gasoline hydrocrackers to improve distillate yield and throughput involves revamping the fractionation section to enable higher feed rates.
Hydrocracker revamp scenarios for maximizing distillate range can range significantly in scope. Shell Global Solutions has successfully increased distillate yields through minor modifications of the fractionation section of hydrocrackers. In gasoline hydrocrackers where light and heavy naphtha are drawn from the main fractionator, the heavy naphtha draw has been redesigned as a distillate draw. This modification increased the cutpoint of the fractionator bottoms and increased the boiling range of the cycle oil, considerably reducing the cracking of light and middle distillate products to light naphtha. Another common hydrocracker revamp involves upgrading reactor internals. Shell Global Solutions has experienced some gasoline hydrocrackers designed for an all-vapor phase quench zone requiring new internals based on changes in feed and conversion. It is well documented in North America and throughout the world, that this minimal capital investment strategy can increase liquid yield. These benefits have been seen in over 300 hydroprocessing applications in hydrocrackers owned and operated by refiners world-wide.
For some refineries, the opportunity to bring heavier feeds into a hydrocracking unit is desirable; but in cases where the fractionator bottoms are diesel pool blending material, adding heavier feed to the hydrocracker is likely to render the diesel unsuitable for blending. The addition of a vacuum flasher to recover diesel uncouples feed back-end from diesel cold properties and enables the processing of heavier/better feeds for increased distillate yield.
In larger scope revamp scenarios, significant increases in unit feed rates can be achieved thru the paralleling the stages (converting to single stage). In one North American refinery where this type of revamp occurred, a portion of the FCC feed was directed to the revamped hydrocracker in return for high quality bottoms product from the hydrocracker. A number of other modifications are required for this type of revamp to succeed, including the fractionation section.
SUBHASH SINGHAL (Kuwait National Petroleum Company)
Units designed for naphtha can be used for distillate based on shift in product demand and resulting financial benefits. Catalyst systems need to be changed for distillate selective yields (lower activity catalyst). A change in reactor severity will also provide enhanced distillate yields.