Our industries are committed to protecting the health and safety of our workers, our contractors, our neighbors, and the environment. When it comes to safety, we are never satisfied.
AFPM supports the work of our members with the following safety programs:
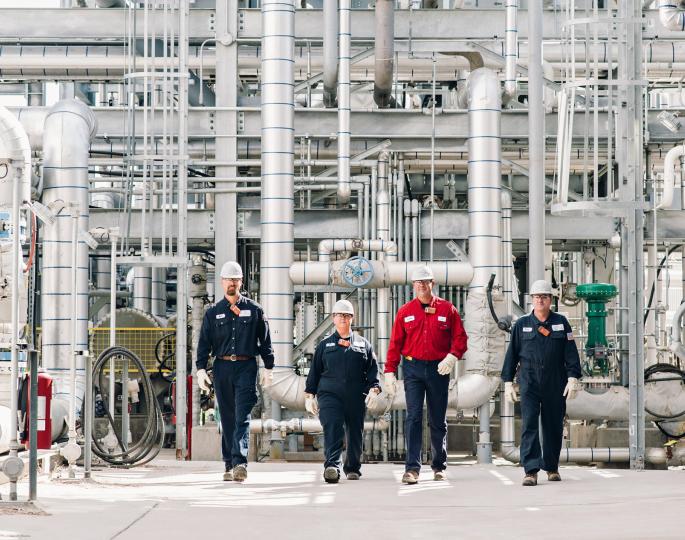
Advancing Process Safety Programs
Advancing Process Safety Programs
A groundbreaking collaboration between AFPM, the American Petroleum Institute (API) and our members designed to continuously improve process safety throughout the industry via data collection and opportunities to share experiences and knowledge.
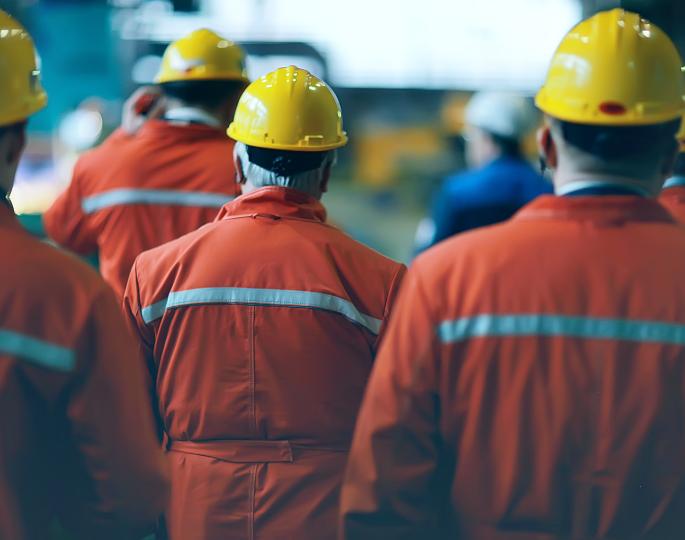
Occupational Safety
Occupational Safety
Employees are our most valuable asset, and nothing is more important than the safety of our workers and contractors.
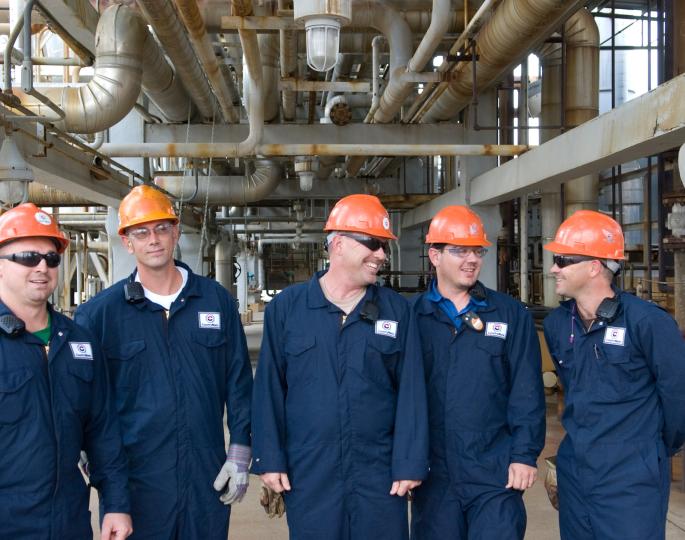
Safety Statistics Programs
Safety Statistics Programs
A comprehensive annual examination of industry-wide safety performance statistics both for injuries and illnesses (OSHA 300A) and for Tier 1 and Tier 2 process safety events (API RP 754). AFPM publishes the Survey of Occupational Injury & Illness report and the Process Safety Events report using the data collected.
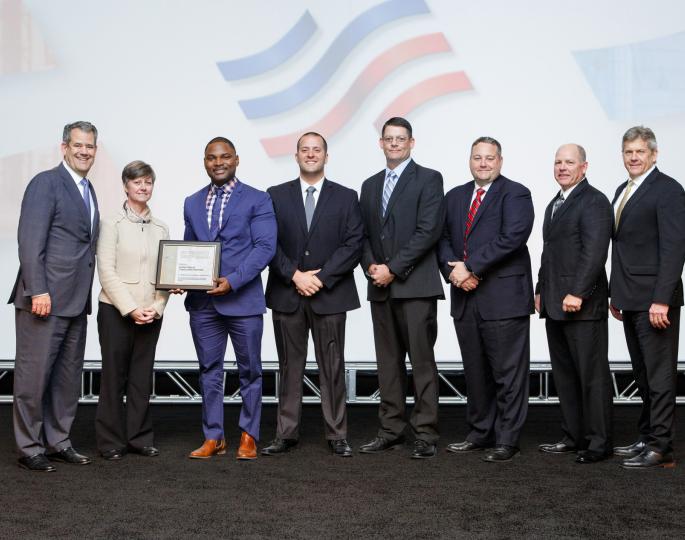
Safety Awards
Safety Awards
A celebration and recognition of those companies that exceed safety standards as measured by OSHA 300A and API RP 754 Process Safety data. The Safety Awards Program is open to AFPM Regular Member companies that operate a U.S. refinery or petrochemical manufacturing plant as well as AFPM Associate Member Contractors.
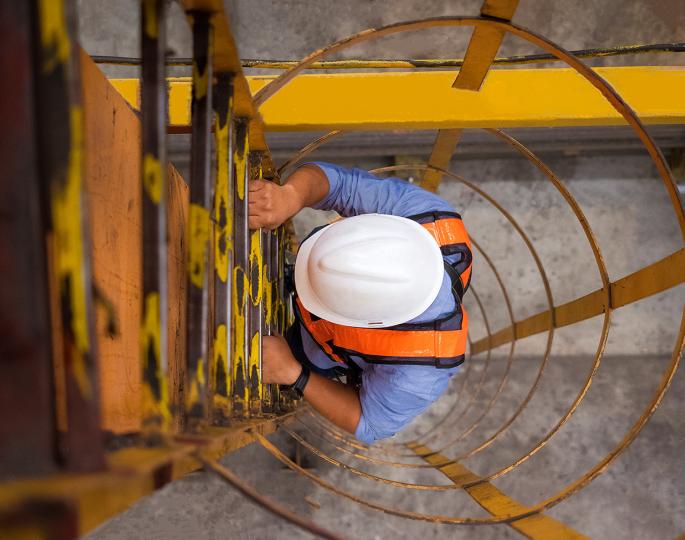
Safety Portal
Safety Portal
AFPM’s online Safety Portal serves as the hub for all Occupational and Process Safety programs.